In the dynamic world of engineering and design, precision, innovation, and efficiency are paramount. To meet these demands, engineers and designers rely on a plethora of software tools that streamline processes and enable the creation of intricate designs and products. One such powerful tool that has revolutionized the way we design and engineer is SolidWorks. SolidWorks is a computer-aided design (CAD) and computer-aided engineering (CAE) software that provides a comprehensive platform for designing, simulating, and visualizing a wide range of products and systems. In this blog post, we will delve into the various applications of SolidWorks in the fields of engineering and design, exploring how it has transformed industries and continues to drive innovation. In addition to its transformative impact on industries, SolidWorks also plays a crucial role in education by providing students with hands-on experience that can help with their SolidWorks assignment, preparing the next generation of engineers and designers to effectively utilize this powerful software in their future careers.
Understanding SolidWorks
SolidWorks, developed by Dassault Systèmes, was first introduced in 1995 and has since become a cornerstone in the CAD/CAE software landscape. Known for its user-friendly interface and robust feature set, SolidWorks empowers engineers and designers to create 3D models, simulate behaviors, and generate detailed drawings with precision. Its parametric design approach allows users to define relationships between various components, facilitating design changes and updates across the entire model.
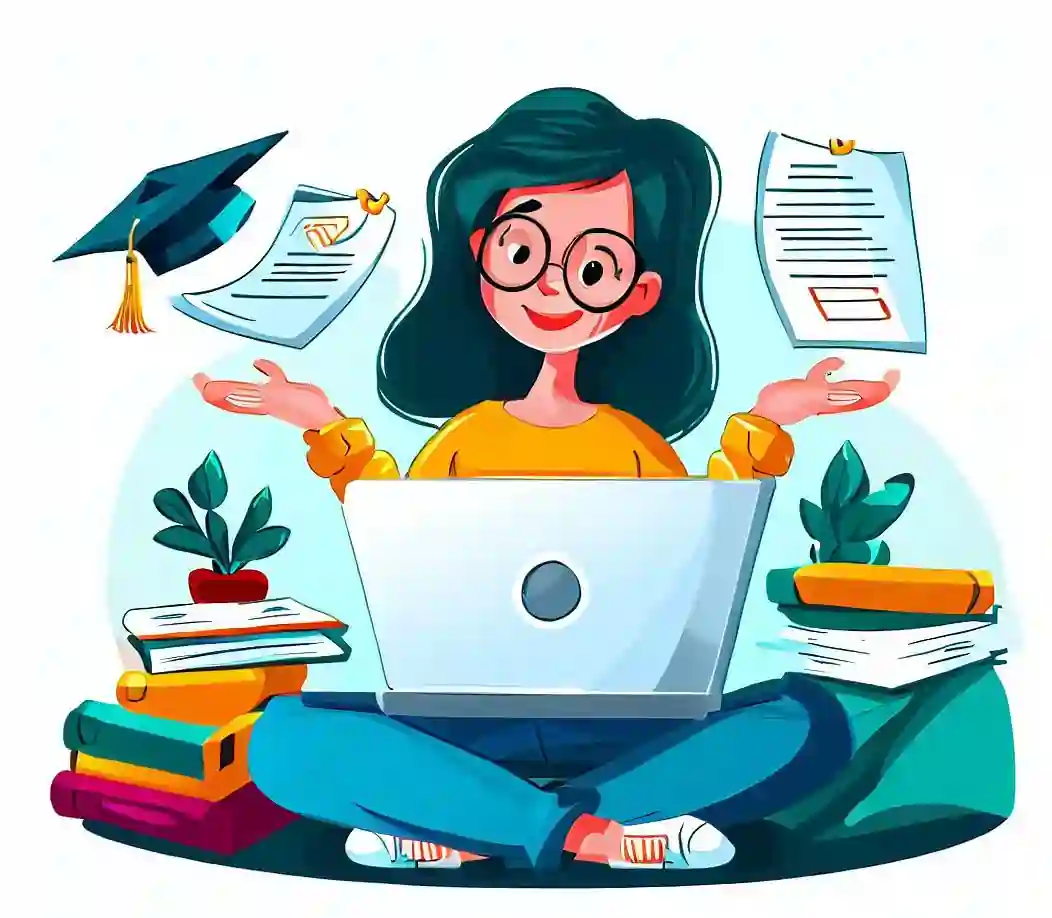
- Product Design and Development
- Mechanical and Industrial Engineering
- Architecture and Construction
- Aerospace and Defense
- Consumer Goods
- Medical and Healthcare
- Automotive Engineering
- Educational Applications
SolidWorks serves as a cornerstone in the realm of product design and development, spanning across a diverse array of industries including consumer electronics, automotive, industrial machinery, and medical devices. The software's role is pivotal in transforming innovative concepts into tangible realities. Engineers begin by sketching their ideas in 2D, after which SolidWorks steps in to breathe life into these concepts through its robust modeling tools. The software's capability to simulate real-world conditions and interactions is a game-changer, ensuring that designs are not only visually appealing but also optimized for functionality and durability.
With SolidWorks, engineers can seamlessly transition from 2D sketches to intricate 3D models that capture every detail. This three-dimensional representation offers a comprehensive view of the product, enabling engineers to identify potential design flaws and make necessary adjustments early in the development process. Moreover, SolidWorks' parametric design approach ensures that modifications made to one component are automatically propagated throughout the entire model, streamlining the iterative design process.
The software's simulation features are particularly invaluable in product design. Engineers can subject their designs to a range of real-world scenarios, such as stress testing, thermal analysis, and fluid dynamics simulations. This empowers them to understand how the product will behave under different conditions, identify potential weak points, and optimize the design for performance and durability. By catching potential issues before the manufacturing phase, SolidWorks contributes to substantial cost and time savings.
Mechanical and industrial engineers find SolidWorks to be an indispensable tool in their design and analysis processes. Whether they are working on intricate machine components or complex assembly models, SolidWorks aids in transforming conceptual designs into well-defined 3D models. This level of precision allows engineers to visualize every aspect of the design before moving forward.
SolidWorks' simulation capabilities play a crucial role in mechanical and industrial engineering. Engineers can subject their models to stress and strain analysis, helping them identify weak points and potential points of failure. By understanding how a design will perform under various loads and conditions, engineers can make informed decisions to enhance the overall reliability and durability of the product.
Another advantage SolidWorks offers to mechanical and industrial engineers is the ability to create assembly models. These models allow engineers to visualize how various components fit together, ensuring that there are no interferences or clashes between parts. This meticulous attention to detail in the virtual environment translates to a smoother and more efficient manufacturing process.
While SolidWorks is commonly associated with engineering and manufacturing, its applications extend to the field of architecture and construction as well. Architects can leverage SolidWorks' capabilities to create detailed 3D models of buildings and structures. These models provide a comprehensive visualization of the architectural design, enabling architects to identify potential design issues and refine their concepts before construction begins.
SolidWorks' simulation features are also relevant in architecture and construction. Architects can simulate factors like structural integrity, heat distribution, and fluid flow within buildings. This enables them to make informed decisions about materials, insulation, and ventilation systems, contributing to the creation of more efficient and sustainable designs. By identifying potential challenges in the virtual realm, architects can mitigate risks and enhance the quality of their projects.
Precision and reliability are non-negotiable in the aerospace and defense sectors. SolidWorks rises to the occasion by offering tools and features that cater to the complex and stringent requirements of these industries. Engineers working on aircraft components, spacecraft, and defense systems rely on SolidWorks to design and visualize intricate structures.
The simulation capabilities of SolidWorks are paramount in aerospace and defense engineering. Engineers can simulate how aerospace systems will perform under different conditions, including extreme temperatures, pressure differentials, and aerodynamic forces. This level of analysis ensures that designs meet safety standards and can withstand the rigors of their intended environments.
Collaboration is also a key aspect of aerospace and defense projects. SolidWorks' collaboration tools facilitate seamless communication among interdisciplinary teams. Engineers, designers, and experts from various fields can collaborate on a single platform, exchanging ideas, data, and insights to achieve the best possible results. This collaborative environment enhances the overall efficiency and effectiveness of aerospace and defense projects.
SolidWorks has a notable impact on the design of consumer goods, spanning a wide range of products from kitchen appliances to sports equipment. Designers in this domain rely on the software to create products that are not only functional but also visually appealing and ergonomic.
One of SolidWorks' strengths in consumer goods design is its ability to generate detailed and realistic 3D models. Designers can accurately visualize the final product, considering factors like size, shape, and aesthetics. This level of detail is crucial in making design decisions that align with user preferences and expectations.
Simulation also plays a role in consumer goods design. SolidWorks enables designers to simulate user interactions with the product, assessing factors like usability, comfort, and safety. For example, a designer working on a chair can simulate how a person's posture and movements would affect comfort levels. This iterative approach allows designers to refine their products based on real-world usage scenarios.
In the medical field, precision and safety are of utmost importance. SolidWorks contributes significantly to the design and development of medical devices, prosthetics, and surgical tools. Engineers collaborate closely with medical professionals to create designs that cater to specific patient needs.
SolidWorks' simulation capabilities are crucial in the medical domain. Engineers can simulate how medical devices will interact with the human body, ensuring that they perform as intended and do not pose any risks to patients. For instance, a prosthetic limb can be simulated to ensure proper fit, comfort, and functionality.
The software also aids in the development of surgical tools. Engineers can design tools that offer optimal ergonomics for surgeons, enhancing their precision and reducing fatigue during procedures. Additionally, the software's simulation features allow engineers to simulate surgical scenarios, providing insights into how the tools will be used in real-life situations.
The automotive industry is characterized by its constant pursuit of innovation and efficiency. SolidWorks is a fundamental tool in this sector, used for designing vehicles, components, and systems that meet the highest standards of performance and safety.
SolidWorks' modeling capabilities allow automotive engineers to create intricate 3D models of engines, chassis, interiors, and more. This level of detail enables engineers to optimize designs for factors like aerodynamics, fuel efficiency, and safety. Engineers can simulate how different design choices impact the vehicle's performance, helping them make informed decisions that contribute to the overall quality of the product.
Assembly modeling is another crucial aspect of automotive engineering that SolidWorks supports. Automotive systems are complex and consist of numerous interconnected components. SolidWorks enables engineers to visualize how these components fit together, detect potential clashes, and ensure proper alignment. This meticulous attention to detail in the virtual realm translates to a smoother manufacturing process and fewer issues during assembly.
SolidWorks isn't only a tool for professionals—it also plays a significant role in education. Many universities and educational institutions incorporate SolidWorks into their engineering curricula to provide students with hands-on experience using industry-standard software.
By introducing students to SolidWorks, educational institutions prepare them for careers in various engineering and design fields. Students gain proficiency in creating 3D models, simulating real-world scenarios, and analyzing designs. This practical experience equips them with skills that are highly sought after in the job market.
Additionally, using SolidWorks in education fosters a deeper understanding of engineering principles and design processes. Students can experiment with different design iterations, simulate their performance, and gain insights into the decision-making process that underlies successful engineering projects. This experiential learning approach prepares students to tackle real-world challenges with confidence.
Benefits of Using SolidWorks
The popularity of SolidWorks can be attributed to the numerous benefits it offers to engineers and designers across industries. Some of the key advantages include:
- User-Friendly Interface
- Parametric Design
- Realistic Simulation
- Rapid Prototyping
- Collaboration and Data Management
- Visualization and Presentation
SolidWorks features an intuitive interface that makes it accessible to both beginners and experienced users. The software's consistent layout and easy-to-navigate tools contribute to a smooth design process.
The parametric design approach in SolidWorks enables engineers to create relationships between different parts of a design. When one parameter changes, the software automatically updates all related components, reducing manual adjustments and errors.
SolidWorks' simulation capabilities allow users to subject designs to real-world conditions such as stress, heat, and fluid flow. This helps identify potential issues early in the design phase and ensures optimal performance.
SolidWorks' ability to generate detailed and accurate 3D models expedites the prototyping process. This means that engineers and designers can quickly move from concept to physical prototype, saving time and resources.
The software provides tools for collaboration and data management, allowing multiple team members to work on the same project simultaneously. This enhances communication, minimizes errors, and ensures that everyone is working with the most up-to-date information.
SolidWorks' rendering capabilities enable users to create realistic visualizations of their designs. This is particularly useful for presentations, marketing materials, and communication with clients.
Future Trends and Innovations
As technology continues to evolve, so does the landscape of engineering and design. SolidWorks, too, is evolving to meet the changing demands of industries. Some of the trends and innovations that we can expect to see in the realm of SolidWorks applications include:
- Generative Design
- Augmented Reality (AR) Integration
- Cloud-Based Collaboration
- Sustainability and Eco-Friendly Design
- Artificial Intelligence (AI) Integration
Generative design is an emerging concept that leverages algorithms to explore a wide range of design possibilities based on specified constraints. SolidWorks is likely to integrate generative design tools, enabling engineers to rapidly generate and evaluate innovative design solutions.
AR technology is making its way into various industries, including engineering and design. SolidWorks might incorporate AR features that allow users to visualize and interact with virtual models in real-world environments.
Cloud computing is transforming the way teams collaborate and work on projects. SolidWorks might enhance its cloud-based capabilities, allowing teams to access and edit designs from anywhere, fostering seamless collaboration.
As environmental concerns become increasingly important, SolidWorks could introduce features that help engineers design products with sustainability in mind. This might include tools to assess the environmental impact of materials and manufacturing processes.
AI-powered features could assist engineers in automating repetitive tasks, predicting design performance, and optimizing designs based on vast amounts of data. This integration could significantly speed up the design process and improve accuracy.
Conclusion
SolidWorks has revolutionized the world of engineering and design by providing a comprehensive platform for creating, simulating, and visualizing complex models. Its applications span across diverse industries, from product design and architecture to aerospace and healthcare. The software's user-friendly interface, parametric design capabilities, and realistic simulations have made it a staple tool for engineers and designers worldwide. As technology continues to advance, SolidWorks is poised to embrace trends like generative design, augmented reality, and cloud-based collaboration. These innovations will further enhance the software's capabilities and empower professionals to create even more innovative and efficient designs. As we move forward, SolidWorks will undoubtedly remain a driving force in shaping the future of engineering and design.