- Importing and Exporting Files in SOLIDWORKS
- Understanding File Formats
- Importing Files
- Key Steps:
- Best Practices:
- Exporting Files
- Key Steps:
- Best Practices:
- Recognizing Features in Non-SOLIDWORKS Parts with FeatureWorks
- What is FeatureWorks?
- Recognizing Features
- Key Steps:
- Best Practices:
- Working with Complex Parts
- Key Steps:
- Best Practices:
- Performing Stress Analysis with SimulationXpress
- What is SimulationXpress?
- Setting Up a Simulation
- Key Steps:
- Best Practices:
- Interpreting Results
- Key Results:
- Best Practices:
- Strengthening the Design
- Key Steps:
- Best Practices:
- Integrating the Skills: A Practical Assignment Workflow
- Conclusion
In the world of modern engineering, collaboration across different software platforms and ensuring the robustness of designs are crucial elements in the success of any project. Whether you're working within a team or with external partners, the ability to import and export files seamlessly, recognize and edit features in non-SOLIDWORKS parts, and perform stress analysis are essential skills in SOLIDWORKS. Mastering these capabilities not only enhances your efficiency but also ensures that your designs meet the highest standards of quality and safety. As you navigate through CAD assignments, having a solid grasp of these tools will empower you to handle complex tasks with confidence. Whether you need SolidWorks assignment help to overcome specific challenges or are seeking to broaden your expertise, understanding these core features is invaluable. In this detailed guide, we will delve into these key aspects, providing you with the knowledge and practical steps needed to excel in your SOLIDWORKS assignments.
Importing and Exporting Files in SOLIDWORKS
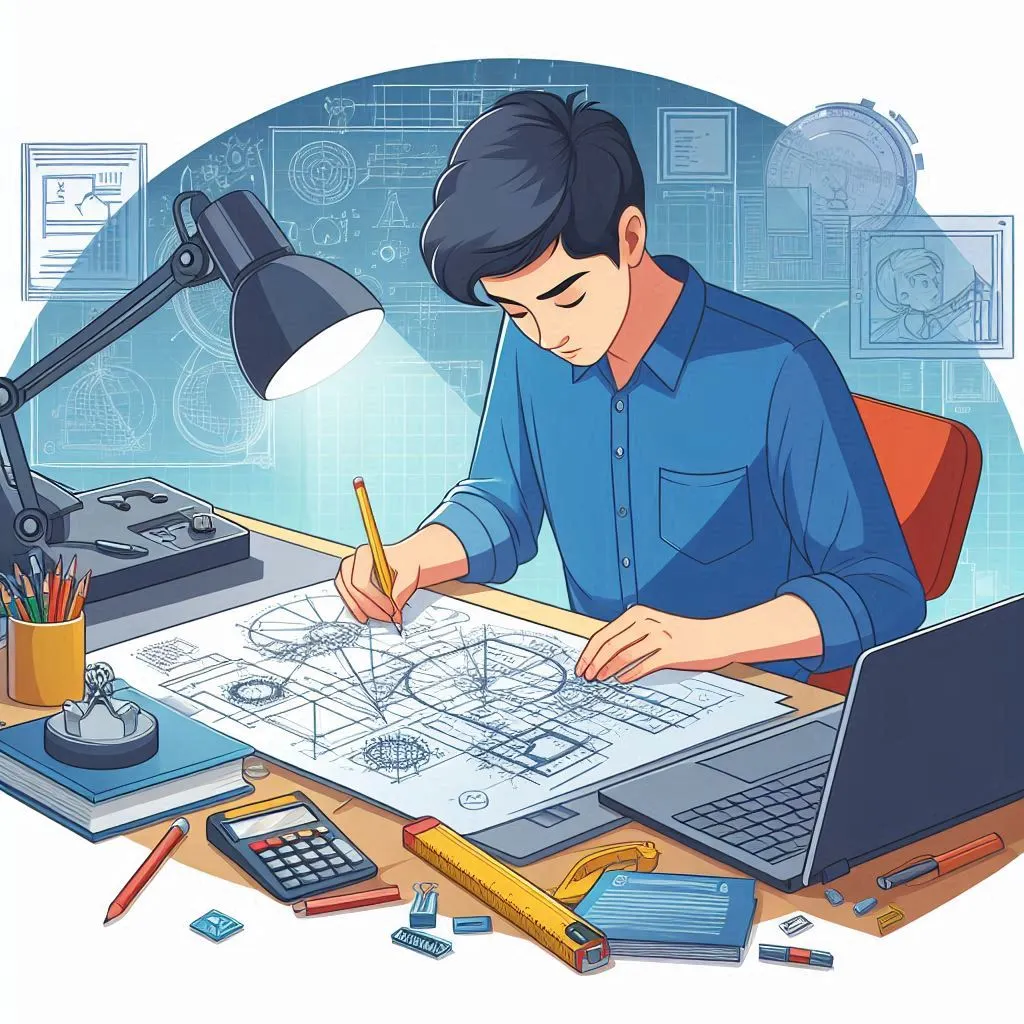
In any collaborative engineering project, the ability to share files across different CAD systems is invaluable. SOLIDWORKS offers robust tools for importing and exporting files, allowing you to work with a variety of file formats and ensuring compatibility with other CAD systems. Whether you need to import legacy data from a vendor or export a design for manufacturing, SOLIDWORKS makes the process straightforward.
Understanding File Formats
SOLIDWORKS supports a wide range of file formats for both import and export. Common formats include:
- STEP (.step, .stp): A widely-used format that supports the exchange of 3D models between different CAD systems.
- IGES (.iges, .igs): Another popular format for sharing 3D data, especially in automotive and aerospace industries.
- DXF/DWG (.dxf, .dwg): Primarily used for 2D drawings, often in collaboration with AutoCAD.
- Parasolid (.x_t, .x_b): The native format for Parasolid-based CAD systems, ensuring precise geometry.
- STL (.stl): Commonly used for 3D printing, representing the surface geometry of a 3D object.
Understanding the strengths and limitations of each format will help you choose the right one for your needs.
Importing Files
When importing a file into SOLIDWORKS, the process begins by navigating to File and Open and selecting the appropriate file type from the drop-down menu. SOLIDWORKS automatically detects the format and offers options to customize the import process.
Key Steps:
- Open the File: Choose the file you wish to import. SOLIDWORKS will provide you with options such as Import Diagnostics, which checks and repairs any geometry issues, ensuring the integrity of the imported model.
- Customize the Import: Depending on the file type, you may have options like Units of Measure, Quality of the Model, and Curve Tolerance. These settings allow you to optimize the import based on your specific needs.
- Check for Errors: After importing, use the Import Diagnostics tool to identify and fix any issues with the model, such as gaps or misaligned surfaces.
Best Practices:
- Use Import Diagnostics: Always run Import Diagnostics to ensure the imported geometry is accurate and free of errors.
- Optimize Settings: Adjust the import settings to balance model accuracy with performance, especially for complex or large assemblies.
Exporting Files
Exporting files from SOLIDWORKS is equally important, especially when sharing designs with external partners or vendors who may use different CAD software. The process is simple but requires attention to detail to ensure the exported file meets the recipient’s needs.
Key Steps:
- Save As: Go to File and Save As and select the desired file format from the drop-down list. SOLIDWORKS provides a variety of export options, including STEP, IGES, DXF/DWG, and STL.
- Customize the Export: Depending on the file format, you can adjust settings like Units of Measure, Tessellation Quality, and Face/Surface Representation. These options allow you to control the precision and compatibility of the exported file.
- Export Selected Entities: If you only need to export a specific part or assembly, SOLIDWORKS allows you to select the entities to include in the export, reducing file size and complexity.
Best Practices:
- Check Compatibility: Before exporting, ensure that the recipient’s CAD system can handle the file format and settings you’ve chosen.
- Simplify Models: If exporting for use in a different CAD system, consider simplifying the model to reduce file size and complexity.
By mastering the import and export functions in SOLIDWORKS, you can ensure seamless collaboration across different CAD platforms, enhancing the flexibility and efficiency of your design process.
Recognizing Features in Non-SOLIDWORKS Parts with FeatureWorks
One of the most powerful aspects of SOLIDWORKS is its ability to work with files from other CAD systems, such as legacy STEP or IGES files. However, these files often lack the parametric features that make SOLIDWORKS models so flexible. This is where FeatureWorks comes in. FeatureWorks allows you to recognize and edit features in imported parts as if they were created natively in SOLIDWORKS, saving you the time and effort of remodeling.
What is FeatureWorks?
FeatureWorks is an add-on application within SOLIDWORKS that recognizes features in imported solid bodies, converting them into editable SOLIDWORKS features. This tool is particularly useful for working with machined and sheet metal parts, where feature recognition can save considerable time.
Recognizing Features
When you import a non-SOLIDWORKS file, such as a STEP or IGES file, the geometry comes in as a solid body without any parametric features. FeatureWorks analyzes this geometry and recognizes features like extrudes, cuts, fillets, and chamfers.
Key Steps:
- Activate FeatureWorks: After importing the file, go to Insert > FeatureWorks > Recognize Features. SOLIDWORKS will prompt you to select the features you want to recognize.
- Automatic vs. Interactive Recognition: FeatureWorks offers both automatic and interactive feature recognition. Automatic recognition is faster and works well for simpler parts, while interactive recognition gives you more control over complex geometries.
- Edit Recognized Features: Once the features are recognized, they appear in the FeatureManager Design Tree like any other SOLIDWORKS feature. You can edit the dimensions, suppress or delete features, and even add new features.
Best Practices:
- Start with Automatic Recognition: Use automatic recognition to quickly identify basic features, then switch to interactive mode for more complex features.
- Refine Feature Definitions: After recognition, review the features and refine their definitions as needed to match your design intent.
Working with Complex Parts
For complex parts with intricate geometries, FeatureWorks allows you to selectively recognize features, giving you control over which aspects of the model are converted to SOLIDWORKS features. This is particularly useful when working with parts that include a mix of simple and complex features.
Key Steps:
- Select Features Manually: In interactive mode, you can manually select specific faces or edges to recognize as features. This allows you to focus on the most critical aspects of the model.
- Use FeatureWorks Options: Customize the recognition process by adjusting options like Feature Recognition Tolerance and Face Merging, which can help with challenging geometries.
Best Practices:
- Break Down Complex Parts: If a part is too complex to recognize all at once, consider breaking it down into simpler segments and recognizing features in stages.
- Verify Geometry: After recognizing features, use tools like Check and Evaluate to verify that the geometry is accurate and meets your design requirements.
FeatureWorks is an invaluable tool for anyone working with imported files, enabling you to convert non-SOLIDWORKS models into fully editable SOLIDWORKS parts. This capability can significantly streamline your workflow, especially when dealing with legacy data or parts from external sources.
Performing Stress Analysis with SimulationXpress
Design validation is a critical part of the engineering process, and SOLIDWORKS offers a powerful tool for this purpose: SimulationXpress. This entry-level stress analysis tool allows you to test the strength and performance of your designs under various conditions, helping you identify potential issues before they become costly problems.
What is SimulationXpress?
SimulationXpress is a simplified version of SOLIDWORKS Simulation, designed for users who need basic stress analysis capabilities. It provides a quick and easy way to evaluate the structural integrity of a part by simulating how it responds to forces, pressures, and constraints.
Setting Up a Simulation
Setting up a stress analysis in SimulationXpress is straightforward, making it accessible even for users with limited experience in simulation.
Key Steps:
- Access SimulationXpress: To start, go to Tools > SimulationXpress. This opens the SimulationXpress wizard, which guides you through the setup process.
- Define Material Properties: Select the material for your part from the SOLIDWORKS material library. The material properties, such as Young’s modulus and Poisson’s ratio, are crucial for accurate stress analysis.
- Apply Fixtures and Loads: Define how the part is constrained (fixtures) and where forces or pressures are applied (loads). For example, you might fix one end of a beam and apply a force to the other end.
- Run the Simulation: Once everything is set up, run the simulation. SimulationXpress calculates the stress distribution, displacement, and factor of safety across the part.
Best Practices:
- Simplify the Model: Start with a simplified version of your part to reduce computation time and complexity.
- Use Symmetry: If your part is symmetric, use symmetry fixtures to reduce the model size and computation time.
Interpreting Results
After running the simulation, SimulationXpress provides a range of results, including stress distribution and displacement plots, factor of safety, and critical regions where failure might occur. Interpreting these results correctly is essential for making informed design decisions.
Key Results:
- Stress Distribution: The stress plot shows how the applied loads are distributed across the part. Areas with high stress concentrations are often at risk of failure, especially if they exceed the material's yield strength.
- Displacement: This plot displays how much the part deforms under load. Excessive displacement can indicate potential issues with structural integrity, especially if it affects the part's functionality.
- Factor of Safety: The factor of safety (FOS) is a measure of how much stronger the part is compared to the required load. A higher FOS indicates a safer design, but it may also suggest that the part is over-engineered, leading to unnecessary material costs.
Best Practices:
- Focus on Critical Areas: Pay particular attention to regions with high stress or large displacements, as these are the area's most likely to require design modifications.
- Balance Safety and Efficiency: While a higher factor of safety is generally better, consider the trade-off between safety and material usage. Aim for an optimal balance that ensures both safety and cost-effectiveness.
Strengthening the Design
Based on the simulation results, you may need to make design changes to improve the part's performance. This might involve increasing material thickness in high-stress areas, altering the material properties, or redesigning features to better distribute loads.
Key Steps:
- Modify the Design: Use the results from SimulationXpress to identify and modify weak points in your design. For example, if a certain region shows excessive stress, you might add a fillet or increase the wall thickness.
- Re-run the Simulation: After making changes, re-run the simulation to see how the modifications affect the stress distribution and displacement. Continue this iterative process until you achieve a satisfactory design.
- Document the Process: Keep detailed records of your design iterations and simulation results. This documentation can be invaluable for future reference and for communicating your design decisions to team members or stakeholders.
Best Practices:
- Iterate and Improve: SimulationXpress is a powerful tool for iterative design. Use it to test multiple design variations, gradually refining your model to achieve the best possible performance.
- Consider Real-world Conditions: While SimulationXpress provides valuable insights, remember that it's a simplified tool. Always consider real-world factors that might affect the part's performance, such as environmental conditions, manufacturing tolerances, and material inconsistencies.
Integrating the Skills: A Practical Assignment Workflow
Now that we've covered the individual tools and techniques, let's consider how you might integrate them into a practical workflow for a SOLIDWORKS assignment. Imagine you are tasked with designing a mechanical component that will be manufactured by a vendor using a different CAD system. The assignment requires you to import the vendor's existing design, recognize and modify its features, and perform a stress analysis to ensure the component meets safety requirements.
- Step 1: Import the Vendor's Design Start by importing the design file provided by the vendor. Use SOLIDWORKS' import tools to bring the file into your workspace, ensuring that any geometry issues are resolved during the import process. This might involve running Import Diagnostics and adjusting the import settings for optimal accuracy.
- Step 2: Recognize and Modify Features Once the design is imported, use FeatureWorks to recognize the key features in the part. Convert these features into editable SOLIDWORKS features, allowing you to make the necessary modifications. For example, you might need to adjust the size of a hole, change the dimensions of an extrude, or add new features that were not included in the original design.
- Step 3: Perform Stress Analysis With the design modifications complete, set up a stress analysis using SimulationXpress. Apply the appropriate material properties, fixtures, and loads, then run the simulation to evaluate the part's performance. Pay close attention to the stress distribution and displacement results, and use this information to make any final adjustments to the design.
- Step 4: Export the Final Design After finalizing the design, export the file in the format required by the vendor. Ensure that all necessary details, such as units of measure and file compatibility, are correctly configured to facilitate a smooth handoff.
- Step 5: Document and Present Your Work Finally, prepare a detailed report that documents your design process, including the initial import, feature recognition, modifications, and stress analysis results. This report will serve as a valuable resource for future projects and provide transparency in your design decisions.
Conclusion
Mastering the ability to import and export files, recognize features in non-SOLIDWORKS parts, and perform stress analysis is essential for any SOLIDWORKS user looking to excel in their assignments and projects. These skills not only enhance your efficiency and flexibility but also ensure that your designs are robust, safe, and ready for real-world application.
By integrating these tools into your workflow, you can tackle even the most complex engineering challenges with confidence, knowing that you have the expertise to handle every aspect of the design process. Whether you're collaborating with external partners, working with legacy data, or ensuring the structural integrity of your parts, these techniques will empower you to deliver high-quality designs that meet the demands of modern engineering.