- Understanding the Importance of a Faucet Assembly Drawing Sheet
- Explode Lines: Illustrating Component Relationships
- Derived Views: Expanding on Standard Views
- Section Views: Revealing Internal Features
- Detail Views: Focusing on Specific Areas
- Additional Drawing Views: Enhancing Visual Representation
- Notes and Other Annotations: Providing Essential Information
- Finalizing the Faucet Assembly Drawing Sheet
- Practical Tips for Creating Effective Assembly Drawings
- Common Challenges and How to Overcome Them
- Conclusion
Creating a detailed faucet assembly drawing sheet in SolidWorks involves several steps and techniques to accurately depict the assembly and its components. This blog will guide you through the process of creating a comprehensive faucet assembly drawing sheet, focusing on key elements such as explode lines, derived views, section views, detail views, additional drawing views, and annotations.
Understanding how to create a faucet assembly drawing sheet is essential for anyone tackling drawing assignments in SolidWorks. Whether you’re a student seeking help with SolidWorks assignments or a professional aiming to enhance your technical documentation skills, mastering these techniques will significantly improve your ability to communicate complex assembly details clearly and effectively.
Explode lines, derived views, section views, and detail views are not just features but critical tools in ensuring that every aspect of the assembly is meticulously documented. This comprehensive approach aids in visualizing how components fit together, identifying potential assembly issues, and ensuring that all necessary information is conveyed accurately. As you progress through this blog, you'll gain valuable insights and practical tips to create precise and professional-quality faucet assembly drawing sheets, streamlining your drawing assignments and providing excellent help with SolidWorks assignments.
Understanding the Importance of a Faucet Assembly Drawing Sheet
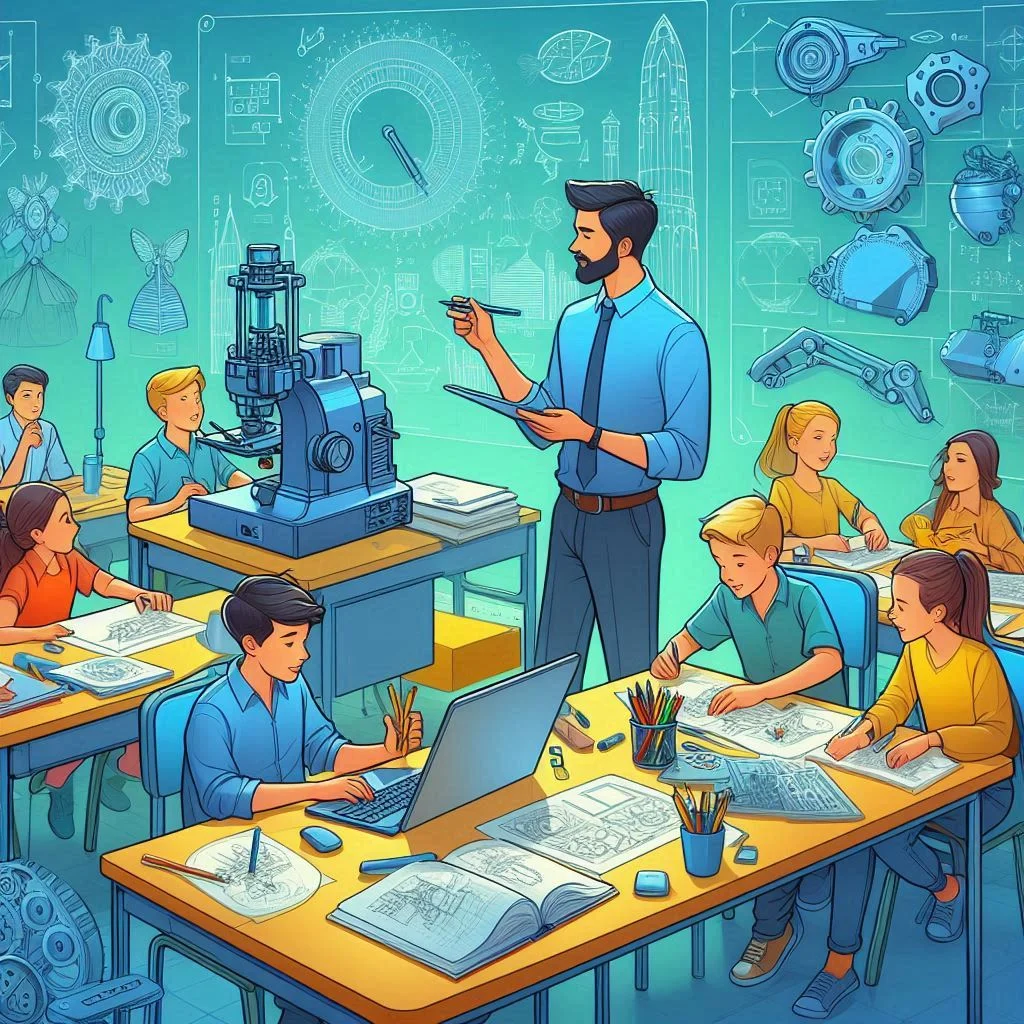
A faucet assembly drawing sheet serves as a vital document in the design and manufacturing process. It provides a visual representation of the assembly, detailing how components fit together, their relationships, and specific features that need attention. This drawing sheet is essential for engineers, manufacturers, and quality control personnel, ensuring that the final product is constructed accurately and meets design specifications.
Explode Lines: Illustrating Component Relationships
Explode lines are crucial for visualizing how components fit together in an assembly. They provide a clear representation of the spatial relationships and assembly order of parts. In SolidWorks, creating explode lines involves the following steps:
- Explode Line Sketch: Begin by opening the faucet assembly document in SolidWorks and switch to the exploded configuration. The exploded view helps in visualizing the individual components separately.
- Add Explode Lines: Use the Explode Line Sketch tool to draw lines between components, indicating how they are connected. This tool is particularly useful for complex assemblies where understanding the sequence and position of parts is essential.
- Jog the Lines: Sometimes, straight lines may overlap or not clearly depict the assembly's structure. In such cases, you can jog the lines to improve clarity. The explode lines are displayed in a phantom line font, which is a standard practice to distinguish them from solid lines representing actual part edges.
- Adjust Line Properties: You can customize the appearance of explode lines, including line thickness and style, to enhance readability and meet specific documentation standards.
Explode lines not only aid in visualizing the assembly but also assist in identifying potential assembly issues, such as interference or misalignment.
Derived Views: Expanding on Standard Views
Derived views in SolidWorks allow you to create additional views from existing standard views without having to modify the model. This feature is particularly useful for presenting different perspectives of the assembly, such as isometric, dimetric, or trimetric views.
- Standard Views Setup: Start by ensuring that your drawing sheet includes the necessary standard views, such as front, top, and right views. These views serve as the basis for creating derived views.
- Creating Derived Views: To create a derived view, select an existing standard view and use the Derived View command. You can then choose the desired orientation for the new view. Derived views can provide alternative perspectives that highlight different aspects of the assembly, such as internal components or hidden features.
- Adjusting Derived Views: You can rotate, scale, or reposition derived views to fit the drawing sheet layout better. This flexibility allows you to present the assembly in the most informative and accessible manner.
- Using Named Views: SolidWorks allows you to save specific orientations of your model as named views. These can be used to quickly create derived views in the drawing sheet, ensuring consistency and saving time during the documentation process.
Derived views are instrumental in providing a comprehensive understanding of the assembly, especially for complex designs with multiple components and intricate details.
Section Views: Revealing Internal Features
Section views are used to cut through an assembly to reveal internal features, such as connections, interfaces, and inner components. In a faucet assembly, section views can provide insights into the construction and assembly of internal parts, which are not visible in standard or derived views.
- Creating Section Views: To create a section view, select a parent view, such as the top view of the faucet assembly. Use the Section View tool to draw a section line through the parent view. This line defines the cutting plane and can be positioned to highlight specific areas of interest.
- Adjusting Section Properties: After creating the section view, you can adjust its properties, including the type of section (full, half, offset, aligned) and the position of the cutting plane. For example, an aligned section view can be used to show features that are not parallel to the principal planes.
- Crosshatching: The sectioned components are automatically displayed with crosshatching, indicating the cut material. You can customize the crosshatching pattern, scale, and angle to differentiate between materials or to highlight specific parts. For instance, different hatch patterns can be used to distinguish between metal and plastic components.
- Detailing Internal Features: Section views are particularly valuable for detailing internal features, such as the faucet pipe walls, connections, and seals. These details are crucial for understanding the functionality and assembly of the faucet.
- Annotation of Section Views: It's important to annotate section views with relevant information, such as part numbers, material specifications, and assembly instructions. This information helps in the manufacturing and quality control processes.
Section views provide a detailed look inside the assembly, making it easier to understand how components interact and fit together. They are essential for verifying the design's integrity and ensuring that all parts are correctly aligned and connected.
Detail Views: Focusing on Specific Areas
Detail views are used to magnify specific areas of a drawing, providing an enlarged view of intricate details that might not be clearly visible in the standard or section views. These views are particularly useful for highlighting critical areas, such as the connection points or small components.
- Creating Detail Views: To create a detail view, select a parent view and use the Detail View tool to draw a circular or irregular boundary around the area of interest. This boundary defines the region that will be enlarged in the detail view.
- Scaling the Detail View: Detail views are typically displayed at a larger scale than the parent view. This enlargement helps in clearly showing small features, such as fasteners, seals, or intricate shapes. In the case of a faucet assembly, a detail view might focus on the connection of the faucet handle or the threading on a pipe.
- Annotating Detail Views: Detail views should be annotated with relevant information, such as dimensions, tolerances, and surface finishes. This information is crucial for manufacturing and inspection purposes, ensuring that the components are produced to the required specifications.
- Positioning Detail Views: Position the detail view close to the area of interest on the drawing sheet, but ensure it does not overlap other views or annotations. This organization helps in maintaining a clean and professional layout.
Detail views provide a closer look at specific areas, making them indispensable for highlighting critical features and ensuring they are clearly understood and accurately represented.
Additional Drawing Views: Enhancing Visual Representation
Additional drawing views in SolidWorks, such as alternate position views, auxiliary views, crop views, broken-out sections, and broken views, provide different perspectives and enhance the visual representation of the assembly.
- Alternate Position Views: These views display overlays of two or more positions of an assembly component, often used to show the range of motion. For example, the faucet handles can be shown in different positions to illustrate their range of motion. The overlay views are displayed in phantom lines, distinguishing them from the main view.
- Auxiliary Views: Auxiliary views are projected perpendicular to a reference edge or plane, showing the true shape of inclined or oblique surfaces. They are useful for accurately depicting features that are not parallel to the principal planes.
- Crop Views: Crop views focus on a specific area of a drawing by removing everything outside a sketched profile. This view is useful for isolating and magnifying a particular feature or area of interest, reducing visual clutter and drawing attention to key details.
- Broken-out Sections: These views remove material inside a sketched profile, exposing internal features without creating a full section view. This method is particularly useful for showing internal components in a localized area.
- Broken Views: Broken views are used to shorten long parts with uniform cross-sections, allowing them to fit on the drawing sheet without losing detail. This technique is often used for long pipes, shafts, or beams.
- Overlay and Combination Views: Sometimes, combining different view types (e.g., an alternate position view with a broken-out section) can provide a comprehensive understanding of the assembly. These combinations should be used judiciously to avoid clutter and ensure clarity.
These additional views enhance the overall understanding of the assembly by providing different perspectives and highlighting various aspects. They are essential for conveying complete and accurate information to those involved in the manufacturing and inspection processes.
Notes and Other Annotations: Providing Essential Information
Annotations are a critical part of any drawing sheet, providing essential information that cannot be conveyed through visuals alone. In a faucet assembly drawing sheet, annotations might include notes, multi-jog leaders, and surface finish symbols.
- Notes and Multi-Jog Leaders: Notes can provide textual information, such as assembly instructions, material specifications, or warnings. Multi-jog leaders are used to point to multiple features from a single note, making it clear which components the note refers to. For example, a note might specify the torque requirements for screws, with multi-jog leaders pointing to each relevant screw in the assembly.
- Surface Finish Symbols: Surface finish symbols indicate the required surface quality of components. They can specify characteristics such as the type of finish (e.g., smooth, rough), direction of lay, roughness, production method, material removal, and rotation. For instance, a faucet handle might have a surface finish symbol specifying a circular finish and a maximum roughness value.
- Dimensional and Tolerance Annotations: These annotations provide critical information about the dimensions and tolerances of components, ensuring they are manufactured to the correct size and fit. Dimensional annotations might include overall dimensions, hole sizes, and thread specifications. Tolerance annotations specify allowable variations in dimensions, ensuring proper fit and function.
- Geometric Tolerances: Geometric tolerance symbols define the permissible limits of form, orientation, and location for features. These symbols ensure that parts will fit together correctly and function as intended. For example, geometric tolerances might specify the allowable deviation from roundness for a cylindrical feature or the flatness of a mating surface.
- Datum Features: Datum symbols indicate reference points, lines, or surfaces used to control the geometry of the assembly. These features are critical for ensuring consistent manufacturing and assembly processes. For example, a datum symbol might indicate the primary reference surface for aligning other components.
Finalizing the Faucet Assembly Drawing Sheet
After incorporating all necessary views, annotations, and symbols, your faucet assembly drawing sheet should provide a thorough and precise representation of the assembly. Here are the final steps to ensure your drawing sheet is complete and professional:
- Review for Completeness: Ensure that all components are represented and that all necessary views are included. Check that explode lines, derived views, section views, detail views, and additional views are correctly placed and clearly labeled.
- Check Annotations: Verify that all annotations, including notes, multi-jog leaders, surface finish symbols, dimensions, tolerances, and geometric tolerances, are accurate and complete. Ensure that the annotations do not overlap or clutter the drawing.
- Layout and Organization: Arrange the views and annotations in a logical and organized manner. The drawing sheet should be easy to read and navigate, with a clear hierarchy of information. Use consistent spacing and alignment to maintain a professional appearance.
- Title Block and Revision History: Ensure that the title block contains all necessary information, including the drawing title, part number, author, date, and revision history. This information is crucial for version control and documentation purposes.
- Compliance with Standards: Verify that your drawing sheet complies with relevant industry standards and company guidelines. This includes standards for dimensioning, tolerancing, and annotation practices. Adhering to these standards ensures that the drawing will be understood and accepted by all stakeholders.
Practical Tips for Creating Effective Assembly Drawings
Creating effective assembly drawings involves more than just following steps. Here are some practical tips to enhance the quality and clarity of your drawings:
- Simplify Where Possible: Avoid overcomplicating the drawing with unnecessary details. Focus on the most critical aspects and use views and annotations to clarify complex areas.
- Use Color Wisely: If your documentation system allows for color printing, use color to differentiate between different types of annotations or components. However, ensure that the drawing remains clear and legible when printed in black and white.
- Leverage SolidWorks Tools: SolidWorks offers many tools and features to aid in creating assembly drawings. Explore and utilize tools like Auto Dimension, Balloon Annotations, and View Alignment to streamline the process and enhance accuracy.
- Collaborate and Review: Assembly drawings often benefit from multiple reviews. Collaborate with colleagues to review the drawing for completeness and accuracy. Peer reviews can catch errors or omissions that you might have missed.
- Document Design Intent: Use notes and annotations to document the design intent clearly. This includes specifying critical dimensions, assembly sequences, and special instructions that are not immediately obvious from the visuals alone.
Common Challenges and How to Overcome Them
Creating detailed assembly drawings can present several challenges. Here are some common issues and strategies to overcome them:
- Complex Assemblies: For very complex assemblies, it might be challenging to fit all necessary views and annotations on a single drawing sheet. Consider using multiple sheets or creating simplified representations of certain subassemblies to manage complexity.
- Cluttered Annotations: Overlapping or cluttered annotations can make a drawing difficult to read. Use multi-jog leaders, break lines, and callouts to organize annotations clearly. Ensure there is sufficient spacing between different elements.
- Consistency in Annotation: Inconsistencies in annotation style or placement can confuse readers. Establish and follow a consistent set of annotation standards and practices. Use SolidWorks’ built-in templates and styles to maintain uniformity.
- Interpreting Design Changes: Design changes during the development process can require significant updates to assembly drawings. Keep detailed revision histories and use version control to manage changes effectively. Regularly update the drawing to reflect the latest design.
Conclusion
Creating a faucet assembly drawing sheet in SolidWorks is a detailed process that involves careful planning and execution. By following the steps outlined in this guide, you can create a comprehensive and accurate drawing sheet that effectively communicates the design intent and assembly details.
Remember to focus on key elements such as explode lines, derived views, section views, detail views, additional drawing views, and annotations. Each of these components plays a critical role in ensuring that the assembly is clearly understood and can be accurately manufactured.
Finally, always review your drawing sheet for completeness, clarity, and compliance with standards. By maintaining high standards and leveraging the powerful tools available in SolidWorks, you can produce professional-quality assembly drawings that meet the needs of engineers, manufacturers, and quality control personnel.
Creating a detailed and well-organized faucet assembly drawing sheet is not just about following steps but also about understanding the design and effectively communicating that understanding to others involved in the manufacturing and assembly process. With practice and attention to detail, you can master this essential aspect of mechanical design documentation.