- Understanding the Workflow
- Design Creation
- CAM Software Integration
- Post-Processing
- Machine Setup
- Tips for Generating CNC Programs from SolidWorks Designs
- Design for Manufacturability
- Clear Design Hierarchy
- Dimensional Accuracy
- Tolerances and Surface Finish
- Accurate Material Information
- Careful CAM Software Selection
- Toolpath Simulation
- Optimize Toolpaths
- Post-Processor Customization
- Embrace Regular Updates
- Best Practices for Seamless CNC Programming
- Collaboration
- Documentation
- Training and Skill Development
- Quality Control
- Continuous Improvement
- Conclusion
Computer Numerical Control (CNC) technology has revolutionized manufacturing processes by automating the production of intricate and precise components, and it can also be essential when you need to complete your SolidWorks assignment. One crucial step in the CNC workflow is generating accurate CNC programs from design files. SolidWorks, a popular computer-aided design (CAD) software, is widely used to create complex 3D designs that serve as the foundation for CNC machining. In this blog, we will delve into the tips and best practices for generating CNC programs from SolidWorks designs, streamlining the manufacturing process, and ensuring high-quality results
Understanding the Workflow
Modern manufacturing processes have been significantly streamlined and optimized through the integration of Computer Numerical Control (CNC) technology. This technology allows for the precise and automated production of intricate components. However, the journey from a conceptual design to a finished CNC-machined part involves a multi-step process that requires careful coordination and technical expertise. Let's delve deeper into the workflow of transforming a SolidWorks design into a functional CNC program.
Design Creation
The initial step in this workflow is the creation of a detailed 3D model using SolidWorks. Engineers and designers leverage this powerful Computer-Aided Design (CAD) software to define the geometry, dimensions, tolerances, and other critical aspects of the part they intend to manufacture. The design phase is where the foundation of the entire manufacturing process is laid. Engineers need to consider factors such as material properties, structural integrity, and design for manufacturability during this stage.
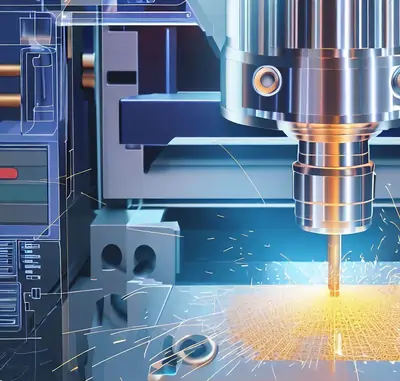
CAM Software Integration
Once the design is complete, the next phase involves the integration of Computer-Aided Manufacturing (CAM) software. CAM software serves as the bridge between the digital design and the physical manufacturing process. It interprets the intricate details of the 3D model created in SolidWorks and translates them into machine instructions. This includes generating toolpaths, specifying cutting strategies, determining tool selection, setting feeds and speeds, and optimizing the machining process for efficiency and accuracy.
The CAM software allows engineers to make critical decisions that impact the final part's quality and manufacturability. Different machining strategies, such as 3-axis or 5-axis milling, turning, or drilling, are selected based on the design's complexity and material properties.
Post-Processing
After the CAM software generates toolpaths and cutting strategies, the output is not yet ready for immediate use by the CNC machine. This is where post-processing comes into play. The generated program often needs to be translated into a machine-specific format, most commonly represented in G-code—a standardized language used to communicate with CNC machines. The post-processing step involves adapting the CAM-generated program to match the syntax and behavior of the target CNC machine's controller.
Additionally, post-processing may include fine-tuning parameters to optimize the program for a specific machine, considering factors like tool change sequences, coolant application, and safety protocols. This ensures that the machine operates smoothly and produces the desired results.
Machine Setup
With the CNC program now in the appropriate format, the next phase involves setting up the CNC machine itself. This step is crucial to ensuring the accuracy and quality of the manufactured parts. Machinists load the necessary tools into the machine's tool changer, secure the workpiece to the machine bed or fixture, and calibrate the machine's origin point based on the design's reference points.
During machine setup, machinists also fine-tune parameters such as tool offsets, workpiece zero coordinates, and toolpath verification. These adjustments are essential for achieving the desired precision and minimizing the risk of errors during machining.
Tips for Generating CNC Programs from SolidWorks Designs
Turning intricate SolidWorks designs into precise CNC programs is a process that demands a blend of design ingenuity and manufacturing acumen. To ensure a seamless transition from digital designs to tangible components, it's crucial to follow a set of proven tips and best practices. Let's delve deeper into these essential strategies for generating impeccable CNC programs.
Design for Manufacturability
Creating a CNC program is inherently easier when the design is optimized for manufacturing. As you craft your SolidWorks design, consider factors such as material selection, tool accessibility, and complexity. Opt for materials that are easily machinable and align with the part's functional requirements. Complex geometries and hard-to-reach features can increase machining time and raise the risk of errors. Strive for a design that marries functionality with manufacturability.
Clear Design Hierarchy
Organizing your SolidWorks designs with a clear hierarchy pays dividends during CNC programming. Utilize layers, assemblies, and components effectively to structure your design logically. A well-organized design streamlines the CNC programming process, making it easier to select specific elements for toolpath generation. Furthermore, a clear hierarchy enhances collaboration between design and manufacturing teams, ensuring everyone is on the same page.
Dimensional Accuracy
Precision is paramount in CNC machining, and it all begins with the SolidWorks design. Ensure that your design accurately represents the intended dimensions of the final product. Even minor discrepancies can lead to significant issues during machining, resulting in parts that don't meet specifications. Regularly verify dimensions against design requirements to catch any discrepancies early in the process.
Tolerances and Surface Finish
Specify tolerances and surface finish requirements explicitly in your SolidWorks design. These details influence the toolpaths generated by CAM software and directly impact the quality of the final product. Clearly defined tolerances help machinists choose appropriate tools, feeds, speeds, and cutting strategies to achieve the desired precision. Likewise, surface finish requirements guide the selection of finishing toolpaths.
Accurate Material Information
Provide accurate material information in your SolidWorks design. CAM software relies on this data to make informed decisions about tool selection, cutting parameters, and machining strategies. Proper material selection ensures that the CNC program is tailored to the material's characteristics, enhancing efficiency and reducing the risk of errors.
Careful CAM Software Selection
Selecting the right CAM software is a pivotal decision. Opt for CAM software that seamlessly integrates with SolidWorks. This integration facilitates smooth data transfer, reducing the chances of errors during the transition from design to CNC program. A well-integrated CAM system can directly read SolidWorks files, preserving design intent and minimizing the need for manual adjustments.
Toolpath Simulation
Most CAM software offers toolpath simulation features, allowing you to visualize machining operations before generating the CNC program. This feature is invaluable for identifying potential collisions, interferences, or inefficient toolpaths. Simulation enables you to catch and rectify issues virtually, mitigating the risk of costly mistakes during actual machining.
Optimize Toolpaths
Experiment with different toolpaths and cutting strategies to identify the most efficient and accurate options. Optimization can lead to reduced machining time, improved surface finish, and enhanced overall productivity. CAM software often provides options for adaptive toolpaths, trochoidal milling, and high-efficiency machining strategies that maximize tool life and minimize cycle times.
Post-Processor Customization
Collaborate with your CAM software's post-processor to tailor the generated G-code to match your specific CNC machine's requirements. Customizing the G-code ensures compatibility between the generated program and the machine's controller. This step is crucial for avoiding syntax errors and ensuring smooth communication between the software and the machine.
Embrace Regular Updates
Stay current with the latest developments by keeping both your SolidWorks design software and CAM software up to date. Updates often include bug fixes, performance enhancements, and new features that can significantly enhance your CNC programming process. Regularly checking for updates demonstrates a commitment to continuous improvement and helps you leverage the latest tools and capabilities.
Best Practices for Seamless CNC Programming
In the realm of CNC programming, achieving seamlessness and precision is paramount to the production of high-quality components. To facilitate this, consider adopting these best practices that encompass collaboration, documentation, training, quality control, and continuous improvement.
Collaboration
Effective collaboration between design and manufacturing teams is the cornerstone of a successful CNC programming process. Here's why it matters:
- Design Intent Clarification: Regular communication ensures that the design intent is clearly understood by the manufacturing team. Any discrepancies or ambiguities can be addressed early in the process.
- Feedback Loop: Manufacturing teams can provide valuable insights into the practical aspects of machining. They may suggest design modifications that can make the machining process more efficient or cost-effective.
- Reducing Rework: Collaboration helps prevent costly and time-consuming rework that may occur if design and manufacturing teams are not aligned in their understanding of the project.
By fostering collaboration, you create an environment where the collective knowledge and expertise of both teams can be harnessed to produce superior CNC programs.
Documentation
Maintaining comprehensive documentation throughout the CNC programming process is crucial for several reasons:
- Design Revisions: Document design revisions as they occur. This ensures that the CNC program stays in sync with the latest design changes, preventing errors and discrepancies.
- Toolpath Strategies: Record the toolpath strategies chosen during CAM programming. This documentation helps in troubleshooting and replicating successful strategies for future projects.
- Parameter Settings: Keep detailed records of parameter settings used for toolpath generation. This ensures consistency and repeatability in CNC programming.
- Post-Processing Modifications: If any adjustments are made during post-processing to accommodate specific machine requirements, document these changes for reference and future use.
Comprehensive documentation serves as a reference point for troubleshooting, quality control, and knowledge transfer within the team.
Training and Skill Development
Investing in training programs for both CAD design and CAM programming is an investment in the proficiency of your team. Consider the following:
- CAD Design Skills: Skilled CAD designers are more likely to create designs that are inherently manufacturable. Training in CAD design principles ensures that designs are optimized for CNC machining.
- CAM Programming Proficiency: Well-trained CAM programmers can leverage the full capabilities of CAM software, resulting in efficient toolpaths and minimized errors. Ongoing training keeps your team updated on the latest software features and techniques.
- Cross-Training: Cross-training team members in both CAD and CAM can enhance collaboration and problem-solving within the team, as individuals gain a deeper understanding of the entire process.
Continual skill development ensures that your team remains competitive, adaptable, and capable of producing high-quality CNC programs.
Quality Control
Implementing a robust quality control process is essential for delivering components that meet or exceed specifications:
- First Article Inspection: Conduct a thorough inspection of the first few manufactured components. Compare them against design specifications to ensure dimensional accuracy, tolerances, and surface finish.
- Tool Wear Monitoring: Regularly monitor tool wear during machining operations. This proactive approach allows for timely tool changes, maintaining machining accuracy and quality.
- Feedback Loop: Establish a feedback loop between quality control personnel and CNC programmers. This ensures that any deviations from desired specifications are promptly addressed in the CNC program.
By prioritizing quality control, you can catch issues early in the process, reduce scrap and rework, and maintain the consistency of your CNC programs.
Continuous Improvement
Regularly assessing your CNC programming workflow for areas of improvement is vital for staying competitive and efficient:
- Technological Advancements: Stay informed about new technologies and techniques in CNC machining and programming. Implement innovations that can enhance your processes.
- Software Updates: Keep your CAM software and CAD tools up to date. Updates often include performance improvements, bug fixes, and new features that can streamline your workflow.
- Process Optimization: Continuously evaluate and refine your CNC programming processes. Identify bottlenecks, inefficiencies, or areas where automation can be introduced to enhance productivity.
By embracing a culture of continuous improvement, you position your team to adapt to evolving industry standards and maintain a competitive edge in the CNC machining arena.
Incorporating these best practices into your CNC programming workflow can lead to smoother operations, higher-quality components, and a more skilled and adaptable team. By fostering collaboration, emphasizing documentation, investing in training, implementing quality control measures, and pursuing continuous improvement, you can navigate the complexities of CNC programming with confidence and success.
Conclusion
Generating CNC programs from SolidWorks designs is a critical step in the modern manufacturing process. By following these tips and best practices, you can ensure that your CNC programs accurately reflect your design intent, leading to efficient machining processes and high-quality components. Remember that successful CNC programming requires a combination of technical expertise, clear communication, and a commitment to continuous improvement.