- Understanding Project Requirements
- Project Overview
- Step-by-Step Guide to 3D Modeling
- Setting Up in Solidworks
- Sketching the Base Components
- Extruding and Creating 3D Bodies
- Utilizing Advanced Features
- Assembly and Interference Checking
- Applying Materials and Finishes
- Testing and Simulation
- Documentation and Presentation
- Conclusion
In the realm of engineering and robotics competitions, mastering 3D modeling is not just a skill but a cornerstone of success. Projects often demand precise design, accurate simulations, and effective collaboration—all achievable through tools like Solidworks. Whether you're designing for a robotics challenge, engineering competition, or academic project, this guide will walk you through the essential steps to excel in 3D modeling. Students can also read this guide which will help them to solve their 3D modelling assignmentwith precision and accuracy.
Solidworks, a leading CAD software, empowers engineers and students alike to transform conceptual ideas into tangible, meticulously designed models. Its user-friendly interface and robust feature set enable you to navigate complex project requirements with ease. By leveraging Solidworks, you gain access to a suite of tools tailored for every stage of the design process—from initial sketching to final simulation and documentation.
Beyond its technical capabilities, Solidworks fosters innovation and problem-solving. It encourages iterative design practices, allowing you to refine and optimize your models based on real-world constraints and performance metrics. This iterative approach not only enhances the functionality of your designs but also prepares you to tackle unforeseen challenges during the implementation phase.
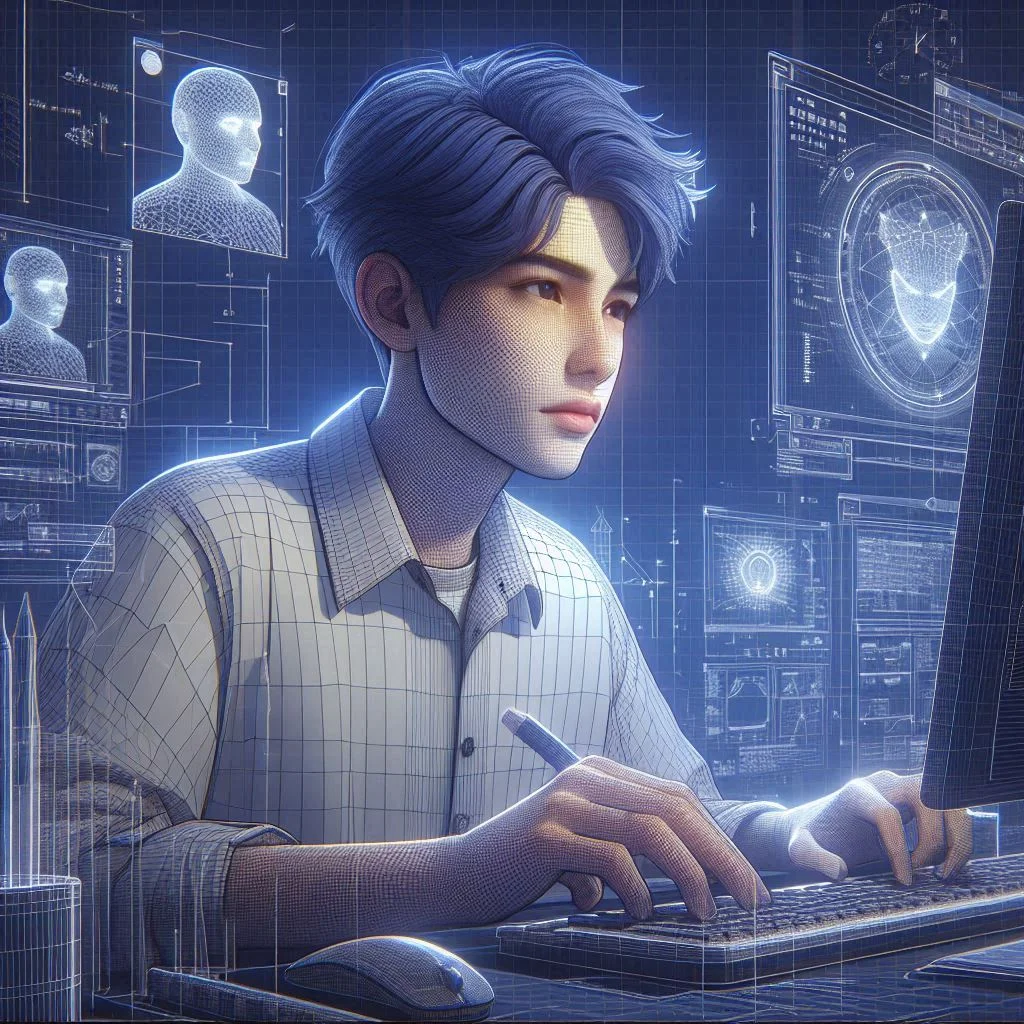
Moreover, mastering Solidworks extends beyond individual proficiency; it promotes effective collaboration within multidisciplinary teams. Through shared access to design files, version control, and collaborative tools, teams can seamlessly integrate their expertise in mechanical design, structural analysis, and electrical systems integration. This collaborative environment nurtures creativity and synergy, ensuring that every aspect of the project aligns with its overarching goals and specifications.
In essence, Solidworks serves as more than just a design tool—it's a catalyst for innovation in engineering education and professional practice. By embracing its capabilities and methodologies, aspiring engineers and students can elevate their 3D modeling skills to meet the rigorous demands of modern engineering challenges. Whether you're aiming to excel in a robotics competition or contribute groundbreaking research in your field, Solidworks equips you with the tools and mindset needed to turn ambitious ideas into reality.
Understanding Project Requirements
At the heart of every successful 3D modeling endeavor lies a deep understanding of project requirements. This foundational understanding sets the stage for accurate modeling and effective problem-solving. For instance, in a robotics competition scenario described earlier, precise knowledge of the table's plywood surface, the dimensions and materials of the starting box, the positioning and dimensions of towers and scoring areas, and the specifics of components like the cross-over tube and pulley system are crucial. Each detail informs the design process, guiding decisions on material selection, structural integrity, and functional simulations. By comprehensively grasping these requirements, you ensure that your 3D models not only meet but exceed expectations in terms of accuracy, functionality, and performance within the given constraints. This approach not only enhances the quality of your final design but also streamlines the iterative process of refinement and optimization. Let's dissect a typical scenario resembling a robotics challenge:
Project Overview
Imagine a robotics competition where teams are tasked with designing a robotic system to navigate and interact with various elements on a contest table. The table features specific components such as:
- Table Surface: Plywood with traction coating, dimensions 7'10-1/2" square.
- Starting Box: Plastic crate with dimensions 12" tall, 10" deep, 22" wide, including a ramp with a 17º incline.
- Trash Cube Scoring Area: Marked rectangle, 6"x10", positioned 28" from the back wall and 6" from the centerline.
- Towers: Six concrete towers dividing the table, varying in height and position.
- Cross-Over Tube: 10" I.D. PVC cylinder with ramps and rotational movement.
- Plant: Attached to a pulley system with sensor segments for scoring.
- Cans and Trash Cubes: Positioned with specific X-Y coordinates for scoring.
Step-by-Step Guide to 3D Modeling
Start by setting up your Solidworks environment, configuring units to match project specifications (typically inches or millimeters), and establishing workspace preferences. Utilize grid and snap options for precise sketching. Next, use 2D sketches to outline fundamental components such as the table surface, starting box, towers, and scoring areas based on provided dimensions and tolerances. Solidworks' sketch tools allow for accurate representation of shapes and dimensions. Once sketches are complete, extrude them to create 3D bodies, adjusting extrusion depths and heights as per project requirements. For example, the starting box may require multiple extrusions to form the crate and its inclined ramp. Utilize Solidworks' advanced features like Sweep for creating features such as the cross-over tube with a cylindrical shape and incline ramps, Loft for smoothly connecting different profiles like the trash cube scoring area's marked rectangle to its surrounding surface, and Revolve for components like the towers, which often feature a square base and tapered height
Setting Up in Solidworks
Begin by setting up your Solidworks environment. This initial step is crucial as it lays the foundation for your entire project. Start by configuring units to match the project specifications—whether in inches or millimeters—to ensure consistency and accuracy throughout the design process. Establishing workspace preferences, such as grid spacing and snap options, aids in achieving precise sketches and alignments. Solidworks provides customizable templates that streamline this setup process, allowing you to save time and maintain consistency across multiple projects.
Sketching the Base Components
With your Solidworks environment configured, move on to sketching the base components of the project. Focus on fundamental elements like the table surface, starting box, towers, and scoring areas. Utilize Solidworks' robust sketch tools to create 2D outlines of each component, adhering closely to provided dimensions and tolerances. These sketches serve as the framework upon which you'll build the 3D models, ensuring that every detail aligns with the project requirements.
Extruding and Creating 3D Bodies
Once your sketches are complete and verified for accuracy, proceed to extrude them into 3D bodies. Extrusion in Solidworks involves pulling 2D sketches along a specified path to create solid shapes. Adjust the extrusion depths and heights according to the project specifications. For instance, the starting box may require multiple extrusions to form both the main crate structure and its inclined ramp. Pay attention to details such as angles and dimensions to accurately represent the physical properties of each component in your 3D model.
Utilizing Advanced Features
SolidWorks offers a range of advanced features to handle complex geometries:
- Sweep: Use for creating features like the cross-over tube with a cylindrical shape and incline ramps.
- Loft: Ideal for smoothly connecting different profiles, such as the trash cube scoring area's marked rectangle to its surrounding surface.
- Revolve: Perfect for components like the towers, which often feature a square base and tapered height.
Assembly and Interference Checking
Assemble components virtually in Solidworks to simulate real-world conditions accurately. Use mates and constraints to ensure parts fit together seamlessly, mimicking actual assembly processes. Solidworks' assembly features allow for precise positioning and alignment, crucial for functional integrity. Perform interference checks to detect and resolve clashes early in the design phase. Identifying interferences ensures all components, from the cross-over tube to the towers and scoring elements, function as intended without spatial conflicts or operational hindrances.
Applying Materials and Finishes
Assign appropriate materials to each component based on their real-world counterparts:
- Table Surface: Plywood with a rough coating for traction.
- Towers: Concrete with sheet steel caps.
- Starting Box: Plastic material with specified structural properties.
- Cross-Over Tube: PVC with defined rigidity and rotational characteristics.
Consider factors like weight, durability, and friction when selecting materials, ensuring your simulations accurately reflect real-world behaviors.
Testing and Simulation
Simulate your design to validate functionality and performance:
- Motion Studies: Analyze movement and interaction of components such as the cross-over tube and pulley system.
- Assembly Simulation: Verify assembly sequences and identify potential assembly issues.
- Stress Analysis: Evaluate structural integrity under load, ensuring components meet safety and performance requirements.
Iterate on your design based on simulation results, refining and optimizing for improved performance.
Documentation and Presentation
Document your design process comprehensively:
- Detailed Drawings: Create annotated drawings with dimensions and manufacturing notes for each component.
- Design Rationale: Explain design decisions, considerations, and optimizations made during the process.
- Presentation: Prepare a visually appealing presentation showcasing your 3D models, simulations, and design insights. Highlight key features and innovations that set your design apart.
Conclusion
Mastering 3D modeling is indeed a transformative journey that blends technical proficiency with creative problem-solving. This guide empowers you to navigate complex challenges, equipping you with the skills needed to excel in robotics, engineering competitions, and academic projects alike. Solidworks' robust toolset not only facilitates precise modeling but also fosters innovation and efficiency in design processes.
Success in 3D modeling hinges on more than just software proficiency; it requires a deep understanding of project requirements, meticulous execution of designs, rigorous testing to validate performance, and clear, detailed documentation to communicate your work effectively. Each step in this process—from initial sketches to final simulations—contributes to refining your design and achieving optimal outcomes.
As you embark on your own projects, remember to embrace the iterative nature of design. Every challenge encountered and overcome is an opportunity for growth and improvement. By embracing these principles and leveraging Solidworks to its fullest potential, you'll not only meet project objectives but also push the boundaries of what's possible in engineering and design.
With dedication and practice, mastering 3D modeling will not only enhance your technical skills but also empower you to innovate and solve complex problems across various disciplines. Start your journey today and unlock the potential of 3D modeling in transforming ideas into reality.