- Identify the Model Requirements
- Understanding Requirements
- Documenting Requirements
- Visualizing Requirements
- Conceptualize the Model Based on the Identified Needs
- Brainstorming Ideas
- Evaluating Concepts
- Selecting the Best Concept
- Develop the Model Based on the Concepts
- Creating Detailed Models
- Iterating the Design
- Collaborating with Team Members
- Analyze the Model
- Structural Analysis
- Thermal Analysis
- Fluid Dynamics Analysis
- Validating the Model
- Prototype the Model
- Creating a Prototype
- Testing the Prototype
- Iterating Based on Feedback
- Construct the Model
- Preparing Detailed Drawings
- Creating Specifications
- Coordinating with Manufacturers
- Edit the Model, if Needed
- Conducting a Thorough Review
- Making Necessary Modifications
- Final Validation
The engineering design process is a structured approach integral to the creation of functional and reliable products in various fields of engineering. Engineers and designers rely on this methodical approach to transform initial concepts into tangible, effective solutions. This process is foundational in ensuring that products not only meet but exceed expectations in terms of performance, durability, and functionality. Each step of this process plays a crucial role in guiding the development of innovative solutions that address specific needs and challenges.
SolidWorks assignment help is particularly beneficial during the conceptualization and development phases of the design process. This powerful CAD software enables engineers to translate complex ideas into detailed 3D models with precision and efficiency. By leveraging SolidWorks, designers can explore multiple design iterations, optimize geometries, and simulate real-world conditions to validate their concepts. This iterative approach fosters creativity and ensures that the final product aligns closely with initial requirements.
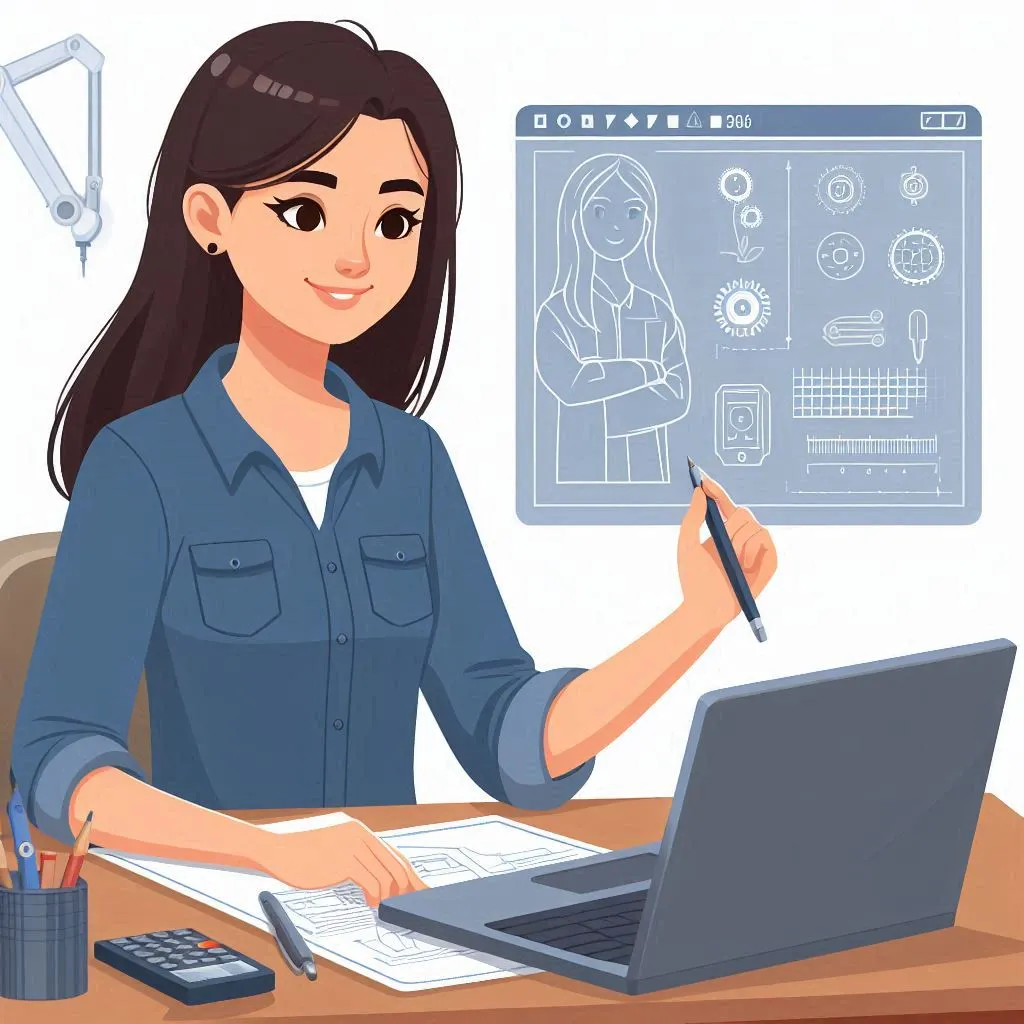
Product design assignment help extends beyond software proficiency, encompassing a holistic understanding of user needs, technological feasibility, and market demands. Engineers collaborate closely with stakeholders, including clients and end-users, to gather comprehensive product design assignment help. This collaborative approach ensures that every aspect of the design—from aesthetics to functionality—is meticulously considered and refined throughout the development process.
The journey from concept to construction involves meticulous planning, collaboration, and continuous refinement. Engineers and designers must navigate through various stages—from initial ideation to prototype testing and final manufacturing. Each step represents an opportunity to innovate, iterate, and enhance the design, ultimately delivering solutions that push the boundaries of what is possible in engineering. By embracing the principles of the engineering design process and leveraging advanced tools like SolidWorks, professionals can achieve remarkable results that meet the highest standards of quality and innovation in product development.
Identify the Model Requirements
The first and most crucial step in any design project is to identify the model requirements. This step sets the foundation for the entire design process and involves understanding the purpose of the model, the conditions it will operate under, and any constraints or specifications that must be met.
Understanding Requirements
Understanding the requirements means you need to have a clear grasp of what the end product is supposed to achieve. This involves discussing with stakeholders, including clients, team members, and end-users, to gather detailed information. Ask questions like:
- What is the primary function of the model?
- What are the expected operating conditions?
- Are there any specific materials or dimensions that must be used?
- Are there any regulatory or compliance standards that must be met?
Documenting Requirements
Documenting requirements is essential to ensure that everyone involved in the project is on the same page. Create a comprehensive list of specifications and constraints. This document should include:
- Functional requirements: What the product needs to do.
- Performance requirements: How well the product needs to perform.
- Physical requirements: Size, weight, and material specifications.
- Environmental requirements: Operating conditions like temperature, humidity, and exposure to chemicals.
- Compliance requirements: Regulatory standards and certifications.
Visualizing Requirements
Visualizing the requirements can help in understanding the project better. Use sketches, diagrams, and initial models to get a visual sense of what is needed. This can also help in identifying any potential issues early in the process.
Tips:
- Communicate with stakeholders to gather all necessary information.
- Create a list of specifications and constraints.
- Use sketches or diagrams to visualize the requirements.
Conceptualize the Model Based on the Identified Needs
Once you have a clear understanding of the requirements, the next step is to conceptualize the model. This involves brainstorming various design solutions and selecting the most promising ones to develop further.
Brainstorming Ideas
Start by brainstorming multiple ideas and design solutions. Don’t limit yourself at this stage; consider all possibilities, no matter how unconventional they may seem. Use techniques like mind mapping and sketching to explore different ideas.
Evaluating Concepts
After generating a range of ideas, evaluate each concept against the identified requirements. Consider factors such as feasibility, cost, and time. Use a scoring system or decision matrix to objectively compare each concept.
Selecting the Best Concept
Choose the concept that best meets the requirements and has the highest potential for success. It’s often useful to select a few top concepts and refine them further before making a final decision.
Tips:
- Generate multiple ideas through brainstorming sessions.
- Evaluate each concept against the identified requirements.
- Use rough sketches and diagrams to explore different design possibilities.
Develop the Model Based on the Concepts
With a solid concept in mind, it’s time to develop the model in detail. This step involves creating precise drawings or 3D models that capture all aspects of the design.
Creating Detailed Models
Use CAD (Computer-Aided Design) software to create detailed models. CAD tools allow for precise control over dimensions and can help in visualizing the final product. Start with basic shapes and gradually add details.
Iterating the Design
Design is an iterative process. You may need to create several versions of the model before arriving at the final design. Each iteration should bring you closer to meeting all requirements.
Collaborating with Team Members
Collaboration is key during the development phase. Work closely with other team members, including engineers, designers, and stakeholders, to ensure that the model meets all expectations.
Tips:
- Start with simple shapes and gradually add complexity.
- Utilize CAD software to create accurate and detailed models.
- Ensure that the model adheres to all identified requirements and constraints.
Analyze the Model
After developing the model, it’s essential to analyze its performance and ensure it meets all requirements. This can involve various types of analysis, such as structural, thermal, or fluid dynamics, depending on the nature of the project.
Structural Analysis
Structural analysis helps in understanding how the model will respond to forces and loads. Use simulation tools to analyze stress, strain, and deformation. Ensure that the model can withstand expected loads without failure.
Thermal Analysis
Thermal analysis is crucial for models that will operate under varying temperature conditions. Analyze how heat will affect the model and ensure that it can maintain its functionality within the specified temperature range.
Fluid Dynamics Analysis
For models involving fluid flow, conduct fluid dynamics analysis to understand how fluids will interact with the model. This can help in optimizing the design for better performance and efficiency.
Validating the Model
Validate the model’s performance against the initial requirements. Identify and address any potential design flaws or weaknesses. Use the results of the analysis to make necessary adjustments.
Tips:
- Use simulation tools to perform detailed analyses.
- Identify and address any potential design flaws or weaknesses.
- Validate the model’s performance against the initial requirements.
Prototype the Model
Prototyping is a critical step that allows you to test the model in real-world conditions. Creating a physical prototype can help identify practical issues that might not be evident in the digital model.
Creating a Prototype
Use techniques like 3D printing, CNC machining, or traditional manufacturing methods to create a physical prototype. Choose the method that best suits the complexity and requirements of your model.
Testing the Prototype
Test the prototype thoroughly to assess its functionality and durability. Conduct tests under conditions that mimic the real-world environment in which the model will operate. Gather feedback from users or stakeholders to identify any issues.
Iterating Based on Feedback
Use the feedback from prototype testing to make necessary adjustments to the design. This may involve refining certain aspects of the model or making significant changes to improve performance.
Tips:
- Use 3D printing or other prototyping techniques to create a physical model.
- Test the prototype thoroughly to assess its functionality and durability.
- Gather feedback from users or stakeholders and make necessary adjustments.
Construct the Model
Once the prototype is validated, you can proceed to construct the final model. This involves creating detailed manufacturing drawings and specifications that guide the construction process.
Preparing Detailed Drawings
Prepare precise and comprehensive construction drawings. These drawings should include all necessary details such as dimensions, tolerances, and materials. Ensure that the drawings are clear and easy to understand.
Creating Specifications
In addition to drawings, create detailed specifications that outline the materials, processes, and quality standards required for construction. This document should serve as a guide for manufacturers and ensure that the final product meets all requirements.
Coordinating with Manufacturers
Work closely with manufacturers to ensure that the model is constructed correctly. Provide them with all necessary documentation and be available to answer any questions or address any issues that arise during construction.
Tips:
- Prepare precise and comprehensive construction drawings.
- Include all necessary details such as dimensions, tolerances, and materials.
- Ensure that the construction documentation complies with industry standards.
Edit the Model, if Needed
The final step is to review and edit the model based on feedback and testing results. This might involve making minor adjustments or significant changes to optimize the design.
Conducting a Thorough Review
Before finalizing the model, conduct a thorough review. Check all aspects of the design to ensure that it meets all requirements and performs as expected.
Making Necessary Modifications
Based on the review, make any necessary modifications to the model. This may involve adjusting dimensions, changing materials, or improving certain features. Document all changes and ensure that the final design is ready for production.
Final Validation
Once all modifications are made, conduct a final validation to ensure that the model is ready for production. This may involve additional testing or analysis to confirm that all requirements are met.
Tips:
- Review the model thoroughly before final submission.
- Make any necessary adjustments to improve performance or manufacturability.
- Document all changes and ensure the final design is ready for production.
By following these steps, you can successfully navigate the engineering design process from start to finish. Each stage is crucial for developing a functional and reliable product that meets all specified requirements. Remember, the design process is iterative, and continuous improvement is key to achieving the best possible outcome.