- Understanding SolidWorks Surface Modeling
- Creating Basic Surface Features
- Advanced Surface Manipulation
- Surface Editing and Modification
- 1. Trimming Surface: Precision Surface Modification
- 2. Mid Surface: Bridging the Gap
- 3. Replace Face: Selective Surface Modification
- 4. Delete Face: Precision Removal
- 5. Untrim Surface: Reversing Surface Modification
- 6. Knit Surface: Creating Watertight Models
- Thickening Surfaces and Face Manipulation
- 1. Thickening a Surface: Transforming Surfaces into Solids
- 2. Move Face: Precise Face Manipulation
- Conclusion
SolidWorks is a powerful and versatile computer-aided design (CAD) software widely used in the engineering and design industry. It offers an array of features and tools to help professionals and students bring their design ideas to life. One crucial aspect of SolidWorks that every user should be well-versed in is surface modeling. Surface modeling allows you to create complex, curved, and organic shapes, which can be particularly useful in various design projects.
In this extensive guide, we'll delve into the world of SolidWorks surface modeling tools. We'll explore the fundamentals of creating surfaces, modifying them, and applying various techniques to enhance your 3D modeling skills. Whether you're a student looking to excel in your Surface Modeling assignments or a professional seeking to broaden your design capabilities, this guide will serve as a valuable resource.
Understanding SolidWorks Surface Modeling
Before we jump into the specifics of surface modeling, let's first understand what it is and why it's essential. Surface modeling is the process of creating 3D shapes using surfaces rather than solids. This is particularly useful when working with complex, freeform shapes, and it's essential for tasks like industrial design, aerospace engineering, and automotive design.
In SolidWorks, surface modeling allows you to create intricate, smooth, and continuous shapes that are challenging to achieve using solid modeling techniques. This chapter will cover the basic concepts of surface modeling and provide insights into when to use surface modeling over solid modeling.
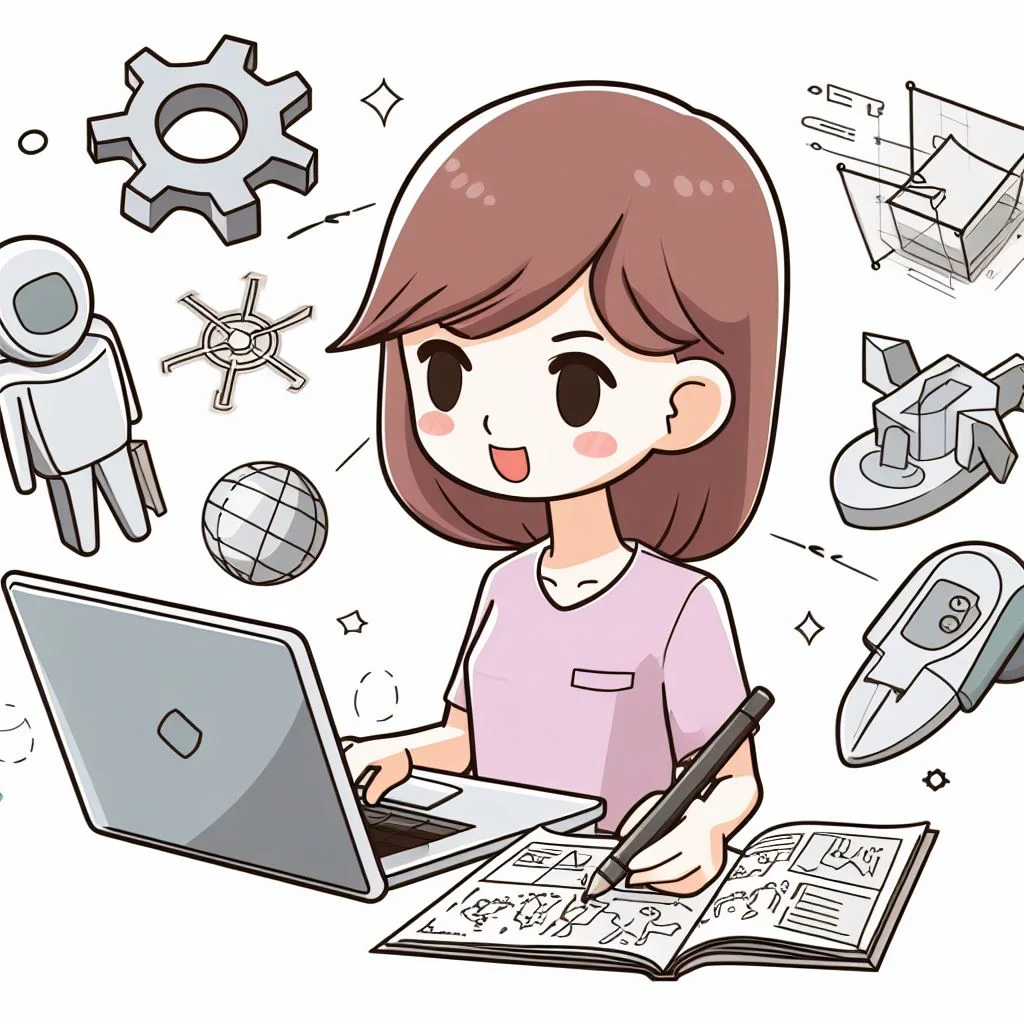
Creating Basic Surface Features
Now that we have a good grasp of the fundamentals, let's dive into creating surface features using SolidWorks. We'll explore various tools such as Extrude, Revolve, Swept, Loft, and Boundary Surface to generate different types of surface geometry.
- Extrude Surface: Extruding a surface is similar to extruding a solid, but instead of creating a volume, it generates a surface. You can control the direction and depth of the extrusion.
- Revolve Surface: Revolve surface allows you to create surfaces by revolving a 2D sketch profile around an axis. This is useful for creating cylindrical and conical surfaces.
- Swept Surface: Swept surface involves creating a surface by sweeping a 2D sketch profile along a path. This tool is handy for creating complex shapes.
- Lofted Surface: Lofted surfaces are generated by blending between two or more profile sketches. This is perfect for creating smooth transitions between shapes.
- Boundary Surface: Boundary surface enables you to create surfaces between multiple boundary curves. It's particularly useful for complex transitions and patching.
Advanced Surface Manipulation
Once you've mastered the basics, it's time to move on to more advanced techniques. In this chapter, we'll explore tools for manipulating existing surfaces and creating additional features to enhance your designs.
- Inserting Planar Surface: Sometimes, you may need to insert a flat surface within a complex design. SolidWorks allows you to insert planar surfaces to create flat regions in your model.
- Offset Surface: Offset surface is used to create a new surface parallel to an existing one, with a specified offset distance. It's an excellent tool for designing components with consistent thickness.
- Radiate Surface: Radiate surface is a feature used to create surfaces that radiate from a single point or curve, spreading outwards like spokes on a wheel.
- Extending a Surface: This tool allows you to extend an existing surface to meet other surfaces or geometry, ensuring continuity and smooth transitions.
- Surface Fill: Surface fill is used to fill gaps between multiple surfaces or sketches, creating a seamless and continuous surface.
- Ruled Surface: Ruled surface generates a surface between two sketches or curves by creating a straight-line connection. It's a powerful tool for creating surfaces with well-defined linear patterns.
Surface Editing and Modification
Surface modeling often involves iterative design processes. In this chapter, we'll explore various tools and techniques for editing and modifying existing surfaces to refine your models.
1. Trimming Surface: Precision Surface Modification
Trimming surfaces is an essential tool for refining your 3D models, as it allows you to cut, extend, or adjust the shape of a surface to meet the desired design requirements. SolidWorks offers a range of robust trimming tools to help you achieve this. Trimming surfaces can be especially useful when working with complex and intricate designs that require precise modifications.
Common use cases for trimming surfaces include:
- Modifying complex shapes: Trim away unwanted surface portions to achieve the exact shape you need.
- Creating blends: Trimming surfaces is vital for creating smooth transitions or blends between different surfaces.
- Intersection surfaces: When surfaces intersect, trimming ensures a clean and precise intersection.
2. Mid Surface: Bridging the Gap
A mid-surface is a special surface that sits exactly between two existing surfaces. This technique is especially useful for designing thin-walled or shell structures where you need to maintain an even thickness throughout. The mid-surface serves as a bridge, providing a surface equidistant from the inner and outer surfaces of your model.
Key applications of mid-surfacing include:
- Shell structures: Mid-surfaces are indispensable when designing products with consistent wall thickness, such as plastic containers or sheet metal parts.
- Lightweight structures: In industries like aerospace, mid-surfaces are essential for creating lightweight and structurally efficient components.
3. Replace Face: Selective Surface Modification
The "Replace Face" tool in SolidWorks is a handy feature that allows you to replace an existing face with another surface or sketch. This can be extremely beneficial when you need to make modifications to your model without altering the entire design. It's particularly useful for maintaining design intent while adjusting specific areas.
Common scenarios where you might use the Replace Face tool include:
- Design updates: When a part of your design needs modification or a different appearance.
- Model optimization: Swapping out complex surfaces for simplified ones.
- Maintaining model integrity: Keeping features like fillets or chamfers consistent across the model.
4. Delete Face: Precision Removal
There are instances when you want to remove a specific face from a surface, but you need to ensure the surrounding surfaces remain intact and continuous. The "Delete Face" tool is perfect for such situations. It allows you to remove unwanted faces without compromising the integrity of your model.
Use cases for the Delete Face tool include:
- Cleanup: Eliminating unnecessary surface elements or features that are not needed in the final design.
- Detail adjustments: Making localized changes to your model without affecting the overall structure.
- Model simplification: Reducing the complexity of a model while preserving its essential features.
5. Untrim Surface: Reversing Surface Modification
In some cases, you might need to reverse the effect of a previous trim operation. The "Untrim Surface" tool lets you recover portions of a surface that were previously trimmed away. This can be invaluable for design iterations or changes in your project requirements.
Common scenarios where you would use the Untrim Surface tool include:
- Design revisions: Restoring portions of your surface that were mistakenly trimmed.
- Restoring design intent: Reverting to a previous state of the model without re-creating it from scratch.
- Exploring design alternatives: Experimenting with different configurations of your model.
6. Knit Surface: Creating Watertight Models
Creating watertight, seamless models is crucial in design and engineering. The "Knit Surface" tool enables you to join multiple surfaces together, creating a single, continuous surface. This is particularly important for ensuring that your model is suitable for manufacturing, simulation, and rendering.
Key applications of the Knit Surface tool include:
- Assembly design: Joining various components to create an integrated, single surface.
- Preparation for analysis: Ensuring your model is ready for finite element analysis (FEA) and other simulations.
- Rendering and visualization: Achieving a flawless appearance in renders and presentations.
In conclusion, these advanced surface manipulation tools in SolidWorks are essential for achieving precision and flexibility in your 3D modeling endeavors. Whether you're working on complex design projects or seeking to fine-tune your models, these tools empower you to make targeted, controlled modifications, maintain model integrity, and ensure that your designs meet the highest standards of quality and functionality.
Thickening Surfaces and Face Manipulation
Thickening surfaces and manipulating faces are advanced techniques in SolidWorks surface modeling that offer users a high degree of control over their 3D designs. In this chapter, we will explore these techniques in detail and understand how they can be applied to enhance your designs.
1. Thickening a Surface: Transforming Surfaces into Solids
Thickening a surface is a fundamental step in transitioning from a surface model to a solid model. While surface models represent the external shape of an object, solid models encapsulate the interior and exterior volume of the object. This transformation is particularly valuable when designing components such as enclosures, casings, or any part that needs to enclose a volume.
To thicken a surface in SolidWorks, follow these steps:
- Select the surface you wish to thicken.
- bNavigate to the "Insert" menu and choose "Thicken" from the dropdown.
- Specify the desired thickness for the surface. You can either enter a numerical value or use the "Up to Surface" option to thicken the surface up to another selected surface.
- Click "OK" to complete the process.
Thickening a surface creates a solid model with defined thickness, ensuring the object's interior is enclosed. This transformation is essential for 3D printing, simulations, and manufacturing processes that require a complete, watertight volume representation.
Use Cases for Surface Thickening:
- Designing product enclosures, such as smartphone cases or electronic devices.
- Creating solid representations of complex, thin-walled structures like sheet metal components.
- Preparing models for finite element analysis (FEA) and simulations.
- Ensuring compatibility with various manufacturing methods, like CNC machining and 3D printing.
2. Move Face: Precise Face Manipulation
The "Move Face" tool in SolidWorks is a powerful feature that allows you to manipulate individual faces of a surface or solid model with precision. It's an essential tool for fine-tuning your design and making intricate adjustments without having to recreate the entire model.
Here's how to use the "Move Face" tool:
- Select the face you want to move within your model.
- Navigate to the "Direct Editing" toolbar and select "Move Face."
- In the "Move Face" property manager, you can specify the following parameters: - Translation: Move the selected face in a specific direction by defining a distance. - Rotation: Rotate the face around an axis. - Scaling: Resize the selected face proportionally.
- After configuring the desired changes, click "OK" to apply them.
Use Cases for Move Face:
- Adjusting draft angles and undercuts in a part for moldability.
- Correcting misalignments in assemblies by modifying faces for a better fit.
- Fine-tuning complex organic shapes or ergonomic designs.
- Iterative design adjustments without the need to reconstruct the entire model.
Combining Surface Thickening and Move Face:The combination of these two techniques is particularly powerful. For example, when designing a complex consumer product like a laptop, the initial model might be a surface-based representation to capture intricate design details. To prepare it for manufacturing, you can thicken the surfaces to create a solid model. Then, you can use the Move Face tool to make minute adjustments to the casing, ensuring that all components fit perfectly and that the aesthetic design remains intact.
Thickening surfaces and manipulating faces in SolidWorks are essential skills for anyone looking to create precise and manufacturable 3D models. The ability to transition from surface models to solid models through thickening surfaces is crucial for enclosing volumes and preparing designs for manufacturing and simulations. Meanwhile, the Move Face tool provides the flexibility to make fine adjustments without the need for extensive remodeling.
By mastering these advanced techniques, you can confidently tackle complex design projects, ensure compatibility with various production methods, and refine your models with the precision required for high-quality engineering and product design. These skills are valuable for both students working on SolidWorks assignments and professionals in the fields of mechanical engineering, product design, and industrial design.
Conclusion
SolidWorks surface modeling is a crucial skill for anyone involved in 3D design and engineering. This comprehensive guide has covered the essential tools and techniques required for creating, manipulating, and enhancing surfaces within SolidWorks. Whether you're a student looking to excel in your assignments or a professional aiming to broaden your design capabilities, the knowledge gained from this guide will undoubtedly help you achieve your goals.
Remember that surface modeling is a skill that improves with practice, so don't be discouraged if you don't master it immediately. Take the time to experiment and apply what you've learned in real-world projects to gain proficiency. SolidWorks is a powerful tool, and your ability to harness its surface modeling features can significantly impact the quality and complexity of your designs.