- The Fundamentals of Meshing
- Advanced Meshing Techniques
- Element Selection Strategies
- Optimizing for Assignment Accuracy
- Case Studies
- Challenges and Solutions
- Conclusion
In the realm of Finite Element Analysis (FEA), achieving accurate results in assignments requires a deep understanding of advanced meshing and element selection. In this blog, we delve into the intricacies of these techniques to optimize FEA accuracy. Understanding these concepts is essential for effectively applying FEA methods to solve engineering problems accurately and efficiently.
To begin with, meshing serves as the foundational step in any FEA simulation. It involves dividing the geometric model into discrete elements, forming a mesh that facilitates the application of mathematical equations. The significance of meshing lies in striking a delicate balance between capturing intricate details and maintaining computational efficiency. Understanding the nuances of mesh density is crucial—a denser mesh provides more accurate results, but it also demands increased computational resources. Thus, finding the optimal mesh density becomes a delicate task, requiring a keen eye for the specific demands of each simulation.
Moving on, the types of meshing employed play a pivotal role in determining the accuracy of FEA simulations. Structured meshes, characterized by a regular arrangement of elements, offer simplicity and computational efficiency. On the other hand, unstructured meshes provide flexibility, allowing for a more accurate representation of complex geometries. Navigating the trade-offs between these meshing types becomes a skill in itself, as engineers must choose the most suitable approach based on the nature of the finite element analysis assignment.
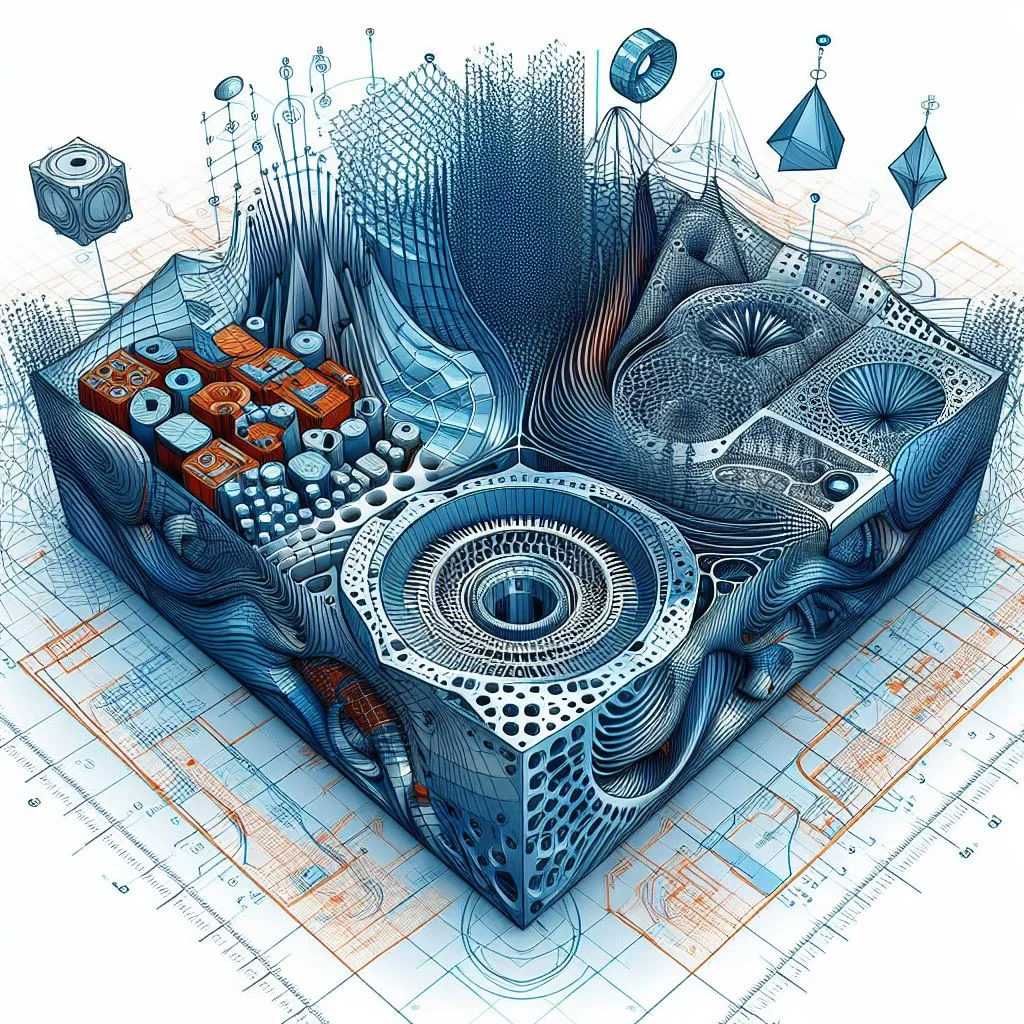
Advanced meshing techniques further enhance the precision of FEA simulations. Adaptive mesh refinement stands out as a powerful tool, dynamically adjusting mesh density based on the evolving solution requirements. This not only ensures accurate results but also optimizes computational resources by concentrating efforts where they matter most. Transitioning from 2D to 3D meshing introduces another layer of complexity. Understanding how this transition impacts accuracy is crucial for successful FEA simulations. Strategies for seamlessly integrating 2D and 3D meshing can make a significant difference in the reliability of results.
Element selection is equally critical in the FEA process. Choosing the right element type involves considerations of geometry, loading conditions, and the physics of the problem at hand. Each element type has its own set of advantages and limitations, making the selection process a nuanced task. Element quality and the application of shape functions also come into play. Ensuring high-quality elements with well-defined shape functions is paramount for accurate FEA results. Engineers must constantly evaluate and refine element selection strategies to align with the intricacies of the simulated problems.
In the quest for optimizing assignment accuracy, mesh sensitivity analysis emerges as a valuable practice. This involves systematically varying mesh parameters to understand their impact on the results. The goal is to identify the sweet spot where mesh density is sufficient for accuracy without unnecessarily burdening computational resources. Fine-tuning element selection based on the specific characteristics of the problem further refines the simulation, ensuring that the chosen elements are best suited for the given conditions.
In real-world applications, these advanced meshing and element selection techniques prove their worth. Case studies showcase their effectiveness in solving complex engineering problems, demonstrating the practical application of theoretical concepts. The challenges encountered in meshing and element selection are diverse but not insurmountable. With the right strategies, these challenges can be addressed, paving the way for accurate and reliable FEA assignments.
Integrating these techniques with Solidworks simulations adds an extra layer of efficiency. Understanding how to seamlessly merge advanced meshing and element selection with Solidworks enhances the overall synergy between engineering expertise and software capabilities. This integration streamlines the simulation process, allowing for more robust and accurate results.
The Fundamentals of Meshing
Understanding Mesh Density is a foundational concept crucial for achieving precision in Finite Element Analysis (FEA). In the realm of FEA simulations, mesh density refers to the number of elements used to discretize the geometry of a model. Striking the right balance in mesh density is vital as it directly impacts the accuracy of the results while considering computational efficiency.
Mesh density plays a pivotal role in capturing critical details of a model. In scenarios where intricate features or areas of high stress concentration exist, a finer mesh is required to ensure accurate representation. However, uniformly refining the mesh across the entire model can lead to unnecessary computational costs. Therefore, a nuanced approach involves selectively increasing mesh density in regions of interest while maintaining a coarser mesh in less critical areas.
Moving beyond mesh density, a crucial aspect of Finite Element Analysis is the selection of appropriate meshing techniques. There are two primary types: structured and unstructured meshes. Structured meshes, organized in a grid-like pattern, are suitable for regular geometries, offering ease of generation and computational efficiency. On the other hand, unstructured meshes, with irregularly shaped elements, are more flexible and adaptable to complex geometries but may require more computational resources.
Understanding when to employ structured or unstructured meshes is key to optimizing results in FEA assignments. Regular geometries might benefit from the efficiency of structured meshes, while complex and irregular shapes often necessitate the adaptability of unstructured meshes. The choice between these techniques depends on the specific characteristics of the model and the accuracy requirements of the simulation.
In conclusion, mesh density and the choice between structured and unstructured meshes are intricately linked elements in the pursuit of accurate FEA results. A judicious understanding of these concepts allows engineers to navigate the delicate balance between capturing critical details and ensuring computational efficiency in their assignments.
Advanced Meshing Techniques
Adaptive Mesh Refinement is a cutting-edge technique that empowers engineers to dynamically adjust mesh density in specific areas, responding to the local solution requirements of a Finite Element Analysis (FEA). Unlike traditional static meshing, adaptive mesh refinement allows for a more efficient allocation of computational resources by concentrating mesh elements in regions of interest. This dynamic adjustment not only enhances the accuracy of FEA results but also minimizes unnecessary computational costs associated with uniform meshing. By focusing computational effort where it matters most, engineers can achieve more precise simulations without compromising efficiency.
Transitioning from 2D to 3D meshing poses a unique set of challenges in the realm of FEA simulations. The shift from a two-dimensional representation to a three-dimensional model introduces nuances that can impact the accuracy of results. Engineers must navigate factors such as geometric complexity and additional degrees of freedom. Strategies for seamless transition involve careful consideration of element types, mesh density, and boundary conditions. Understanding the intricacies of this transition is crucial for obtaining improved accuracy in FEA simulations, ensuring that the third dimension is appropriately captured without introducing unnecessary computational overhead. By implementing effective strategies, engineers can navigate the complexities of 2D to 3D meshing, optimizing their simulations for enhanced accuracy and reliability.
Element Selection Strategies
In the realm of Finite Element Analysis (FEA), the process of selecting the right element type is a pivotal step that profoundly impacts the accuracy of your assignments. Each element type possesses unique characteristics, and understanding their strengths and limitations is crucial for successful simulations. For instance, linear elements may be suitable for basic analyses, while quadratic elements offer higher accuracy in capturing complex geometries and variations in material properties.
Moreover, delving into the realm of element quality unveils its critical role in the reliability of FEA results. Element quality is essentially a measure of how well an element represents the physical reality of the structure being analyzed. Poor-quality elements can introduce errors and inaccuracies in the simulation, leading to unreliable outcomes. Shape functions, which define the spatial distribution of displacements within an element, directly contribute to element quality.
Ensuring optimal element quality involves employing techniques to evaluate and enhance these shape functions. This includes refining mesh density in specific regions, adjusting element types based on the analysis requirements, and validating the results against known solutions or physical testing. By paying meticulous attention to element selection and quality, you lay the foundation for precise and trustworthy FEA assignments, delivering results that align closely with real-world behavior.
Optimizing for Assignment Accuracy
Optimizing for assignment accuracy is a critical aspect of achieving reliable results in Finite Element Analysis (FEA). Mesh sensitivity analysis is a sophisticated technique that allows engineers to assess the impact of varying mesh densities on the precision of FEA outcomes. This involves systematically adjusting mesh parameters and observing changes in results to identify the optimal mesh for specific assignments. Engineers can gain valuable insights into how the mesh influences the solution, enabling them to strike the right balance between accuracy and computational efficiency.
Moreover, fine-tuning element selection is another pivotal step in the pursuit of accuracy. This process involves adjusting the type and characteristics of elements based on the unique features of the engineering problem. By aligning the element selection with the problem's intricacies, engineers can enhance the fidelity of their FEA simulations. Fine-tuning is an iterative process, often requiring a keen understanding of the structural behavior and the desired level of analysis precision. It allows for a tailored approach, ensuring that the chosen elements accurately capture the nuances of the real-world scenario, ultimately elevating the overall accuracy of FEA simulations.
Case Studies
In delving into the practical realm of FEA, examining real-world applications through case studies is paramount. These case studies serve as illuminating windows into the successful application of advanced meshing and element selection techniques in tackling intricate engineering challenges.
One notable case study involves the analysis of a complex mechanical structure subjected to varying loads. By employing adaptive mesh refinement, the simulation dynamically adjusted the mesh density in regions of high stress, providing a more accurate representation of the structural response. This adaptive approach not only enhanced the accuracy of stress predictions but also optimized computational resources.
Another compelling example revolves around the transition from 2D to 3D meshing in a fluid dynamics simulation. The strategic use of different element types facilitated a seamless transition, capturing the fluid flow intricacies with enhanced precision. This case study underscores the importance of thoughtful element selection and its direct impact on the accuracy of simulations.
These real-world applications provide valuable insights into the effectiveness of advanced meshing and element selection strategies. By navigating through the challenges posed by complex engineering problems, these case studies offer a practical guide for implementing these techniques effectively in your own FEA assignments.
Challenges and Solutions
In the realm of Finite Element Analysis (FEA), encountering challenges in meshing and element selection is inevitable. Common pitfalls include issues like mesh distortion, element aspect ratio problems, and difficulties in capturing boundary layer effects. These challenges can compromise the accuracy of simulation results and hinder the reliability of FEA assignments.
To overcome mesh distortion challenges, practitioners often employ techniques such as mesh smoothing and optimization algorithms. These approaches help alleviate distortions, ensuring a more accurate representation of the physical structure in the simulation. Additionally, addressing element aspect ratio problems involves refining the mesh in critical areas and selecting appropriate element types to maintain numerical stability.
Capturing boundary layer effects, especially in fluid dynamics simulations, requires careful consideration. Implementing boundary layer meshing techniques and adjusting mesh parameters can enhance the simulation's ability to model flow characteristics accurately.
In the integration phase with Solidworks, another set of challenges may arise. Mismatched mesh formats, data transfer issues, and software compatibility problems can impede a smooth workflow. However, understanding the intricacies of Solidworks simulations and adopting standardized data exchange practices can facilitate seamless integration. Leveraging shared databases and ensuring proper units and scaling between FEA software and Solidworks contribute to a more cohesive simulation environment.
Ultimately, adeptly navigating these challenges strengthens your FEA expertise, ensuring that your simulations are not only accurate but also reliable in real-world engineering scenarios. Enhancing the synergy between advanced meshing and element selection techniques with Solidworks simulations is key to overcoming these hurdles and achieving optimal results in FEA assignments.
Conclusion
In conclusion, the exploration of advanced meshing and element selection has provided valuable insights into optimizing Finite Element Analysis (FEA) accuracy. One of the key takeaways is the critical role played by mesh density in achieving precision without sacrificing computational efficiency. Striking the right balance in mesh density is an art that engineers must master to ensure accurate FEA results.
The understanding of various meshing techniques, including structured and unstructured meshes, adds another layer of complexity to the process. Learning when and how to employ these techniques can significantly impact the outcome of FEA assignments. A well-informed choice between 2D and 3D meshing is crucial, and the transition between them demands careful consideration to maintain accuracy in simulations.
Advanced meshing techniques, such as adaptive mesh refinement, offer a dynamic approach to adjusting mesh density based on local solution requirements. This not only enhances accuracy but also optimizes computational resources by focusing on areas of interest. Transitioning into 3D meshing introduces a new dimension to simulations, and understanding the intricacies of this shift is imperative for engineers seeking precise FEA outcomes.
Equally important is the selection of the right element type, which can significantly influence the accuracy of FEA assignments. By delving into the nuances of element types and understanding their applicability, engineers can make informed decisions that align with the characteristics of the problem at hand. Element quality and shape functions further contribute to the reliability of FEA results, emphasizing the need for meticulous evaluation and enhancement strategies.
Optimizing for assignment accuracy involves conducting mesh sensitivity analyses, providing a clear understanding of how mesh density impacts FEA outcomes. Fine-tuning element selection based on problem-specific characteristics is another crucial step toward achieving precision in simulations. These strategies, when implemented thoughtfully, contribute to the successful resolution of complex engineering problems.
Real-world case studies underscore the practical application of advanced meshing and element selection techniques in solving intricate engineering challenges. These examples provide engineers with a tangible understanding of how to implement these strategies effectively, bridging the gap between theoretical knowledge and practical problem-solving.
Despite the benefits, challenges may arise during the meshing and element selection process. Identifying and overcoming these challenges is paramount for ensuring the accuracy and reliability of FEA assignments. Integrating advanced meshing and element selection techniques with Solidworks simulations further enhances the synergy between software capabilities and engineering expertise.
In essence, the journey through advanced meshing and element selection is a multifaceted exploration that empowers engineers to navigate the complexities of FEA with precision. The importance of these techniques cannot be overstated; they form the bedrock for successful engineering simulations, providing the foundation for innovation and problem-solving in the ever-evolving field of finite element analysis.