- Introduction to SolidWorks Simulation
- Understanding Study Cases in SolidWorks Simulation
- 1. Virtual Wall
- 2. Bonded
- 3. Pin Connect
- Methodology for Solving SolidWorks Simulation Study Cases
- Step 1: Setting Up the Study
- Step 2: Applying Loads
- Step 3: Running the Simulation
- Step 4: Analyzing Results
- Interpreting Results from SolidWorks Simulation
- Case Studies and Results
- Recommendations
- Recommendations for Practical Applications
- Future Work and Advanced Studies
- Conclusion
SolidWorks Simulation is indeed a cornerstone tool for engineers, offering the capability to foresee and evaluate real-world behaviors of products without physical prototypes. By employing SolidWorks Simulation, engineers can meticulously analyze structural responses under diverse operating conditions, ensuring designs meet performance expectations and regulatory standards from the outset of development. This software integrates Finite Element Analysis (FEA) to simulate the complex interactions between components, providing insights into stress distribution, deformation tendencies, and critical failure points. Mastering SolidWorks Simulation is essential for effectively analyzing and optimizing engineering designs through advanced Finite Element Analysis techniques.
In this guide, we delve into several pivotal SolidWorks Simulation study cases, each tailored to replicate specific mechanical scenarios with precision. These cases—such as virtual wall, bonded, and pin connect—serve as fundamental building blocks for understanding structural dynamics and optimizing designs for various applications. Through a systematic approach encompassing geometry preparation, material definition, boundary conditions, and rigorous analysis of simulation results, engineers can derive actionable insights to refine and enhance product performance.
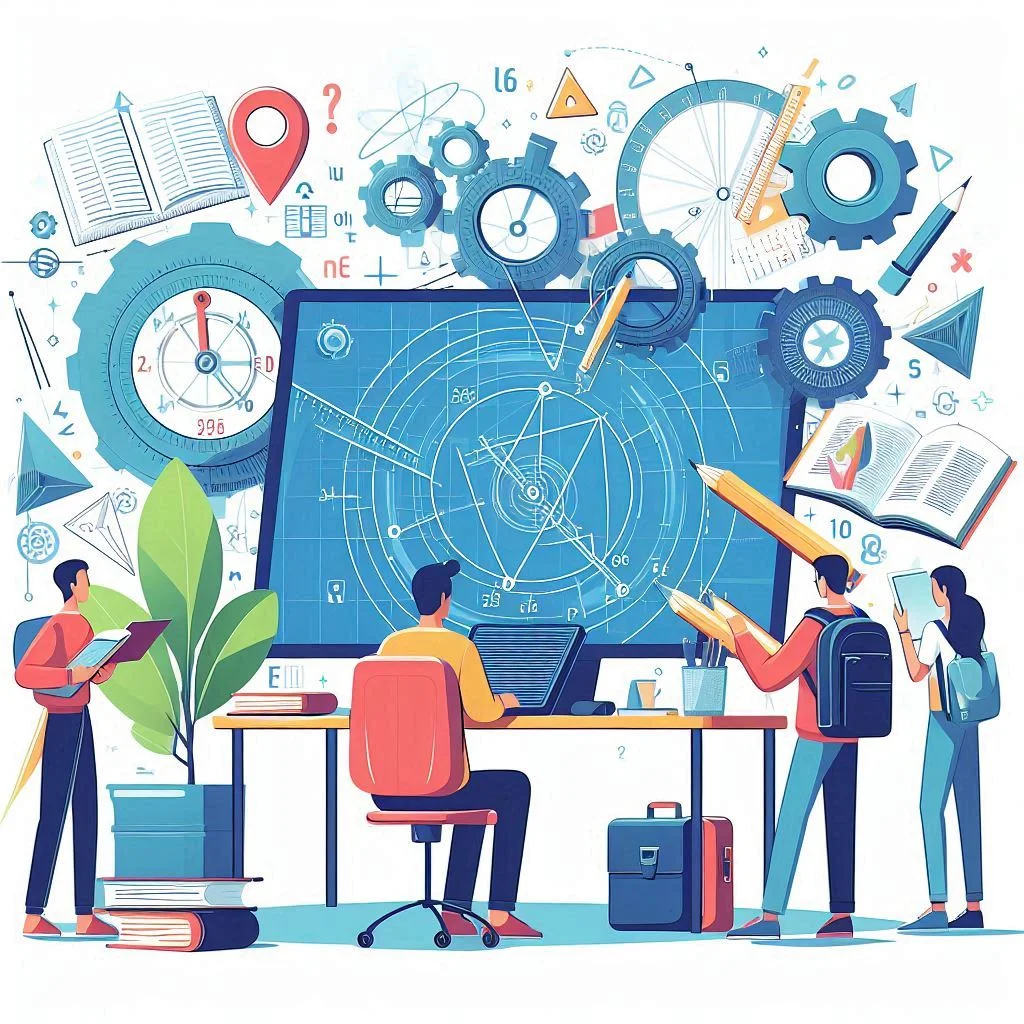
SolidWorks Simulation empowers engineers to iterate and fine-tune designs virtually, thereby reducing the time and costs associated with physical prototyping. By mastering these simulation study cases and leveraging advanced analysis tools, engineers can confidently navigate complex design challenges and deliver innovative solutions that excel in reliability and efficiency.
Introduction to SolidWorks Simulation
SolidWorks Simulation empowers engineers by providing a virtual testing environment where they can simulate and analyze the behavior of designs under varying mechanical conditions. Utilizing Finite Element Analysis (FEA), this tool calculates intricate details such as stresses and displacements within structures. By doing so, engineers can gain invaluable insights into how their designs will perform in real-world scenarios before physical prototypes are manufactured.
This predictive capability is instrumental in optimizing designs for enhanced strength, durability, and overall performance. Engineers can iteratively refine their designs based on simulation results, ensuring that potential issues are identified and resolved early in the development process. SolidWorks Simulation thus accelerates innovation while reducing costs associated with physical testing and iterations, making it an indispensable tool in modern engineering practices.
Understanding Study Cases in SolidWorks Simulation
SolidWorks Simulation offers several types of study cases, each tailored to simulate specific mechanical scenarios. These simulations are crucial for understanding how different constraints and interactions affect the performance and integrity of designs under various conditions. Whether it's simulating a rigid virtual wall to prevent movement, using bonded contacts to allow limited rotational freedom, or employing pin connectors for controlled linear motion, SolidWorks Simulation provides engineers with the flexibility to accurately model real-world behaviors. This versatility ensures that designs can be thoroughly tested and optimized before physical manufacturing, thereby reducing costs and time-to-market while enhancing overall product quality and reliability. These include:
1. Virtual Wall
- Description: In this case, the structure is constrained by a virtual wall, which acts as a rigid boundary that the structure cannot penetrate.
- Application: Used when a component or structure needs to be fixed in a specific position without any freedom to move or rotate.
2. Bonded
- Description: Here, two components are bonded together, meaning they cannot separate or move relative to each other, but rotation is allowed.
- Application: Suitable for assemblies where parts need to maintain positional alignment while allowing rotational movement.
3. Pin Connect
- Description: In this case, two components are connected by a pin, allowing translation along the pin axis but preventing relative rotation.
- Application: Useful for designs requiring linear movement while maintaining fixed orientation relative to another part.
Methodology for Solving SolidWorks Simulation Study Cases
To effectively simulate and analyze these study cases in SolidWorks Simulation, meticulous attention to detail during setup is crucial. Begin by ensuring the 3D CAD model accurately represents the physical structure or assembly to be analyzed. Define material properties meticulously, including Young's Modulus, Poisson's ratio, and density, to ensure simulation fidelity. Apply restraints meticulously according to the chosen study case—whether virtual wall, bonded, or pin connect—ensuring they accurately replicate real-world constraints. This careful setup ensures the simulation generates meaningful results that reflect the actual behavior of the design under specified conditions, follow these steps:
Step 1: Setting Up the Study
- Geometry Preparation: Import or create the 3D CAD model of the structure or assembly to be analyzed.
- Material Definition: Specify material properties such as Young's Modulus, Poisson's ratio, and density for accurate simulation results.
- Restraints Application: Depending on the study case (virtual wall, bonded, pin connect), apply appropriate restraints to simulate real-world boundary conditions effectively.
Step 2: Applying Loads
- Load Definition: Define the type, magnitude, and direction of loads acting on the structure or assembly. This could include forces, pressures, torques, or gravity.
- Boundary Conditions: Ensure that all necessary boundary conditions are applied correctly to represent the actual operating environment of the design.
Step 3: Running the Simulation
- Solver Execution: Run the simulation to compute results such as displacements, stresses, strains, and factor of safety.
- Convergence Checking: Verify that the solution has converged adequately for accurate results.
Step 4: Analyzing Results
- Post-Processing: Review and interpret simulation results using SolidWorks Simulation's post-processing tools.
- Result Evaluation: Analyze maximum deformation, stress distribution, and any other relevant outputs based on the study case parameters.
Interpreting Results from SolidWorks Simulation
Upon completing the simulation, interpret the results to understand the behavior of the structure under the simulated conditions:
- Deformation Analysis: Evaluate how much the structure displaces under the applied load or constraint. Lower deformations may indicate stiffer designs capable of maintaining shape integrity under load. This analysis helps in determining if the design meets dimensional tolerances and functional requirements without excessive deformation.
- Stress Analysis: Examine stress concentrations throughout the structure to pinpoint potential failure points or areas where material may yield. High stress areas can indicate where modifications or reinforcements are necessary to ensure structural reliability and longevity. Understanding stress distribution aids in optimizing material usage and design configurations to enhance overall performance and durability under operational conditions.
Case Studies and Results
Let's consider typical results from three SolidWorks Simulation study cases:
Case Maximum Deformation (mm) Maximum Stress (N/m^2)
Virtual Wall 0.000 7.197e+008
Bonded 4.429e+000 4.288e+008
Pin Connect 4.352e+000 7.253e+008
Recommendations
Based on the results obtained from the simulation study cases:
- Virtual Wall Case: The minimal deformation observed in the virtual wall case is attributed to the rigid constraint that prohibits any translational or rotational movement of the structure. This constraint leads to the highest stress concentrations within the material, as the forces applied cannot dissipate through movement, resulting in localized high stress areas.
- Bonded Case: In contrast to the virtual wall case, the bonded condition allows some rotational freedom while preventing translational movement between components. This results in moderate deformation across the structure, as the rotational degrees of freedom enable some stress relief. However, the stress distribution in the bonded case differs from that of the virtual wall, as the structure is permitted to redistribute forces internally due to rotational flexibility.
- Pin Connect Case: Similar to the bonded case, the pin connect condition allows for translational movement along a defined axis while restricting rotational movement. This leads to deformation patterns comparable to the bonded case. However, similar stress patterns to the virtual wall case emerge due to the constraint on rotational freedom, causing stress concentrations where movement is restricted.
These distinctions underscore the importance of selecting the appropriate study case based on project requirements to balance deformation and stress considerations effectively. Each condition offers unique advantages depending on the desired structural behavior and operational constraints of the design.
Recommendations for Practical Applications
- Optimal Case Selection: Choose the appropriate contact type based on specific project requirements to balance between deformation and stress. For instance, if minimal deformation is critical but high stress tolerance is acceptable, consider using the virtual wall contact. Conversely, for applications where some deformation is permissible, but stress must be minimized, the bonded or pin connect options may be more suitable.
- Further Studies: Explore detailed stress distribution, parameter sensitivity, and the effect of varying loading conditions to refine analysis accuracy. Conducting detailed studies on stress distribution will provide insights into localized areas of concern within the structure. Additionally, sensitivity analysis on parameters like mesh density, material properties adjustments, and contact definitions can optimize simulation accuracy. Investigating different loading conditions will enhance understanding of how the structure responds under diverse operational scenarios, contributing to robust design validation and performance prediction.
These recommendations aim to empower engineers in making informed decisions during the design and simulation process, ensuring that designs meet performance criteria while minimizing risks and potential failures.
Future Work and Advanced Studies
To enhance simulation accuracy and broaden understanding, consider the following areas for future exploration:
- Detailed Stress Distribution: Investigate stress concentrations and distribution patterns within the structure to pinpoint critical areas prone to failure under specific loading conditions. Understanding these patterns helps in refining design modifications and improving structural reliability.
- Parameter Sensitivity Analysis: Study the impact of changing simulation parameters such as mesh density, material properties (like yield strength variations), and contact definitions (including friction coefficients). This analysis provides insights into how sensitive the design is to these parameters, guiding engineers in optimizing design choices for performance and cost-effectiveness.
- Loading Condition Variations: Analyze how different types, magnitudes, and positions of loads affect structural behavior and performance. By simulating various loading scenarios, engineers can assess the design's robustness under realistic operational conditions, ensuring it meets safety and performance standards across a range of use cases.
Conclusion
SolidWorks Simulation stands as an indispensable tool for engineers aiming to optimize designs and accurately predict product performance. Through mastery of simulation study cases and adherence to a systematic approach, engineers gain the ability to thoroughly analyze structural behavior, ensure reliability under diverse conditions, and expedite the design iteration process.
This guide provides a comprehensive framework, equipping you with the essential knowledge and methodology to leverage SolidWorks Simulation effectively across various engineering applications. Whether you're tasked with validating a new product design, optimizing existing structures, or conducting in-depth performance assessments, SolidWorks Simulation empowers you to make informed decisions with confidence.
For personalized guidance or detailed project inquiries, consider consulting with experts or accessing specialized resources such as SolidWorksAssignmentHelp.com. These avenues offer tailored support to navigate complex simulation scenarios and extract maximum value from the software's capabilities.
By integrating SolidWorks Simulation into your design workflow, you can achieve robust and efficient designs while minimizing the need for costly physical prototypes. Embrace these tools today to foster innovation, elevate engineering standards, and propel your projects toward success in an ever-evolving technological landscape.