Tip of the day
News
Key Topics
- Understanding Finite Element Analysis (FEA)
- Why Use FEA?
- The Basics of SolidWorks
- SolidWorks Simulation
- Performing Finite Element Analysis in SolidWorks
- Material Definition
- Boundary Conditions
- Meshing
- Setting Up the Analysis
- Running the Analysis
- Interpreting FEA Results
- Deformation Analysis
- Safety Factor
- Tips for SolidWorks Assignments
- Document Assiduously
- Verify Results
- Seek Guidance and Collaborate
- Conclusion
Finite Element Analysis (FEA) is a sophisticated and indispensable tool in the realm of engineering and design. It empowers engineers and designers to simulate the behavior of intricate structures and components under diverse conditions without the necessity for physical prototypes, thereby saving significant time and resources in the product development process. FEA is not just a convenience but a necessity in modern engineering, where complex designs and stringent performance requirements are the norm, making it essential to complete your Finite Element Analysis assignment.
When it comes to analyzing 3D parts, SolidWorks stands as a widely embraced software equipped with robust FEA capabilities, making it the go-to choice for many professionals and students alike. SolidWorks has earned its reputation as a versatile and user-friendly 3D CAD software, and its integration of FEA capabilities seamlessly into the design workflow sets it apart as a comprehensive solution for engineers and designers.
In this comprehensive guide, we will delve deeply into the fundamentals of Finite Element Analysis and explore how it can assist students in effectively solving SolidWorks assignments. Through a detailed examination of the principles, methodologies, and practical applications of FEA, this guide aims to provide students with a thorough insight into the captivating world of 3D modeling and analysis, equipping them with the knowledge and skills needed to excel in their academic pursuits and future careers in engineering and design.
Understanding Finite Element Analysis (FEA)
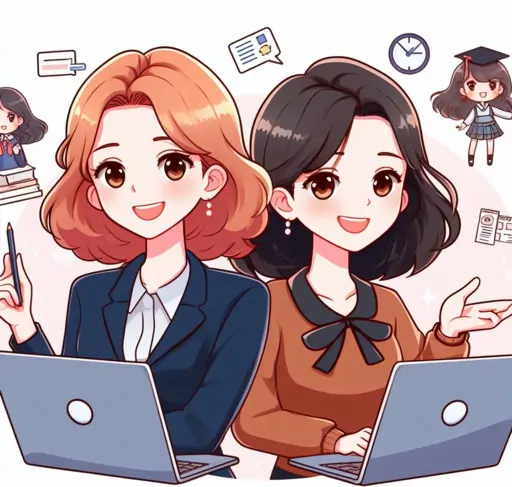
Finite Element Analysis (FEA) is an exceedingly sophisticated numerical simulation technique that assumes an indispensable role in engineering and design. It holds the power to accurately predict the intricate behaviors of complex structures and components by ingeniously dividing them into smaller, finite elements. These elements, resembling interconnected building blocks, are strategically positioned at nodes within the design, and meticulously formulated mathematical equations are rigorously applied to discern, with exceptional precision, the response of each individual element. This exhaustive computational approach amalgamates these intricate responses to offer engineers and designers an all-encompassing, highly detailed perspective of precisely how the entire structure will perform under meticulously defined and simulated conditions. These comprehensive insights provided by FEA are a cornerstone in ensuring the optimal performance, safety, and reliability of engineering designs, serving as an invaluable asset in the toolbox of modern engineers and designers.
Why Use FEA?
FEA is embraced within the engineering and design communities for a multitude of reasons, some of which are elucidated below:
- Cost-Effective Analysis:FEA significantly mitigates the need for constructing physical prototypes, thereby resulting in substantial cost savings during the product development phase.
- Handling Complex Geometries:It excels in handling intricate 3D geometries that often pose a formidable challenge for analysis using traditional methods.
- Optimization Capabilities:FEA serves as an optimization tool, offering insights into critical factors such as stress, deformation, and structural performance, which are pivotal for enhancing product designs.
- Enhanced Safety: By simulating real-world conditions and stressors, FEA ensures that products are engineered with the utmost safety and reliability in mind, reducing the risk of structural failures.
The Basics of SolidWorks
SolidWorks, a preeminent 3D Computer-Aided Design (CAD) software, stands as a preferred choice for engineers and designers worldwide. Its reputation as a go-to tool is bolstered by its intuitive user-friendly interface and unparalleled modeling capabilities. SolidWorks not only simplifies the often complex process of 3D design but also offers a versatile environment for crafting intricate 3D parts and assemblies. With its extensive feature set, from parametric modeling to dynamic simulation, SolidWorks has become an indispensable asset in the realm of 3D modeling and analysis, catering to the diverse needs of professionals across various industries.
SolidWorks Simulation
Incorporated seamlessly within SolidWorks, the simulation module empowers users with the ability to proficiently conduct Finite Element Analysis (FEA) on their intricate 3D models. This deep-rooted integration assures that students, while engaged in SolidWorks assignments, possess a formidable and indispensable tool that enables them to comprehensively simulate, scrutinize, and gain profound insights into the behavior of complex structures and components.
Performing Finite Element Analysis in SolidWorks
Before delving into FEA in SolidWorks, meticulous model preparation is paramount. This multifaceted process involves defining materials, assigning boundary conditions, and meshing the geometry, and is integral to obtaining accurate and insightful results. Let's break down these steps in detail, as a solid foundation in these aspects is key to ensuring the success of your Finite Element Analysis simulations and enhancing your understanding of how 3D parts behave under various conditions.
Material Definition
- Material Properties:SolidWorks provides engineers and designers with a remarkable degree of flexibility by offering a comprehensive library replete with a wide array of predefined material options. Moreover, it empowers users to delve even deeper into customization, enabling the creation of bespoke material properties meticulously tailored to the exacting requirements of specific engineering applications.
- Applying Materials:The process of assigning chosen material properties to the corresponding components of the 3D model assumes paramount importance. This step is the linchpin for accurately replicating the nuanced physical attributes and behaviors of the selected materials within the digital realm, ensuring that the simulation faithfully mirrors real-world conditions and responses.
Boundary Conditions
- Fixtures:In the realm of Finite Element Analysis (FEA), fixtures or boundary conditions play a pivotal role in defining the structural constraints. They specify the precise locations where the model is either firmly constrained or fixed, replicating real-world constraints and restrictions. These constraints can encompass immobilizing certain faces or edges, mimicking the exact conditions that the physical structure would face in practical applications.
- Loads:The application of loads is a critical aspect of FEA, as it mirrors real-world operating conditions. These loads include external forces, pressures, or any other pertinent factors affecting the model's behavior. Achieving meaningful results in FEA hinges on the precise definition of these loads, ensuring that the simulation faithfully replicates the intricacies of the actual operating environment, and thereby providing accurate insights into structural performance.
Meshing
Meshing, a fundamental and intricately critical step in Finite Element Analysis (FEA), entails the meticulous process of discretizing the 3D model into finite elements. SolidWorks, with its comprehensive toolkit, offers users a versatile spectrum of choices encompassing automatic and manual meshing. This multifaceted flexibility empowers users to finely tune and calibrate the mesh density, thereby ensuring not only the utmost precision in analysis but also optimal computational efficiency throughout the simulation process, a pivotal aspect in achieving accurate and expedient results.
Setting Up the Analysis
Following model preparation, specifying the type of analysis to be performed is paramount. SolidWorks offers an array of analysis types, including:
- Static Analysis:Static analysis evaluates the response of a structure under steady-state loads, providing insights into stress distribution and deformation under fixed conditions.
- Dynamic Analysis:Dynamic analysis investigates the behavior of a structure under time-varying loads, including vibrations and transient forces.
- Thermal Analysis:Thermal analysis assesses temperature distribution within a part or assembly, enabling designers to optimize heat dissipation and thermal performance.
- Modal Analysis:Modal analysis uncovers the natural frequencies and mode shapes of a structure, which is crucial for understanding its dynamic behavior.
Running the Analysis
With the analysis setup complete, SolidWorks proceeds to solve the complex mathematical equations governing each finite element within the model. These intricate calculations unveil critical insights into stress distribution, deformation, and safety factors, thereby offering a comprehensive understanding of the structural behavior of the 3D part or assembly under meticulous examination.
Interpreting FEA Results
Stress analysis stands as a cornerstone of FEA, yielding critical insights into the structural integrity of a design. SolidWorks provides detailed stress results, including:
- Von Mises Stress: This scalar value represents the equivalent stress in the material, offering a key metric for assessing yielding and failure.
- Normal Stress:Normal stress is the stress acting perpendicular to the face, crucial for understanding load-bearing capabilities.
- Shear Stress:Shear stress arises from forces parallel to the face and is pivotal in evaluating the material's response to shearing forces.
Deformation Analysis
Deformation analysis provides critical insights into the extent of displacement and distortion experienced by a 3D part or assembly when subjected to applied loads. This analysis is instrumental in pinpointing regions where excessive deformation may compromise the functionality, structural integrity, or safety of the design, thereby enabling engineers to implement meticulous design optimizations and refinements for enhanced performance and reliability.
Safety Factor
The safety factor is a paramount parameter in FEA, serving as a critical indicator of design reliability and structural integrity. It quantifies the margin of safety by meticulously comparing the maximum allowable stress, which the material or structure can withstand, to the actual stress experienced during simulation. A safety factor greater than 1 provides an unequivocal assurance that the design is not only safe but possesses a significant buffer against failure, thus instilling confidence in its ability to endure and excel under the applied loads. This crucial metric plays a pivotal role in ensuring the robustness and longevity of engineered components and structures.
Tips for SolidWorks Assignments
When embarking on SolidWorks assignments involving Finite Element Analysis (FEA), it is prudent to commence with straightforward geometries and progressively advance to more intricate models. This stepwise approach is essential for developing a robust understanding of SolidWorks' capabilities and the nuances of FEA, as it allows students to gradually grasp the intricacies of material properties, boundary conditions, and meshing techniques. Furthermore, starting with simpler models provides a solid foundation for mastering the software's tools and functions, ensuring that students are well-prepared to tackle complex, real-world engineering problems as they progress in their FEA journey. This methodical approach not only builds confidence but also enhances problem-solving skills, making it an indispensable part of the learning process.
Document Assiduously
Thorough documentation is a non-negotiable and fundamental aspect of conducting Finite Element Analysis (FEA). It's imperative to meticulously record every facet of your analysis, which includes documenting the specific settings employed, the intricacies of boundary conditions applied, and the underlying assumptions made throughout the simulation process. This comprehensive and organized documentation serves a dual purpose – not only does it aid in keeping an accurate and transparent record of your work, but it also significantly enhances your ability to present your results and methodologies in a coherent and compelling manner, which is essential in engineering and design projects.
Verify Results
Validation and verification are pivotal and non-negotiable aspects of Finite Element Analysis (FEA). It is imperative to rigorously compare your simulation results with theoretical calculations or hand calculations where feasible, as this meticulous validation process serves as the linchpin for establishing the unwavering accuracy, trustworthiness, and robustness of your FEA model and the consequential results it generates. By diligently validating your FEA analyses, you not only enhance the credibility of your work but also ensure that your engineering solutions are firmly grounded in scientific and engineering principles, setting a solid foundation for informed decision-making in design and analysis.
Seek Guidance and Collaborate
In the realm of engineering and design, collaboration is not just beneficial but absolutely essential. Do not hesitate to actively seek guidance and wisdom from your experienced instructors or foster collaborative efforts with your fellow peers when confronted with complex challenges. It's worth noting that SolidWorks boasts an exceptionally vibrant and supportive user community. Furthermore, an abundance of online resources, ranging from forums to tutorials, is readily accessible to provide valuable insights and solutions, enriching your learning and problem-solving journey in the ever-evolving world of engineering and design.
Conclusion
Finite Element Analysis, when harnessed within SolidWorks, emerges as an indispensable skill for engineering students. It empowers them to dissect, analyze, and optimize 3D parts and assemblies, ultimately leading to the creation of superior designs. By grasping the essentials of FEA, SolidWorks, and the art of interpreting simulation results, students can excel in their SolidWorks assignments and gain a distinct competitive advantage as they embark on their future careers in engineering and design. Remember, the path to mastery involves practice, persistence, and an unwavering commitment to exploring and harnessing the full potential of SolidWorks' FEA capabilities. So, dive in, explore, and let your journey into the fascinating world of 3D modeling and analysis begin.
You Might Also Like to Read
Desgning Complex SolidWorks Assignments with a Step-by-Step Approach
SolidWorks is an essential tool for engineers, designers, and students engaged in CAD (Computer-Aided Design) projects. Whether you are new to SolidWorks or an experienced user, solving complex assignments can be a challenging task. Many students often find themselves searching for guidance, ...
How to Design SolidWorks Assignments Using Finite Element Analysis (FEA)
Finite Element Analysis (FEA) plays a crucial role in engineering simulations, enabling engineers to predict how components will react under various physical conditions. Whether you're tackling a complex simulation or struggling with meshing techniques, understanding FEA is essential for accu...
Optimizing Your SolidWorks Workflow for Efficient CAD Assignments
SolidWorks is a powerful and widely used 3D CAD modeling tool, essential for engineering students and professionals in design, manufacturing, and product development. However, many students struggle with SolidWorks assignments, especially when working with features like revolve, sweep, hole w...
How to Design Perfect Collages with Scales and Rotations in Solid works Assignment
SolidWorks assignments, particularly those requiring intricate designs like scaled and rotated collages, challenge students to showcase precision, creativity, and technical proficiency. These assignments push learners beyond basic modeling, urging them to apply critical thinking and embrace c...
Efficient Techniques for Completing SolidWorks Assignments
SolidWorks is a versatile and widely-used 3D CAD software that empowers engineers and designers to bring their ideas to life. From intricate designs to advanced simulations, the software offers unmatched capabilities. When faced with an assignment that involves diverse topics like lofts, swee...
SolidWorks Tools You Need in 2025 to Ace Your Assignments
SolidWorks is a powerful 3D CAD software, and mastering it can open doors to exciting opportunities in design, engineering, and manufacturing. However, tackling SolidWorks assignments can be challenging, especially when dealing with complex designs, tight deadlines, or advanced features. If y...
Analyzing Structural Stability in College Assignments Through SolidWorks
When tackling college assignments that require structural stability analysis, SolidWorks is a powerful tool. It allows students to validate their designs, ensuring that they meet the required safety and performance standards. This blog provides a step-by-step guide on using SolidWorks to valid...
How to Optimize SolidWorks Sheet Metal Assignments Using Forming Tools
SolidWorks is a powerful CAD tool widely used for designing and modeling mechanical parts and assemblies. One of its most practical features for sheet metal design is the Forming Tools module, which simplifies the creation of intricate patterns and shapes like louvers, ribs, and dimples. Thes...
How to Tackle PCB Design Assignments Effectively with SolidWorks Electrical
In today's fast-paced technological world, Printed Circuit Board (PCB) design plays a vital role in electrical engineering. For students pursuing engineering and design courses, completing PCB design assignments can be challenging due to the intricacies involved in schematics, component placem...
Must-Have Plugins & Add-Ons to Ace Your College Assignments
SolidWorks, a powerful 3D design and engineering software, is a cornerstone for many college students pursuing engineering and design-related courses. Despite its extensive capabilities, working on SolidWorks assignments can be daunting due to the steep learning curve and the sheer volume of ...
Designing Boat Components in SolidWorks for Marine Engineering
Marine engineering is the field dedicated to the design, construction, and maintenance of ships, boats, and other marine vessels. In this discipline, assignments often focus on practical tasks like designing and optimizing boat components. One of the most valuable tools for marine engineers is So...
Part Configurations, Automatic Updates, and Collaborative CAD Workflows
When it comes to modern CAD design, flexibility and efficiency are paramount. Whether you’re designing intricate assemblies or simple parts, the ability to create multiple configurations, update models automatically, and work seamlessly with others is crucial. SOLIDWORKS offers a robust set of ...
An In-depth Look into What Your Professor Expects from You
For the creation of intricate 3D models and engineering drawings, Solidworks is a potent software tool that is frequently used in the engineering and design fields. You may have worked on Solidworks drawing assignments as a student, where you had to demonstrate your proficiency with the program. Thi...
6 Steps to Prioritize Multiple SolidWorks Assignments
Students studying engineering and design frequently use SolidWorks, a potent computer-aided design (CAD) program. However, SolidWorks also brings a tonne of projects and assignments that can be overwhelming for students. Prioritization and time management skills are essential for managing multipl...
Tips for Generating CNC Programs from SolidWorks Designs
Computer Numerical Control (CNC) technology has revolutionized manufacturing processes by automating the production of intricate and precise components, and it can also be essential when you need to complete your SolidWorks assignment. One crucial step in the CNC workflow is generating a...
Benefit of SolidWork : Architectural Design and Construction
In the ever-evolving field of architecture and construction, technology has become an indispensable tool for architects, engineers, and builders. Among the myriad of software applications available, SolidWorks stands out as a powerful and versatile solution with a wide range of applications, ev...
How to Overcome Common Challenges Faced by SolidWorks Users
SolidWorks, a powerful computer-aided design (CAD) software, has been widely adopted by engineers, designers, and manufacturers across the globe. Its user-friendly interface, comprehensive tools, and versatile capabilities make it a go-to solution for creating 3D models, simulations, and engine...
Simulating Real-World Behavior for Design Validation
In the world of product design and engineering, ensuring the reliability and performance of a new design is crucial before it goes into production, and it can also be crucial when you need to complete your simulation assignment. The cost of fixing design flaws after production can be astronomic...
Mastering SolidWorks: Essential Tips and Tricks for Efficient Modeling
In the world of 3D modeling and design, SolidWorks stands as a cornerstone for professionals and enthusiasts alike. Its robust features and user-friendly interface make it a go-to choice for engineers, designers, and manufacturers looking to bring their ideas to life. To truly excel in SolidWor...
SolidWorks for Industrial Design: Enhancing Aesthetics and Ergonomics
In the realm of product design, aesthetics, and ergonomics play a pivotal role in shaping not only the visual appeal but also the usability and functionality of a product. If you're aiming to complete your SolidWorks assignment, this delicate balance between form and function can be achieved th...