- Understanding the Importance of Thermal Analysis
- Common Thermal Analysis Challenges
- Introduction to SolidWorks Flow Simulation
- Key Features of SolidWorks Flow Simulation for Thermal Analysis
- Step-by-Step Guide to Solving Thermal Analysis Problems with SolidWorks Flow Simulation
- Step 1 - Model Geometry
- Step 2 - Define Material Properties
- Step 3 - Set Boundary Conditions
- Step 4 - Meshing
- Step 5 - Running the Simulation
- Step 6 - Post-Processing and Analysis
- Case Studies - Real-World Applications
- Conclusion
In the dynamic landscape of engineering design, mastering thermal analysis is a cornerstone for ensuring the optimal performance and reliability of diverse products. Engineers grapple with intricate thermal challenges across industries, from electronic devices susceptible to overheating to automotive components demanding efficient cooling systems. SolidWorks Flow Simulation emerges as an indispensable solution, seamlessly integrating thermal analysis capabilities into the SolidWorks CAD environment. If you need assistance with your thermal analysis assignment, our team at computeraideddesignassignmenthelp.com is here to provide the help you need.
Navigating the nuances of thermal analysis requires a sophisticated tool that goes beyond conventional approaches, and SolidWorks Flow Simulation rises to the occasion with its advanced computational fluid dynamics (CFD) capabilities. This H1 sets the stage for a deep dive into the key features and applications of SolidWorks Flow Simulation, emphasizing its prowess in accurate heat transfer modeling, conjugate heat transfer analysis, and user-friendly interfaces. As we unravel the steps in employing SolidWorks Flow Simulation to address thermal challenges, this blog aims to empower engineers with practical insights, enabling them to harness the full potential of this powerful tool in crafting designs that excel in the face of diverse thermal environments.
Understanding the Importance of Thermal Analysis
In the intricate realm of engineering, where innovation meets functionality, thermal analysis stands as a pivotal discipline. Its importance reverberates across diverse industries, influencing the design and performance of a myriad of products. Engineers face the challenge of ensuring that their creations can withstand the rigors of varying temperature conditions, making thermal analysis an indispensable tool in the design and validation process. Without a comprehensive understanding of how heat dissipates or accumulates within a system, products may succumb to premature failure, compromised efficiency, or even safety hazards. Thermal analysis acts as a preemptive measure, allowing engineers to anticipate and address potential thermal challenges before they manifest in the real-world environment.
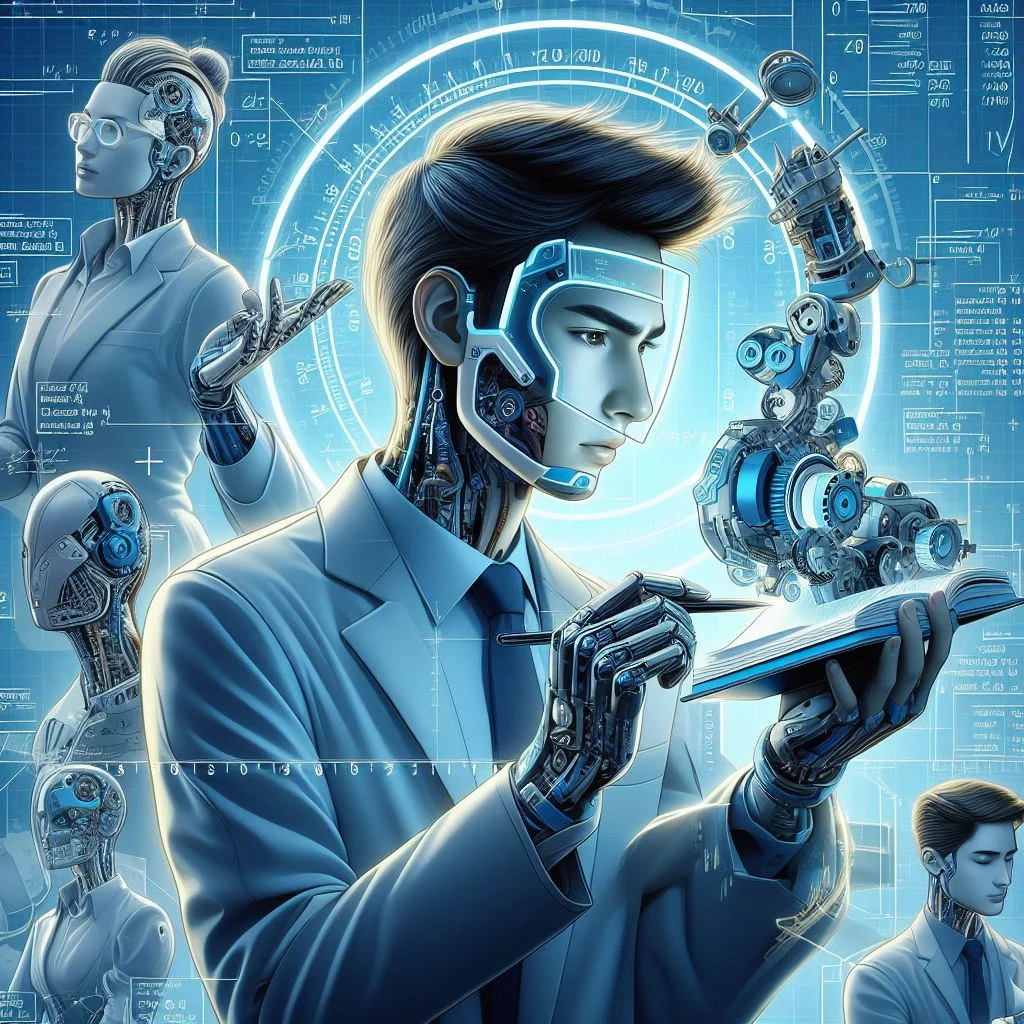
As technology advances and engineering solutions become more intricate, the need for effective thermal management becomes increasingly apparent. Electronic components, automotive systems, and industrial machinery all grapple with thermal considerations that can significantly impact their performance and longevity. Thermal analysis not only ensures compliance with safety standards but also unlocks opportunities for innovation by pushing the boundaries of design possibilities. It serves as the compass guiding engineers through the complex terrain of heat transfer, enabling them to create products that not only meet specifications but also excel in the face of diverse thermal demands. In essence, understanding the importance of thermal analysis is synonymous with empowering engineers to forge a future where designs not only survive but thrive in the dynamic interplay of temperature and functionality.
Common Thermal Analysis Challenges
- Heat Dissipation in Electronics:Electronics are prone to overheating, impacting performance and longevity. SolidWorks Flow Simulation allows engineers to model heat dissipation in electronic components, optimizing their designs to prevent thermal issues.
- Cooling Systems in Automotive Design:Efficient thermal management is critical in automotive design, especially with the increasing complexity of modern vehicles. SolidWorks Flow Simulation aids in simulating and improving cooling systems, preventing engine overheating and ensuring optimal performance.
- Industrial Machinery and Thermal Stress:Heavy-duty machinery often faces extreme temperature conditions, leading to thermal stress. SolidWorks Flow Simulation enables engineers to analyze and mitigate thermal stress, enhancing the durability and reliability of industrial equipment.
Introduction to SolidWorks Flow Simulation
SolidWorks Flow Simulation stands as a pinnacle in the world of computational fluid dynamics (CFD), offering a comprehensive suite of tools designed to go beyond mere fluid dynamics and delve into the intricate realm of thermal analysis. Developed as an integral component of the SolidWorks suite, this software seamlessly integrates into the SolidWorks CAD environment, fostering a synergistic relationship between design and analysis. Engineers and designers find SolidWorks Flow Simulation particularly advantageous due to its intuitive interface and robust capabilities, providing a unified platform where they can not only visualize fluid flow but also simulate and optimize thermal performance within the same familiar workspace.
As a CFD tool, SolidWorks Flow Simulation goes beyond the basics, incorporating advanced features such as conjugate heat transfer analysis, enabling the simulation of heat exchange between solids and fluids. This capability is especially crucial in scenarios where components have both solid and fluid domains, allowing for a more accurate representation of real-world thermal behavior. Whether tackling complex electronic systems, automotive cooling challenges, or industrial machinery, SolidWorks Flow Simulation empowers users to perform thorough thermal analyses, fostering innovation and efficiency in the product development process.
Key Features of SolidWorks Flow Simulation for Thermal Analysis
- Accurate Heat Transfer Modeling: SolidWorks Flow Simulation employs advanced algorithms to model heat transfer in solids and fluids accurately. This capability allows engineers to visualize temperature distribution within a design and identify potential hotspots.
- Conjugate Heat Transfer Analysis:The tool supports conjugate heat transfer analysis, enabling the simulation of heat exchange between solids and fluids. This is invaluable for assessing the thermal performance of components with both solid and fluid domains.
- Parametric Studies for Optimization: Engineers can leverage parametric studies to explore various design configurations and identify the most thermally efficient solutions. This iterative process facilitates optimization, ensuring that the final design meets or exceeds thermal performance requirements.
- User-Friendly Interface:SolidWorks Flow Simulation boasts an intuitive interface, making it accessible to both novice and experienced users. The software provides a range of pre-defined materials and boundary conditions, streamlining the setup of thermal simulations.
Step-by-Step Guide to Solving Thermal Analysis Problems with SolidWorks Flow Simulation
Solving thermal analysis problems with SolidWorks Flow Simulation involves a systematic and intuitive step-by-step process. The first crucial step is to import the SolidWorks CAD model into the Flow Simulation environment and meticulously define the geometry of the system. This includes accurately representing all components relevant to thermal analysis, such as heat sinks, electronic circuits, and any other elements affecting heat transfer. With a well-defined geometry, engineers can move on to the second step, wherein material properties are assigned. SolidWorks Flow Simulation provides an extensive material library, allowing users to specify thermal conductivity, specific heat, and other essential properties for each component. This step lays the foundation for accurate simulations by ensuring that the software understands the physical characteristics of the materials involved.
Moving forward, the third step involves setting boundary conditions, a critical aspect of thermal analysis. Engineers define the environmental conditions, such as the ambient temperature surrounding the system, and introduce heat sources or sinks where applicable. These boundary conditions emulate real-world scenarios and are essential for simulating how a design responds to thermal challenges. Once boundary conditions are established, engineers proceed to meshing, the fourth step. Generating a mesh involves breaking down the model into smaller elements, and SolidWorks Flow Simulation's automatic meshing tools simplify this process. A fine mesh is crucial for obtaining accurate results, as it allows the software to capture intricate details of heat transfer within the system. With the mesh in place, engineers move on to running the simulation, initiating the software to solve the governing equations of heat transfer numerically. Monitoring the simulation provides real-time insights into temperature distribution and heat flux, allowing engineers to identify and address thermal challenges effectively. The final steps involve post-processing and analysis, where engineers utilize SolidWorks Flow Simulation's visualization tools to interpret simulation results, ensuring a comprehensive understanding of the thermal performance of their designs. For this example, we'll focus on optimizing the cooling system for an electronic component.
Step 1 - Model Geometry
In the initial phase of solving thermal analysis problems using SolidWorks Flow Simulation, the foundation lies in accurately defining the geometry of your design. Begin by seamlessly importing your SolidWorks CAD model into the Flow Simulation environment. This step ensures that the electronic component or system you're analyzing is faithfully represented, down to the finest detail. Pay meticulous attention to the inclusion of all pertinent components, such as heat sinks, fans, or any structures influencing heat flow. SolidWorks Flow Simulation's capacity to work seamlessly within the SolidWorks CAD platform facilitates a smooth transition from design to analysis, allowing for a precise and comprehensive representation of the thermal landscape within your model. This fidelity in geometry sets the stage for subsequent steps in the thermal analysis process, laying the groundwork for a robust and accurate simulation.
Step 2 - Define Material Properties
In the realm of thermal analysis using SolidWorks Flow Simulation, defining accurate material properties is a pivotal step to ensure the fidelity of simulations. Once the geometry of the model is established, the next critical task is assigning appropriate material characteristics to each component. SolidWorks Flow Simulation provides engineers with a comprehensive material library, offering a diverse range of predefined materials commonly used in engineering applications. Engineers must meticulously specify properties such as thermal conductivity, specific heat, and density for each material involved in the analysis. This step not only establishes the foundation for accurate heat transfer simulations but also allows for a nuanced understanding of how different materials within the design contribute to overall thermal performance. By leveraging the robust material library and ensuring precise property assignments, engineers lay the groundwork for a reliable and insightful thermal analysis using SolidWorks Flow Simulation.
Step 3 - Set Boundary Conditions
Setting accurate and representative boundary conditions is a pivotal step in conducting a successful thermal analysis using SolidWorks Flow Simulation. In this phase, engineers define the environmental factors and thermal inputs that influence the behavior of the system. Begin by specifying the ambient conditions, such as the surrounding air temperature, which forms the baseline for the simulation. Identify and apply heat sources or sinks within the model, accounting for the thermal contributions of components like electronic circuits, motors, or any other heat-emitting elements. Accurate representation of these boundary conditions ensures a realistic simulation, allowing engineers to capture the dynamic interplay of heat transfer within the design. The precision with which these conditions are set directly impacts the reliability of the thermal analysis results and informs subsequent steps in the simulation process.
Step 4 - Meshing
Meshing, a pivotal step in the SolidWorks Flow Simulation process, involves breaking down the complex geometry of your model into smaller, manageable elements. This process, akin to creating a digital grid, allows for precise calculations of thermal behavior. A finely tuned mesh is crucial for accurate simulation results, as it captures the nuances of temperature distribution and heat transfer within the design. SolidWorks Flow Simulation simplifies this intricate task with its automatic meshing tools. Engineers can seamlessly generate a mesh tailored to the specific intricacies of their model, ensuring that the simulation accurately represents the physical reality of the thermal environment. By striking the right balance between mesh density and computational efficiency, SolidWorks Flow Simulation enables engineers to obtain reliable insights into the thermal performance of their designs, laying the foundation for informed decision-making and optimization.
Step 5 - Running the Simulation
With the model properly defined, materials assigned, and boundary conditions set, it's time to set the thermal wheels in motion by initiating the simulation. SolidWorks Flow Simulation employs state-of-the-art numerical methods to solve the governing equations of heat transfer, providing a comprehensive analysis of thermal behavior within the designated model. As the simulation progresses, the software tracks temperature distribution, heat flux, and other critical parameters, generating a wealth of data for analysis. Engineers can closely monitor the process, ensuring that the simulation converges to a reliable solution. This step is pivotal, as it unveils the intricate thermal dynamics at play within the design, offering insights that are crucial for optimizing the system's thermal performance. Through this iterative and insightful simulation process, SolidWorks Flow Simulation empowers engineers to make informed decisions that lead to robust and thermally efficient designs.
Step 6 - Post-Processing and Analysis
In the final phase of our thermal analysis journey using SolidWorks Flow Simulation, the spotlight turns to post-processing and analysis. As the simulation completes, engineers gain access to a wealth of data that unveils the intricacies of temperature distribution within the designed system. SolidWorks Flow Simulation provides a suite of post-processing tools that allow users to dissect and interpret the results effectively. Visualizing temperature contours, heat flux, and thermal gradients offers a comprehensive understanding of the model's thermal behavior. By examining these visual representations, engineers can pinpoint critical areas of concern, identify potential hotspots, and validate the efficacy of their thermal management strategies. This step serves as a crucial checkpoint, enabling engineers to make informed decisions for refining the design, optimizing heat dissipation, and ensuring the thermal integrity of the product under consideration. SolidWorks Flow Simulation's user-friendly post-processing capabilities empower engineers to extract meaningful insights, guiding them towards a meticulously engineered and thermally resilient final product.
Case Studies - Real-World Applications
In the realm of engineering, the proof of a tool's efficacy lies in its real-world applications. SolidWorks Flow Simulation has left an indelible mark on various industries by providing tangible solutions to intricate thermal analysis challenges. Consider a case where a leading electronics manufacturer faced persistent overheating issues in their intricate circuitry. By employing SolidWorks Flow Simulation, engineers were able to identify and address hotspots, optimizing the design of heat sinks and airflow channels. This resulted in a significant reduction in device temperatures, enhancing both performance and reliability. Another noteworthy application comes from the automotive sector, where a renowned car manufacturer utilized SolidWorks Flow Simulation to refine the cooling system of a high-performance engine. The simulation facilitated the fine-tuning of radiator configurations, ensuring optimal heat dissipation and preventing thermal-related malfunctions. These real-world case studies underscore the practical impact of SolidWorks Flow Simulation in overcoming thermal analysis hurdles and elevating the quality of engineered products.
Conclusion
In conclusion, SolidWorks Flow Simulation stands out as an indispensable tool for engineers seeking to conquer thermal analysis challenges. The software's ability to seamlessly integrate with SolidWorks CAD, coupled with its robust features like accurate heat transfer modeling, parametric studies, and conjugate heat transfer analysis, provides a comprehensive solution for addressing thermal issues across diverse industries. By leveraging its user-friendly interface, engineers can navigate the complexities of thermal simulations with ease, empowering them to optimize designs for superior thermal performance.
As technology continues to advance and engineering designs become more intricate, the demand for effective thermal analysis solutions intensifies. SolidWorks Flow Simulation not only meets this demand but surpasses expectations by facilitating in-depth insights into temperature distribution and heat flux. The step-by-step guide outlined in this blog offers a roadmap for engineers to follow, ensuring that they can harness the full potential of SolidWorks Flow Simulation in their quest to create products that not only meet but exceed thermal performance requirements. In essence, SolidWorks Flow Simulation is not just a tool; it is a key ally in the pursuit of innovation, reliability, and efficiency in engineering design.