- Concepts
- Tips:
- Terminology
- Key Terms:
- Tips:
- User Interface
- Key Components:
- Tips:
- Design Process
- Steps:
- Tips:
- Design Intent
- Strategies:
- Tips:
- Design Method
- Approaches:
- Tips:
- Sketches
- Key Techniques:
- Tips:
- Features
- Common Features:
- Tips:
- Assemblies
- Key Techniques:
- Tips:
- Drawings
- Key Techniques:
- Tips:
- Model Editing
- Key Techniques:
- Tips:
- Conclusion
Tackling assignments in CAD modeling requires a solid understanding of various concepts and tools. Whether you're a student, a professional, or someone looking to enhance their skills, having a clear grasp of these fundamentals is essential for success. This blog will guide you through essential topics, providing tips and strategies to help you efficiently solve assignments. By breaking down complex tasks into manageable sections and offering SolidWorks assignment help, we aim to make the learning process smoother and more effective. Additionally, we provide 3D modeling assignment help to address specific challenges you might face. With these insights, you will be better equipped to approach your assignments with confidence and precision, ensuring that you can tackle any problem that comes your way. Whether you need help with sketching, feature creation, assemblies, or model editing, our comprehensive approach will provide you with the necessary tools and knowledge to succeed.
Concepts
Understanding fundamental concepts is crucial. CAD modeling operates on a feature-based parametric approach, allowing for complex designs through defining features and parameters.
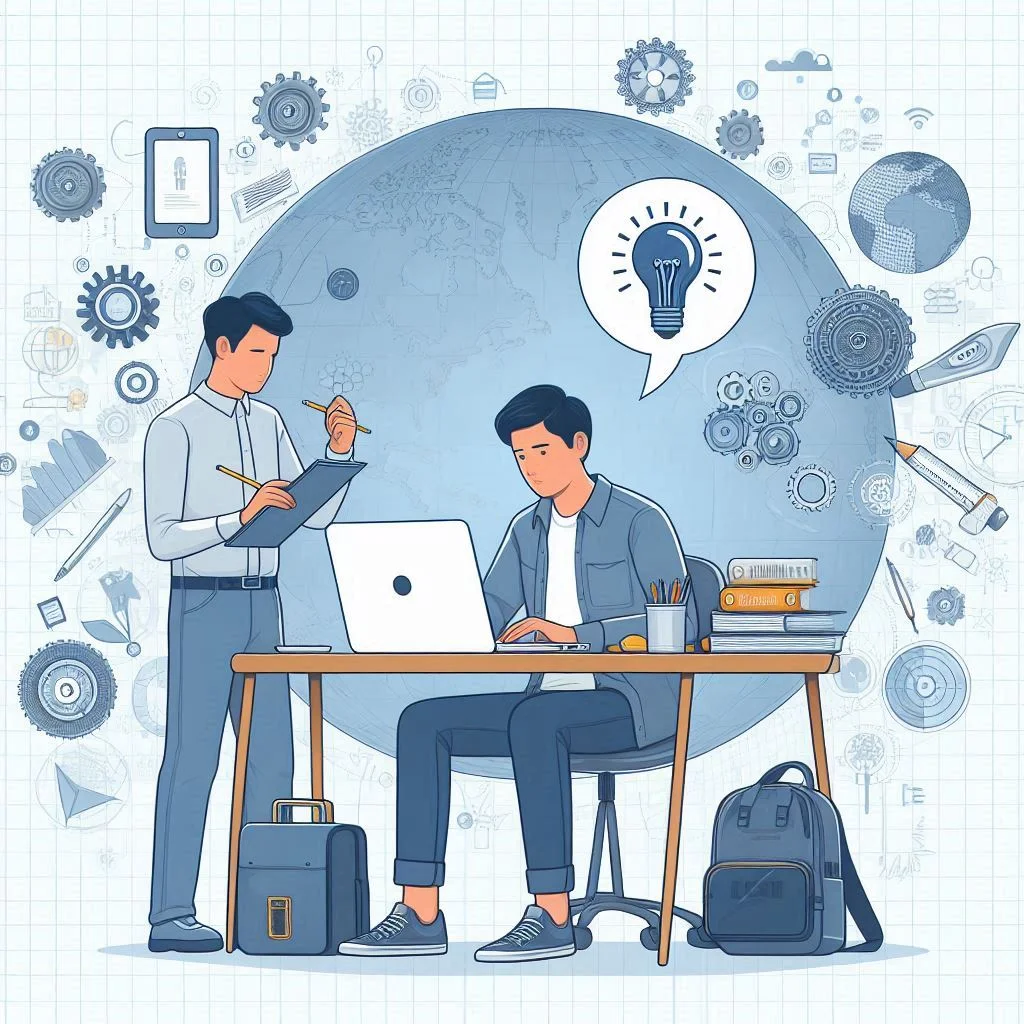
These core concepts underpin everything you do in CAD software, making it essential to grasp them early on.
- Feature-Based Modeling: Feature-based modeling allows you to create 3D models by adding and modifying features. Each feature represents a different aspect of the part, such as a hole, fillet, or boss. By combining these features, you can build complex models from simple geometric shapes.
- Parametric Design: Parametric design is a method where you define key parameters that control the dimensions and relationships of your model. When you change a parameter, the entire model updates automatically to reflect the change. This approach is highly efficient and allows for easy adjustments and iterations.
Tips:
- Familiarize yourself with feature-based modeling. Start with basic features like extrude and cut, and gradually move to more advanced features like loft and sweep.
- Understand parametric design and how changing one parameter can update the entire model. Practice creating models with parameters that you can easily adjust.
Terminology
CAD modeling has its own set of terminologies that you need to understand to follow tutorials and guides effectively. Knowing the terminology will help you communicate more effectively and understand instructions better.
Key Terms:
- Sketch: A 2D drawing that forms the basis of 3D features. Sketches are essential for creating features like extrusions, revolves, and sweeps.
- Feature: 3D shapes and operations that build up the part. Examples include extrude, cut, fillet, and chamfer.
- Assembly: A collection of parts put together to form a complete product. Assemblies allow you to see how different parts interact and fit together.
- Drawing: 2D representations of 3D models for manufacturing. Drawings include dimensions, annotations, and views to convey all necessary information for production.
Tips:
- Learn and memorize key CAD terminology. This will help you follow tutorials, read documentation, and communicate effectively with others.
- Use glossaries and reference materials to familiarize yourself with any unfamiliar terms you encounter.
User Interface
The user interface (UI) of CAD software can be overwhelming for beginners. However, understanding the UI will streamline your workflow and make you more efficient.
Key Components:
- Command Manager: A toolbar that provides access to commonly used tools and commands. The Command Manager is context-sensitive and changes based on the current task (e.g., Sketch, Features, Assembly).
- Feature Manager Design Tree: A hierarchical list of all features, sketches, and components in your model. The Feature Manager Design Tree allows you to view and modify the structure of your model.
- Graphics Area: The main workspace where you create and manipulate your model. The Graphics Area provides visual feedback and allows you to interact with your model directly.
- Property Manager: A panel that displays options and settings for the currently selected tool or feature. The Property Manager allows you to customize and control your tools and features.
Tips:
- Customize toolbars for quick access to frequently used tools. You can add, remove, and rearrange tools to suit your workflow.
- Use the Command Manager to access tools based on the current task. This will help you stay organized and focused.
- Familiarize yourself with keyboard shortcuts. Shortcuts can significantly speed up your workflow and reduce the need to navigate through menus.
Design Process
A well-structured design process is essential for efficient modeling. The design process involves several stages, from conceptualization to refinement.
Steps:
- Conceptualization: Define the problem and brainstorm solutions. This stage involves understanding the requirements, constraints, and goals of the project. Create rough sketches and outlines to visualize your ideas.
- Sketching: Create initial 2D sketches of your design. Sketches are the foundation of your 3D model and provide a basis for creating features. Focus on capturing the key shapes and dimensions of your design.
- Modeling: Develop 3D models from your sketches. Use features to build up the part and create complex shapes. Pay attention to dimensions, constraints, and relationships to ensure your model is accurate and functional.
- Refinement: Optimize your design for functionality and manufacturability. This stage involves making adjustments, adding details, and refining the model to meet the project requirements. Consider factors like material properties, assembly, and production processes.
Tips:
- Follow a structured design process to stay organized and efficient. Break down the project into manageable stages and focus on one task at a time.
- Iterate and refine your design based on feedback and testing. Be open to making changes and improvements to achieve the best possible outcome.
- Document your design process, including sketches, notes, and decisions. This will help you track your progress and communicate your ideas effectively.
Design Intent
Design intent ensures that your model behaves predictably when changes are made. By considering design intent, you can create models that are flexible, adaptable, and easy to modify.
Strategies:
- Use Relationships and Constraints: Apply geometric relationships (e.g., parallel, perpendicular, tangent) and constraints (e.g., equal, fixed) to control the behavior of your sketches and features. Relationships and constraints help maintain the intended geometry and prevent unintended changes.
- Apply Parametric Dimensions: Use dimensions to control the size and position of features. Parametric dimensions allow you to change key parameters and automatically update the entire model. This approach is highly efficient and reduces the risk of errors.
- Consider Assembly Interactions: Think about how parts will interact and fit together in assemblies. Ensure that parts are designed with proper clearances, alignments, and tolerances to avoid issues during assembly.
Tips:
- Plan your design intent before starting your model. Consider the key parameters, relationships, and constraints that will control your model's behavior.
- Use parametric dimensions and relationships to create flexible and adaptable models. Avoid over-constraining your sketches and features, as this can limit your ability to make changes.
- Test your design intent by making changes to key parameters and observing how the model updates. Adjust your design as needed to achieve the desired behavior.
Design Method
Different design methods can be applied based on project requirements. Choosing the right design method can significantly impact the efficiency and quality of your model.
Approaches:
- Top-Down Design: Start with the overall assembly and design individual parts based on it. In top-down design, you create the assembly first and then design the parts in the context of the assembly. This approach is useful for ensuring that parts fit together properly and meet the overall design requirements.
- Bottom-Up Design: Create individual parts first and then assemble them. In bottom-up design, you design each part independently and then assemble them to form the complete product. This approach is useful for designing standard parts that can be reused in different assemblies.
Tips:
- Choose the design method that best suits your project requirements. Consider factors like the complexity of the assembly, the need for part reuse, and the importance of assembly interactions.
- Use a combination of top-down and bottom-up design as needed. For example, you can use top-down design for critical parts that need to fit together precisely and bottom-up design for standard parts.
- Document your design method and approach. This will help you stay organized and communicate your design process effectively.
Sketches
Sketches are the foundation of your 3D models. Creating accurate and well-defined sketches is essential for building reliable and functional models.
Key Techniques:
- Geometric Constraints: Use geometric constraints (e.g., perpendicular, parallel, tangent) to control the behavior of your sketches. Constraints help maintain the intended geometry and ensure that your sketches are fully defined.
- Dimensions: Apply dimensions to control the size and position of sketch elements. Dimensions allow you to create precise and accurate sketches that can be easily modified.
- Construction Geometry: Use construction geometry (e.g., reference lines, points, and circles) to help define your sketches. Construction geometry provides additional reference points and guides for creating and modifying sketch elements.
Tips:
- Keep sketches simple and fully defined. Avoid creating overly complex sketches that are difficult to modify and maintain.
- Use geometric constraints and dimensions to control the behavior of your sketches. Ensure that your sketches are fully defined and do not have any undefined elements.
- Apply construction geometry as needed to help define and guide your sketches. Construction geometry can provide valuable reference points and guides for creating and modifying sketch elements.
Features
Features turn sketches into 3D models. Understanding how to create and use features is essential for building complex and functional models.
Common Features:
- Extrude: Create 3D shapes by extending a 2D sketch along a straight path. Extrude is one of the most commonly used features and is essential for creating basic shapes.
- Revolve: Create 3D shapes by rotating a 2D sketch around an axis. Revolve is useful for creating cylindrical and symmetrical shapes.
- Loft: Create 3D shapes by connecting multiple 2D sketches along a curved path. Loft is useful for creating complex and organic shapes.
- Sweep: Create 3D shapes by sweeping a 2D sketch along a predefined path. Sweep is useful for creating shapes with a consistent cross-section along a curved path.
Tips:
- Combine features strategically to build complex shapes. Use a combination of extrude, revolve, loft, and sweep to create the desired geometry.
- Use reference geometry (planes, axes) to control feature creation. Reference geometry provides additional reference points and guides for creating and modifying features.
- Apply fillets and chamfers to add finishing touches to your model. Fillets and chamfers help smooth edges and improve the appearance and functionality of your model.
Assemblies
Assemblies bring together multiple parts to form a complete model. Understanding how to create and manage assemblies is essential for designing complex products.
Key Techniques:
- Mates: Use mates to define relationships between parts. Mates control how parts interact and fit together in the assembly. Common mates include coincident, parallel, and tangent.
- Subassemblies: Organize components into subassemblies for easier management. Subassemblies group related parts together and allow you to manage them as a single unit. This approach simplifies the assembly process and reduces the risk of errors.
- Configurations: Use configurations to manage different versions of your assembly. Configurations allow you to create multiple variations of your assembly with different parts, mates, and features. This approach is useful for designing products with different options and variations.
Tips:
- Use mates to define clear and precise relationships between parts. Ensure that mates are properly defined and do not conflict with each other.
- Organize components into subassemblies to simplify the assembly process. Subassemblies help manage complex assemblies and reduce the risk of errors.
- Use configurations to manage different versions of your assembly. Create configurations for different options and variations to streamline the design process.
Drawings
Drawings provide the necessary details for manufacturing your designs. Understanding how to create and use drawings is essential for communicating your design to others.
Key Techniques:
- Multiple Views: Include multiple views (front, top, side) to fully represent the model. Multiple views provide a complete and accurate representation of the model and help convey all necessary information for manufacturing.
- Dimensions and Annotations: Add dimensions and annotations to specify details. Dimensions and annotations provide critical information about the size, position, and features of the model. Ensure that all necessary dimensions and annotations are included and clearly defined.
- Templates: Use templates to maintain consistency across drawings. Templates provide a standard format and layout for your drawings and help ensure that all necessary information is included.
Tips:
- Include multiple views to fully represent your model. Ensure that all critical features are visible and clearly defined in the views.
- Add dimensions and annotations to specify details. Ensure that all necessary dimensions and annotations are included and clearly defined.
- Use templates to maintain consistency across drawings. Create and use standard templates to ensure that all necessary information is included and that your drawings are consistent and professional.
Model Editing
Editing models is a common task as designs evolve. Understanding how to edit and modify models is essential for making changes and improvements.
Key Techniques:
- Feature Manager: Use the Feature Manager to access and modify features. The Feature Manager provides a hierarchical list of all features, sketches, and components in your model and allows you to view and modify the structure of your model.
- Configurations: Use configurations to manage different versions of your model. Configurations allow you to create multiple variations of your model with different features, dimensions, and parameters. This approach is useful for designing products with different options and variations.
- Design Tables: Apply design tables for complex parametric variations. Design tables allow you to create and manage multiple configurations and variations of your model using a spreadsheet interface.
Tips:
- Use the Feature Manager to access and modify features. Ensure that all features are properly defined and organized in the Feature Manager.
- Make use of configurations to manage different versions of your model. Create configurations for different options and variations to streamline the design process.
- Apply design tables for complex parametric variations. Use design tables to create and manage multiple configurations and variations of your model.
Conclusion
Mastering these key topics in CAD modeling will enable you to tackle assignments with confidence. Practice regularly, explore tutorials, and participate in forums to enhance your skills further. With a solid understanding of concepts, terminology, and tools, you’ll be well-equipped to handle any CAD modeling assignment.