- Understanding Oxford's Motion Analysis Framework
- Theoretical Foundations of Oxford's Motion Analysis
- Key Components and Terminology
- Setting the Stage: Preparing Your SolidWorks Environment
- Configuring SolidWorks for Motion Analysis
- Best Practices in SolidWorks Environment Setup
- Building SolidWorks Motion Studies
- Defining Kinematic Joints in SolidWorks
- Motor Specification Techniques
- Advanced Motion Analysis Tools in SolidWorks
- Force and Torque Analysis in SolidWorks
- Dynamic Simulation Techniques
- Optimizing Performance: Tips for Efficient Motion Analysis
- Simulation Time Reduction Strategies
- Workflow Enhancements in SolidWorks Motion Analysis
- Conclusion:
Motion analysis stands as a cornerstone in the realm of engineering design, serving as the bridge between theoretical concepts and real-world applications. The ability to simulate and analyze the movement of mechanical systems is a skill that can elevate an engineer's proficiency to new heights. Amidst the myriad of tools available, SolidWorks emerges as a powerhouse in this arena, offering a robust platform for motion analysis. However, within the vast landscape of SolidWorks capabilities, mastering Oxford's Motion Analysis concepts introduces engineers to a distinctive set of challenges and opportunities. If you need help with your motion analysis assignment, understanding and applying these concepts within the SolidWorks environment becomes crucial. This article aims to guide engineers through the intricacies of motion analysis, providing insights and strategies to navigate Oxford's Motion Analysis concepts effectively. By delving into the specifics of SolidWorks and its motion analysis capabilities, this resource seeks to empower engineers to tackle their assignments with confidence, ensuring a comprehensive understanding of both theoretical principles and practical applications.
The journey into mastering Oxford's Motion Analysis in SolidWorks is akin to navigating uncharted territory, where each principle and technique acts as a compass guiding engineers through the complexities of dynamic simulations. Oxford's Motion Analysis concepts add a layer of sophistication to the process, emphasizing a nuanced understanding of mechanical systems' behavior. This mastery goes beyond mere technical prowess; it requires a holistic approach that blends theoretical knowledge with practical application, ensuring that engineers can not only simulate but also interpret and optimize motion scenarios effectively.
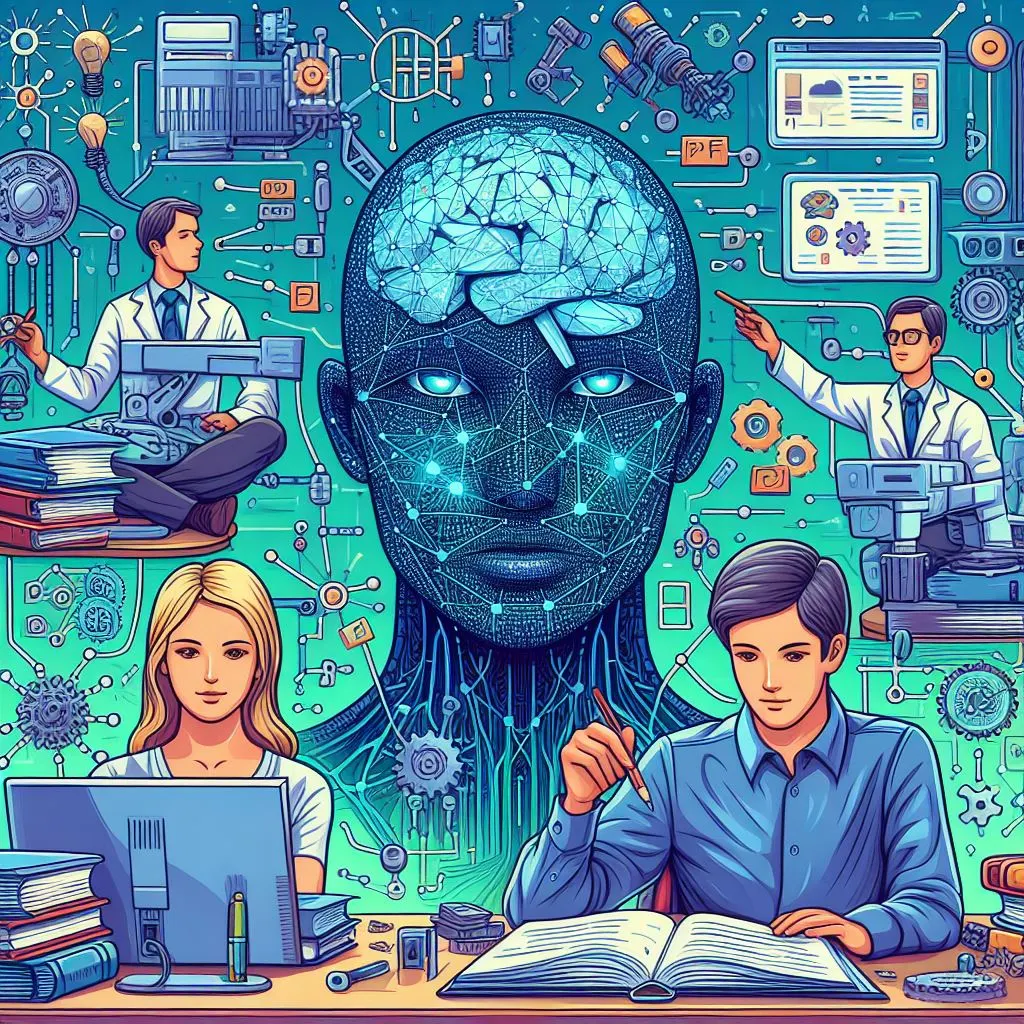
As we embark on this exploration, it becomes evident that Oxford's Motion Analysis is more than a series of steps or commands within SolidWorks; it's a framework that opens the door to a deeper comprehension of kinematics, dynamics, and the interplay of forces in mechanical systems. These concepts lay the groundwork for engineers to tackle a diverse range of projects, from designing cutting-edge robotics to optimizing the performance of complex machinery in industrial settings.
The complexity of motion analysis is magnified when considered within the context of SolidWorks, a tool celebrated for its versatility and depth. This blog serves as a beacon, guiding engineers through the intricacies of Oxford's Motion Analysis Concepts in SolidWorks. From the initial setup of motion studies to the integration with advanced simulation tools, each section of this guide is crafted to empower engineers with the knowledge and confidence needed to navigate and excel in this specialized domain.
In essence, the title "Mastering Oxford's Motion Analysis Concepts in SolidWorks" encapsulates the essence of this comprehensive guide. It signifies more than just acquiring a skill; it denotes a journey towards mastery, a progression from understanding the basics to confidently applying advanced concepts. As we unravel the layers of SolidWorks motion analysis, it becomes apparent that this journey is not a solitary endeavor; it's a collective exploration undertaken by engineers worldwide who share a common passion for precision, innovation, and excellence in engineering design.
The chapters that follow delve into the specifics, offering insights into the theoretical foundations, practical applications, and real-world implications of mastering Oxford's Motion Analysis in SolidWorks. Let's navigate this exciting terrain together, where challenges are transformed into stepping stones, and each lesson learned brings us closer to the pinnacle of motion analysis proficiency.
Understanding Oxford's Motion Analysis Framework
Oxford's Motion Analysis framework is a robust and holistic approach to dissecting the intricate dance of mechanical systems. At its core, this framework operates on the principles of kinematics and dynamics, unraveling the complex relationships governing motion. The foundation lies in comprehending the interplay of forces, torques, and constraints that orchestrate the graceful, or sometimes erratic, movements of mechanical components.
A cornerstone of Oxford's approach is its emphasis on real-world accuracy. This means transcending the realm of mere simulations and aligning virtual models with the physical laws that govern the tangible world. By incorporating principles of physics and mathematics, Oxford's Motion Analysis provides engineers with a nuanced understanding of how mechanical systems behave under diverse conditions.
Before immersing ourselves in the application of these principles within the SolidWorks environment, it's imperative to recognize the significance of precision in motion analysis. Oxford's framework encourages engineers to think beyond idealized scenarios, considering the nuanced effects of friction, material properties, and external influences. This holistic perspective forms the bedrock for an effective application of motion analysis in the context of SolidWorks simulations.
Understanding the intricacies of Oxford's Motion Analysis Framework prepares us to embark on a journey where virtual prototypes seamlessly mirror the behavior of their real-world counterparts. It's a mindset shift from traditional simulation towards a more encompassing analysis that aligns theoretical underpinnings with practical applications, setting the stage for a comprehensive exploration of motion studies in SolidWorks.
Theoretical Foundations of Oxford's Motion Analysis
Delving into the theoretical foundations of Oxford's Motion Analysis is akin to unlocking the intellectual framework that propels the entire field forward. At its core, Oxford's approach is grounded in the principles of classical mechanics, with a keen emphasis on mathematical precision. Concepts such as Newtonian physics and Lagrangian mechanics serve as the bedrock, providing engineers with a robust foundation to analyze and simulate mechanical systems accurately.
Understanding the theoretical underpinnings involves grasping the intricacies of kinematics and dynamics, unraveling the mathematical expressions that describe the motion of interconnected components. This theoretical depth is not just an academic exercise; it forms the cornerstone for translating real-world mechanical phenomena into the virtual realm of SolidWorks.
Key Components and Terminology
Delving into the theoretical foundations of Oxford's Motion Analysis is akin to unlocking the intellectual framework that propels the entire field forward. At its core, Oxford's approach is grounded in the principles of classical mechanics, with a keen emphasis on mathematical precision. Concepts such as Newtonian physics and Lagrangian mechanics serve as the bedrock, providing engineers with a robust foundation to analyze and simulate mechanical systems accurately.
Understanding the theoretical underpinnings involves grasping the intricacies of kinematics and dynamics, unraveling the mathematical expressions that describe the motion of interconnected components. This theoretical depth is not just an academic exercise; it forms the cornerstone for translating real-world mechanical phenomena into the virtual realm of SolidWorks.
Setting the Stage: Preparing Your SolidWorks Environment
A proper setup is the foundation for successful motion analysis. Explore the necessary configurations and settings in SolidWorks to ensure accurate simulations and realistic results.
A well-prepared SolidWorks environment is fundamental to the success of motion analysis endeavors. As you embark on the journey of simulating dynamic mechanical systems, the initial configuration of your SolidWorks workspace becomes the bedrock upon which accurate and reliable simulations are built.
Begin by immersing yourself in the realm of SolidWorks configurations, tailoring the software to the specific requirements of motion analysis. Carefully calibrate settings to establish a virtual environment that mirrors real-world conditions with precision. This meticulous setup ensures that the simulations generated will provide insights that align seamlessly with physical reality.
Consider the nuances of your project as you navigate through SolidWorks configurations. Tailor parameters such as gravity, material properties, and contact interactions to mimic the behavior of your mechanical system authentically. Each adjustment made within the SolidWorks environment serves as a building block, contributing to the overall accuracy and reliability of the ensuing motion analysis.
Moreover, pay meticulous attention to the intricacies of mates and constraints, as these dictate the degrees of freedom within your assembly. A judicious selection and application of mates pave the way for a well-defined and controlled motion study. In essence, the SolidWorks environment becomes your canvas, and the configurations are the brushstrokes that bring your virtual designs to life in a dynamic, simulated space.
As you navigate through the configurations and settings in SolidWorks, envision the impact each adjustment will have on the outcome of your motion analysis. This foresight, coupled with a thorough understanding of the intricacies of the SolidWorks environment, positions you for success in creating motion studies that not only meet but exceed the expectations of accuracy and realism. In this realm of preparation, attention to detail becomes your guiding principle, ensuring that your SolidWorks environment is not merely a stage but a dynamic, responsive partner in the exploration of motion analysis concepts.
Configuring SolidWorks for Motion Analysis
Configuring SolidWorks for motion analysis requires meticulous attention to detail. Start by navigating through the software settings, ensuring that the configurations align with the specific requirements of motion studies. This involves setting up key parameters such as time increments, solver options, and contact settings. The importance of a well-tailored configuration cannot be overstated, as it forms the backbone of accurate and reliable motion simulations.
Beyond the basic configurations, delve into the intricacies of specifying material properties and defining contact interactions. Understanding the nuances of these settings is crucial for capturing realistic behavior in motion studies. This section provides step-by-step instructions, demystifying the configuration process and empowering you to create motion analyses that reflect real-world scenarios with precision.
Best Practices in SolidWorks Environment Setup
Efficient environment setup is essential for optimizing hardware resources and ensuring a fluid motion analysis workflow. Explore the best practices for configuring hardware settings to harness the full potential of your computing resources. This includes considerations for graphics cards, processors, and memory allocation, allowing you to strike the right balance between performance and accuracy.
Workspace organization plays a pivotal role in maintaining clarity and efficiency throughout the motion analysis process. Learn how to structure your workspace, arrange components, and streamline the overall environment for enhanced productivity. This section goes beyond the technical configurations, providing insights into creating an ergonomic and intuitive workspace tailored to the demands of motion analysis.
In summary, configuring SolidWorks for motion analysis involves more than just adjusting settings; it's about crafting an environment that fosters precision, efficiency, and a seamless workflow. By mastering these configurations and adhering to best practices, you lay the groundwork for successful motion studies that stand up to the complexities of real-world engineering challenges.
Building SolidWorks Motion Studies
Creating motion studies in SolidWorks is a critical skill that requires a systematic approach. Begin by defining mates to establish relationships between components, allowing them to move as intended. Specify motors to introduce forces and drive the motion, simulating real-world conditions accurately. Setting up contact interactions is crucial to mimicking the physical constraints and interactions that components may face during operation.
Understanding the step-by-step process is fundamental. Defining mates involves selecting appropriate constraints, ensuring components move realistically while maintaining the integrity of the assembly. Specifying motors adds the dynamic element, enabling the simulation of forces and motion over time. Additionally, setting up contact interactions is vital for capturing the effects of collisions and interactions between components.
SolidWorks provides a user-friendly interface for executing each of these steps, making the creation of motion studies accessible even to those new to the software. As you embark on this journey, experimentation and iteration are key. Fine-tune your parameters, observe the results, and refine your approach to achieve the desired motion behavior.
By mastering the intricacies of building SolidWorks motion studies, you lay a solid foundation for accurate simulations, paving the way for a more profound understanding of mechanical systems in motion.
Defining Kinematic Joints in SolidWorks
In the realm of SolidWorks, defining kinematic joints is akin to setting the stage for a dynamic performance. SolidWorks offers a diverse array of kinematic joints, each serving a specific purpose in replicating real-world mechanical connections. From revolute joints that mimic rotational movements to prismatic joints facilitating linear motion, understanding the nuances of these joints is essential for accurate representation. Dive deep into the various kinematic joints available in SolidWorks, exploring their applications and learning how to leverage them effectively to bring your designs to life.
Motor Specification Techniques
When it comes to motion studies in SolidWorks, the heartbeat of dynamic simulations lies in motor specification. Detailed insights into specifying motors go beyond the basic mechanics – it involves the art of applying forces and torques strategically. Uncover the intricacies of this art, gaining a profound understanding of how to simulate realistic motion scenarios. Whether it's replicating the nuanced rotations of a complex mechanism or mimicking the force dynamics in a robotic arm, mastering motor specification techniques is your gateway to unlocking the true potential of SolidWorks for motion analysis.
Advanced Motion Analysis Tools in SolidWorks
SolidWorks, as a powerful engineering tool, goes beyond the basics, offering a myriad of tools to dissect and understand motion intricacies. One such feature is force analysis, a tool that provides insight into the impact of external forces on your system. By leveraging force analysis, engineers can anticipate and mitigate potential design flaws, ensuring robust performance under diverse conditions.
Additionally, torque analysis in SolidWorks elevates your motion analysis capabilities by scrutinizing the effects of torques on components within a system. This is invaluable for designing machinery where torque dynamics are critical, allowing engineers to optimize for efficiency and durability.
Dynamic simulation takes the analysis a step further, enabling the exploration of system behavior over time. It facilitates the observation of how components interact under dynamic conditions, uncovering nuances that may remain hidden in static analyses. Engineers can refine their designs, accounting for real-world scenarios and enhancing the reliability of their systems.
Force and Torque Analysis in SolidWorks
Unlock the capabilities of SolidWorks for in-depth force and torque analysis, enhancing the accuracy of your motion simulations. SolidWorks provides a robust set of tools for dissecting forces and torques acting on your mechanical systems. By precisely defining and analyzing these forces, engineers gain insights into the intricate interactions within their designs. This level of detail is invaluable in optimizing components for performance, durability, and efficiency. Whether you are designing machinery or evaluating the structural integrity of a product, SolidWorks' force and torque analysis tools empower you to make informed decisions, elevating the quality of your motion studies.
Dynamic Simulation Techniques
Delve into dynamic simulation tools within SolidWorks, exploring their applications and benefits for comprehensive motion analysis. Dynamic simulation goes beyond static studies, accounting for the effects of time, inertia, and acceleration on your mechanical systems. SolidWorks provides a dynamic simulation environment where you can simulate realistic movements, reactions to external forces, and dynamic loading scenarios. By delving into dynamic simulation techniques, you open doors to a more accurate representation of real-world conditions. This level of sophistication allows you to uncover nuances in your designs, ensuring that they not only function correctly but also withstand the dynamic forces they may encounter during operation.
Optimizing Performance: Tips for Efficient Motion Analysis
Efficiency lies at the heart of successful motion analysis projects in SolidWorks. As you embark on the intricacies of complex simulations, it's crucial to implement strategies that not only optimize performance but also streamline your workflow. SolidWorks offers a robust platform, and with the right techniques, you can significantly enhance the efficiency of your motion analyses.
One key aspect of optimizing performance is understanding the intricacies of SolidWorks settings. Take time to explore and fine-tune configurations that align with the specific requirements of your project. Adjusting parameters such as time-step and accuracy settings can have a profound impact on simulation time without compromising the fidelity of results.
Additionally, consider leveraging the power of hardware. As technology advances, ensuring your hardware is up to par can greatly contribute to the speed and accuracy of motion analyses. Investing in a system with ample processing power and graphic capabilities can substantially reduce computation times, allowing for smoother simulations.
Furthermore, strategic simplification of models can significantly enhance efficiency. Identify non-essential components or features that do not contribute significantly to the analysis and temporarily exclude them from the simulation. This selective simplification not only expedites the analysis but also allows you to focus on the critical aspects of the motion.
Collaboration and knowledge sharing also play a pivotal role in optimization. Engage with the SolidWorks community to exchange insights and discover innovative approaches. Understanding how others tackle similar challenges can provide valuable shortcuts and perspectives, ultimately contributing to a more efficient workflow.
In conclusion, optimizing performance in SolidWorks motion analysis involves a multifaceted approach. By fine-tuning settings, leveraging hardware capabilities, strategically simplifying models, and actively participating in the SolidWorks community, you can unlock new levels of efficiency in your motion analysis projects. These tips, combined with a proactive mindset, will not only reduce simulation time but also enhance your overall proficiency in SolidWorks motion analysis.
Simulation Time Reduction Strategies
Practical strategies to reduce simulation time without compromising the accuracy of your motion analysis are essential for improving overall efficiency. One effective approach is the judicious use of simplifications in complex models. By strategically simplifying non-essential components or utilizing approximate methods for certain analyses, you can significantly cut down simulation times. Moreover, leveraging parallel processing capabilities and optimizing hardware configurations can further expedite simulations without sacrificing precision.
Workflow Enhancements in SolidWorks Motion Analysis
Exploring features and techniques within SolidWorks that streamline your workflow is paramount for saving time and increasing productivity. SolidWorks offers time-saving tools like motion templates, enabling the reuse of predefined motion scenarios across projects. Additionally, mastering keyboard shortcuts, utilizing design tables, and leveraging parametric modeling techniques contribute to a more seamless workflow. By incorporating these enhancements, you not only expedite the motion analysis process but also enhance the overall efficiency of your design workflow in SolidWorks.
Conclusion:
Mastering Oxford's Motion Analysis Concepts in SolidWorks is a journey of continuous learning and application. As you venture into the world of motion studies, remember that practical experience and experimentation are invaluable. Embrace challenges as opportunities to deepen your understanding and refine your skills.
Whether you are optimizing suspension systems in the automotive industry or simulating complex mechanisms in aerospace, SolidWorks provides a robust platform for comprehensive motion analysis. The integration of Oxford's Motion Analysis concepts with SolidWorks Simulation offers a powerful toolkit for engineers seeking precision and efficiency in their designs.
As you apply the knowledge gained from this guide, consider sharing your experiences and insights with the SolidWorks community. Engaging with peers, participating in forums, and continuing your education will further enrich your expertise.
In conclusion, mastering motion analysis in SolidWorks is not just about achieving proficiency with the software; it's about transforming challenges into opportunities for growth and innovation. Armed with the insights from this guide, go forth and confidently tackle Oxford's Motion Analysis Concepts, pushing the boundaries of what is possible in the dynamic world of engineering design.