- Understanding SolidWorks in Aerospace Design
- Key Features of SolidWorks for Aerospace Applications
- The Art of 3D Modeling in SolidWorks
- Simulating Real-World Conditions: SolidWorks in Aerospace Simulation
- Case Studies: Realizing Aerospace Dreams with SolidWorks
- Challenges and Solutions in Aerospace Component Design
- The Future of Aerospace Design: SolidWorks Innovations
- Conclusion:
In the dynamic world of aerospace engineering, SolidWorks emerges as a powerhouse for crafting intricate 3D aircraft components. Let's delve into the fascinating journey of designing these components and the pivotal role SolidWorks plays in elevating aviation technology. If you need help with your 3D Modeling assignment, exploring SolidWorks as a tool for designing aircraft components offers valuable insights into the practical applications of 3D modeling in aerospace engineering, providing a hands-on approach to mastering the intricacies of 3D modeling techniques.
Aerospace engineering stands at the forefront of technological advancement, demanding precision, innovation, and efficiency. In this fast-paced industry, the design and development of aircraft components require state-of-the-art tools to meet the ever-evolving demands of modern aviation. SolidWorks, a prominent player in the realm of Computer-Aided Design (CAD), has risen to prominence as a go-to solution for engineers and designers striving to push the boundaries of aerospace innovation.
SolidWorks facilitates a seamless transition from conceptualization to realization, providing a comprehensive platform for creating intricate 3D models of aircraft components. This CAD software is renowned for its user-friendly interface, making it accessible to both seasoned professionals and aspiring engineers alike. The journey of crafting 3D aircraft components begins with a vision, and SolidWorks acts as the bridge between imagination and tangible reality.
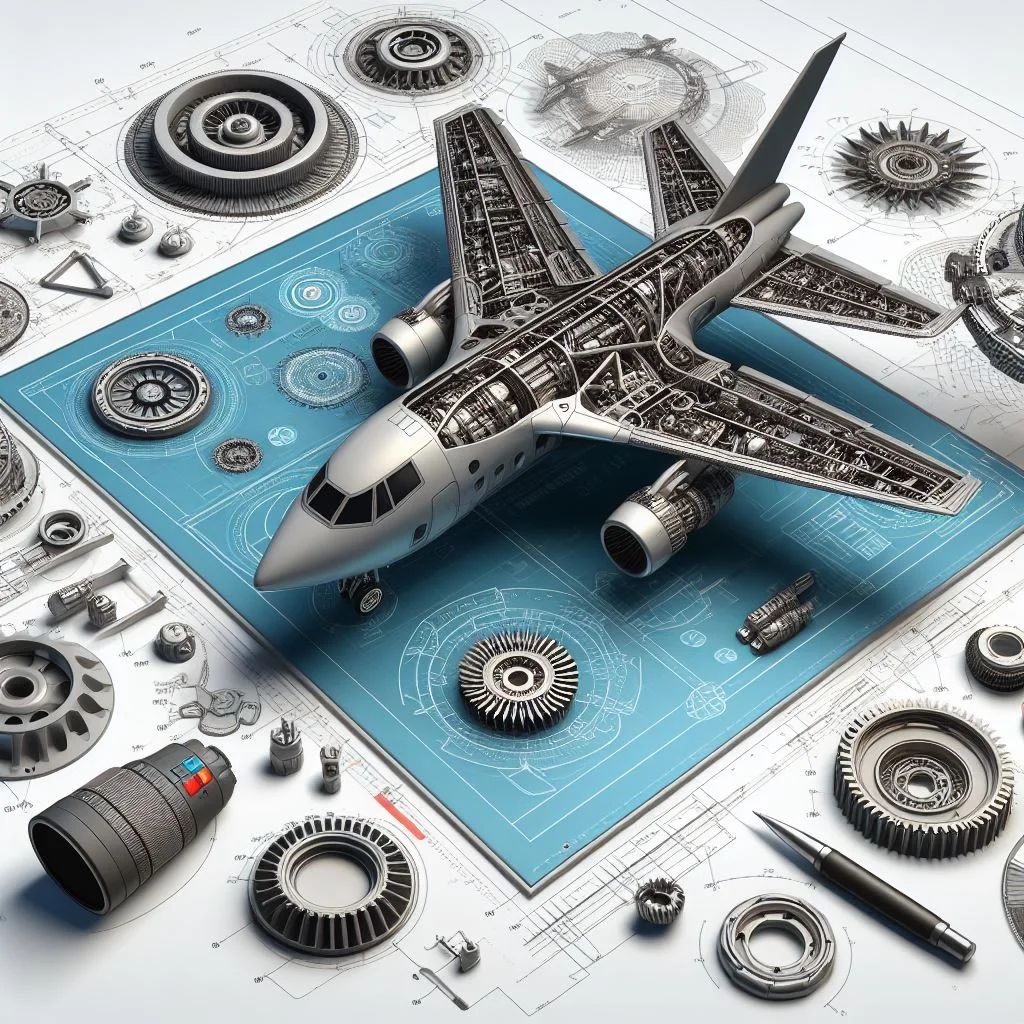
One of the key strengths of SolidWorks lies in its parametric modeling capabilities. Engineers can create models that are not only visually stunning but also possess intelligent properties. Changes made to one part of the design are automatically reflected throughout the entire model, ensuring consistency and coherence in the final product. This parametric approach significantly streamlines the design process, allowing for quick iterations and adjustments as needed.
As we navigate through the intricate world of 3D modeling with SolidWorks, it becomes evident that the software's prowess extends beyond mere visualization. The assembly modeling feature empowers engineers to simulate the integration of various components, providing a holistic view of the entire aircraft structure. This feature is invaluable in identifying potential clashes or interferences early in the design phase, saving both time and resources.
Moreover, SolidWorks excels in its ability to simulate real-world conditions. In the aerospace industry, where functionality and reliability are paramount, this simulation capability becomes a game-changer. Engineers can subject their designs to a variety of environmental factors, stress tests, and performance simulations, ensuring that the final 3D aircraft components not only meet but exceed industry standards.
A closer look at the software's application in aerospace reveals that SolidWorks is not just a design tool but a comprehensive solution for innovation. The iterative process of refining and perfecting designs is made efficient, allowing engineers to focus on pushing the boundaries of what is possible. This iterative approach is particularly crucial in an industry where cutting-edge technology and breakthroughs often define success.
In the next sections, we will explore the specific features of SolidWorks that cater to the unique demands of aerospace design, shedding light on the art of 3D modeling and the pivotal role of simulation in crafting reliable aircraft components. Additionally, we will delve into real-world case studies, uncovering instances where SolidWorks has been instrumental in bringing revolutionary aerospace concepts to life.
As we embark on this exploration, it becomes evident that SolidWorks is not just a tool; it is an enabler of aerospace dreams, propelling the industry toward new heights of innovation and excellence. Stay tuned as we unravel the layers of this intricate journey, showcasing how SolidWorks continues to redefine the landscape of aerospace engineering.
Understanding SolidWorks in Aerospace Design
SolidWorks, a preeminent Computer-Aided Design (CAD) software, stands as the linchpin in the intricate processes of aerospace design. Its pervasive influence extends beyond mere utility, ushering in a new era of innovation within the aviation industry. A closer examination of SolidWorks reveals a rich tapestry of features meticulously crafted to facilitate the creation of intricate 3D aircraft components.
At the heart of SolidWorks lies its parametric modeling capabilities, empowering designers to create models defined by parameters and establish dynamic relationships between various components. This not only expedites the design process but also ensures that modifications can be effortlessly integrated without compromising the overall integrity of the project. The software's intuitive interface allows aerospace engineers to harness the power of parametric design, enabling the swift exploration of diverse design possibilities.
Furthermore, SolidWorks boasts robust assembly modeling tools, facilitating the seamless integration of individual components into a cohesive and functional whole. This capability is particularly crucial in the aerospace industry, where the synergy between different parts plays a pivotal role in the overall performance and safety of aircraft. SolidWorks' assembly modeling not only streamlines the design process but also enhances the accuracy and reliability of the final 3D aircraft components.
In addition to its prowess in parametric and assembly modeling, SolidWorks encompasses a spectrum of features tailored for aerospace design challenges. These include advanced surface modeling, allowing for the creation of complex aerodynamic shapes, and built-in simulation tools that enable engineers to predict and optimize the performance of 3D aircraft components under various conditions.
Key Features of SolidWorks for Aerospace Applications
In the intricate realm of aerospace design, SolidWorks stands as a versatile and indispensable tool, equipped with a myriad of features tailored to the unique demands of the industry. Parametric modeling, one of SolidWorks' flagship features, allows designers to create 3D models with parameters, facilitating easy modifications and adjustments. This proves crucial in the iterative process of aerospace design, where precision and adaptability are paramount.
Furthermore, SolidWorks boasts a sophisticated assembly modeling capability, enabling the seamless integration of various components into a cohesive aircraft design. This feature ensures that every element, from the smallest bolt to the most complex engine part, fits together with precision, mirroring the intricacies of real-world aerospace engineering.
Simulation capabilities within SolidWorks are a game-changer in the field. Engineers can subject their designs to rigorous virtual testing, simulating a range of conditions from structural stresses to fluid dynamics. This not only expedites the development process but also enhances the reliability and safety of the final aircraft components.
SolidWorks goes beyond traditional CAD software by incorporating finite element analysis (FEA), allowing designers to evaluate how components will perform under stress, ensuring they meet the stringent standards of the aerospace industry. Additionally, the software's compatibility with a range of file formats enhances collaboration among multidisciplinary teams, fostering a holistic approach to aircraft component design. SolidWorks, with its comprehensive toolkit, continues to redefine the boundaries of innovation in aerospace applications.
The Art of 3D Modeling in SolidWorks
Diving into the world of 3D modeling with SolidWorks is an immersive journey that unveils the intricate techniques behind transforming conceptual ideas into tangible and functional aircraft components. At the heart of this transformative process lies the concept of parametric design, a fundamental feature of SolidWorks that enables engineers to establish relationships between different elements of the model. This dynamic approach allows for the creation of models with parameters that can be easily modified, offering unparalleled flexibility during the design phase.
Assembly modeling, another pivotal aspect of SolidWorks, allows designers to bring together individual components into a cohesive and interactive model. This capability is particularly crucial in aerospace engineering, where the integration of various parts is intricate and demands precise coordination. SolidWorks facilitates this process, enabling engineers to visualize and analyze the assembled components before they physically come together, ensuring a seamless fit and functionality.
The iterative nature of the design process is a hallmark of aerospace innovation, and SolidWorks plays a crucial role in facilitating this continuous refinement. Engineers can rapidly iterate designs, making adjustments, and improvements as they progress. This iterative approach not only accelerates the design phase but also contributes to the development of more optimized and efficient 3D aircraft components. SolidWorks empowers designers to explore various design alternatives, evaluate their performance, and refine them iteratively, ultimately leading to the creation of high-performance and reliable aerospace components.
Simulating Real-World Conditions: SolidWorks in Aerospace Simulation
SolidWorks stands out not only for its prowess in design but also for its robust simulation capabilities, a critical aspect in the aerospace industry. Simulation tools within SolidWorks allow engineers to replicate real-world conditions, providing a virtual testing ground for 3D aircraft components. This step is pivotal in ensuring that the designed components not only meet specifications but also perform optimally under the demanding circumstances of flight.
The significance of simulating real-world conditions cannot be overstated. Aerospace components operate in extreme environments, subjected to varying temperatures, pressures, and forces during flight. SolidWorks' simulation tools enable engineers to assess how these components will behave under such conditions, allowing for adjustments and refinements before physical prototypes are even created. This not only accelerates the design process but also minimizes the risk of potential issues in the final product.
Furthermore, the simulation capabilities extend to factors like structural integrity, aerodynamics, and thermal performance. Engineers can evaluate stress points, airflow patterns, and heat dissipation, ensuring that every aspect of the 3D aircraft component is thoroughly analyzed and optimized. The ability to simulate and refine designs in a virtual environment ultimately leads to enhanced functionality, reliability, and safety of aerospace systems.
Case Studies: Realizing Aerospace Dreams with SolidWorks
In exploring the realm of case studies, it becomes evident that SolidWorks has played a pivotal role in translating visionary aerospace concepts into tangible realities. One noteworthy example involves the design and development of streamlined wings for next-generation aircraft. SolidWorks facilitated the intricate modeling and analysis required to optimize wing shapes for enhanced aerodynamics, fuel efficiency, and overall performance. The software's parametric design capabilities allowed engineers to swiftly iterate through various wing configurations, ensuring the final design met rigorous industry standards.
Additionally, SolidWorks has left an indelible mark on the creation of intricate engine components, pushing the boundaries of what's possible in aviation technology. Engineers leveraged the software's advanced assembly modeling features to meticulously design and simulate complex propulsion systems. Through detailed virtual testing and analysis, SolidWorks enabled the identification and resolution of potential issues before the manufacturing phase, saving both time and resources. The result is a generation of aircraft engines that exhibit superior efficiency, reduced emissions, and heightened reliability – all made possible by the innovative application of SolidWorks in the aerospace industry.
These case studies underscore SolidWorks' transformative impact, not just on individual components, but on the broader landscape of aviation. The software's role in realizing aerospace dreams goes beyond mere design; it acts as a catalyst for pushing the boundaries of innovation, making sustainable and high-performance aircraft a reality for the future.
Challenges and Solutions in Aerospace Component Design
Navigating the intricate landscape of aerospace component design presents a myriad of challenges, each demanding meticulous attention and innovative solutions. One such challenge lies in the realm of complex geometries. Aircraft components often require intricate shapes and structures, posing a significant hurdle in the design process. SolidWorks rises to the occasion, offering a suite of tools that excel in handling complex geometries with precision. The software's parametric modeling capabilities allow designers to manipulate and refine shapes effortlessly, ensuring that even the most intricate aircraft components can be accurately represented in the virtual space before physical production.
Material considerations further add to the complexity of aerospace component design. The selection of materials plays a pivotal role in the performance, durability, and safety of aircraft. SolidWorks facilitates this critical aspect by providing extensive material libraries and simulation tools. Designers can assess the behavior of different materials under various conditions, allowing for informed decisions on the optimal choice for each component. This integrated approach streamlines the material selection process, reducing the likelihood of unforeseen issues during the later stages of development.
Moreover, SolidWorks addresses the challenge of ensuring seamless collaboration in multi-disciplinary teams. In the aerospace industry, where collaboration among experts in various domains is crucial, SolidWorks' collaborative features enable concurrent design activities. Engineers, aerodynamicists, and structural analysts can work cohesively within the same digital environment, fostering efficient communication and reducing the risk of errors in the final design.
The Future of Aerospace Design: SolidWorks Innovations
Peer into the future of aerospace design with SolidWorks and anticipate a wave of groundbreaking innovations that are set to revolutionize the way 3D aircraft components are conceived and materialized. SolidWorks, as a pioneer in the field of CAD technology, is continually evolving to meet the ever-changing demands of the aerospace industry.
One notable innovation on the horizon is the integration of artificial intelligence (AI) into SolidWorks. This transformative addition aims to enhance the design process by automating repetitive tasks, providing intelligent suggestions, and optimizing the overall efficiency of 3D modeling. With AI-assisted design, engineers can expect a significant reduction in time-consuming tasks, allowing them to focus more on creativity and problem-solving.
Additionally, SolidWorks is poised to introduce advancements in virtual reality (VR) and augmented reality (AR) features. Imagine being able to immerse yourself in a virtual environment to interact with and manipulate 3D aircraft components seamlessly. This integration of VR and AR not only streamlines collaboration among team members but also offers a more immersive and intuitive design experience.
Furthermore, SolidWorks is actively exploring sustainable design practices. The future of aerospace design will see an increased emphasis on eco-friendly materials, energy-efficient components, and streamlined manufacturing processes. SolidWorks aims to empower engineers to create innovative solutions that not only meet performance standards but also contribute to a more sustainable and environmentally conscious aviation industry.
As we look ahead, SolidWorks continues to be at the forefront of technological advancements, ensuring that the future of aerospace design is marked by efficiency, sustainability, and unprecedented creativity. The upcoming features and innovations in SolidWorks are not just enhancements; they are a glimpse into the transformative journey that awaits the aerospace industry.
Conclusion:
In conclusion, the transformative impact of SolidWorks on aerospace engineering is profound, revolutionizing the way 3D aircraft components are conceived and realized. From the initial stages of conceptualization through the rigorous process of simulation and beyond, SolidWorks stands as a stalwart force in shaping the trajectory of aerospace design.
SolidWorks serves as a catalyst in the conceptualization phase, providing engineers and designers with a versatile platform to translate abstract ideas into tangible 3D models. Its intuitive parametric modeling capabilities empower users to experiment with various design iterations, fostering creativity and innovation in the early stages of aircraft component development. This iterative process not only accelerates design cycles but also allows for the exploration of unconventional concepts, pushing the boundaries of what is achievable in aerospace engineering.
As the design progresses, SolidWorks plays a pivotal role in simulation, a critical aspect of ensuring the reliability and functionality of 3D aircraft components. The software's robust simulation tools enable engineers to subject their designs to real-world conditions, predicting performance, identifying potential issues, and refining the components for optimal efficiency. This simulation-driven approach minimizes the need for physical prototypes, reducing development costs and accelerating time-to-market for groundbreaking aerospace technologies.
Moreover, SolidWorks extends its influence beyond the traditional realms of design and simulation, seamlessly integrating with emerging technologies that are poised to shape the future of aerospace engineering. The software's compatibility with additive manufacturing processes, such as 3D printing, opens new avenues for manufacturing complex and lightweight components, contributing to the ongoing trend of aircraft weight reduction and fuel efficiency.
The collaborative nature of SolidWorks further amplifies its impact on the aerospace industry. Design teams can work seamlessly across geographical boundaries, fostering a global exchange of ideas and expertise. This collaborative environment not only expedites the design process but also promotes cross-disciplinary innovation, as experts from diverse fields contribute their insights to the development of 3D aircraft components.
Looking forward, SolidWorks continues to evolve, embracing emerging technologies and industry trends. The software's commitment to staying at the forefront of innovation is evident in its regular updates and feature enhancements. As aerospace engineering advances, SolidWorks adapts, ensuring that designers and engineers have the tools they need to push the boundaries of what is possible.
In essence, SolidWorks is not merely a software tool; it is a driving force propelling aerospace engineering into new frontiers. Its influence extends from the conception of ideas to the simulation of real-world conditions, and its adaptability ensures that it remains a cornerstone of 3D aircraft component design. As we stand on the brink of an era defined by technological leaps, SolidWorks stands poised to lead the way, solidifying its legacy as an indispensable companion in the pursuit of aerospace innovation.