- Understanding Mates in Assemblies
- Types of Mates:
- Creating a Faucet Subassembly
- Step-by-Step Process:
- Applying Mates for Accurate Positioning
- Steps to Apply a Coincident Mate:
- Steps to Apply a Concentric Mate:
- Positioning the Components Precisely
- Fine-Tuning the Position:
- Load Additional Components
- Steps to Load Additional Components:
- Additional Tips for Successful Assemblies
- 1. Plan Your Assembly:
- 2. Use Subassemblies:
- 3. Leverage Design Tables:
- 4. Utilize Assembly Features:
- 5. Check for Interferences:
- 6. Document Your Assembly:
- Conclusion
SolidWorks is a powerful tool for 3D modeling and computer-aided design (CAD) that allows users to create detailed assemblies from individual parts. Understanding how to use mates and position components correctly within an assembly is crucial for creating functional and accurate designs. In this blog, we will explore the concepts of mates and positioning in assemblies, with a focus on creating a faucet subassembly. We will cover the different types of mates, how to load components into an assembly, and the step-by-step process of positioning components using coincident and concentric mates. Whether you are a beginner or looking to refine your skills, mastering these techniques is essential for any assembly assignment. Accurate positioning and proper use of mates not only ensure that your components fit together seamlessly but also enhance the overall functionality and durability of your design. If you encounter challenges, remember that seeking solidworks assignment help can be beneficial in understanding complex concepts and improving your proficiency in this powerful software.
Understanding Mates in Assemblies
Mates are fundamental to assembling components in SolidWorks. They define the relationships between components, controlling their relative movement and orientation. Mates create geometric relationships between parts, ensuring that they interact correctly. There are several types of mates, each suited for different geometric configurations.
Types of Mates:
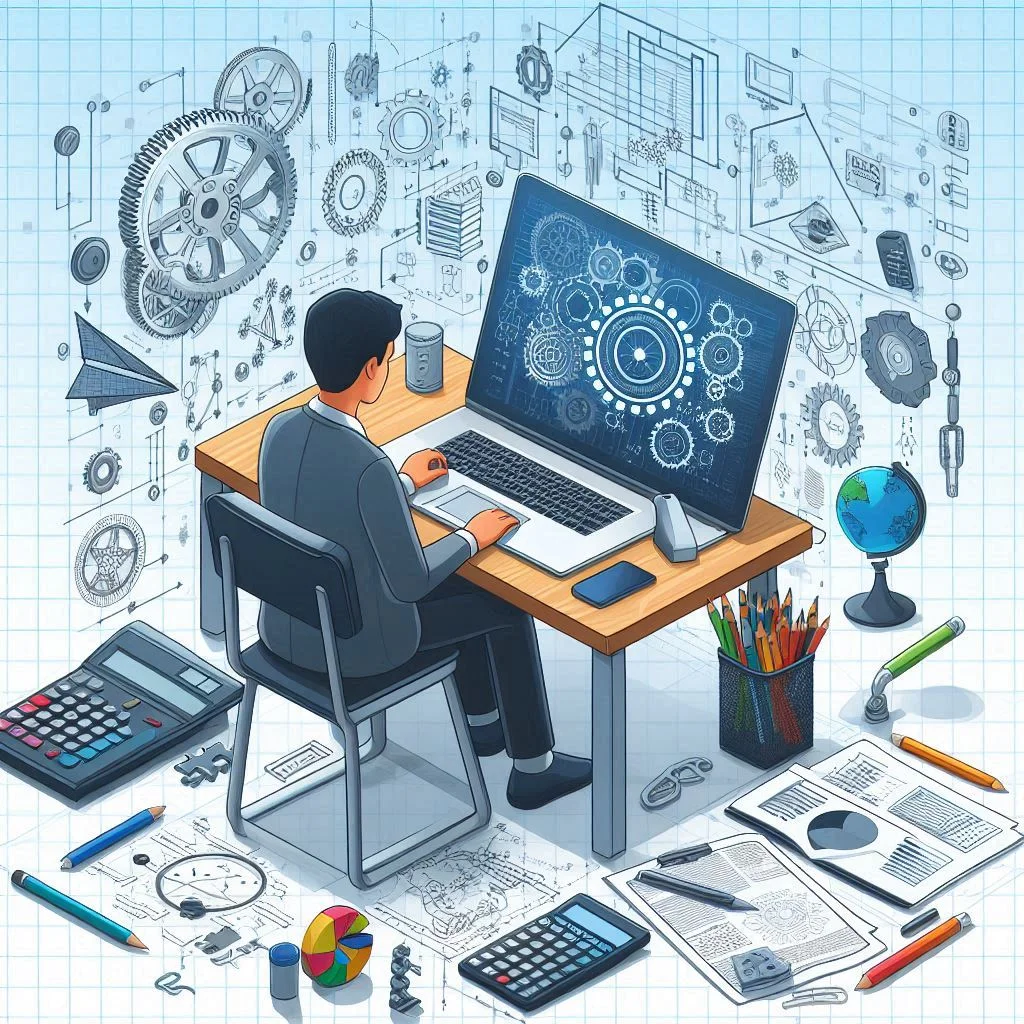
1. Coincident Mate:
- Aligns two planar surfaces to be on the same plane.
- Often used for flat surfaces, ensuring they are flush with each other.
2. Concentric Mate:
- Aligns the axes of two cylindrical or spherical features.
- Commonly used for holes and shafts to ensure they are aligned.
3. Distance Mate:
- Specifies a fixed distance between two entities.
- Useful for setting precise gaps or clearances between parts.
4. Angle Mate:
- Sets an angular relationship between two entities.
- Ideal for parts that need to be positioned at specific angles.
5. Perpendicular Mate:
- Ensures two entities are at a 90-degree angle to each other.
- Useful for components that must be aligned orthogonally.
6. Parallel Mate:
- Keeps two entities parallel to each other.
- Ensures that parts remain aligned along a common direction.
7. Tangent Mate:
- Ensures two entities remain in contact along their tangential surfaces.
- Useful for components with curved surfaces that must touch.
Each mate type is valid for specific combinations of geometry such as cones, cylinders, planes, and extrusions. For example, if you mate a cone to another cone, the valid types of mates you can use include coincident, concentric, and distance. Understanding these mates and when to use them is key to successful assembly design.
Creating a Faucet Subassembly
To illustrate the use of mates and positioning, let's create a faucet subassembly. This example involves assembling a faucet and its handle, showcasing the application of coincident and concentric mates.
Step-by-Step Process:
1. Open Components:
- Start by opening the faucet and handle components. These are the individual parts that will be assembled.
- Create a new assembly document in SolidWorks. This document will house the assembly of the faucet and handle.
2. Load the First Component:
- Begin with the faucet component since it remains fixed relative to other components.
- Drag the faucet component from the FeatureManager design tree into the assembly document (.sldasm).
- Align it with the assembly origin for proper orientation. This step is crucial as it anchors the faucet, ensuring that the planes in both the part and assembly documents are aligned.
3. Add Additional Components:
- Drag the handle components into the assembly document.
- Position the handles approximately where they will be fixed. In the example of the faucet subassembly, you will drag in two instances of the handle.
4. Positioning Components:
- Use the left mouse button to drag components closer to their desired positions.
- Right mouse button rotates components for proper orientation.
- Middle mouse button functions:
- Rotate all components.
- Pan all components with Ctrl.
- Zoom in/out with the mouse wheel.
Applying Mates for Accurate Positioning
Coincident Mate: To create a coincident mate between the handle component and the faucet component, you need to attach the flat bottom face of the handles to the flat top face of the faucet. This mate ensures that the two surfaces are flush with each other.
Steps to Apply a Coincident Mate:
- Select the flat bottom face of the handle component.
- Select the flat top face of the faucet component.
- Apply the coincident mate using the Mate tool in the Assembly toolbar.
When you apply the coincident mate, the faucet handle component moves closer to the faucet component. Note that you can still slide the handle anywhere along the top face of the faucet by dragging it with the left mouse button, indicating that a second mate is required to further define the position of the two components.
Concentric Mate: To further refine the positioning, you will apply a concentric mate. This mate aligns the axes of cylindrical features, such as the round face on the faucet handle and the round face on the faucet stem.
Steps to Apply a Concentric Mate:
- Select any round face on the faucet handle.
- Select the round face of the faucet stem (the portion of the component that slides into the countertop and connects to the supply pipe).
- Apply the concentric mate using the Mate tool.
Once you apply the concentric mate between the faucet handle component and the faucet component, you can no longer move the faucet handle along the top face of the faucet to shift its position. You can, however, use the left mouse button to drag the faucet handle on its axis.
Positioning the Components Precisely
After applying the mates, you may need to fine-tune the position of the handle on the faucet. This process involves ensuring that the handle is centered over the faucet stems and sits correctly on the faucet base.
Fine-Tuning the Position:
1. Zoom and Rotate:
- Use the middle mouse button to rotate the view and ensure you have a clear view of the relevant component areas.
- Zoom in to get a closer look at the mating faces.
2. Check Alignment:
- Verify that the handle is centered over the faucet stems. This ensures that the handle operates correctly when turned.
3. Adjust Mates if Necessary:
- If the handle is not perfectly aligned, you may need to adjust the mates.
- Reapply the coincident or concentric mate if the initial positioning was not accurate.
4. Use Reference Geometry:
- Utilize reference geometry such as planes, axes, or points to aid in precise positioning.
- For example, you can create a reference plane through the center of the faucet stem and the handle to ensure they are perfectly aligned.
Load Additional Components
In more complex assemblies, you may need to add additional components and mates. The process remains similar, with each new component being dragged into the assembly document and mated to existing components.
Steps to Load Additional Components:
1. Drag Components:
- Drag the additional components from the FeatureManager design tree into the assembly document.
- Position them approximately where they will be fixed.
2. Apply Mates:
- Use the Mate tool to create the necessary geometric relationships.
- For example, if adding a second handle, apply the coincident and concentric mates as before.
3. Check for Conflicts:
- Ensure that the new mates do not conflict with existing mates.
- Adjust the mates or component positions if conflicts arise.
4. Anchor Fixed Components:
- Ensure that the primary component (e.g., the faucet) remains anchored.
- Only moveable components (e.g., handles) should be adjusted.
Additional Tips for Successful Assemblies
Creating a successful assembly in SolidWorks requires attention to detail and a good understanding of the software's tools. Here are some additional tips to help you create accurate and functional assemblies:
1. Plan Your Assembly:
- Before starting, plan the assembly process. Identify which components will be fixed and which will move.
- Determine the necessary mates and their order of application.
2. Use Subassemblies:
- For complex projects, consider using subassemblies. This approach simplifies the main assembly by grouping related components.
- Subassemblies can be treated as single components in the main assembly, reducing the complexity.
3. Leverage Design Tables:
- Use design tables to manage configurations of parts and assemblies. This is especially useful for assemblies with multiple variations.
- Design tables allow you to easily switch between different configurations without manually adjusting mates.
4. Utilize Assembly Features:
- Assembly features, such as holes and cuts, can be added directly in the assembly document.
- This approach ensures that features are correctly positioned relative to multiple components.
5. Check for Interferences:
- Use the Interference Detection tool to check for overlaps or interferences between components.
- Resolve any interferences to ensure that the assembly operates smoothly.
6. Document Your Assembly:
- Create detailed assembly drawings to document the design. Include exploded views, part lists, and assembly instructions.
- Detailed documentation is crucial for manufacturing and assembly teams.
Conclusion
Creating assemblies in SolidWorks requires a solid understanding of mates and positioning techniques. By using mates effectively, you can precisely control the movement and orientation of components within an assembly. In this blog, we explored the process of creating a faucet subassembly, highlighting the use of coincident and concentric mates to achieve accurate positioning.
Remember, the key to successful assemblies is careful planning, attention to detail, and leveraging the powerful tools available in SolidWorks. Whether you are working on a simple subassembly or a complex project, following these steps and tips will help you create functional and accurate designs.