- Understanding SolidWorks 3D Modeling
- Key Concepts in 3D Modeling
- Step-by-Step Guide to 3D Modeling in SolidWorks
- Step 1: Setting Up Your Workspace
- Step 2: Creating a New Part
- Step 3: Starting with a Sketch
- Step 4: Extruding the Sketch
- Step 5: Adding Features
- Step 6: Creating Assemblies
- Best Practices for 3D Modeling in SolidWorks
- Advanced Techniques in SolidWorks
- Surface Modeling
- Configurations
- Simulation
- Conclusion
SolidWorks is a leading CAD (Computer-Aided Design) software used by engineers, designers, and professionals across various industries. At its core, SolidWorks is designed for creating detailed 3D models, which are essential for visualizing, simulating, and manufacturing products. This guide will delve deep into the intricacies of 3D modeling in SolidWorks, providing you with the knowledge and skills needed to excel in your assignments and projects. Whether you are a student or a professional, seeking 3D modeling assignment help can significantly enhance your understanding and efficiency in using SolidWorks. The software's robust features and user-friendly interface make it an invaluable tool for creating complex geometries and assemblies.
SolidWorks' parametric design capabilities allow for easy adjustments and modifications, ensuring that your models are always up-to-date with the latest changes. This is particularly useful in educational settings, where students often need to make iterative changes to their designs based on feedback. By utilizing SolidWorks assignment help, students can gain insights into best practices and advanced techniques, enabling them to produce high-quality models that meet industry standards.
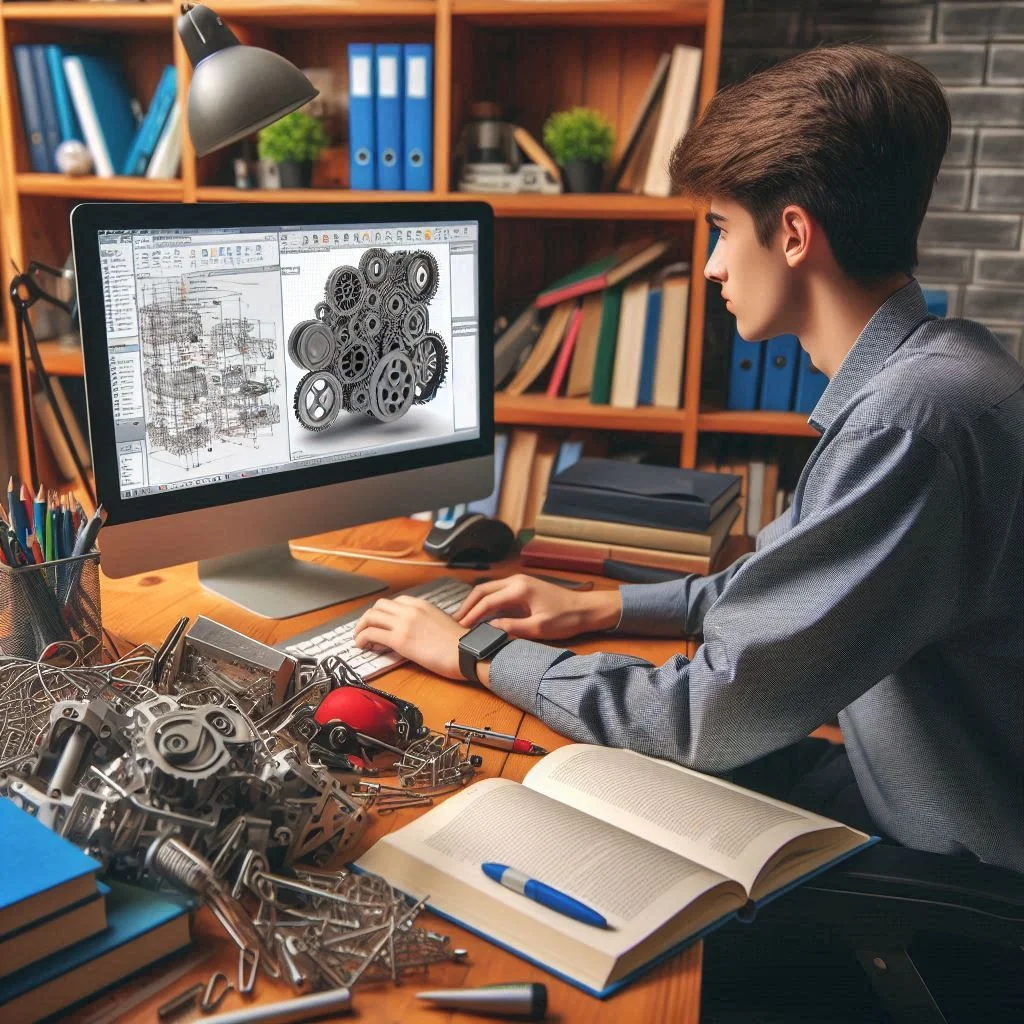
Furthermore, SolidWorks supports a wide range of applications, from mechanical and electrical design to simulation and manufacturing. This versatility makes it a preferred choice for professionals across different sectors. Engaging with experts for 3D modeling assignment help can provide you with the guidance needed to navigate these diverse applications effectively. Whether you're designing a simple part or a complex assembly, mastering SolidWorks will empower you to bring your ideas to life with precision and confidence. With the right support and resources, you can harness the full potential of SolidWorks and achieve excellence in your 3D modeling assignments.
Understanding SolidWorks 3D Modeling
3D modeling in SolidWorks involves creating digital representations of objects in three dimensions. These models are constructed using various features and tools within the software, allowing for precise and detailed design. The process begins with a 2D sketch, which is then transformed into a 3D model through extrusion, revolution, or lofting.
Key Concepts in 3D Modeling
- Sketching: The foundation of any 3D model in SolidWorks is the 2D sketch. Sketches are created on planes and consist of basic geometric shapes such as lines, circles, and arcs. Accurate sketching is crucial as it directly influences the final 3D model.
- Features: Features are the building blocks of 3D models. Common features include extrudes, revolves, lofts, sweeps, fillets, and chamfers. Each feature adds or removes material from the model, shaping it into the desired form.
- Parametric Design: SolidWorks uses parametric design principles, meaning that dimensions and relationships between features are defined by parameters. This allows for easy modification and updating of the model, as changes to parameters automatically propagate throughout the design.
- Design Intent: Capturing the design intent is crucial in SolidWorks. Design intent refers to the way a model reacts to changes. By understanding and defining relationships and constraints, you can ensure that your model behaves predictably when modified.
Step-by-Step Guide to 3D Modeling in SolidWorks
To set up your workspace, select units like millimeters or inches, and customize your grid and snap preferences. Starting with a new part file is straightforward, and defining sketches on planes like the front or top is crucial. Fully defining sketches with dimensions and relations ensures stability and precision in your design.
Step 1: Setting Up Your Workspace
Before you start modeling, it's essential to set up your workspace in SolidWorks. This includes selecting the appropriate units (inches, millimeters, etc.), setting grid and snap preferences, and configuring the user interface to suit your needs.
Tips:
- Use the CommandManager for quick access to frequently used tools.
- Customize toolbars and shortcuts to streamline your workflow.
- Save your workspace settings to maintain consistency across projects.
Step 2: Creating a New Part
To start a new 3D model, create a new part file. This will be the container for your model and its features.
- File > New > Part
- Save the part with a descriptive name.
Step 3: Starting with a Sketch
Begin your 3D model with a 2D sketch on a plane. The front, top, and right planes are commonly used as starting points.
- Select a Plane: Choose a plane to sketch on (e.g., Front Plane).
- Sketch Tools: Use the Line, Circle, Rectangle, and other sketch tools to create the basic outline of your part.
- Dimensions and Relations: Add dimensions to define the size of your sketch. Use geometric relations (e.g., parallel, perpendicular, coincident) to constrain the sketch fully.
Step 4: Extruding the Sketch
Once your sketch is complete and fully defined, you can extrude it to create a 3D model.
- Features > Extruded Boss/Base
- Select the Sketch: Choose the sketch you want to extrude.
- Set Parameters: Specify the extrusion depth and direction. You can also create a solid or a thin feature.
Step 5: Adding Features
To refine your model, add additional features. Here are some common features and their applications:
- Revolve: Used for creating symmetrical parts around an axis (e.g., cylinders, cones).
- Features > Revolved Boss/Base
- Select the Sketch and Axis of Revolution
- Loft: Used for creating complex shapes by blending multiple profiles.
- Features > Lofted Boss/Base
- Select the Profiles to Blend
- Sweep: Used for creating parts with a consistent cross-section along a path (e.g., pipes, tubes).
- Features > Swept Boss/Base
- Select the Profile and Path
- Fillet: Adds rounded edges to a part.
- Features > Fillet
- Select Edges and Specify the Radius
- Chamfer: Adds beveled edges to a part.
- Features > Chamfer
- Select Edges and Specify the Distance and Angle
Step 6: Creating Assemblies
Assemblies in SolidWorks are collections of parts and subassemblies. They allow you to visualize and test the interaction between different components.
- File > New > Assembly
- Insert Components: Bring in individual parts or subassemblies.
- Mates: Define relationships between components (e.g., coincident, concentric, parallel) to position them correctly.
- Test and Simulate: Check for interferences and simulate motion to ensure proper function.
Best Practices for 3D Modeling in SolidWorks
- Plan Your Design: Before starting, outline the design process and identify key features and components. This helps in maintaining a logical and efficient workflow.
- Keep Sketches Simple: Avoid overly complex sketches. Use multiple sketches and features to build up your model incrementally.
- Fully Define Sketches: Ensure that all sketches are fully defined with dimensions and relations. This prevents unexpected changes and ensures model stability.
- Use Symmetry: Take advantage of symmetry to reduce modeling time and ensure consistency. Use mirror and pattern features where applicable.
- Save Frequently: Regularly save your work to avoid losing progress. Use different versions or incremental saves for significant milestones.
- Leverage Design Library: Use the Design Library to store and reuse commonly used features and components. This can save time and maintain consistency across projects.
- Check for Errors: Regularly check for and resolve errors in sketches and features. Use the “Evaluate” tab to analyze and validate your model.
- Document Your Design: Create detailed drawings and documentation for your model. Include dimensions, tolerances, and material specifications.
Advanced Techniques in SolidWorks
Advanced techniques in SolidWorks, such as surface modeling, configurations, and simulation, provide designers with powerful tools to create complex shapes, manage multiple design variations, and analyze model behavior under real-world conditions. Mastering these techniques enhances your ability to produce innovative and optimized designs efficiently.
Surface Modeling
Surface modeling involves creating complex, freeform surfaces that are not possible with standard solid modeling techniques. This is useful for designing aesthetically driven parts, such as car bodies and consumer products.
Steps:
- Create Surface Features: Use tools like Boundary Surface, Lofted Surface, and Sweep Surface.
- Trim and Knit: Modify surfaces with Trim and Knit tools to create a continuous surface.
- Thicken Surface: Convert the surface model into a solid body using the Thicken tool.
Configurations
Configurations allow you to create multiple variations of a part or assembly within a single file. This is useful for managing different sizes, materials, or versions of a design.
Steps:
- Add Configuration: Go to the ConfigurationManager tab and add a new configuration.
- Modify Parameters: Change dimensions, features, or properties specific to each configuration.
- Switch Configurations: Toggle between configurations to view and edit different versions of the model.
Simulation
SolidWorks Simulation tools allow you to analyze the behavior of your model under real-world conditions. This includes stress analysis, thermal analysis, and motion studies.
Steps:
- Setup Study: Choose the type of simulation study (e.g., static, thermal, motion).
- Apply Materials: Define material properties for the parts.
- Define Loads and Fixtures: Apply forces, pressures, and constraints.
- Run Simulation: Analyze the results and make necessary design adjustments.
Conclusion
Mastering 3D modeling in SolidWorks is essential for anyone involved in design and engineering. By understanding the fundamental concepts and following a structured approach, you can create detailed, accurate, and functional 3D models. Remember to plan your design, keep sketches simple, and use advanced techniques to enhance your models. With practice and dedication, you'll become proficient in SolidWorks and excel in your assignments and projects. Additionally, continuously exploring new features and staying updated with the latest software developments will further enhance your skills. Engaging with the SolidWorks community, participating in forums, and attending webinars or training sessions can provide valuable insights and tips from experienced users. Moreover, utilizing the vast array of online resources, including tutorials and documentation, can help you overcome challenges and learn more efficient ways to accomplish tasks. As you gain experience, consider experimenting with custom macros and automation to streamline repetitive tasks, further boosting your productivity and expertise in SolidWorks.