- Understanding Weldments in SolidWorks
- Customizing Weldment Profiles
- Structural Members and Cut Lists
- Advanced Weldment Tools
- Working with Weld Beads
- Simulating Welded Connections
- Weldment Drawings and Documentation
- Integrating Weldments with Other SolidWorks Features
- Best Practices for Weldment Design
- Conclusion
SolidWorks stands as a cornerstone in the realm of 3D CAD software, renowned for its comprehensive suite of tools tailored for the creation of intricate welded structures. Its prowess extends far beyond mere drafting, providing engineers and designers with a versatile platform that caters to the complexities of modern design challenges. In the following sections, we will journey through the advanced weldment features embedded within SolidWorks, unraveling a realm of possibilities that elevate the standards of design and fabrication. If you need help with your weldment assignment, exploring the advanced weldment features in SolidWorks can significantly enhance your understanding and proficiency in designing welded structures.
SolidWorks excels in offering an integrated environment where users can seamlessly transition from conceptualization to realization. The software's robust toolset empowers users to fashion weldments with precision and efficiency, laying the groundwork for groundbreaking designs. This fusion of creativity and functionality makes SolidWorks a preferred choice for professionals across diverse industries, from aerospace engineering to structural design.
In our exploration, we'll navigate the intricacies of weldment profiles, a fundamental building block for any structural design. SolidWorks facilitates the customization of these profiles, allowing users to tailor their components to adhere to specific industry standards or project-specific requirements. This adaptability is a testament to SolidWorks' commitment to user-centric design, providing a flexible canvas for the realization of creative visions.
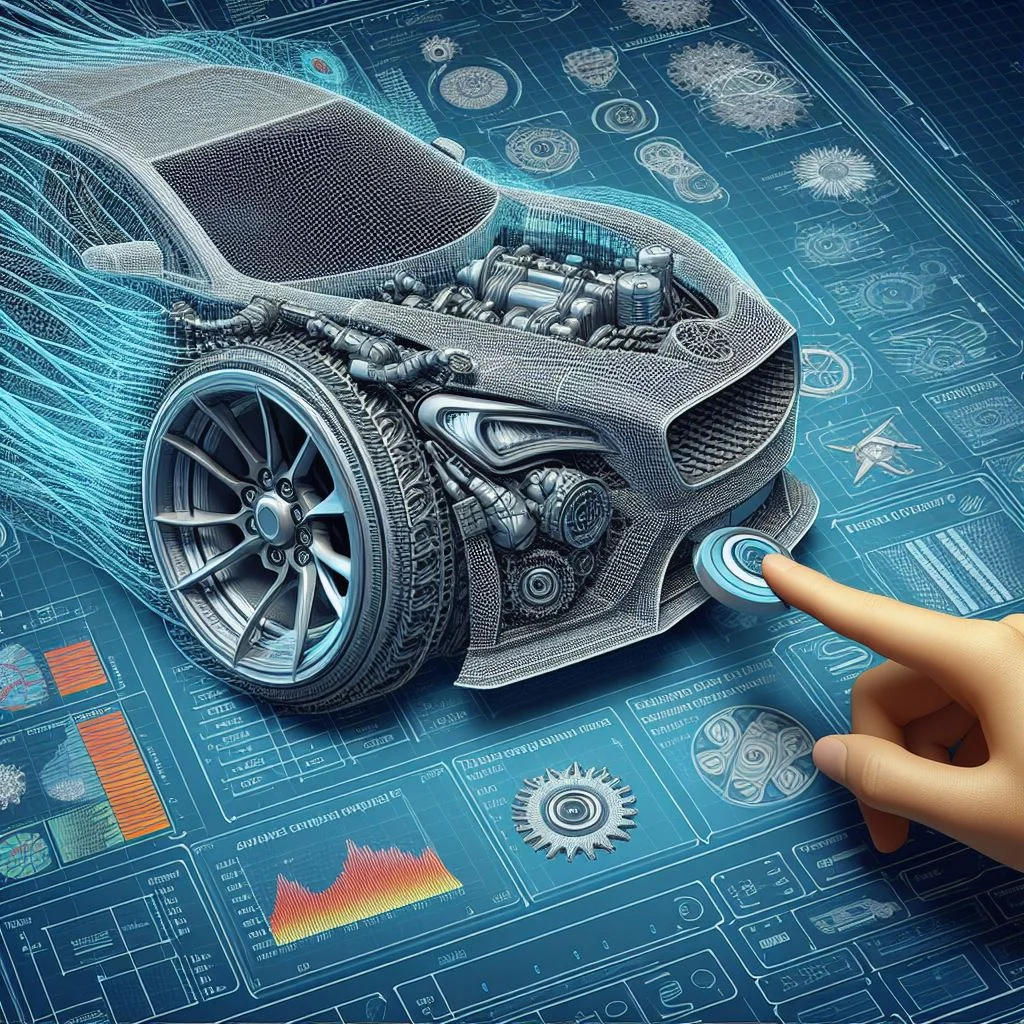
Structural members and cut lists form the backbone of any weldment project. SolidWorks streamlines this process by offering an extensive library of standard shapes, enabling designers to effortlessly integrate components that meet industry specifications. The software's intuitive interface facilitates the generation of accurate cut lists, paving the way for seamless collaboration between design and fabrication teams. This collaborative approach ensures that the envisioned design not only meets aesthetic standards but also aligns with the practicalities of material usage.
As we progress into the advanced features of SolidWorks weldments, the spotlight turns to tools that elevate precision and complexity. Miter cuts and coping functionalities emerge as indispensable assets in crafting intricate structures. The software's ability to handle these advanced techniques ensures that designers can bring their visionary concepts to life, pushing the boundaries of what's achievable in the realm of welded structures.
Weld beads add a touch of realism to virtual designs, mirroring the intricacies of real-world welding. SolidWorks provides a suite of tools for simulating weld beads, allowing designers to fine-tune their joints with utmost accuracy. This attention to detail not only enhances the visual representation of welds but also contributes to the overall integrity and authenticity of the design.
Simulation takes center stage as we explore SolidWorks' capabilities in assessing the structural soundness of welded connections. The software's simulation tools empower designers to subject welds to rigorous testing, identifying potential weak points and optimizing designs for optimal performance and safety. This simulation-driven approach aligns with industry best practices, ensuring that virtual prototypes are not only aesthetically pleasing but also functionally robust.
Weldment drawings and documentation form the bridge between virtual design and real-world fabrication. SolidWorks facilitates the creation of comprehensive drawings, complete with assembly views, dimensions, and bills of materials. This documentation not only serves as a blueprint for fabrication but also streamlines the communication between different stakeholders involved in the project, fostering a collaborative and efficient workflow.
As we seamlessly integrate weldments with other SolidWorks features like sheet metal, assemblies, and drawings, the software's versatility shines through. SolidWorks becomes more than just a CAD tool; it transforms into a holistic design environment where different facets of a project seamlessly converge. This integration not only enhances efficiency but also ensures design consistency throughout the various stages of a project's lifecycle.
Our exploration concludes with a discussion on best practices, offering insights into optimizing the weldment design process. From efficient modeling techniques to collaboration tips, these best practices serve as a compass for designers navigating the complex terrain of weldment design in SolidWorks. By adhering to these principles, users can elevate their proficiency, resulting in designs that not only meet industry standards but also surpass expectations.
Understanding Weldments in SolidWorks
Weldments in SolidWorks serve as a powerful tool for engineers and designers, enabling the efficient creation of intricate structural frameworks. As we embark on this journey to understand the fundamentals, it's crucial to emphasize the versatility and user-friendly nature of SolidWorks weldments.
At the core of weldment design lies the ability to set up a comprehensive weldment profile library. SolidWorks provides an extensive range of predefined profiles, allowing users to choose from a variety of standard shapes and sizes. However, the true strength of SolidWorks emerges when users customize these profiles to match specific industry standards or project requirements. This customization not only enhances design flexibility but also ensures that the resulting structures align seamlessly with the intended specifications.
Once armed with a personalized weldment profile library, the next step involves creating the initial framework for a project. SolidWorks simplifies this process through intuitive tools that facilitate the assembly of structural members. Users can effortlessly sketch the layout of their design, selecting and placing the appropriate profiles to construct the framework. This initial stage sets the foundation for the entire weldment project, emphasizing precision and efficiency in the early phases of design.
Understanding the basics of SolidWorks weldments not only streamlines the design process but also lays the groundwork for exploring more advanced features. With a strong foundation in place, designers can confidently delve into the intricacies of customization, simulation, and documentation, unlocking the full potential of SolidWorks for weldment design.
Customizing Weldment Profiles
Customizing weldment profiles in SolidWorks is a powerful feature that empowers designers to meet diverse project demands with precision and efficiency. SolidWorks, recognized for its versatility, allows users to go beyond standard profiles and create customized shapes, catering to specific industry standards or the unique requirements of a particular project.
The process of customizing weldment profiles involves defining the cross-sectional shape of structural members, enabling designers to adapt to various design specifications. This level of flexibility is particularly advantageous when working in industries with specific standards or when tackling projects with distinct geometric requirements.
SolidWorks simplifies the customization process, offering an intuitive interface for designing profiles that align with your vision. Whether you're adhering to industry standards or pushing the boundaries of innovation with unique shapes, SolidWorks provides the tools needed to bring your ideas to life.
By mastering the art of customizing weldment profiles, designers can elevate their projects, ensuring that structural elements not only meet but exceed expectations. The ability to tailor profiles enhances the adaptability of SolidWorks, making it a preferred choice for those seeking precision and creativity in their weldment designs. Explore this feature, and open doors to a realm of possibilities in structural design within the SolidWorks environment.
Structural Members and Cut Lists
SolidWorks' strength in simplifying structural member creation lies in its extensive library of standard shapes. By leveraging these predefined profiles, designers can expedite the modeling process while ensuring compliance with industry standards. Whether you're working on a straightforward project or a complex structure, SolidWorks' structural members cater to a diverse range of design needs.
The ability to efficiently generate cut lists is a game-changer in the realm of structural design. SolidWorks empowers users to create accurate material estimates by automating the process of documenting and categorizing individual components within a weldment. This functionality not only streamlines the design phase but also proves invaluable during the fabrication stage.
The seamless collaboration between designers and fabricators is another notable benefit of SolidWorks' structural members and cut lists. The software facilitates clear communication by providing a comprehensive breakdown of the materials required. Fabricators can easily interpret and act upon the information, minimizing errors and ensuring that the final product aligns with the intended design.
In essence, SolidWorks transforms the often intricate task of creating structural members into an intuitive and efficient process. The integration of predefined profiles and the automated generation of cut lists not only save time but also contribute to the precision and reliability of your weldment designs. As we continue our exploration of SolidWorks' advanced weldment features, these foundational elements serve as the building blocks for more intricate and sophisticated structures.
Advanced Weldment Tools
Within SolidWorks, the realm of advanced weldment tools opens up a plethora of possibilities for designers seeking precision and complexity in their projects. Miter cuts, a fundamental feature, play a pivotal role in achieving seamless joints at various angles. Whether you are working on angular frames or intricate structures, mastering the art of miter cuts ensures a flawless integration of components, enhancing both aesthetic appeal and structural integrity.
Coping, another powerful tool, adds a layer of sophistication to weldment designs. This technique involves creating precise cuts at the intersection of two members, allowing them to fit together seamlessly. It's a game-changer for projects requiring intricate connections or those with complex geometric shapes. SolidWorks' coping tool streamlines this process, providing designers with the means to achieve meticulous fits and ensuring that every joint is as strong as it is visually pleasing.
Furthermore, the software offers an array of features beyond miter cuts and coping. Explore advanced fillet options to add curvature and smoothness to weldment joints. Dive into the intricacies of weld gap control, managing the spaces between components with precision. These tools empower designers to fine-tune every aspect of their weldment structures, resulting in a level of sophistication that goes beyond basic functionality.
Working with Weld Beads
In SolidWorks, the inclusion of weld beads is a crucial step in achieving a lifelike representation of welded joints within your designs. These virtual weld beads not only contribute to the visual realism of your models but also play a significant role in simulating the welding process accurately.
To start working with weld beads in SolidWorks, first, understand how to apply them to joints seamlessly. The software offers intuitive tools that allow you to place weld beads precisely along the desired paths, mimicking real-world welding procedures. This feature becomes especially valuable when communicating design intent to stakeholders, as it provides a tangible preview of the welding aesthetics and ensures a comprehensive understanding of the final product.
Customization is key in the world of weld beads, and SolidWorks provides a plethora of options to tailor their properties. Explore parameters such as size, shape, and penetration depth, allowing you to fine-tune the appearance of the welds according to project specifications or industry standards. This level of detail not only enhances the visual appeal of your designs but also contributes to a more accurate representation of the welding process.
Moreover, ensuring that your virtual welds align with industry standards is paramount for the structural integrity of your designs. SolidWorks facilitates this by providing tools to validate your welds against industry-specific criteria. By incorporating these checks into your design process, you can confidently move forward, knowing that your virtual welds meet the required standards for strength and durability.
Simulating Welded Connections
Simulating welded connections plays a pivotal role in ensuring the robustness and reliability of your designs. SolidWorks Simulation provides a powerful platform for this critical task, allowing engineers to delve into the intricate details of welds. By utilizing SolidWorks Simulation, you gain the capability to perform in-depth analyses that go beyond mere visual representation.
Through simulation, you can precisely evaluate the stress distribution within weldments, identifying potential weak points or areas susceptible to fatigue. This level of insight is invaluable in the quest for optimal structural integrity. SolidWorks Simulation empowers you to simulate various load scenarios, including static, dynamic, and thermal conditions, providing a comprehensive understanding of how welded connections will perform under different circumstances.
Moreover, the simulation results enable engineers to make informed decisions on material selection, weld sizes, and joint configurations. This not only enhances the overall performance of the weldment but also contributes significantly to safety considerations.
The optimization capabilities offered by SolidWorks Simulation allow you to fine-tune your weldment design for maximum efficiency. By iteratively adjusting parameters based on simulation feedback, you can achieve a balance between structural strength and material usage, resulting in cost-effective yet robust designs. In essence, the simulation process becomes a virtual testing ground, where you can refine and perfect your welded connections before physical fabrication begins.
Incorporating simulation into your workflow elevates your ability to deliver designs that not only meet industry standards but surpass them, ensuring the longevity and reliability of your welded structures.
Weldment Drawings and Documentation
Creating comprehensive documentation is an integral part of the engineering process, ensuring clarity, precision, and effective communication throughout a project's lifecycle. SolidWorks excels in facilitating this critical aspect with its robust capabilities for generating detailed weldment drawings.
SolidWorks allows users to seamlessly create weldment drawings that go beyond mere representations of 3D models. Through assembly views, designers can present an intricate visualization of the weldment, providing stakeholders with a clear understanding of how components fit together. These assembly views serve as a valuable resource during the manufacturing and assembly phases, minimizing errors and streamlining the production process.
In addition to visual representations, SolidWorks enables the inclusion of precise dimensions in weldment drawings. Accurate measurements are crucial for fabricators and ensure that the final product aligns with the design intent. SolidWorks' intuitive dimensioning tools empower users to annotate their drawings with clarity, making it easier for all parties involved to interpret and execute the design accurately.
Furthermore, the software's capability to generate bills of materials (BOM) enhances the documentation process. The BOM provides a comprehensive list of all components within the weldment, aiding in material procurement, cost estimation, and inventory management. This feature streamlines collaboration between designers and manufacturers, fostering a more efficient and organized workflow.
Integrating Weldments with Other SolidWorks Features
Discover how weldments seamlessly integrate with other SolidWorks features like sheet metal, assemblies, and drawings. Learn valuable tips for maintaining design consistency across different aspects of your project.
SolidWorks offers a holistic approach to design by allowing smooth integration between weldments and other crucial features. One key integration point is with sheet metal functionalities. By seamlessly combining weldments with sheet metal design, engineers can create comprehensive structures that incorporate both structural frames and sheet metal components. This integration ensures a unified approach to design, reducing the need for manual adjustments and enhancing overall efficiency.
Furthermore, when working with assemblies, SolidWorks provides tools to effortlessly incorporate weldments into larger projects. This streamlined integration facilitates the creation of intricate assemblies, enabling designers to visualize the complete product and identify potential clashes or interferences early in the design process. The ability to seamlessly merge weldments with assemblies not only enhances the overall design workflow but also contributes to more accurate representations of real-world structures.
In addition to assemblies, SolidWorks allows for the integration of weldments into detailed drawings. This feature is invaluable for producing comprehensive documentation, as designers can easily showcase weldment details, dimensions, and annotations in a standardized format. This integration ensures that the information conveyed in the drawings accurately reflects the weldment design, aiding in effective communication with fabricators and collaborators.
Best Practices for Weldment Design
In the realm of weldment design within SolidWorks, adopting best practices is paramount to ensure not just efficiency but also precision and collaborative success. Efficient modeling techniques form the cornerstone of a streamlined design process. Utilizing standard structural shapes and optimizing profiles can significantly reduce modeling time while maintaining industry standards. Implementing modular design principles allows for the creation of reusable components, fostering consistency across projects and accelerating the design phase.
Moreover, effective collaboration is at the heart of successful engineering projects. SolidWorks provides collaborative features that enable seamless teamwork. Utilize version control, annotations, and comments to facilitate communication within design teams. Integrating design review processes ensures that all stakeholders are on the same page, fostering a collaborative environment that minimizes errors and maximizes productivity.
Another crucial aspect of best practices in weldment design involves meticulous documentation. Clearly define weld symbols, annotations, and dimensions in your drawings to convey critical information to fabricators accurately. Consistent labeling and proper documentation not only enhance communication but also contribute to a smoother manufacturing process, reducing the likelihood of errors during fabrication.
By incorporating these best practices into your SolidWorks weldment design workflow, you'll not only optimize your individual design processes but also contribute to a more collaborative and error-resistant project environment. Remember, the key to success lies not just in mastering the tools at your disposal but also in adopting methodologies that foster efficiency and effective teamwork.
Conclusion
In the realm of weldment design within SolidWorks, our exploration has unraveled a tapestry of advanced features that not only streamline the design process but also open new avenues for creativity and precision. As we conclude this journey through the intricate world of SolidWorks weldments, it's evident that the software stands as a beacon of innovation, empowering designers to elevate their projects to unprecedented heights.
SolidWorks, with its integrated and user-centric environment, serves as more than just a tool; it is a catalyst for transformative design thinking. The robust toolset provided by SolidWorks empowers users to seamlessly transition from conceptualization to realization, laying the foundation for groundbreaking designs. This intersection of creativity and functionality positions SolidWorks as the go-to choice for professionals spanning various industries.
The customization prowess of SolidWorks in weldment profiles underscores its commitment to flexibility and adaptability. By allowing users to tailor components to specific industry standards or project-specific requirements, SolidWorks provides a versatile canvas for turning creative visions into tangible structures. This adaptability not only fosters innovation but also ensures that designs align with the ever-evolving demands of diverse engineering projects.
Structural members and cut lists, essential components of any weldment project, find optimal expression within SolidWorks. The software's extensive library of standard shapes and the ability to generate accurate cut lists streamline collaboration between design and fabrication teams. This collaborative synergy not only enhances the practical aspects of material usage but also ensures that the design remains true to its aesthetic and functional objectives.
The exploration of advanced features like miter cuts and coping has illuminated SolidWorks' capacity to handle intricate design techniques. These tools elevate precision and complexity, enabling designers to breathe life into visionary concepts. SolidWorks' commitment to accommodating these advanced features is a testament to its dedication to pushing the boundaries of what's achievable in the realm of welded structures.
Weld beads, often an overlooked detail in virtual designs, become a focal point in SolidWorks. The simulation tools for weld beads enhance the authenticity of virtual welds, contributing to both the visual representation and overall integrity of the design. This attention to detail reflects SolidWorks' commitment to mirroring real-world welding intricacies within the virtual environment.
Simulation takes the spotlight in assessing the structural soundness of welded connections. SolidWorks' simulation tools enable designers to subject welds to rigorous testing, ensuring optimal performance and safety. This simulation-driven approach aligns with industry best practices, emphasizing not just the aesthetic appeal but also the functional robustness of virtual prototypes.
As weldment designs materialize into detailed drawings and documentation, SolidWorks proves its mettle as a holistic design environment. The seamless integration with other features ensures design consistency throughout a project's lifecycle. The documentation serves as a blueprint for fabrication, fostering efficient communication and collaboration among different stakeholders.