- Unveiling the Complexity of Weldment Assignments
- Understanding the Top Challenges
- Inaccurate Material Selection
- Complex Geometries and Joint Configurations
- Welding Sequence and Process Challenges
- Lack of Standardization
- Strategies for Overcoming Weldment Challenges
- Embrace Advanced Simulation Techniques
- Collaborate with Welding Experts
- Leverage SolidWorks Automation Tools
- Continuous Learning and Professional Development
- Conclusion:
Embarking on the journey of mastering weldment assignments demands a comprehensive understanding of the challenges that often accompany this intricate facet of 3D design. Solve your Weldment assignment with precision, as weldments, characterized by their complex geometries and diverse joint configurations, present a unique set of obstacles that require adept problem-solving skills. From the crucial selection of materials to the nuanced consideration of welding sequences, engineers and designers must navigate a landscape where precision is paramount. This blog aims to illuminate the common hurdles encountered in weldment assignments and, more importantly, provide actionable insights into overcoming these challenges with finesse.
As the backbone of structural design, weldments demand meticulous attention to detail, making the accuracy of material selection a cornerstone for success. The inherent intricacies in welding processes, coupled with the need for standardized design practices, further contribute to the complexity. In this exploration, we will delve into the depths of these challenges, unraveling the nuances that often perplex even the most seasoned professionals. By addressing these hurdles head-on and employing strategic solutions, individuals can elevate their proficiency in weldment assignments, ultimately achieving a mastery that extends beyond theoretical knowledge to practical, real-world applications.
Unveiling the Complexity of Weldment Assignments
The world of engineering design is both fascinating and intricate, with weldment assignments standing out as particularly complex endeavors. The challenges embedded in weldment assignments stem from the intricate dance between artistry and precision required to bring three-dimensional structures to life. Unlike conventional designs, weldments involve the fusion of multiple components through welding processes, adding layers of complexity that demand a nuanced approach. The intricacies of weldment assignments lie not only in conceptualizing the form and function of the structure but also in navigating the practicalities of material selection, joint configurations, and welding processes. Engineers embarking on weldment assignments find themselves at the crossroads of creativity and technical prowess, facing a dynamic puzzle that demands both strategic planning and a deep understanding of the physical properties governing the materials involved.
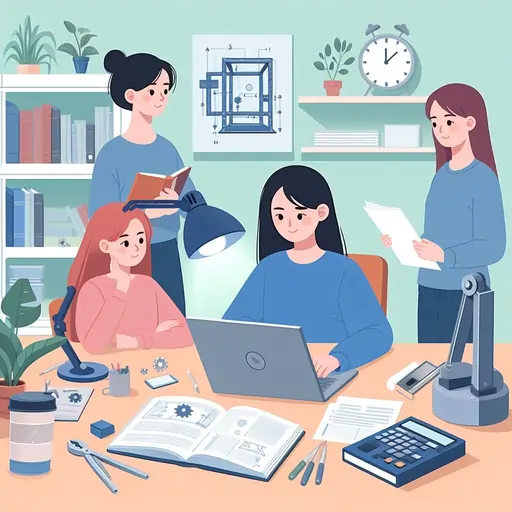
Navigating the complexities of weldment assignments requires a holistic understanding of design principles, material science, and manufacturing processes. From selecting the appropriate materials to seamlessly integrating complex geometries and joints, engineers must orchestrate a symphony of elements to ensure the structural integrity of their designs. The challenges intensify as they delve into the realm of welding sequences and processes, where the choice of techniques can significantly impact the final outcome. Lack of standardization further complicates matters, demanding a disciplined approach to maintain consistency across diverse weldment projects. As we unravel the layers of complexity inherent in weldment assignments, it becomes evident that a comprehensive strategy, leveraging advanced tools and collaborative practices, is essential to surmounting these challenges and achieving excellence in the realm of three-dimensional design.
Understanding the Top Challenges
Understanding the top challenges in weldment assignments is crucial for engineers and designers striving for excellence in their 3D modeling endeavors. One prominent obstacle lies in the meticulous process of material selection, where inaccuracies can compromise the structural integrity of a design. Complex geometries and intricate joint configurations pose another significant challenge, demanding a strategic approach to break down and simplify intricate shapes. The welding sequence and process can be a stumbling block, requiring careful consideration and collaboration with welding experts to ensure optimal structural stability. Additionally, the lack of standardization in design can lead to inconsistencies, emphasizing the importance of adhering to industry standards and implementing a systematic approach. By comprehending and addressing these challenges head-on, professionals can elevate their weldment assignments to new heights of precision and efficiency.
Inaccurate Material Selection
One of the primary challenges faced in weldment assignments is the potential for inaccurate material selection. The repercussions of choosing the wrong materials can be severe, impacting the structural integrity and performance of the final design. Engineers must navigate a myriad of factors, including material strength, durability, and compatibility with welding processes. The solution lies in meticulous research and analysis during the initial stages of the project. By leveraging SolidWorks tools to thoroughly investigate material properties, engineers can make informed decisions, ensuring that the selected materials not only meet the design requirements but also contribute to the overall success of the weldment. Overcoming the challenge of inaccurate material selection is a pivotal step toward creating weldments that not only meet but exceed performance expectations.
Complex Geometries and Joint Configurations
Navigating the intricacies of complex geometries and joint configurations is a common hurdle in weldment assignments. To overcome this challenge, engineers can employ a systematic approach. Break down the design into manageable components, focusing on simplifying each element before integrating them into the overall structure. SolidWorks provides powerful tools such as the Weldment feature and Structural Member, which allow for precise control over joint configurations. By utilizing these features strategically, designers can streamline the creation of complex weldments, ensuring that each joint aligns seamlessly with the intended design. Additionally, employing the Weld Beads feature in SolidWorks facilitates the visualization and implementation of welds, contributing to a more accurate representation of the final product. Through a combination of thoughtful component design and leveraging SolidWorks capabilities, engineers can confidently tackle the challenges posed by complex geometries and joint configurations in weldment assignments.
Welding Sequence and Process Challenges
One of the critical aspects of weldment assignments lies in devising the optimal welding sequence and process. The challenges in this arena often revolve around ensuring not only the structural integrity of the design but also the practical feasibility of the welding procedures. To overcome these challenges, collaboration with welding experts is indispensable. By engaging in an open dialogue with professionals well-versed in the nuances of welding, designers can gain invaluable insights into the intricacies of welding sequences. Additionally, leveraging SolidWorks simulation tools proves to be a game-changer, allowing engineers to virtually visualize and analyze the welding process. This proactive approach not only identifies potential issues but also empowers designers to fine-tune their welding sequences, ensuring a seamless transition from the virtual realm to the physical creation of robust and weld-friendly structures.
Lack of Standardization
One of the persistent challenges in weldment assignments is the lack of standardization, which can introduce inconsistencies and errors into the design process. Without a unified set of guidelines and practices, engineers may find themselves grappling with varied approaches, hindering collaboration and increasing the likelihood of oversights. To overcome this challenge, it is essential to establish and adhere to industry-standard protocols in weldment design. SolidWorks, with its extensive libraries and templating features, provides a robust framework for enforcing standardization across projects. By implementing standardized procedures and leveraging the tools available, engineers can mitigate the risk of errors, enhance collaboration, and ensure that their weldment assignments meet the highest quality and compliance standards.
Strategies for Overcoming Weldment Challenges
When confronted with the intricacies of weldment challenges, employing strategic approaches is pivotal to ensuring successful outcomes. Firstly, embrace advanced simulation techniques offered by SolidWorks Simulation. This allows for a virtual testing ground, enabling engineers to identify potential issues and refine designs before they progress to the manufacturing stage. Additionally, fostering collaboration with welding experts proves invaluable. Their practical insights into welding sequences and processes can significantly enhance the feasibility and efficiency of your designs. Leveraging SolidWorks automation tools, such as Weldment Profiles, Structural Member, and Weld Beads, streamlines the design process, minimizing errors and expediting project timelines. Lastly, commit to continuous learning and professional development to stay at the forefront of 3D modeling advancements, ensuring that your approach to weldment assignments remains innovative and adaptive. By integrating these strategies, engineers can navigate and conquer the challenges inherent in weldment assignments with precision and confidence.
Embrace Advanced Simulation Techniques
To overcome the challenges embedded in weldment assignments, engineers can significantly benefit from embracing advanced simulation techniques. SolidWorks Simulation, a powerful tool within the SolidWorks ecosystem, empowers designers to virtually test and analyze weldment structures under a myriad of conditions. By simulating the complex interactions between materials and forces, engineers gain invaluable insights into the structural behavior of their designs. This proactive approach allows for the identification of potential weaknesses or inefficiencies early in the design process, enabling necessary adjustments to be made before the physical prototyping stage. Embracing advanced simulation not only enhances the overall accuracy of the weldment assignment but also fosters a more robust and efficient design workflow, ultimately contributing to the creation of structurally sound and reliable weldments.
Collaborate with Welding Experts
Collaboration with welding experts is a pivotal strategy for overcoming challenges related to welding sequences and processes in weldment assignments. Welding professionals bring a wealth of practical experience to the table, offering insights that can significantly enhance the manufacturability and structural integrity of your designs. By fostering an open dialogue with experts in the field, engineers can gain valuable knowledge about the nuances of different welding techniques, optimal sequences, and potential pitfalls to avoid. This collaborative approach not only ensures the feasibility of the design but also promotes a synergy between theoretical concepts and real-world application. Through this partnership, engineers can refine their understanding of welding intricacies, leading to more informed decision-making and ultimately producing weldment designs that stand up to rigorous standards and expectations.
Leverage SolidWorks Automation Tools
One key strategy to overcome challenges in weldment assignments is to leverage the powerful automation tools provided by SolidWorks. These tools are designed to enhance efficiency and accuracy throughout the design process. SolidWorks offers features such as Weldment Profiles, which allow users to quickly define and apply standardized cross-sections for structural members. The Structural Member tool streamlines the creation of complex frame structures, enabling designers to focus on the overall concept rather than getting bogged down in the details. Additionally, the Weld Beads feature automates the generation of weld beads along specified joints, ensuring precise and consistent weld representations. By incorporating these automation tools into your workflow, you not only save valuable time but also minimize the risk of errors, leading to more robust and well-executed weldment designs.
Continuous Learning and Professional Development
In the ever-evolving landscape of 3D modeling and design, the commitment to continuous learning and professional development is the linchpin for overcoming challenges in weldment assignments. Embracing a mindset of perpetual growth allows engineers and designers to stay ahead of emerging technologies and industry trends. Engaging in ongoing education, attending workshops, and participating in online forums provide invaluable platforms for knowledge exchange and skill enhancement. Furthermore, staying connected with professional networks fosters a collaborative environment where individuals can share insights and learn from each other's experiences. By prioritizing continuous learning, professionals not only refine their proficiency in SolidWorks but also gain a deeper understanding of evolving welding techniques and best practices, empowering them to tackle complex weldment assignments with adaptability and expertise.
Conclusion:
In the realm of 3D design and engineering, overcoming the challenges inherent in weldment assignments is not just a task but a journey toward mastery. The intricacies of material selection, the puzzle of complex geometries, and the precision required in welding processes all contribute to the multifaceted nature of weldment assignments. As we navigate through these challenges, it becomes evident that the key to mastering weldments lies in a holistic approach. By embracing advanced simulation techniques, collaborating with welding experts, leveraging automation tools in SolidWorks, and committing to continuous learning, designers and engineers can navigate the intricate path of weldment assignments with confidence.
The journey toward mastering weldments is not only about overcoming challenges but also about fostering a mindset of innovation and adaptability. In a field that is constantly evolving, the ability to embrace new technologies and methodologies is crucial. The conclusion, therefore, is not the end but a starting point for a continuous cycle of improvement and growth. As designers and engineers refine their skills, apply lessons learned from challenges, and stay attuned to industry advancements, they not only master the intricacies of weldment assignments but also contribute to the evolution of 3D design and engineering as a whole. In this journey, confidence is not just a result; it's a mindset that propels professionals toward excellence in weldment assignments and beyond.