- Preprocessing Stage
- Define the Problem Statement
- Generate a Suitable Mesh
- Assign Material Properties
- Solution Stage
- Apply Boundary Conditions
- Solve the Finite Element Equations
- Postprocessing Stage
- Visualize and Verify Results
- Perform Result Interpretation
- Perform Sensitivity Analysis
- Conclusion
Engineering professionals frequently use the numerical method known as finite element analysis (FEA) to analyze and simulate complex systems. The ability to predict and comprehend the behavior of structures and components under various loading conditions has made it an essential tool in a variety of industries, including structural engineering, automotive, and aerospace. Approaching FEA assignments can occasionally be a difficult task for both professionals and students, requiring a methodical and well-structured approach. This tutorial's goal is to offer a thorough explanation of how to approach finite element analysis assignments and a clear road map for completing all of the necessary steps. Individuals can confidently take on FEA assignments and achieve accurate and reliable results by understanding the fundamentals of FEA, including problem definition, mesh generation, material properties assignment, boundary conditions application, and solution techniques. To emphasize the significance of verifying and comprehending the obtained results, the postprocessing stage, which entails result visualization, interpretation, and sensitivity analysis, will also be discussed. For students and professionals looking to develop their skills and advance engineering solutions, mastering the approach to finite element analysis assignments is essential.
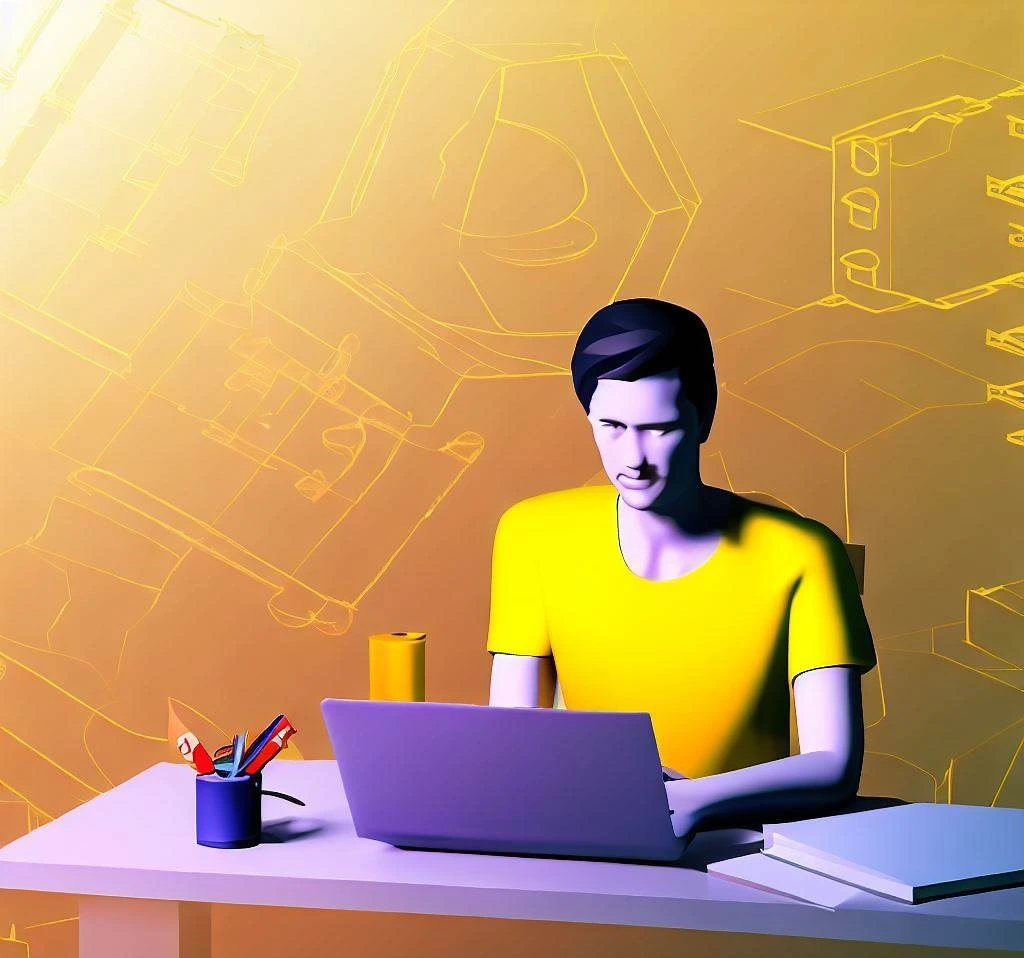
Preprocessing Stage
Preprocessing is a crucial stage in FEA assignments and entails a number of crucial tasks that lay the groundwork for precise and trustworthy simulations. Clarifying the problem statement is the first task at this stage. It is crucial to comprehend the analysis's goals, choose the appropriate analysis type (such as static, dynamic, or thermal), and establish the boundary conditions. The direction of subsequent stages of the analysis is established by a clearly stated problem statement. The creation of a suitable mesh is the next important task in the preprocessing phase. To effectively and accurately represent the structure or component, mesh generation involves breaking down the system's intricate geometry into smaller components. The quality of the analysis's findings is significantly influenced by the mesh's density and element type selection. Depending on the geometry of the system and the type of element being used, such as triangles, quadrilaterals, tetrahedrons, or hexahedrons, may be used. Another crucial task during the preprocessing stage is assigning the proper material properties. Assigning the appropriate material properties, such as Young's modulus, Poisson's ratio, density, and thermal conductivity, is necessary to accurately simulate the behavior of the system. Accurate analysis results depend on having a solid understanding of the behavior of the subject matter and having access to trustworthy data. Another crucial task during the preprocessing stage is assigning the proper material properties. Assigning the appropriate material properties, such as Young's modulus, Poisson's ratio, density, and thermal conductivity, is necessary to accurately simulate the behavior of the system. Accurate analysis results depend on having a solid understanding of the behavior of the subject matter and having access to trustworthy data.
Define the Problem Statement
It is crucial to begin by stating the problem clearly in any FEA assignment. Understanding the goal, identifying the type of analysis needed (static, dynamic, thermal, etc.), and figuring out the boundary conditions are all part of this.
Generate a Suitable Mesh
To make analysis easier, complex geometry is divided into a finite number of smaller elements during mesh generation. The accuracy and effectiveness of the analysis are significantly impacted by the mesh density and element type selection. Elements like triangles, quadrilaterals, tetrahedrons, and hexahedrons can be used, depending on the issue.
Assign Material Properties
Assigning suitable material properties to the model is necessary in order to faithfully simulate the behaviour of the system. These characteristics could include things like density, thermal conductivity, Poisson's ratio, Young's modulus, etc. Accurate analysis results depend on having access to reliable data and an understanding of the behaviour of the subject matter.
Solution Stage
The solution stage, where the actual computation and solution of the finite element equations take place, is a crucial stage in finite element analysis (FEA) assignments. To achieve the desired outcomes, boundary conditions must be applied and equations must be solved. Applying suitable boundary conditions to the model comes first in the solution stage. Boundary conditions specify the loads and restrictions placed on the system. In this, certain degrees of freedom may be fixed, forces or pressures may be applied, and temperature conditions may be specified. For precise and significant results, the boundary conditions must be defined correctly. The finite element equations describing the behavior of the system must then be solved after the boundary conditions have been applied. The equations frequently have many degrees of freedom and are nonlinear. These equations can be resolved numerically using a variety of methods, such as iterative or direct solvers. The size and complexity of the problem determine the solver to use. The objective is to determine the displacements, stresses, and strains as well as other important parameters that describe the behavior of the system.
Apply Boundary Conditions
The restrictions and loads placed on the system are specified by the boundary conditions. In this, certain degrees of freedom may be fixed, forces or pressures may be applied, and temperature conditions may be specified. For meaningful results, the boundary conditions must be defined correctly.
Solve the Finite Element Equations
The large system of equations representing the behavior of the system must be numerically solved in order to solve the finite element equations. These equations can be effectively solved using a variety of numerical methods, including direct solvers and iterative approaches. The size and complexity of the problem determine the solver to use.
Postprocessing Stage
In finite element analysis (FEA) assignments, the postprocessing stage is a crucial stage where the results obtained from the solution stage are visualized, interpreted, and validated. This step entails analyzing the numerical data and turning it into information that is useful for decision-making. Visualizing the outcomes is the first task in the postprocessing phase. Several methods, including contour plots, vector plots, and animations, can be used to accomplish this. Displacements, stresses, strains, and temperatures are just a few examples of parameters that can be visualized to help understand how the system behaves and spot problem areas. The next step is to interpret the results after they have been visualized. This entails comparing the calculated values to experimental data, safety considerations, or design criteria. Engineers can determine whether the system satisfies the necessary specifications or if any modifications are required by comparing the results to predetermined standards. A thorough understanding of the system's response to various loads and boundary conditions is made possible by result interpretation.
Visualize and Verify Results
After the analysis is finished, it's crucial to see and confirm the outcomes. You can see parameters like displacements, stresses, strains, and temperatures using postprocessing tools in the FEA software. Careful analysis of these findings aids in identifying potential problems or regions that need more elaboration.
Perform Result Interpretation
To use the analysis to produce meaningful conclusions, it is essential to interpret the results. This entails comparing the calculated values to experimental data, safety considerations, or design criteria. Engineers can make informed decisions and improve the system's design or performance by analyzing the results.
Perform Sensitivity Analysis
Sensitivity analysis aids in comprehending how different parameters affect the system's behavior. It entails changing the input parameters within a range and tracking how the output changes in response. Sensitivity analysis assists in locating important design parameters and improving the efficiency of the system.
Conclusion
In conclusion, approaching finite element analysis (FEA) assignments successfully necessitates a methodical and well-organized approach throughout various stages. Accurate simulations are built on a solid understanding of the fundamentals of finite element analysis, including problem definition, mesh generation, material property assignment, and boundary condition application. To produce meaningful results, the solution stage entails solving the finite element equations and applying the proper boundary conditions. Engineers can validate their findings and make informed decisions by visualizing and interpreting the results during the postprocessing stage. Additionally, performing a sensitivity analysis helps with understanding how different parameters affect the behavior of the system and maximizing its performance. Individuals can improve their understanding and proficiency in FEA by following this step-by-step tutorial, producing more accurate and dependable results. But it's crucial to remember that FEA requires practice and actual application before it can be mastered. The development of abilities and expertise in this potent numerical technique will be furthered by working with real-world examples and seeking advice from knowledgeable experts. Individuals can succeed in FEA assignments and help to advance engineering solutions if they are focused and have a firm grasp of the fundamental ideas.