- Understanding the Assignment
- Project Overview:
- Key Constraints:
- Planning Your Approach
- Initial Research:
- Setting Design Parameters:
- SolidWorks Tools and Techniques
- CAD Modeling:
- Simulation and Analysis:
- Iterative Design Process
- Prototyping:
- Feedback Integration:
- Documentation and Presentation
- Technical Documentation:
- Presentation Skills:
- Tips for Success
- Time Management:
- Collaboration:
- Resource Utilization:
- Conclusion
Designing components for high-performance vehicles like Indy racecars requires more than just technical prowess in Solidworks; it demands a deep understanding of aerodynamics, structural engineering, and efficient project management. In this comprehensive guide, we'll explore how you can approach and excel in complex Solidworks assignments, using the hypothetical Indy racecar wing design project as a model.
Solidworks proficiency is crucial not only for CAD modeling assignment help but also for integrating theoretical knowledge with practical application. Engineers tasked with such projects must design visually appealing models that meet rigorous performance criteria, considering factors like airflow dynamics, material strength, and structural integrity to optimize vehicle performance.
These assignments simulate real-world scenarios where engineers must optimize designs within specific constraints and deadlines, balancing aerodynamic efficiency with structural robustness through collaboration in multidisciplinary teams. This iterative process refines the final product, enhancing problem-solving and critical thinking skills crucial for professional engineering practice.
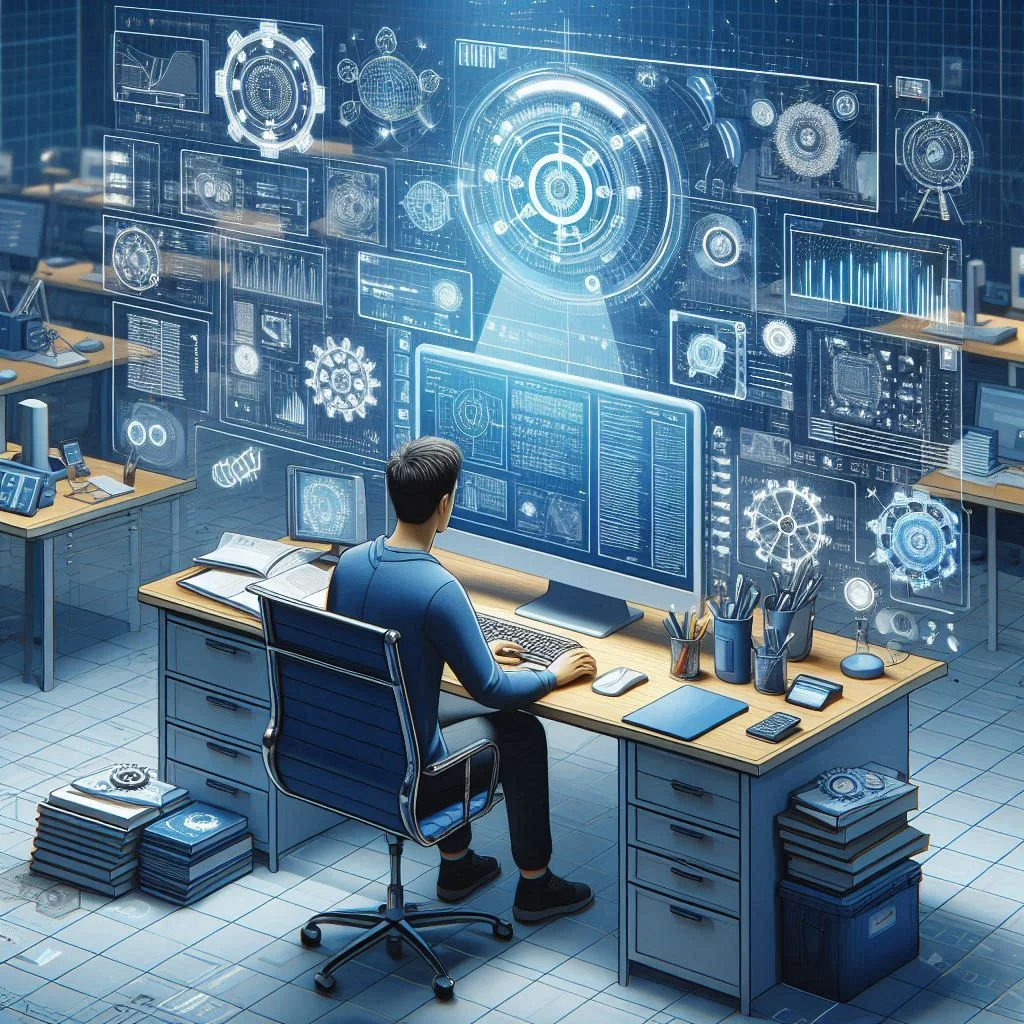
Mastering Solidworks through projects like the Indy racecar wing design not only enhances technical proficiency but also cultivates a holistic understanding of engineering principles. This hands-on experience prepares students for careers where innovation and efficiency are essential, equipping them to tackle real-world engineering challenges with confidence.
Understanding the Assignment
Understanding the assignment involves grasping its multifaceted demands beyond mere technical execution. It requires delving into the intricacies of aerodynamics and structural engineering while navigating stringent constraints. The Indy racecar wing design project, for instance, challenges students to balance the aerodynamic efficiency necessary for competitive racing with practical considerations like material selection and manufacturing feasibility. By immersing themselves in the project's requirements, students cultivate not only technical skills but also critical thinking and problem-solving abilities essential for real-world engineering challenges. This holistic approach ensures that designs not only meet performance criteria but also integrate seamlessly into broader project objectives and constraints.
Project Overview:
The Indy racecar wing design project involves creating a rear-mounted wing that maximizes downforce (negative lift) while minimizing drag and additional weight. Teams typically consist of two members—an aerodynamicist and a structural engineer—who collaborate to conceive, design, prototype, and test their wing designs over a specified period.
Key Constraints:
- Design envelope: 20” x 20” x 40” (width x height x span)
- Material options: Aluminum 6061 plate (0.125" or 0.25" thick)
- Attachment methods: Epoxy, possible fiberglass reinforcement
- Performance criteria: Maximize downforce, minimize drag, optimize weight
Planning Your Approach
Before diving into Solidworks, conduct thorough research on aerodynamic principles relevant to racecar design. Understand how wing shapes, angles, and materials impact performance metrics like downforce and drag. Familiarize yourself with previous designs and case studies to glean insights into effective design strategies. Once you have a solid theoretical foundation, outline clear design parameters based on project requirements and constraints using Solidworks. Define the 2D wing sections and 3D support structures within the specified dimensions. This initial setup will guide your modeling and simulation efforts, ensuring your designs are both innovative and technically sound.
Initial Research:
Before diving into SolidWorks, conduct thorough research on aerodynamic principles relevant to racecar design. Understand how wing shapes, angles, and materials impact performance metrics like downforce and drag. Familiarize yourself with previous designs and case studies to glean insights into effective design strategies.
Setting Design Parameters:
Use SolidWorks to establish clear design parameters based on project requirements and constraints. Define the 2D wing sections and 3D support structures within the specified dimensions. This initial setup will guide your modeling and simulation efforts.
SolidWorks Tools and Techniques
SolidWorks provides a robust suite of tools essential for engineering design projects like the Indy racecar wing. Beyond basic CAD modeling, features such as assembly modeling allow for intricate integration of components like wing sections and support structures. Solidworks Simulation enables detailed analysis, predicting how designs will perform under real-world conditions. This includes aerodynamic simulations to optimize wing shape and structural analyses ensuring designs meet safety standards. By leveraging these tools, engineers can iterate designs efficiently, refining them based on virtual tests before physical prototyping. This integrated approach minimizes errors, accelerates development, and ultimately leads to more innovative and effective solutions in engineering design.
CAD Modeling:
SolidWorks serves as your primary tool for creating detailed 3D models of the wing and its supporting structures. Utilize features like extrusions, lofts, and sweeps to accurately represent aerodynamic shapes and structural components. Pay attention to details such as attachment points and load-bearing capacities.
Simulation and Analysis:
Employ SolidWorks Simulation or Cosmos Works to perform virtual tests and analyses. Simulate airflow over your wing design to predict aerodynamic performance metrics such as lift and drag forces. Conduct structural analyses to ensure that your design meets safety and performance standards under varying load conditions.
Iterative Design Process
During the iterative design process, it's crucial to maintain a dynamic approach to prototype development. As you build prototypes using Solidworks and physical materials, focus on testing various configurations rapidly. Evaluate each prototype rigorously against performance criteria derived from simulations and initial design goals. Incorporate feedback from these evaluations into successive design iterations, aiming to optimize not only aerodynamic performance but also structural integrity and manufacturability. By iteratively refining your models based on real-world testing and simulation data, you can ensure that your final design meets or exceeds project specifications while adhering to time and resource constraints.
Prototyping:
Build prototypes of your design using SolidWorks and physical materials. Use rapid prototyping techniques if available to test different configurations quickly. Evaluate each prototype rigorously against performance criteria and iterate based on feedback from simulations and physical tests.
Feedback Integration:
Integrate feedback from simulations and prototypes into subsequent design iterations. Continuously refine your models to optimize performance metrics while considering manufacturing feasibility and cost-effectiveness.
Documentation and Presentation
Effective technical documentation is crucial in engineering projects like the Indy racecar wing design. It serves not only to record your design process but also to justify your decisions and demonstrate your understanding of engineering principles. Detailed CAD drawings, simulation results, and performance metrics provide a clear picture of your design's capabilities. Charts and graphs illustrate trends and optimizations, while comprehensive reports outline the iterative improvements made. Presentation skills are equally vital; clear communication of technical details and concise summaries of your findings help stakeholders understand the significance of your design solutions and the rigorous process undertaken to achieve them.
Technical Documentation:
Prepare comprehensive reports documenting your design process, simulation results, and prototype testing outcomes. Include detailed CAD drawings, simulation screenshots, and charts/graphs illustrating performance metrics. Provide clear explanations of design decisions and optimizations made throughout the project.
Presentation Skills:
Practice presenting your findings and design rationale effectively. Communicate technical information clearly and concisely, highlighting key features of your design and its potential impact on performance. Demonstrate your understanding of engineering principles and project management skills during presentations.
Tips for Success
Effective time management is crucial; break down the project into manageable tasks, setting clear deadlines for each phase. Collaborate closely with team members, leveraging diverse skills and perspectives to solve challenges efficiently. Regular communication ensures everyone stays informed and aligned throughout the project. Utilize available resources like Solidworks tutorials and simulation software to enhance technical proficiency. Seek guidance from faculty or mentors to address complex technical issues and refine design strategies. Embrace iterative improvement by integrating feedback from simulations and prototypes, continuously optimizing designs for performance, manufacturability, and cost-effectiveness.
Time Management:
Break down the project into manageable tasks with specific deadlines. Allocate sufficient time for research, modeling, simulation, prototyping, and documentation to avoid last-minute rushes.
Collaboration:
Effectively communicate and collaborate with your team members, leveraging each other's expertise to tackle complex challenges more efficiently. Regularly update each other on progress and coordinate efforts to meet shared goals.
Resource Utilization:
Make full use of available resources such as Solidworks tutorials, simulation software, and expert advice from faculty or industry mentors. Take advantage of workshops or training sessions to enhance your Solidworks proficiency and broaden your engineering skill set.
Conclusion
Mastering projects like the Indy racecar wing design not only enhances your Solidworks proficiency but also prepares you for the dynamic challenges of engineering practice. By following a structured approach—from initial research and CAD modeling to iterative prototyping and comprehensive documentation—you can develop robust design solutions that meet performance objectives and exceed expectations. Embrace the learning opportunities presented by such assignments to build a strong foundation in engineering design and innovation.
Engaging in projects of this nature fosters essential skills beyond technical proficiency. You'll learn critical aspects of project management, such as timeline adherence, resource allocation, and collaborative teamwork. These skills are invaluable in real-world engineering environments where interdisciplinary collaboration and efficient problem-solving are essential.
Moreover, tackling complex assignments like the Indy racecar wing design encourages creative thinking and innovation. As you navigate through challenges such as optimizing aerodynamic performance while adhering to strict material and dimensional constraints, you'll develop a strategic mindset for overcoming technical hurdles. This process not only sharpens your technical skills in Solidworks and simulation software but also cultivates your ability to think critically and adapt to evolving project requirements.
Ultimately, the experience gained from projects like these equips you with the confidence and expertise needed to tackle future engineering challenges with creativity and precision. Whether you pursue a career in automotive design, aerospace engineering, or any other technical field, the skills honed through projects like the Indy racecar wing design will serve as a solid foundation for your professional journey.