- Importance of SolidWorks in Marine Engineering Assignments
- Key Features of SolidWorks for Marine Engineering:
- Understanding Marine Engineering Components for Design
- Types of Boat Components
- Technical Considerations in Component Design
- Step-by-Step Guide to Designing a Boat Hull in SolidWorks
- Advanced Techniques for Boat Component Design
- Integrating Propulsion Systems
- Simulating Propulsion Systems
- Designing Deck Fittings
- Tips for Optimizing SolidWorks Designs
- Efficient Use of SolidWorks Tools
- Debugging and Refinement
- Conclusion
Marine engineering is the field dedicated to the design, construction, and maintenance of ships, boats, and other marine vessels. In this discipline, assignments often focus on practical tasks like designing and optimizing boat components. One of the most valuable tools for marine engineers is SolidWorks, a powerful 3D CAD software that simplifies the modeling, analysis, and simulation of components. SolidWorks enables engineers to create highly detailed designs, analyze materials and structures, and test performance under real-world conditions. For students tackling assignments that involve boat component design, mastering SolidWorks is crucial. With its wide range of features, such as parametric modeling, flow simulations, and assembly tools, students can create precise and functional designs. Whether you're working on hull structures, propulsion systems, or deck fittings, SolidWorks allows you to visualize and optimize your ideas effectively. For those struggling with complex tasks or lacking experience, seeking help with SolidWorks assignment can be a great way to gain insights and guidance from experts. With proper use of SolidWorks, students can complete marine engineering assignments more efficiently, producing high-quality designs that meet industry standards. This blog provides a step-by-step approach to help students succeed in their SolidWorks assignments and enhance their understanding of marine engineering design.
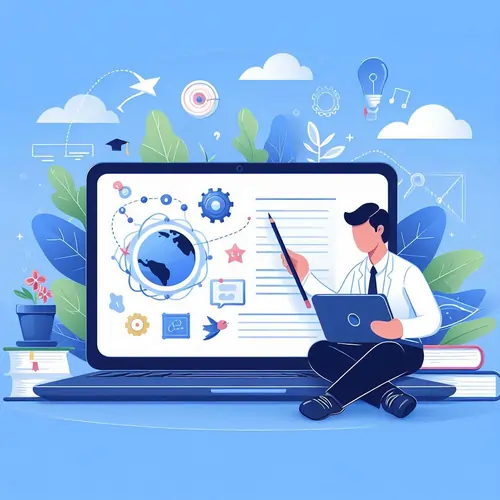
Importance of SolidWorks in Marine Engineering Assignments
SolidWorks plays a significant role in marine engineering, offering advanced modeling capabilities that are invaluable for designing and analyzing boat components. Its tools allow engineers to create detailed 3D models and simulate real-world scenarios, ensuring designs meet functional and performance requirements. For students, mastering SolidWorks is a game-changer, enabling them to efficiently handle marine engineering assignments and develop practical design solutions. The software supports tasks like hydrodynamic analysis, structural validation, and precise assembly of components, making it a versatile tool in the field. By understanding how to utilize its features effectively, students can not only excel academically but also build a strong foundation for professional success. SolidWorks provides the opportunity to innovate, test, and refine designs, giving future marine engineers a competitive edge in tackling complex challenges and contributing to advancements in maritime technology.
Key Features of SolidWorks for Marine Engineering:
- 3D Parametric Modeling: Allows precise control of dimensions and features.
- Simulation Tools: Analyze components for stress, buoyancy, and hydrodynamics.
- Assembly Design: Build and test complex assemblies, such as hulls and propulsion systems.
- Drafting Tools: Create production-ready technical drawings with ease.
- Material Selection: Choose materials based on mechanical properties and marine standards.
Understanding these tools is vital for designing efficient and innovative boat components.
Understanding Marine Engineering Components for Design
Understanding marine engineering components is crucial for effective design and solving assignments. Key boat components, such as the hull, propulsion system, deck fittings, steering mechanisms, and structural reinforcements, each play vital roles. The hull is the main body of the boat, designed for buoyancy and hydrodynamics, ensuring stability and efficiency in water. Propulsion systems, including propellers, shafts, and engines, enable movement and must be precisely designed for performance. Deck fittings, such as cleats and hatches, enhance functionality and safety, while steering mechanisms, like rudders, provide navigational control. Structural reinforcements, including bulkheads and frames, add strength and durability, ensuring the boat withstands marine stresses. Each component requires careful consideration of technical factors like material selection, weight distribution, and hydrodynamic efficiency. A clear understanding of these components helps students design practical and innovative solutions, addressing both functionality and safety in their assignments.
Types of Boat Components
Before diving into SolidWorks, it's essential to understand the key components of a boat and their design considerations:
- Hull: The boat’s primary body, designed for buoyancy and hydrodynamics.
- Propulsion System: Includes propellers, shafts, and engines for movement.
- Deck Fittings: Includes cleats, winches, and hatches, essential for functionality and safety.
- Steering Mechanisms: Rudders and control systems to navigate the boat.
- Structural Components: Reinforcements like bulkheads and frames for stability.
Each of these components has unique design requirements that students must address in their assignments.
Technical Considerations in Component Design
When designing boat components, several technical factors come into play:
- Hydrodynamics: Ensure the hull design minimizes resistance in water.
- Structural Integrity: Materials and shapes should withstand marine stresses, such as waves and corrosion.
- Weight Distribution: Improper distribution can compromise stability.
- Material Selection: Must be durable, lightweight, and corrosion-resistant.
Understanding these considerations ensures your SolidWorks designs are realistic and practical.
Step-by-Step Guide to Designing a Boat Hull in SolidWorks
Designing a boat hull in SolidWorks involves understanding the principles of hydrodynamics, structural stability, and material properties. The hull serves as the primary interface between the vessel and water, influencing performance and safety. A well-designed hull minimizes drag, ensures buoyancy, and provides structural support. SolidWorks offers advanced tools like spline-based sketching, surface modeling, and simulation features to create precise and functional hull designs. By leveraging these capabilities, students can experiment with different shapes and configurations, validate their designs through simulations, and optimize for real-world conditions. This process integrates technical knowledge with practical application, essential for marine engineering success.
Step 1: Creating a Sketch
- Begin with a 2D sketch of the hull’s cross-section using the Spline Tool for smooth curves.
- Define key dimensions, such as length, width, and depth, ensuring compliance with the assignment’s specifications.
Step 2: Extrude the Hull Profile
- Use the Extrude Boss/Base feature to transform the sketch into a 3D model.
- Adjust the extrusion length to match the boat’s required dimensions.
Step 3: Refining the Shape
- Use the Fillet Tool to smooth edges and corners, improving hydrodynamics.
- Apply the Shell Tool to hollow the model, defining the hull’s thickness.
Step 4: Adding Structural Features
- Create ribs and bulkheads using the Extruded Cut or Linear Pattern tools.
- Ensure these reinforcements align with the load distribution.
Step 5: Simulating Hydrodynamic Performance
- Utilize the Flow Simulation Add-in to analyze water flow around the hull.
- Identify and address areas of high resistance to optimize performance.
By following these steps, you can create a functional and efficient hull design in SolidWorks.
Advanced Techniques for Boat Component Design
Advanced techniques in boat component design involve a deeper understanding of performance optimization and functionality. These techniques include leveraging simulation tools to analyze stress, buoyancy, and hydrodynamics for various components like the hull and propulsion systems. Designers also focus on precision material selection, ensuring durability, corrosion resistance, and weight efficiency. Integrating modular design principles helps in creating adaptable and repairable components, enhancing longevity. Advanced modeling tools in SolidWorks, like the Surface and Sheet Metal features, are often used to create intricate geometries. These approaches enable marine engineers to design innovative and high-performing components tailored for specific operational requirements.
Integrating Propulsion Systems
Propulsion systems are critical for movement. Here’s how to design them:
- Propeller Design:
- Sketch a blade profile using the Loft Tool to create smooth transitions.
- Define blade angles and curvature to optimize thrust.
- Shaft Design:
- Use Revolve to create cylindrical shafts.
- Ensure dimensions accommodate engine specifications.
- Assembly:
- Combine components in an Assembly File, testing for clearances and alignments.
Simulating Propulsion Systems
- Apply the Motion Study Tool to simulate rotational movement and ensure smooth operation.
- Use Material Analysis to confirm the components can handle operational stresses.
Designing Deck Fittings
Deck fittings like cleats and hatches enhance functionality.
- Cleats:
- Use the Sweep Tool to create rounded profiles.
- Ensure they can withstand tensile forces from ropes.
- Hatches:
- Design frames with the Extrude Tool.
- Use the Mate Tool to test the hatch’s opening and closing mechanism.
Attention to detail in these designs ensures usability and safety.
Tips for Optimizing SolidWorks Designs
Optimizing designs in SolidWorks involves leveraging its advanced features to enhance efficiency and accuracy. Utilize the Design Library for reusable components and the Mass Properties Tool to ensure proper weight distribution and balance. Configurations allow for easy comparison of design variations, while simulation tools help validate performance under real-world conditions. Regularly refine your model by addressing material selection, structural stability, and hydrodynamic performance. By combining creativity with SolidWorks’ capabilities, you can create robust and functional marine engineering designs.
Efficient Use of SolidWorks Tools
- Design Library: Utilize pre-made components to save time.
- Configurations: Create multiple design variations for comparison.
- Mass Properties Tool: Calculate weight and center of gravity to validate stability.
Debugging and Refinement
- Regularly check for interference in assemblies.
- Use the Feature Manager to adjust parameters without starting over.
- Leverage simulation results to refine designs iteratively.
Conclusion
Mastering SolidWorks is an essential skill for marine engineering students tasked with designing boat components. By grasping the principles of boat design and utilizing the powerful features of SolidWorks, students can create innovative and efficient solutions for various marine challenges. The software’s advanced tools for 3D modeling, simulation, and analysis make it ideal for tackling complex assignments.
This guide has highlighted key steps, from sketching and refining hull shapes to designing propulsion systems and deck fittings, all while considering crucial factors like hydrodynamics, material selection, and structural integrity. With practice and attention to technical details, students can produce realistic and high-performance designs that meet assignment requirements.
SolidWorks provides a comprehensive platform for turning ideas into functional marine components, making it a valuable asset in the field. Embrace its capabilities to enhance your skills and excel in your marine engineering assignments with confidence.