- Step 1: Creating the Base Feature with an Extrude
- 1. Start a New Sketch
- 2. Extrude the Sketch
- Step 2: Adding an Extrude to the Base
- 1. Convert Entities
- 2. Extrude the Sketch
- Step 3: Removing Material with the Cut-Extrude
- 1. Create a Cut-Extrude Sketch
- 2. Cut-Extrude the Sketch
- Step 4: Creating the Sink with a Loft
- 1. Sketch the Bottom Profile
- 2. Use the Loft Tool
- Step 5: Hollowing the Sink with the Shell Tool
- 1. Select the Shell Tool
- 2. Set the Shell Parameters
- Step 6: Rounding Edges with Fillets
- 1. Apply Fillets
- 2. Finalize the Design
- Conclusion
Creating a countertop with an integrated sink in SolidWorks is an excellent exercise to familiarize yourself with various essential modeling techniques. This tutorial will guide you step-by-step through the process, ensuring you understand each tool and technique along the way. By leveraging SolidWorks Assignment Help, you'll gain a deeper understanding of how to effectively use tools like extrudes, cut-extrudes, lofts, shells, and fillets to craft a detailed and functional countertop model. This practical exercise is designed not only to enhance your modeling skills but also to prepare you for more complex projects. As you follow along, you’ll see how each feature contributes to the overall design, making it an invaluable experience for anyone seeking 3D Modeling Assignment Help. By the end of this tutorial, you’ll have a comprehensive understanding of these tools and how to apply them in your projects, setting a solid foundation for advanced modeling techniques.
SolidWorks is a powerful 3D CAD software that allows you to create complex designs with precision. Whether you’re a beginner or an experienced user, mastering fundamental tools is crucial for developing efficient and effective modeling practices. In this tutorial, we will use several core SolidWorks tools to design a functional countertop with an integrated sink, including Extrude, Cut-Extrude, Loft, Shell, and Fillet.
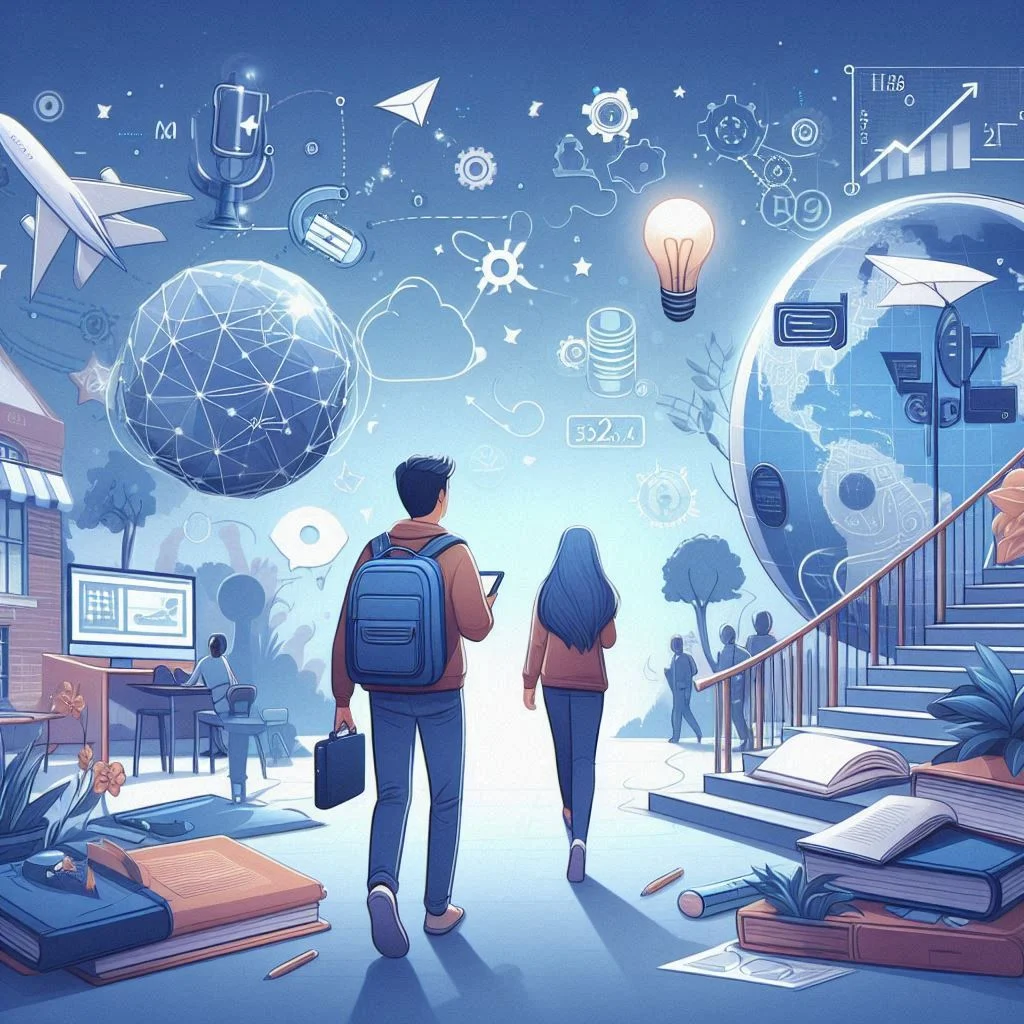
Step 1: Creating the Base Feature with an Extrude
Begin by setting up a solid foundation for your countertop design. By sketching a 2D rectangle and extruding it, you establish the main body of your countertop. This initial extrusion creates a 3D base that forms the starting point for further modifications. Precision in this step ensures that subsequent features, like additional extrusions or cutouts, align perfectly. Always verify dimensions and sketch accuracy to ensure a robust and error-free model as you progress with the design.
1. Start a New Sketch
- Open a New Part File: Launch SolidWorks and create a new part document. This will be the workspace where you build your countertop.
- Create a Sketch on the Top Plane: Begin by selecting the Top Plane from the Feature Manager Design Tree. Click on the Sketch tab and then select Sketch to start a new 2D sketch on this plane.
- Draw the Rectangle: Use the Rectangle tool to draw a rectangle starting at the origin (0,0). The dimensions for this rectangle should be 600mm x 580mm. This represents the top view of the countertop.
- Dimension the Sketch: After drawing the rectangle, use the Smart Dimention tool to set the dimensions. Click on each edge of the rectangle and enter the respective values (600mm and 580mm). Ensuring your sketch is fully dimensioned and defined is crucial for accurate extruding.
2. Extrude the Sketch
- Select the Extrude Tool: With the rectangle sketch active, navigate to the Features tab and select Extruded Boss/Base. This tool will convert your 2D sketch into a 3D feature.
- Set the Extrude Parameters: In the Extrude menu, set the extrusion depth to 34mm. This creates the initial base feature of your countertop, providing the necessary thickness.
- Confirm the Extrude Operation: Click OK or Check Mark to complete the extrusion. Your countertop base is now a solid 3D feature, which will serve as the foundation for further modifications.
Step 2: Adding an Extrude to the Base
To enhance the base feature, the additional extrusion plays a crucial role in defining the countertop's edges and overall shape. By projecting existing geometry onto a new sketch using the Convert Entities tool, you ensure that the added material aligns perfectly with the base. This approach maintains consistency in your design and simplifies the creation of detailed features. Properly executing this step will contribute significantly to the precision and functionality of the final countertop model.
1. Convert Entities
- Start a New Sketch: Select the top face of your extruded base feature and start a new sketch on this face.
- Use the Convert Entities Tool: Go to the Sketch tab and click on Convert Entities. This tool allows you to project existing edges of the base feature onto the new sketch plane, making it easier to add details that align with the base geometry.
- Select the Edges: In the Convert Entities dialog, select the left and upper edges of the base rectangle. These projected edges will help you create a consistent design when you extrude additional features.
2. Extrude the Sketch
- Create the New Extrude: With the converted entities sketch active, go back to the Features tab and select Extruded Boss/Base.
- Set the Parameters: Define the depth of the new extrusion to add material to the edges of the countertop. Adjust the parameters as needed to achieve the desired shape and size of the countertop edges.
- Confirm the Operation: Click OK or Check Mark to finalize the extrusion. You have now added additional material to enhance the edges of your countertop.
Step 3: Removing Material with the Cut-Extrude
Removing material with the Cut-Extrude tool is essential for creating precise openings and complex features in your model. By defining a 2D sketch that represents the desired cut, you ensure that the removal process is accurate and aligned with your design specifications. The Cut-Extrude tool operates by projecting the sketch through the part, effectively carving out the material. This approach is particularly useful for integrating components like sinks, where precise cutouts are critical for both functionality and aesthetics.
1. Create a Cut-Extrude Sketch
- Start a New Sketch: Select the top face of the countertop where the sink will be located. Start a new sketch on this face.
- Draw the Sink Cutout: Use the Ellipse tool to draw an oblong shape that represents the sink cutout. This shape will define the opening where the sink will be located.
- Dimension the Sketch: Add dimensions to the ellipse to ensure it fits the desired sink size and shape. Accurate dimensions are crucial for a well-fitting sink.
2. Cut-Extrude the Sketch
- Select the Cut-Extrude Tool: With the ellipse sketch active, go to the Features tab and select Extruded Cut. This tool will remove material from the countertop based on your sketch.
- Set the Cut Parameters: Define the depth of the cut to create the opening for the sink. Make sure the cut is deep enough to accommodate the sink.
- Confirm the Operation: Click OK or Check Mark to complete the cut-extrude. Your countertop should now have an opening for the sink.
Step 4: Creating the Sink with a Loft
To create a realistic sink, start by accurately defining the profiles for lofting. The Loft tool connects two different sketches, such as the elliptical bottom and the circular top, seamlessly transitioning between them. Ensure that the sketches are well-defined and positioned correctly on their respective planes to avoid errors. The Loft tool offers a shaded preview to help visualize the transition before finalizing. This step is crucial for achieving the correct sink shape and smooth surface.
1. Sketch the Bottom Profile
- Convert Entities for Sink Profile: Use the Convert Entities tool to project the ellipse from the sink cutout onto the bottom face of the countertop. This will serve as the bottom profile for the sink.
- Create a New Plane: To define the sink depth, create an offset plane (Plane1) from the Top Plane. Go to Features > Reference Geometry > Plane, and set the offset distance according to the sink’s depth.
- Sketch the Top Profile: On Plane1, start a new sketch and use the Circle tool to draw a circle. This circle represents the top profile of the sink.
2. Use the Loft Tool
- Select the Loft Tool: With both sketches (ellipse on the bottom and circle on the new plane) created, go to the Features tab and select Lofted Boss/Base.
- Define the Loft Parameters: Choose the ellipse and circle sketches as the profiles to loft between. The Loft tool will create a smooth transition between the two profiles, forming the shape of the sink.
- Preview and Confirm: SolidWorks will display a shaded preview of the lofted feature. Ensure the preview matches your expectations, then confirm the loft operation.
Step 5: Hollowing the Sink with the Shell Tool
The Shell tool is essential for creating a hollow cavity within your model, particularly useful for features like sinks where material needs to be removed from the interior while maintaining a consistent wall thickness. By using the Shell tool, you can efficiently hollow out the sink and remove the top face in one operation. This not only saves time but also ensures that the walls of the sink are uniformly thick, providing structural integrity and a realistic appearance.
1. Select the Shell Tool
- Activate the Shell Tool: With the sink feature created, go to the Features tab and select Shell. This tool will hollow out the sink, leaving a thin wall thickness.
- Select the Top Face: Click on the top face of the sink to remove it. This step will open the sink cavity and define the shell's thickness.
2. Set the Shell Parameters
- Define the Wall Thickness: Enter the desired wall thickness for the sink. This will hollow out the sink while maintaining a solid structure.
- Confirm the Shell Operation: Click OK or Check Mark to complete the shell operation. The sink is now hollowed out, with the top face removed.
Step 6: Rounding Edges with Fillets
Adding fillets to your design enhances both the aesthetics and functionality of your model. Smooth, rounded edges not only improve the visual appeal but also eliminate sharp corners that could be prone to wear or injury. In practical terms, fillets can also aid in the manufacturing process by reducing stress concentrations and improving the flow of materials during production. This step is crucial for creating a polished, professional-looking final product, ensuring both form and function are optimized.
1. Apply Fillets
- Select the Fillet Tool: Go to the Features tab and select Fillet. This tool will round off sharp edges on your model.
- Choose the Edges: Select the edges of the countertop and sink where you want to apply fillets. These are the areas where you want to smooth out sharp transitions.
- Set the Fillet Radius: Define the radius for the fillet. A larger radius will create a smoother, more rounded edge, while a smaller radius will produce a tighter curve.
2. Finalize the Design
- Review the Model: Rotate and inspect your model to ensure that all edges are appropriately rounded. Check for any inconsistencies or areas that need adjustment.
- Adjust Fillet Parameters: If needed, modify the fillet radius or apply additional fillets to achieve the desired appearance.
Conclusion
Designing a countertop with an integrated sink in SolidWorks involves a series of methodical steps and the use of key modeling tools. By following this comprehensive guide, you’ve learned how to effectively use the Extrude, Cut-Extrude, Loft, Shell, and Fillet tools to create a detailed and functional 3D model.
Each step in the process builds upon the previous one, from establishing the base feature to hollowing out the sink and rounding edges. Mastering these techniques not only enhances your SolidWorks skills but also prepares you for more complex modeling challenges.
Feel free to revisit any step or tool as needed, and remember that practice is key to becoming proficient in SolidWorks. Happy modeling, and good luck with your assignments!