SolidWorks, a leading 3D CAD (Computer-Aided Design) software, is a powerful tool used by engineers and designers worldwide to create detailed and precise 3D models. Among its many features, assembly design plays a pivotal role in bringing complex designs to life. One of the key components of assembly design is the use of mates. Mates define how different components within an assembly relate to each other, and understanding them is crucial for any SolidWorks user.
In this extensive guide, we will delve into the world of mates, starting from the fundamental standard mates and progressing to the advanced and mechanical mates that SolidWorks offers. By the end of this journey, you will have a firm grasp on how to apply these mates effectively and efficiently in your projects. If you need assistance with your SolidWorks assignment, we are here to provide the help you require.
Standard Mates: Building Blocks of Assembly Design
SolidWorks provides a range of standard mates that are fundamental to assembly design. These mates define the basic relationships between components. Let's explore each one in detail:
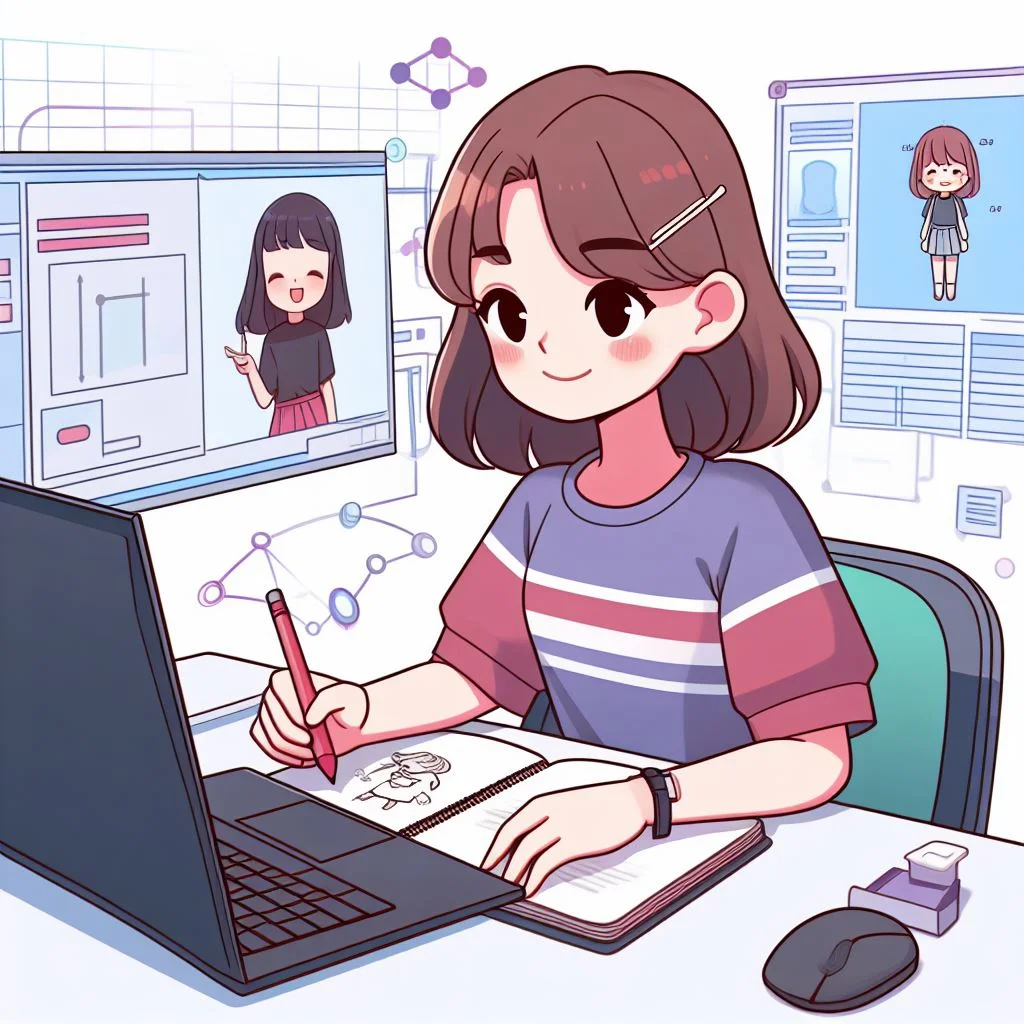
- Coincident Mate:The coincident mate aligns two faces, edges, or points of two components so that they share the same location in 3D space. It's particularly useful for connecting parts together accurately.
- Parallel Mate:The parallel mate aligns selected edges or faces of two components parallel to each other. This is handy when you need parts to be aligned but not necessarily touching.
- Perpendicular Mate:The perpendicular mate orients two components so that their selected edges or faces are perpendicular to each other. This is often used to create 90-degree connections between parts.
- Tangent Mate:The tangent mate establishes a tangent relationship between a cylindrical or conical face of one component and a curved face of another. This is essential for connecting parts like wheels to axles.
- Concentric Mate: The concentric mate aligns the axes of two cylindrical or conical faces, ensuring that they share the same center point. This is crucial for assembling rotating components.
- Lock Mate: The lock mate restricts the movement of components relative to each other. It essentially freezes a part in place, allowing no translation or rotation, which can be useful in certain design scenarios.
- Distance Mate:The distance mate sets a specific gap or distance between selected faces or edges of two components. This is helpful for ensuring components maintain a specific separation in an assembly.
- Angle Mate:The angle mate defines an angular relationship between two components. You can use it to control the orientation of parts relative to each other.
Advanced Mates: Enhancing Assembly Functionality
While standard mates are essential for basic assembly design, SolidWorks also offers a range of advanced mates to provide more complex and sophisticated relationships between components. Here's an overview of these advanced mates:
1. Symmetric Mate: The Symmetric Mate in SolidWorks is a versatile tool that allows designers to create balanced and symmetric assemblies with ease. It is often used to establish symmetry between two components, ensuring that parts are positioned symmetrically relative to an axis or plane. This mate is invaluable when you want to achieve aesthetic and functional balance in your designs.
Imagine you are designing a vehicle's chassis, and you want to ensure that the suspension components on both sides are symmetrical. By applying the Symmetric Mate, you can position the suspension components in such a way that they are mirror images of each other, resulting in a balanced and visually pleasing design. This mate not only streamlines the modeling process but also ensures that your assembly maintains its symmetry, which can be crucial for manufacturing and performance.
2. Width Mate:The Width Mate in SolidWorks is a practical mate used to align the faces of two components along their widths. This mate is particularly useful when you need to ensure that parts maintain a specified distance apart while allowing for width adjustments. It provides the flexibility to control the distance between components without being restricted to specific points or edges.
Suppose you are designing a shelving unit with adjustable shelves. By applying the Width Mate, you can easily adjust the distance between the shelves, allowing for different-sized objects to be stored on each shelf. This mate ensures that your design is not only functional but also adaptable to various requirements, making it a valuable tool for creating user-friendly and versatile assemblies.
3. Path Mate:The Path Mate is a remarkable feature in SolidWorks that allows components to follow a specified path or curve within an assembly. This mate is essential when designing mechanisms that require precise movement along predefined trajectories. Path Mates are commonly employed in applications such as conveyor belts, robotic arms, or even complex packaging machinery.
For instance, if you are designing a robotic arm for pick-and-place operations, the Path Mate enables you to specify the precise path the end-effector should follow. This results in accurate and predictable movements, ensuring that your robotic arm functions flawlessly in industrial automation. The Path Mate provides both realism and functionality, crucial for any designer working on complex, motion-based systems.
4. Linear/Linear Coupler Mate:The Linear/Linear Coupler Mate is a valuable tool for modeling linear motion relationships between components in SolidWorks. This mate is particularly handy for simulating linear actuation or motion, which is often seen in various applications, including drawer slides, telescopic mechanisms, or linear actuators.
Consider designing an extendable ladder. The Linear/Linear Coupler Mate allows you to precisely control the extension and retraction of ladder segments, mimicking real-world behavior. By defining the linear relationship, you ensure that the ladder functions smoothly, locks securely in place, and retracts with ease. This mate simplifies the design process while guaranteeing the accuracy of the mechanism's operation.
5. Limit Mate:The Limit Mate is a mate that adds movement limits to components within a SolidWorks assembly. This feature is invaluable for accurately modeling real-world mechanical constraints. It allows you to restrict the range of motion of components, preventing them from moving beyond specified limits.
Let's say you are working on a wheel assembly for a vehicle. With the Limit Mate, you can set limits on the wheel's rotation, ensuring that it only turns within a specific range. This mate is also crucial for modeling hydraulic or pneumatic systems, where the extension and retraction of components must be controlled precisely. By implementing the Limit Mate, you can guarantee that your design adheres to real-world constraints, enhancing both safety and functionality.
These advanced mates in SolidWorks, including Symmetric Mate, Width Mate, Path Mate, Linear/Linear Coupler Mate, and Limit Mate, empower designers to create highly sophisticated and functional assemblies. By using these mates effectively, you can achieve symmetry, control the distance between components, define complex motion paths, simulate linear motion, and apply real-world movement constraints. These tools not only streamline the design process but also enable you to create realistic, precise, and adaptable assemblies that meet the demands of your engineering projects.
Mechanical Mates: Creating Realistic Mechanical Assemblies
In the world of mechanical design and engineering, the devil is in the details. When it comes to modeling intricate mechanical systems in SolidWorks, the software offers a set of specialized mates known as mechanical mates. These mates allow you to accurately represent the behavior of various mechanical components, resulting in realistic, functional, and highly detailed assemblies. Let's explore these mechanical mates and understand how they can be effectively applied in your projects.
1. Cam Mate: The Cam Mate is a remarkable tool in SolidWorks that allows you to simulate the interaction between a cam and a follower. In real-world applications, cams are often used in engines, printers, industrial machinery, and a wide array of devices to convert rotary motion into reciprocating or oscillatory motion. The Cam Mate within SolidWorks replicates this intricate motion by defining the cam profile and the follower's response.
For instance, when designing a piston-driven engine, you can use the Cam Mate to accurately model the movement of the piston as it follows the contour of the camshaft. This level of detail is crucial for precise kinematic analysis and for ensuring that the components in your assembly function as they would in reality.
2. Hinge Mate:The Hinge Mate in SolidWorks is designed to mimic the behavior of a hinge. This mate is indispensable when you need components to rotate freely around a specified axis, just like a door or lid in the real world. Hinge Mates are commonly used in a wide range of applications, from designing doors and lids to simulating the motion of articulated mechanical arms or joints.
Imagine you are designing a cabinet with doors that need to swing open and closed. By employing the Hinge Mate, you can easily specify the axis around which the doors rotate, allowing them to move realistically, giving your design that authentic touch.
3. Gear Mate:Gears are ubiquitous in mechanical systems, serving as a means to transmit motion and power between rotating components. The Gear Mate in SolidWorks empowers you to accurately model the interaction between gears in your assemblies. This mate allows you to define crucial parameters such as gear ratio, backlash, and pitch diameter, making it possible to create highly realistic gear systems.
When designing a gearbox for a machine, for example, the Gear Mate helps you ensure that the gears mesh correctly, transmit motion with the desired ratio, and respond to one another's movements as they would in the physical world. It's an essential tool for achieving precision in gear-driven systems.
4. Rack Pinion Mate: The Rack and Pinion Mate in SolidWorks simulates the motion of a rack and pinion gear meshing together. This is particularly useful in applications where linear motion needs to be converted into rotary motion or vice versa. Common applications include CNC (Computer Numerical Control) machines, where the rotation of a motor needs to be translated into precise linear movement, or steering systems in vehicles.
By employing the Rack and Pinion Mate, you can accurately replicate the behavior of these components, ensuring that they move in harmony and respond to the input motion as expected, making your designs both functional and true to reality.
5. Screw Mate:Screws, nuts, and bolts are fundamental components in mechanical assemblies, used to join parts together, provide adjustability, or create linear motion. The Screw Mate in SolidWorks allows you to model the movement of threaded components accurately. It's an essential mate for designing assemblies that involve threaded connections.
For example, in the construction of a vice, you can use the Screw Mate to simulate the turning of the vice handle, causing the threaded screw to move and exert pressure on the workpiece. This level of detail is vital for ensuring that your designs not only fit together but also operate realistically.
6. Universal Joint Mate: Universal joints, also known as Cardan joints, are used to transmit rotational motion between non-aligned shafts. They are commonly found in drive shafts of vehicles and machinery. The Universal Joint Mate in SolidWorks replicates the complex, non-linear motion of these joints, allowing you to accurately model their behavior.
In an automotive context, the Universal Joint Mate can be used to design the drive shaft that connects the transmission to the wheels. By applying this mate, you can ensure that the drive shaft accommodates the variations in angles and positions between the transmission and the wheels, allowing for smooth and efficient power transmission.
SolidWorks' mechanical mates are invaluable for creating realistic mechanical assemblies that accurately mimic the behavior of real-world components. Whether you're designing engines, gear systems, doors, or any other intricate mechanical system, these mates empower you to model the precise interactions and movements required for your project. By leveraging these advanced features, your SolidWorks designs will not only look true to life but also function with the precision and realism needed for successful engineering projects. So, next time you embark on a mechanical design project, remember that SolidWorks' mechanical mates are your go-to tools for creating exceptional, true-to-life assemblies.
Conclusion:
SolidWorks mates are the backbone of assembly design, allowing you to define the relationships between components and create intricate 3D models. By mastering standard mates, advanced mates, and mechanical mates, you gain the capability to design a wide range of assemblies, from simple structures to complex mechanical systems.
Whether you're a student working on SolidWorks assignments or a professional engineer designing real-world products, understanding and effectively applying these mates will significantly enhance your design capabilities and improve your efficiency. So, start experimenting with mates in your next SolidWorks project and watch your design skills soar to new heights. SolidWorks' powerful mate tools will undoubtedly be your key to success in the world of 3D modeling and assembly design.