- Understanding the Essence of Finite Element Analysis
- The Role of SolidWorks in FEA
- Tips for Mastering Finite Element Analysis with SolidWorks
- 1. Mastering the Basics: Building a Strong Foundation
- 2. Efficient Geometry Creation and Cleanup
- 3. Material Properties and Meshing Strategies
- 4. Boundary Conditions and Constraints
- 5. Result Interpretation and Validation
- Conclusion
Mastering Finite Element Analysis (FEA) is a pivotal skill for engineers seeking to ensure the structural integrity and performance of their designs, and SolidWorks stands as an indispensable ally in this endeavor. In the realm of engineering simulation, "Mastering Finite Element Analysis with SolidWorks: Tips for Your Assignments" serves as a guiding beacon for those navigating the complexities of structural analysis. This comprehensive guide is tailored to empower SolidWorks users, from novices to seasoned professionals, with practical insights and strategies to elevate their FEA proficiency. As we unravel the intricacies of this dynamic duo – SolidWorks and Finite Element Analysis – readers will gain valuable tips that extend beyond the conventional boundaries of simulation, providing a holistic approach to addressing real-world engineering challenges. Whether you're a student seeking help with your finite element analysis assignment or a professional looking to enhance your skills, this guide is designed to support your journey.
Embarking on a journey through the nuances of geometry creation, material assignment, meshing strategies, and result interpretation, this blog serves as a roadmap for success in FEA assignments. From the fundamental principles of accurate model representation to advanced techniques in post-processing and result validation, each section offers actionable advice that bridges the gap between theoretical knowledge and practical application. Whether you are an engineering student working on assignments or a seasoned professional aiming to enhance your simulation capabilities, "Mastering Finite Element Analysis with SolidWorks" is your comprehensive guide to unlocking the full potential of structural analysis within the SolidWorks
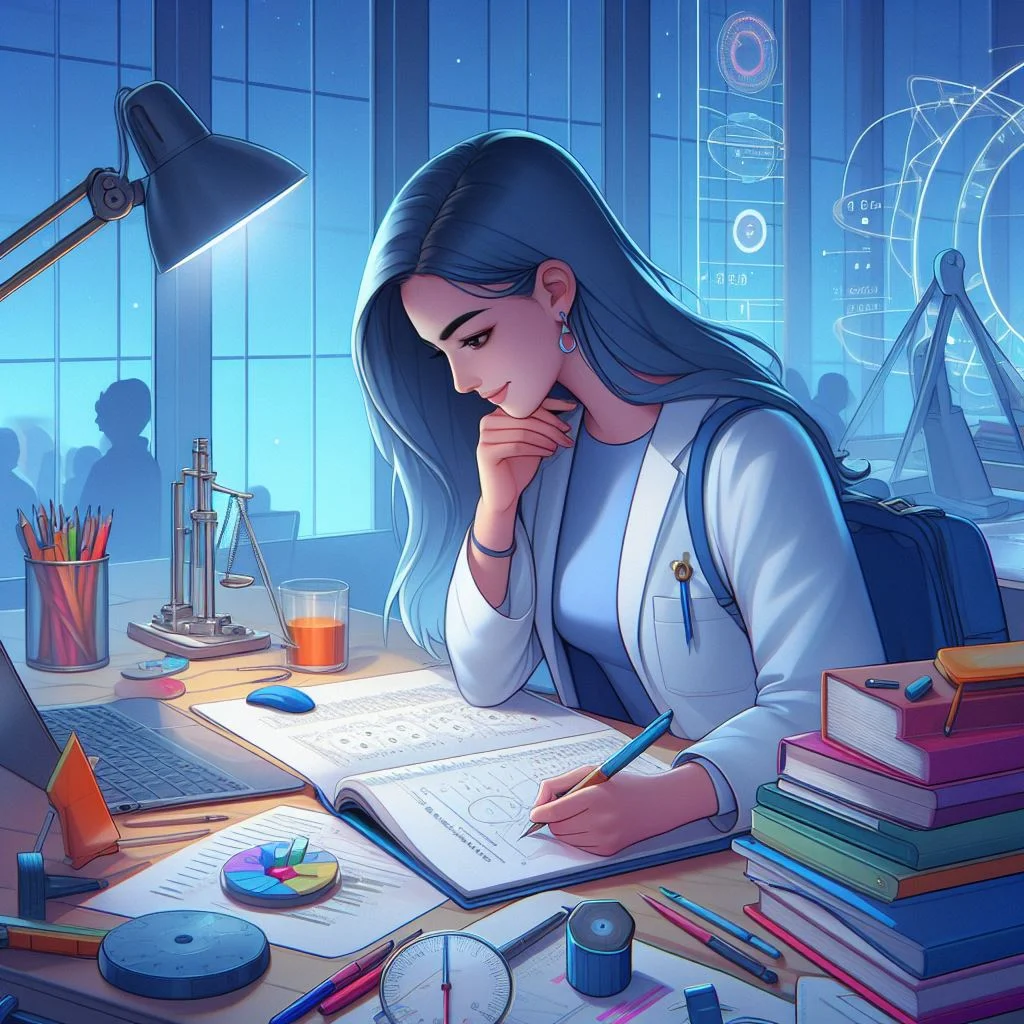
Understanding the Essence of Finite Element Analysis
In the realm of engineering and scientific simulations, Finite Element Analysis (FEA) stands as a pivotal technique, wielding immense power in unraveling the intricacies of complex structures and systems. At its essence, FEA is a numerical method employed to approximate and analyze the behavior of physical systems under various conditions. By discretizing a complex geometry into finite elements, FEA allows engineers and researchers to model the intricate interactions between different components, materials, and forces. The method has found extensive applications across diverse fields such as structural mechanics, heat transfer, fluid dynamics, and electromagnetics, offering a versatile toolset for understanding and optimizing designs. Through the meticulous application of mathematical principles and computational algorithms, FEA provides engineers with invaluable insights into how structures respond to external stimuli, enabling them to refine and innovate designs with a profound understanding of their performance under real-world conditions.
Delving deeper, the essence of Finite Element Analysis lies in its ability to bridge the gap between theoretical abstraction and practical engineering challenges. As engineers grapple with the complexities of modern design, FEA serves as a virtual laboratory, offering a controlled environment to predict and analyze the behavior of structures subjected to a myriad of loading conditions. The technique empowers designers to iterate rapidly, assess multiple design alternatives, and make informed decisions based on quantitative data. Understanding the nuances of FEA involves not only grasping the underlying mathematical and computational principles but also appreciating its transformative impact on the design process. As industries strive for innovation and efficiency, a profound comprehension of FEA becomes not just a technical skill but a strategic asset in the pursuit of robust and optimized engineering solutions.
The Role of SolidWorks in FEA
SolidWorks plays a pivotal role in Finite Element Analysis (FEA), serving as a robust and versatile tool for engineers and designers. FEA is a computational technique used to analyze and simulate the behavior of structures under various conditions. In the realm of mechanical engineering, SolidWorks stands out as a leading software for its seamless integration with FEA workflows. Engineers leverage SolidWorks to create intricate 3D models of components and assemblies, which can then be imported into FEA simulations. The software's intuitive interface allows users to define material properties, boundary conditions, and loads with precision, providing a comprehensive understanding of how a design will perform under real-world conditions.
Furthermore, SolidWorks facilitates efficient mesh generation, a critical step in FEA that involves dividing the model into small elements to accurately represent its geometry. The software's advanced meshing capabilities ensure a balance between computational accuracy and efficiency. Engineers can analyze stress, strain, and deformation in a virtual environment, enabling them to optimize designs, identify potential weaknesses, and iterate rapidly. SolidWorks' integration with FEA empowers engineers to make informed decisions early in the design process, reducing the need for costly physical prototypes and accelerating product development cycles. In essence, SolidWorks plays an indispensable role in enhancing the accuracy, efficiency, and reliability of FEA simulations, making it an invaluable tool for engineers seeking to design robust and optimized structures.
Tips for Mastering Finite Element Analysis with SolidWorks
Embarking on the journey to master Finite Element Analysis (FEA) within SolidWorks demands a strategic approach and a keen understanding of the software's capabilities. As you delve into the intricacies of structural simulation, consider these indispensable tips to elevate your proficiency. Firstly, focus on mastering the basics by building a strong foundation in 3D modeling, material assignment, and boundary condition definition. Efficient geometry creation and cleanup are pivotal; utilize parametric modeling and thorough geometry checks to ensure accuracy. Secondly, delve into material properties and meshing strategies, understanding the significance of accurate material assignment and adopting effective meshing practices. Thirdly, pay meticulous attention to boundary conditions and constraints, mimicking real-world scenarios for comprehensive simulations. Lastly, prioritize result interpretation and validation through SolidWorks' post-processing tools, ensuring your FEA outcomes align with practical engineering expectations. By incorporating these tips into your workflow, you'll navigate the complexities of SolidWorks FEA with confidence and precision.
1. Mastering the Basics: Building a Strong Foundation
In the realm of Finite Element Analysis (FEA) with SolidWorks, laying a robust foundation is the first crucial step toward mastery. A strong grasp of the basics is akin to constructing a sturdy framework for a building—every subsequent analysis relies on the integrity of this groundwork. Begin by immersing yourself in SolidWorks' fundamental features, from creating precise 3D models to understanding the nuances of assigning materials. Embrace the power of parametric modeling to easily tweak dimensions and use SolidWorks' versatile sketching tools for accuracy. Regularly engage with the wealth of tutorials and documentation provided by SolidWorks, ensuring that your knowledge of the basics evolves in tandem with the software's capabilities. Remember, proficiency in the fundamentals is the key to navigating the complexities of Finite Element Analysis and unlocking the full potential of SolidWorks as your analytical tool of choice.
2. Efficient Geometry Creation and Cleanup
In the realm of Finite Element Analysis, the efficiency of your simulation heavily relies on the accuracy of the geometry you create and the meticulousness with which you clean it up. SolidWorks provides a robust platform for 3D modeling, and mastering the art of efficient geometry creation is paramount. Leverage the power of parametric modeling to effortlessly modify dimensions and adapt your design iteratively. The sketching tools offered by SolidWorks are invaluable for achieving precision in your geometry. To ensure a seamless simulation, pay close attention to detail by incorporating fillets and chamfers judiciously. Regularly scrutinize your model for any geometry errors, employing SolidWorks' error-checking features to nip potential simulation issues in the bud. A well-crafted and refined geometry is the cornerstone of an accurate Finite Element Analysis, making the upfront investment in efficient creation and cleanup an indispensable step in your engineering workflow.
1. Tips for Efficient Geometry Creation
- Utilize parametric modeling to easily modify dimensions.
- Take advantage of SolidWorks' sketching tools for precise geometry.
- Regularly check and fix any geometry errors to prevent simulation issues.
3. Material Properties and Meshing Strategies
When it comes to Finite Element Analysis (FEA) in SolidWorks, the meticulous assignment of material properties and the strategic application of meshing techniques play pivotal roles in the accuracy of simulations. The selection and characterization of materials are not mere checkboxes but critical decisions that can profoundly influence simulation outcomes. It's imperative to delve into SolidWorks' extensive material library, grasp the nuances of custom material creation, and align material properties with the real-world behavior of your design. Additionally, the art of meshing cannot be overstated. Meshing strategies impact computational efficiency and the precision of results. Choosing the appropriate mesh type and refining it judiciously based on geometry intricacies are indispensable steps. In this realm, precision and computational efficiency coalesce to form the foundation of a robust Finite Element Analysis, ensuring your SolidWorks simulations mirror reality with accuracy and reliability.
1. Optimizing Material Assignment
- Understand the material selection for specific engineering applications.
- Validate material properties using external references and material databases.
- Regularly update material properties to reflect changes in the design.
2. Meshing Best Practices
- Choose an appropriate mesh type (tetrahedral, hexahedral, etc.) based on the geometry.
- Refine the mesh in critical areas to capture details without sacrificing computational efficiency.
- Perform mesh sensitivity analyses to ensure the reliability of results.
4. Boundary Conditions and Constraints
In the realm of Finite Element Analysis (FEA) using SolidWorks, the accurate application of boundary conditions and constraints is paramount to achieving meaningful simulation results. Think of boundary conditions as the set of rules that govern how your structure interacts with its environment. SolidWorks offers a versatile array of options for defining constraints, including fixed geometry, roller/slider supports, and prescribed displacements. It's crucial to choose constraints that closely mimic the real-world scenario your design will encounter, ensuring the simulation accurately represents the physical behavior of the structure. Applying symmetry and simplification techniques judiciously not only reduces computational complexity but also facilitates a more efficient analysis process. In essence, mastering the intricacies of boundary conditions and constraints in SolidWorks FEA empowers engineers to create simulations that align closely with the complexities of actual structural performance, paving the way for more accurate and insightful engineering assessments.
1. Essential Boundary Condition Tips
- Apply constraints that mimic the physical environment of the structure.
- Use symmetry and simplification to reduce computational complexity.
- Verify boundary conditions through manual calculations for validation.
5. Result Interpretation and Validation
In the realm of scientific inquiry, the interpretation and validation of results hold paramount importance as they are pivotal in establishing the credibility and reliability of any study. In this context, delves into the intricate process of deciphering the obtained results, drawing meaningful insights, and ensuring their validity. The interpretation phase involves a meticulous examination of data patterns, statistical analyses, and relevant contextual factors. Researchers must navigate through the intricacies of their findings, considering potential biases, confounding variables, and alternative explanations. This nuanced approach not only enhances the depth of understanding but also fosters a more comprehensive and accurate portrayal of the phenomena under investigation.
Validation, the second facet , serves as the litmus test for the robustness of the obtained results. Rigorous validation methodologies, ranging from statistical techniques to independent replication, are employed to corroborate the study's outcomes. This process ensures that the observed effects are not mere statistical artifacts but genuine reflections of the underlying phenomena. Moreover, validation serves as a means to enhance the generalizability of findings, offering confidence in the applicability of results beyond the specific sample or experimental conditions. By meticulously navigating the terrain of result interpretation and validation, contributes to the establishment of a solid foundation upon which subsequent scientific discourse and practical applications can be built.
1. Post-Processing Strategies
- Utilize contour plots, stress plots, and deformation plots to visualize results.
- Validate FEA results through hand calculations and theoretical analysis.
- Consider conducting sensitivity analyses to assess the impact of changes.
Conclusion
Mastering Finite Element Analysis with SolidWorks requires a combination of theoretical knowledge, practical skills, and a deep understanding of the software's capabilities. By following the tips outlined in this guide, you can enhance your proficiency in using SolidWorks for FEA, ultimately leading to more accurate and reliable engineering simulations. As you continue to explore the world of FEA, remember that continuous learning and hands-on practice are key to becoming a proficient user of this powerful tool.