- Importance of Meshing in FEA
- Types of Meshing Techniques in SolidWorks
- Guidelines for Advanced Meshing
- Element Selection Strategies for FEA Precision
- Common Meshing Challenges and Solutions
- Case Studies on Optimizing Meshing for Accurate FEA
- Best Practices for Element Selection in SolidWorks
- Integrating Meshing and Element Selection in SolidWorks
- Future Trends in FEA Meshing and Element Selection
- Conclusion
In the dynamic landscape of engineering simulation, Finite Element Analysis (FEA) stands as a cornerstone, serving as a powerful and indispensable tool for engineers and designers alike. FEA transcends the boundaries of traditional analysis methods, providing a sophisticated means of understanding and predicting the complex behaviors exhibited by structures and components across diverse conditions. If you need assistance with your finite element analysis assignment, exploring the capabilities and applications of FEA can provide valuable insights and support to tackle your engineering simulation tasks effectively.
At its essence, FEA is a computational method that breaks down complex structures into smaller, manageable elements, enabling engineers to simulate and analyze their responses to various loads and environmental factors. This process allows for a comprehensive examination of structural integrity, stress distribution, and deformation, providing invaluable insights that are challenging to obtain through traditional analytical approaches.
The significance of FEA lies in its ability to bridge the gap between theoretical design and real-world performance. Engineers leverage FEA to assess the structural robustness of components, ensuring they meet safety standards and performance requirements. By subjecting virtual models to a spectrum of conditions – from static loads to dynamic vibrations – FEA enables the identification of potential weaknesses, guiding the refinement of designs before they manifest in physical prototypes.
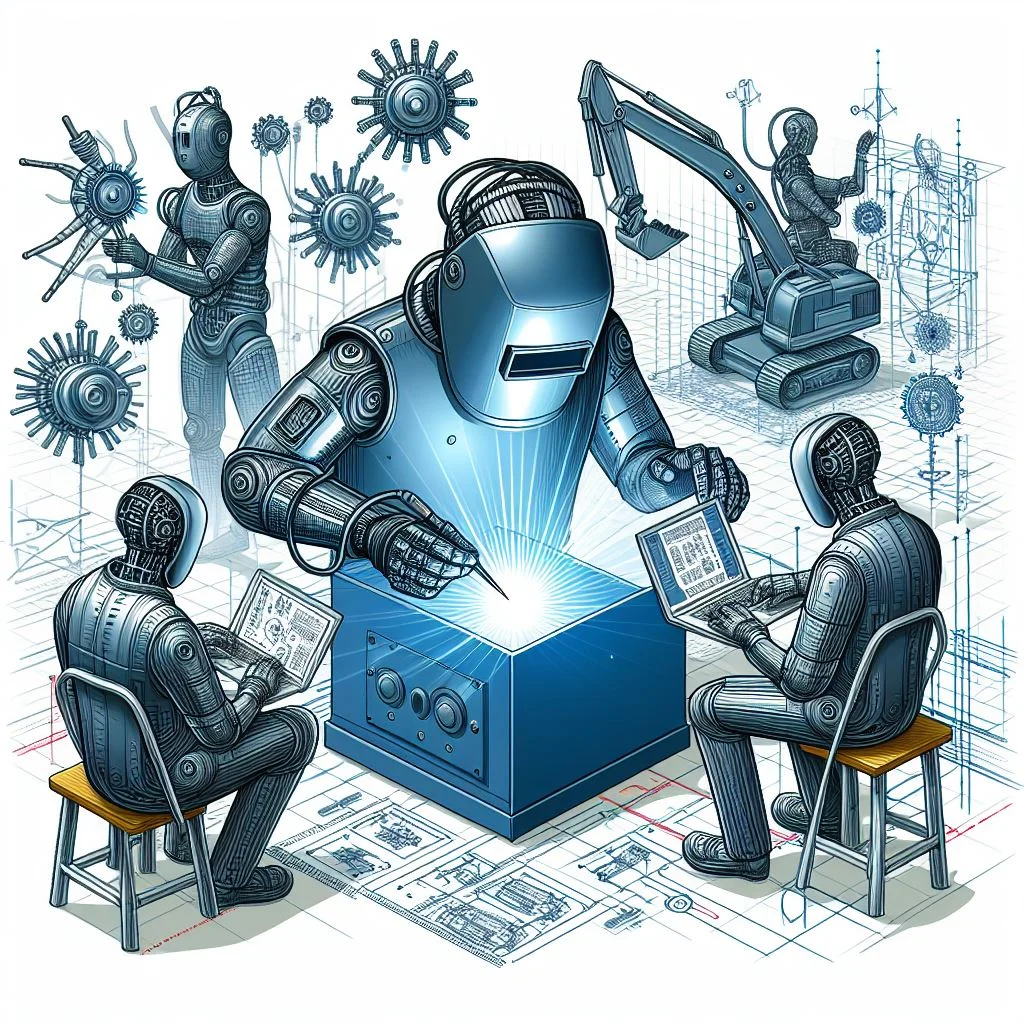
One of the key strengths of FEA is its adaptability across various engineering disciplines, including mechanical, civil, aerospace, and biomedical engineering. The versatility of FEA extends its application to a wide array of scenarios, ranging from the evaluation of automotive components' crashworthiness to the assessment of building structures under seismic forces. This versatility underscores the universality of FEA as a transformative technology that has reshaped the landscape of engineering analysis.
The predictive capabilities of FEA empower engineers to make informed decisions during the design phase, minimizing the need for costly trial-and-error approaches in the physical realm. As technology advances, FEA continues to evolve, incorporating sophisticated algorithms and computational methodologies that enhance its accuracy and efficiency. The integration of FEA into popular CAD software, such as SolidWorks, has democratized access to this powerful simulation technique, enabling engineers at various proficiency levels to harness its capabilities.
Furthermore, FEA serves as a bridge between theoretical knowledge acquired in academic settings and its practical application in professional engineering projects. This simulation method empowers students and practicing engineers to visualize the intricacies of structural behavior, fostering a deeper understanding of the principles governing materials and their responses to external forces.
In the context of SolidWorks assignments, an adept understanding of FEA becomes paramount. SolidWorks, with its user-friendly interface and robust simulation capabilities, offers a platform where engineers can seamlessly implement FEA to enhance their design processes. From validating product performance to optimizing structural components, SolidWorks becomes a playground for FEA enthusiasts seeking to push the boundaries of simulation accuracy.
Importance of Meshing in FEA
Efficient meshing serves as the cornerstone of accurate Finite Element Analysis (FEA), acting as the silent architect that shapes the reliability and precision of simulation outcomes. Meshing, in essence, is the process of discretizing complex geometries into smaller, manageable elements. As we navigate the intricacies of FEA, it becomes clear that the significance of meshing extends beyond a procedural step – it profoundly influences the very essence of engineering simulations and shapes the trajectory of assignment outcomes.
The impact of meshing on simulation results is profound, as the quality of the mesh directly determines the accuracy of the analysis. A well-structured mesh, tailored to the intricacies of the simulated model, allows for the representation of intricate details and subtle nuances in structural behavior. Conversely, a poorly generated mesh introduces errors and inaccuracies that can compromise the reliability of the entire analysis. The size, shape, and arrangement of mesh elements intricately define how forces and deformations are distributed throughout the model, making efficient meshing a critical factor in obtaining meaningful and trustworthy results.
Moreover, the influence of meshing extends beyond the digital realm into the practical applications of engineering assignments. An accurately meshed model not only ensures the precision of simulation outcomes but also facilitates a more profound understanding of how a structure or component behaves under various conditions. This comprehension is invaluable in real-world scenarios, guiding engineers in the design, optimization, and validation processes.
Types of Meshing Techniques in SolidWorks
Diving deeper into the intricacies of meshing techniques in SolidWorks opens up a world of possibilities for engineers seeking optimal simulation outcomes. Structured meshes, characterized by a regular arrangement of elements, offer simplicity and ease of control. Particularly advantageous for simple geometries, structured meshes excel in capturing straightforward simulations with uniform elements. Their predictability and efficiency make them a popular choice in scenarios where computational resources are a critical consideration.
On the flip side, unstructured meshes introduce a higher degree of flexibility, adapting seamlessly to complex geometries. These meshes consist of irregularly shaped elements, allowing for a more accurate representation of intricate structures. Unstructured meshes shine in simulations involving irregular geometries, providing a finer level of detail and precision that structured meshes may struggle to achieve. This versatility comes at the cost of increased computational demands, but the trade-off often proves worthwhile when accuracy is paramount.
The sweet spot between structured and unstructured meshes is found in hybrid meshes, which combine elements of both approaches. By strategically employing structured meshes in regions of geometric simplicity and unstructured meshes in complex areas, engineers can strike a balance between computational efficiency and accuracy. This hybrid approach leverages the strengths of each technique, offering a tailored solution that optimizes simulation performance across a spectrum of scenarios.
In SolidWorks simulations, understanding the nuances of these meshing techniques empowers engineers to make informed decisions based on the specific requirements of their projects. Whether aiming for computational efficiency in straightforward analyses or pushing the boundaries of accuracy in intricate simulations, the selection of the appropriate meshing technique becomes a pivotal factor in achieving FEA excellence.
Guidelines for Advanced Meshing
To achieve advanced meshing in Finite Element Analysis (FEA), practitioners must adhere to a set of key guidelines that go beyond the basics. Firstly, mesh refinement strategies play a pivotal role in enhancing simulation accuracy. By strategically refining the mesh in regions with high stress gradients or complex geometry, engineers can capture intricate details that might be missed with a coarse mesh. This targeted approach ensures that the simulation results accurately represent the intricacies of the physical system under analysis.
Secondly, considerations for element aspect ratio are crucial in achieving a well-behaved mesh. Element aspect ratio refers to the ratio of the longest side of an element to the shortest side. Maintaining a balanced aspect ratio helps prevent distortion in the mesh, ensuring that elements are not excessively elongated or compressed. This, in turn, contributes to improved simulation accuracy and stability.
Optimization techniques form the third pillar of advanced meshing. Employing optimization algorithms allows for the automatic adjustment of mesh parameters to achieve an optimal balance between accuracy and computational efficiency. This dynamic approach ensures that computational resources are utilized judiciously, focusing on refining areas of significance while maintaining an efficient overall mesh.
Element Selection Strategies for FEA Precision
In the realm of Finite Element Analysis (FEA), the significance of element selection cannot be overstated. It is a nuanced process that involves choosing the right type of elements to represent the geometry and material properties of the structure accurately. The role of element types in FEA is akin to selecting the appropriate building blocks for constructing a complex puzzle – each piece contributing to the overall accuracy and reliability of the simulation.
Element selection involves a careful consideration of the simulation's unique requirements, encompassing factors such as geometric intricacies, loading conditions, and material behaviors. Different types of elements, ranging from simple one-dimensional elements to more complex three-dimensional elements, offer distinct advantages in capturing specific aspects of structural behavior. For instance, in scenarios where bending or deformation is a critical parameter, selecting beam or shell elements might be more appropriate than simpler alternatives.
Best practices for element selection extend beyond the understanding of the structural components alone. They encompass a holistic approach that takes into account the physics of the problem at hand. Are there areas of high stress concentration? Does the structure exhibit nonlinear behavior under certain conditions? These considerations guide the engineer in choosing elements that align precisely with the simulation scenario, ensuring that the FEA model is not only accurate but also reflective of real-world conditions.
Furthermore, the choice of elements directly influences the computational efficiency of the simulation. Striking the right balance between model accuracy and computational cost is an art, and seasoned engineers understand the intricate dance between refining the model and optimizing computational resources. By navigating this delicate equilibrium, practitioners can craft simulations that not only meet the precision standards demanded by their assignments but also do so in a resource-efficient manner.
Common Meshing Challenges and Solutions
Addressing common meshing challenges is crucial for ensuring the robustness of Finite Element Analysis (FEA) simulations. One prevalent issue faced by engineers is mesh distortion, where irregularities in the mesh elements can compromise the accuracy of the simulation. This distortion often occurs when dealing with complex geometries or regions with significant variations in structural features. To overcome mesh distortion, engineers can employ adaptive mesh refinement techniques, focusing on areas where distortion is most pronounced. By selectively refining the mesh in these problematic zones, practitioners can maintain accuracy while efficiently utilizing computational resources.
Another challenge in meshing lies in maintaining high-quality elements throughout the entire simulation model. Element quality issues can arise due to poor aspect ratios or distorted shapes, leading to inaccurate results. Utilizing mesh optimization tools, engineers can enhance the quality of elements by adjusting their shapes and sizes to align with simulation requirements. This proactive approach not only mitigates potential inaccuracies but also contributes to a more stable and efficient FEA process.
By understanding and addressing these common challenges, engineers can fortify the foundation of their FEA simulations, ensuring that the mesh accurately represents the physical behavior of the structure under analysis. Through a judicious combination of adaptive refinement and mesh optimization, practitioners can navigate the intricacies of meshing challenges, paving the way for more reliable and precise SolidWorks assignments.
Case Studies on Optimizing Meshing for Accurate FEA
Delving deeper into the realm of real-world applications, case studies provide compelling evidence of how advanced meshing techniques profoundly influence the accuracy of Finite Element Analysis (FEA) results within SolidWorks assignments. These practical examples serve as illuminating beacons, guiding engineers and students alike through the intricacies of implementing advanced meshing strategies for optimal outcomes.
One noteworthy case study involves a structural analysis scenario where a complex assembly of components underwent a simulation to assess its response to varying loads. By employing advanced meshing methodologies, the simulation not only accurately predicted stress distribution but also provided insights into potential failure points. This level of precision allowed engineers to make informed design modifications, ultimately enhancing the structural integrity of the assembly.
In another case study focusing on fluid dynamics within SolidWorks, advanced meshing played a pivotal role in simulating the behavior of fluid flows around a streamlined structure. The results not only mirrored the expected aerodynamic performance but also provided nuanced details, such as turbulent zones and pressure differentials. These insights proved instrumental in refining the design for optimal efficiency.
These case studies underscore the practical significance of mastering advanced meshing techniques, transcending theoretical knowledge to tangible, real-world impact. Engineers armed with a profound understanding of meshing intricacies in SolidWorks can confidently navigate diverse simulation scenarios, ensuring that their FEA results align with actual physical behaviors. The integration of these case studies into the broader narrative reinforces the transformative potential of advanced meshing, urging practitioners to embrace these techniques as indispensable tools in their engineering arsenal.
Best Practices for Element Selection in SolidWorks
In the intricate landscape of SolidWorks simulations, mastering the art of element selection is a multifaceted endeavor that demands a nuanced understanding of various factors. Best practices for element selection extend beyond the mere application of finite elements; they require a holistic approach that takes into account the specific characteristics of the materials, the nature of loading conditions, and the geometric complexities inherent in the model.
When delving into SolidWorks simulations, the choice of material properties is foundational to the accuracy of the analysis. Different materials exhibit distinct mechanical behaviors under stress and strain, and selecting appropriate elements tailored to these material properties is crucial. Whether dealing with ductile or brittle materials, understanding their response to loading conditions informs the selection of elements that can capture the intricacies of their behavior with precision.
Loading conditions, another critical consideration, vary across different engineering scenarios. Whether subjected to static loads, dynamic forces, or thermal effects, the chosen elements must align with the anticipated conditions. Robust simulations necessitate the use of elements that can accurately depict the structural response to diverse loading scenarios, ensuring that the model's behavior mirrors real-world dynamics.
Geometric complexities further complicate the element selection process. SolidWorks, with its versatile capabilities, often accommodates complex geometries in engineering designs. The challenge lies in selecting elements that can faithfully represent the intricacies of these geometries. Balancing element size and model complexity is an art, requiring engineers to strike a delicate equilibrium that ensures both computational efficiency and result accuracy.
Integrating Meshing and Element Selection in SolidWorks
Understanding the synergy between meshing and element selection is fundamental to harnessing the full potential of SolidWorks for Finite Element Analysis (FEA). These two processes, often treated as distinct steps, are intricately connected and their integration is key to achieving highly accurate and reliable simulations.
In SolidWorks, meshing defines the discretization of the model into elements, while element selection involves choosing the appropriate type of elements for analysis. The seamless integration of these two steps is akin to aligning the pieces of a puzzle – each element chosen should complement the meshing strategy to ensure a cohesive and accurate representation of the physical system under study.
When meshing and element selection work in harmony, the simulation becomes a more accurate reflection of the real-world scenario. Mesh refinement, a key aspect of advanced meshing, can be strategically applied based on the demands of specific elements selected. For example, regions of high stress or complex geometry may benefit from a finer mesh, enhancing the simulation's fidelity in those critical areas.
Furthermore, the integration allows for a holistic consideration of simulation parameters. By carefully selecting elements compatible with the material properties, loading conditions, and geometric intricacies, engineers can refine their simulations to capture nuanced behaviors and responses. The synergy between meshing and element selection is not a mere technicality but a strategic approach that enhances the overall reliability and precision of FEA in SolidWorks.
Future Trends in FEA Meshing and Element Selection
As we peer into the future of Finite Element Analysis (FEA), the landscape is marked by continual innovation and the relentless pursuit of precision. Emerging trends in FEA meshing and element selection promise to reshape the way engineers approach simulations, offering novel solutions to age-old challenges.
In the realm of meshing algorithms, the rise of artificial intelligence and machine learning has begun to make significant waves. These cutting-edge technologies are being harnessed to develop adaptive meshing strategies that dynamically adjust mesh resolution based on the evolving simulation conditions. This adaptability not only enhances the efficiency of the simulation process but also ensures that computational resources are allocated judiciously, striking a delicate balance between accuracy and computational cost.
Furthermore, the integration of topology optimization techniques into meshing algorithms is gaining traction. By leveraging advanced optimization algorithms, engineers can automatically generate optimized mesh structures that minimize material usage while meeting specified performance criteria. This not only streamlines the design process but also paves the way for more sustainable and resource-efficient engineering solutions.
In the realm of element selection methodologies, the focus is shifting towards automated approaches driven by artificial intelligence. Machine learning algorithms are being trained on vast datasets of simulation results, enabling them to discern optimal element types for specific scenarios. This data-driven approach holds the promise of expediting the simulation setup process, allowing engineers to rapidly configure simulations with a high degree of confidence in the chosen elements' appropriateness.
As these trends unfold, their potential impact on assignments is profound. Engineers can anticipate faster and more intelligent simulation setups, reducing the time spent on manual meshing and element selection tasks. This not only accelerates the overall simulation process but also empowers engineers to explore a broader design space, fostering innovation and pushing the boundaries of what is achievable in the realm of FEA.
Conclusion
In the dynamic realm of engineering simulation, achieving unparalleled accuracy in Finite Element Analysis (FEA) is not merely a goal; it is a necessity. As we conclude our exploration of advanced meshing and element selection strategies in SolidWorks assignments, it becomes evident that these techniques are indispensable for optimizing FEA accuracy and, consequently, elevating the quality of engineering simulations.
The journey through this blog has been a comprehensive expedition into the intricacies of FEA, starting with an understanding of its foundational concepts. Finite Element Analysis, as a powerful tool for predicting structural behavior, relies heavily on the accuracy of the meshing process. Efficient meshing serves as the bedrock upon which precise simulations are built. From structured to unstructured and hybrid meshes, each technique has its merits, and their selection depends on the specific requirements of the simulation scenario.
Guidelines for advanced meshing have been discussed in detail, emphasizing the importance of mesh refinement, element aspect ratio considerations, and optimization strategies. These guidelines serve as a roadmap for engineers and students seeking to enhance the quality of their FEA simulations. By adhering to these principles, practitioners can overcome common challenges such as mesh distortion and element quality issues, ensuring a robust foundation for accurate analysis.
Element selection, the often-overlooked facet of FEA, was highlighted as a critical factor in simulation precision. The blog provided insights into selecting the appropriate element types based on material properties, loading conditions, and geometric complexities. By aligning the chosen elements with the specific requirements of the simulation, engineers can significantly improve the reliability and accuracy of their FEA results.
Real-world case studies showcased the practical application of advanced meshing and element selection in SolidWorks assignments. These examples underscored the transformative impact these techniques can have on the accuracy of simulation results. As engineers navigate through complex projects, the ability to address challenges and implement effective solutions becomes paramount. This blog has equipped readers with the knowledge and tools to tackle common meshing challenges, ensuring the integrity of their simulations.
The integration of meshing and element selection emerged as a theme central to achieving optimal FEA precision. Recognizing the synergy between these two components allows engineers to design simulations that mirror real-world scenarios more accurately. By seamlessly integrating meshing and element selection in SolidWorks, practitioners can unlock new levels of reliability in their analyses.
Looking ahead, the blog touched upon future trends in FEA meshing and element selection. As technology continues to evolve, so too will the tools and methodologies employed in FEA. Emerging trends in meshing algorithms and element selection methodologies hint at a future where simulations become even more sophisticated and accurate.