- Understanding SolidWorks Simulation
- Types of Analysis in SolidWorks Simulation
- Starting a Simulation Session
- Nonlinear Analysis in SolidWorks
- What is a Nonlinear Problem?
- Handling Nonlinear Problems
- Topology Optimization and Iteration
- Topology Optimization
- Iteration in SolidWorks
- Modal Analysis and Thermal Stress
- Modal Analysis
- Thermal Stress Analysis
- Case Studies: Practical Application
- Static Analysis Example: Eyebar Assembly
- Structural Analysis of Steel Shed
- Thermal Analysis: Heat Sink Assembly
- Conclusion
SolidWorks is a powerful tool that plays a pivotal role in modern engineering, enabling professionals and students alike to execute intricate design, thorough simulation, and detailed analysis. Its versatility extends across various domains, from mechanical and structural engineering to thermal and dynamic simulations. For students embarking on SolidWorks assignments, navigating its capabilities can initially seem daunting but adhering to a structured approach can simplify complex tasks and yield comprehensive solutions. This guide will provide essential help with your Simulation assignment, ensuring you can effectively leverage SolidWorks' features to achieve precise and insightful results in your projects.
Firstly, grasping the fundamental types of analyses available in SolidWorks Simulation is crucial. These include static analysis, which assesses the effects of loads on structures assuming no motion occurs; dynamic analysis, which considers the impact of forces over time; thermal analysis, focusing on temperature distribution and its effects; and nonlinear analysis, addressing scenarios where material properties or loads cause non-proportional responses. Each analysis type demands specific setup considerations and interpretations of results, tailored to the assignment's objectives.
Initiating a simulation session within SolidWorks involves meticulous planning. Begin by defining the scope and objectives of the analysis. This includes detailing the geometry of the model, assigning appropriate material properties, defining boundary conditions such as supports and loads, and selecting the type of analysis (static, dynamic, thermal, etc.). SolidWorks provides intuitive tools to assist in these initial setup stages, ensuring accurate representation and simulation of real-world scenarios.
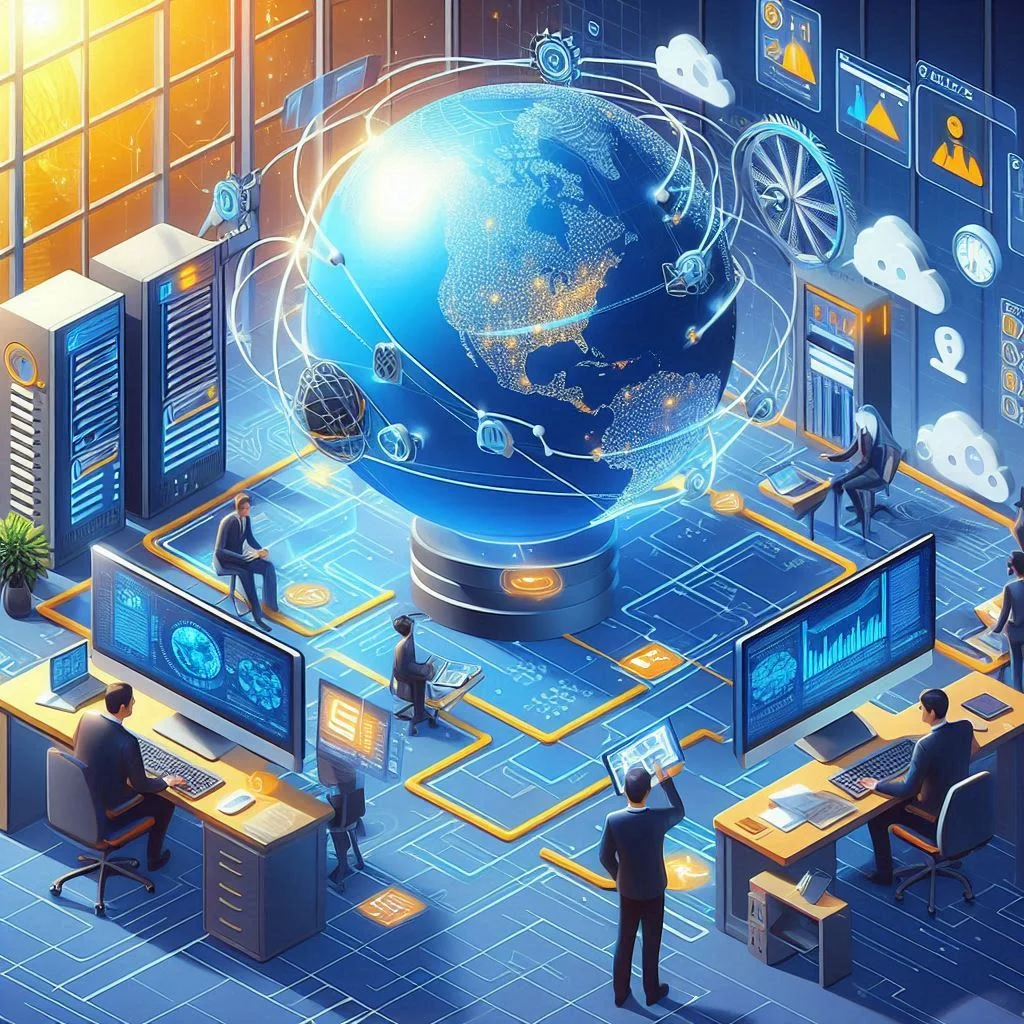
Nonlinear problems in SolidWorks Simulation present unique challenges compared to linear problems. Understanding these distinctions is crucial for effective problem-solving. Nonlinearities can arise from material behaviors (like plasticity or hyperelasticity), geometric complexities (large deformations), or contact interactions (friction, impact). Unlike linear analyses where relationships between forces and displacements remain constant, nonlinear analyses require iterative calculations to converge on accurate solutions, often necessitating segmented calculations to manage complexity and ensure stability.
Moreover, SolidWorks' topology optimization feature revolutionizes design processes by automatically redistributing material within a defined design space to achieve optimal performance objectives. Students can harness this tool to streamline assignments involving weight reduction, structural integrity improvements, or performance enhancements across diverse engineering applications.
In practical applications such as modal analysis and thermal stress assessment, SolidWorks enables students to delve deeper into understanding structural dynamics and thermal behaviors. Modal analysis identifies natural frequencies and corresponding mode shapes, crucial for designing structures to withstand specific vibration frequencies. Meanwhile, thermal stress analysis evaluates structural integrity under varying temperature gradients, offering insights into potential material fatigue or failure due to thermal expansion or contraction.
Case studies further reinforce theoretical knowledge with hands-on application. For instance, conducting static analysis on complex assemblies like the eyebar assembly demands meticulous consideration of material properties, bolted connections, and boundary conditions. Similarly, analyzing steel structures for stress and displacement under specific loads showcases SolidWorks' capability to simulate real-world scenarios accurately, guiding students towards informed design decisions and optimizations.
In conclusion, mastering SolidWorks for engineering assignments requires not just technical proficiency but also a structured approach encompassing comprehensive understanding, methodical setup, iterative refinement, and insightful interpretation of results. By adhering to these principles and actively engaging with the software's capabilities, students can develop proficiency in SolidWorks Simulation, equipping themselves with essential skills for solving diverse engineering challenges effectively.
Understanding SolidWorks Simulation
SolidWorks Simulation is a pivotal tool in the realm of engineering, offering a comprehensive suite of analysis capabilities that are indispensable for designing robust and optimized mechanical systems. By harnessing SolidWorks Simulation, engineers can delve into various types of analyses such as static, dynamic, thermal, and nonlinear studies. Each type caters to distinct engineering challenges, from assessing structural integrity under static loads to predicting dynamic responses to varying forces and temperatures.
The versatility of SolidWorks Simulation extends beyond mere analysis; it empowers users to simulate real-world conditions accurately, ensuring designs meet performance criteria before physical prototypes are built. Starting a simulation session involves meticulous setup of geometry, material properties, and boundary conditions within the intuitive SolidWorks interface, allowing for precise control over every aspect of the analysis process.
Types of Analysis in SolidWorks Simulation
SolidWorks Simulation encompasses a range of analysis types tailored to different engineering needs. Static analysis evaluates the structural integrity under steady loads, ideal for determining safety factors and deformations in static conditions. Dynamic analysis, on the other hand, examines how structures behave under varying loads over time, crucial for assessing resonance and vibration effects. Thermal analysis predicts temperature distributions and heat transfer within components, essential for optimizing cooling systems and preventing overheating. Nonlinear analysis addresses complex material behaviors like plasticity or large deformations, vital for accurately simulating real-world scenarios such as impact or contact mechanics.
Starting a Simulation Session
Initiating a successful simulation session in SolidWorks begins with clearly defining the analysis objectives. For stress analysis, specify the expected loads and constraints to simulate the response of materials to mechanical forces accurately. In thermal analysis, define heat sources, thermal conductivity properties, and environmental conditions to model heat dissipation and temperature gradients effectively. Frequency analysis requires setting up resonance studies to identify natural frequencies and mode shapes of structures, crucial for avoiding resonance-induced failures. Setting up model geometry involves creating or importing CAD models, assigning material properties, and defining boundary conditions such as fixed supports or applied loads to accurately simulate real-world behaviors.
Nonlinear Analysis in SolidWorks
dvancement in engineering simulation, enabling engineers to tackle complex real-world scenarios that traditional linear analyses cannot adequately capture. Unlike linear problems, which assume a proportional relationship between loads and displacements, nonlinear analyses consider factors such as material nonlinearity, large deformations, and contact interactions. These elements are pivotal in simulating scenarios like plastic deformation of materials, structural collapse under extreme loads, or mechanisms involving frictional contact.
SolidWorks addresses these challenges by breaking down nonlinear analyses into smaller, iterative steps, ensuring accurate convergence towards a solution. Each step refines the simulation based on updated conditions from the previous iteration, progressively improving the accuracy of results until convergence criteria are met. This iterative process is essential for handling the complexities inherent in nonlinear behavior, such as stress concentrations, post-yield behavior of materials, and contact forces between components.
By leveraging SolidWorks Simulation tools for nonlinear analysis, engineers can simulate diverse scenarios with confidence, from automotive crash simulations to nonlinear material modeling in aerospace applications. This capability not only enhances design accuracy but also empowers engineers to optimize product performance, durability, and safety under realistic operating conditions, ensuring robust designs that meet stringent performance criteria across various industries.
What is a Nonlinear Problem?
Nonlinear problems in SolidWorks Simulation typically arise from complexities such as material nonlinearities, large deformations, or contact interactions within the model. Unlike linear problems where the relationship between loads, displacements, and material properties remains linear throughout, nonlinear problems exhibit varying degrees of change in these relationships under different conditions. This variation necessitates a more sophisticated analysis approach to accurately capture the behavior of materials and structures under realistic operating conditions.
Handling Nonlinear Problems
SolidWorks addresses nonlinear analyses by breaking them down into incremental steps, where each step iteratively refines the solution until convergence is achieved. This iterative process is essential because nonlinear behaviors can lead to unpredictable outcomes without careful stepwise refinement. Setting up accurate nonlinear boundary conditions, such as frictional contact or large strain formulations, is critical to simulating real-world scenarios effectively. Interpreting nonlinear results involves understanding how different parameters influence the overall behavior and ensuring that the model's response aligns with physical expectations under nonlinear loading conditions.
Topology Optimization and Iteration
Topology optimization is a powerful tool in SolidWorks that revolutionizes design by optimizing material distribution within a given design space. It operates on the principle of minimizing material volume while satisfying structural and performance constraints. By iteratively redistributing material based on stress, displacement, or other performance metrics, topology optimization uncovers novel and efficient designs that traditional methods might overlook.
In practice, this iterative process involves setting up initial design parameters and constraints, such as maximum allowable stress or displacement thresholds. SolidWorks then iterates through multiple design iterations, gradually refining the material distribution until it converges on an optimized solution. This approach not only reduces material usage, leading to lighter and more efficient structures, but also enhances overall performance by ensuring designs meet functional requirements.
Furthermore, topology optimization in SolidWorks accommodates complex geometries and multiple load scenarios, allowing engineers to explore a wide range of design possibilities without compromising structural integrity. By integrating topology optimization into their workflow, students and professionals alike can leverage SolidWorks’ capabilities to innovate and optimize designs that are both robust and resource-efficient, aligning with modern engineering principles of sustainability and performance optimization.
Topology Optimization
SolidWorks offers topology optimization to design lightweight structures by distributing material optimally. This process begins with defining the structural goals and constraints, such as maximum stress limits or displacement requirements. SolidWorks then iteratively removes material from non-critical areas while preserving structural integrity, resulting in an optimized design that minimizes weight without compromising performance.
Implementing topology optimization involves defining design constraints and loading conditions. Engineers specify factors like allowable stress levels, manufacturing constraints, and operational loads. SolidWorks Simulation iteratively adjusts the material distribution to meet these criteria, generating designs that are both efficient and functional. By simulating multiple scenarios and analyzing results, engineers can refine designs to achieve optimal performance under real-world conditions.
Iteration in SolidWorks
Iteration is used in SolidWorks for tasks like mesh refinement, convergence checks in nonlinear analyses, and optimizing designs based on analysis results. In mesh refinement, SolidWorks adjusts the computational mesh to ensure accurate simulation results. For nonlinear analyses, iteration is crucial to achieve convergence, where the solution stabilizes to accurately reflect real-world behavior. Furthermore, SolidWorks enables iterative optimization based on analysis outcomes, allowing engineers to refine designs incrementally for improved performance and efficiency. Understanding how iteration drives refinement and accuracy empowers engineers to leverage SolidWorks effectively in complex simulation and design scenarios, ensuring robust and reliable engineering solutions.
Modal Analysis and Thermal Stress
Modal analysis and thermal stress analysis are critical aspects of structural engineering that leverage SolidWorks Simulation's capabilities to enhance design robustness and reliability. Modal analysis investigates the natural frequencies and mode shapes of a structure, essential for understanding its dynamic behavior under varying loads. By identifying resonant frequencies and corresponding mode shapes, engineers can mitigate potential vibration issues and optimize designs to meet performance criteria.
On the other hand, thermal stress analysis addresses the effects of temperature differentials within a structure. SolidWorks Simulation enables engineers to simulate thermal gradients, predict thermal expansion-induced stresses, and assess material integrity under thermal loading conditions. This capability is crucial in designing components subjected to fluctuating temperatures, ensuring they withstand operational environments without failure due to thermal stresses.
Both modal analysis and thermal stress analysis play pivotal roles in ensuring structural integrity and performance across diverse engineering applications. By integrating these analyses early in the design phase, engineers can refine designs iteratively, optimize material usage, and enhance overall product durability. SolidWorks Simulation's comprehensive tools empower engineers to simulate real-world conditions accurately, leading to more informed design decisions and ultimately delivering robust, efficient, and reliable engineering solutions.
Modal Analysis
Determine the natural frequencies and mode shapes: Modal analysis in SolidWorks helps engineers identify the natural frequencies at which a structure vibrates without external excitation. This information is crucial for understanding how the structure will respond to dynamic loads and vibrations. By determining these frequencies, engineers can ensure that potential resonance issues are addressed during the design phase, which is critical for preventing structural failures due to excessive vibrations.
Mode shapes illustrate the vibration patterns: Mode shapes visually represent how the structure vibrates at different natural frequencies. These patterns show areas of high and low displacement, aiding engineers in identifying critical points prone to stress and potential failure. Understanding mode shapes helps in optimizing designs to reduce unwanted vibrations and improve structural performance under dynamic conditions, ensuring the reliability and durability of the final product.
Thermal Stress Analysis
Thermal stress occurs due to temperature gradients: Thermal stress arises when temperature differences within a structure cause uneven expansion and contraction of materials. This phenomenon can lead to mechanical deformation, fatigue, or even failure over time. SolidWorks Simulation enables engineers to predict these stresses accurately by simulating heat transfer, thermal expansion coefficients, and thermal boundary conditions. By identifying areas prone to thermal stress, engineers can design effective thermal management solutions, such as heat sinks or insulation, to mitigate potential issues and ensure the longevity of the structure.
Analyzing thermal stress involves setting up heat sources: To simulate thermal stress accurately, engineers define heat sources such as electronic components or environmental conditions that affect temperature distribution. Material properties, including thermal conductivity and specific heat capacity, are crucial inputs for determining how materials respond to thermal loads. SolidWorks allows for precise boundary conditions, including convection and radiation effects, to capture real-world thermal behavior. By analyzing thermal stresses early in the design process, engineers can optimize material selections and structural geometries to enhance thermal performance and reliability under operating conditions.
Case Studies: Practical Application
SolidWorks assignments often include detailed case studies that simulate real-world engineering challenges. These case studies not only test theoretical knowledge but also require practical application of SolidWorks Simulation tools. For instance, conducting a static analysis on an eyebar assembly involves meticulous setup of material properties, bolted connections, and boundary conditions. Students must accurately define constraints and loading conditions to simulate the assembly’s behavior under applied forces, ensuring structural integrity and safety.
Similarly, analyzing a steel shed’s structural stability under varying loads demands proficiency in SolidWorks Simulation. By implementing finite element analysis (FEA), students can calculate stress distribution and displacement to assess design adequacy. Recommendations for design enhancements based on simulation results are crucial, demonstrating the iterative nature of engineering design and analysis.
Furthermore, thermal analysis of a heat sink assembly illustrates the application of SolidWorks Simulation in heat transfer studies. Students learn to model convection, radiation, and thermal conductivity properties to optimize heat dissipation efficiency. These case studies not only reinforce theoretical concepts but also equip students with practical skills essential for tackling complex engineering challenges in industries ranging from aerospace to mechanical engineering.
Mastering SolidWorks Simulation through such case studies prepares students to confidently apply their knowledge in solving real-world engineering problems, enhancing their readiness for professional practice and innovation in the field.
Static Analysis Example: Eyebar Assembly
Performing a static analysis on an eyebar assembly involves meticulously defining material properties such as ABS for the eyebar and Aluminum 6061 Alloy for the bolts. SolidWorks Simulation tools enable accurate simulation of bolted connections, ensuring realistic contact interactions between parts. By fixing constraints appropriately and applying the 1000N load evenly distributed on the end face, engineers can predict stress distributions and structural integrity. This process aids in identifying potential failure points and optimizing design robustness through iterative adjustments in SolidWorks.
Structural Analysis of Steel Shed
Conducting a static analysis on a steel shed requires assessing stress and displacement under varied loads, including maximum roof and floor loads. SolidWorks facilitates detailed evaluation of structural components using AISI 304 material properties and ISO 40x40 square tube geometry. Analysis results guide engineers in recommending enhancements to meet displacement criteria, such as adjusting material thickness or reinforcing critical areas. This iterative process ensures structural reliability and compliance with design specifications in real-world applications.
Thermal Analysis: Heat Sink Assembly
Analyzing a heat sink assembly with SolidWorks Simulation involves modeling temperature gradients and heat flux distributions accurately. By specifying thermal properties of materials like 1060 Aluminum Alloy and ceramic porcelain, engineers simulate convection and radiation effects. This comprehensive analysis aids in optimizing heat dissipation efficiency and preventing thermal failures. The resultant temperature gradient plots, heat flux maps, and vector diagrams provide insights into thermal management strategies, crucial for designing reliable electronic cooling systems.
These detailed explanations provide students with a practical understanding of how to approach and execute SolidWorks assignments related to static, structural, and thermal analyses. Each section emphasizes the importance of leveraging SolidWorks Simulation tools to achieve accurate results and make informed design decisions.
Conclusion
Successfully completing SolidWorks assignments demands more than just technical proficiency; it requires a blend of systematic approach, problem-solving skills, and practical application of engineering principles. SolidWorks Simulation, as a tool, offers a wide array of capabilities from static and dynamic analyses to thermal and nonlinear simulations. Each of these analyses serves a unique purpose in assessing the performance and behavior of engineering designs under different conditions.
Understanding the types of analyses available in SolidWorks Simulation is crucial. It enables engineers to choose the appropriate simulation type based on the specific requirements of the design problem at hand. For instance, static analysis helps in evaluating the structural integrity by simulating steady-state loads, while dynamic analysis is used to study the dynamic response of structures subjected to varying loads over time.
Setting up simulations involves accurately defining the geometry, material properties, boundary conditions, and loads. This step ensures that the simulation replicates real-world scenarios as closely as possible. Interpreting results from simulations involves not only understanding numerical outputs but also translating them into meaningful insights about the performance and safety of the design.
Moreover, suggesting design improvements based on simulation results is a critical aspect of the engineering process. It requires creativity and analytical thinking to optimize designs for factors such as strength, weight, and cost-effectiveness.
Regular practice is key to mastering SolidWorks Simulation. It not only enhances technical skills but also improves problem-solving abilities and confidence in tackling complex engineering challenges. By approaching assignments with a structured methodology—understanding the problem, setting up simulations effectively, interpreting results critically, and proposing improvements—students can develop a robust foundation in engineering analysis using SolidWorks.