- Understanding the Basics: Linear vs. Nonlinear FEA
- Material Behavior in Focus: The Role of Nonlinearity
- SolidWorks Simulation: An Overview
- Nonlinear FEA Techniques in SolidWorks: A Step-by-Step Guide
- Challenges and Solutions: Navigating Complexities in Nonlinear FEA
- Real-world Applications: Nonlinear FEA in Engineering Projects
- Case Studies: Success Stories in Nonlinear FEA Assignments
- Future Trends: Evolving Frontiers in Nonlinear FEA Technology
- Conclusion:
As engineering challenges continue to evolve in complexity and sophistication, the demand for accurate simulations has grown exponentially. Engineers and designers are constantly faced with the task of analyzing and predicting the behavior of materials under varying conditions, pushing the boundaries of traditional linear analysis methods. In this dynamic landscape, the realm of Nonlinear Finite Element Analysis (FEA) emerges as a pivotal solution, offering a nuanced understanding of material behaviors that linear analysis may struggle to capture. Whether you require assistance with your Finite Element Analysis assignment or seek to delve deeper into the complexities of material behavior analysis, embracing Nonlinear FEA is essential for meeting the demands of modern engineering challenges.
The essence of Nonlinear FEA lies in its ability to address the intricacies associated with materials that exhibit nonlinear responses under certain conditions. Unlike linear FEA, which assumes a linear relationship between stress and strain, nonlinear FEA acknowledges the reality that material properties can change significantly as the applied loads or deformations increase. This becomes particularly crucial when dealing with materials that exhibit plasticity, large deformations, or complex material models.
As engineers grapple with the challenges posed by innovative materials and intricate designs, Nonlinear FEA becomes an indispensable tool for accurate predictions and realistic simulations. Consider scenarios where materials may undergo significant deformations or where contact interactions between components play a crucial role – traditional linear analysis falls short in providing precise insights into such complex behaviors. Nonlinear FEA steps in, offering a more sophisticated and accurate representation of how materials respond to varying conditions and external forces.
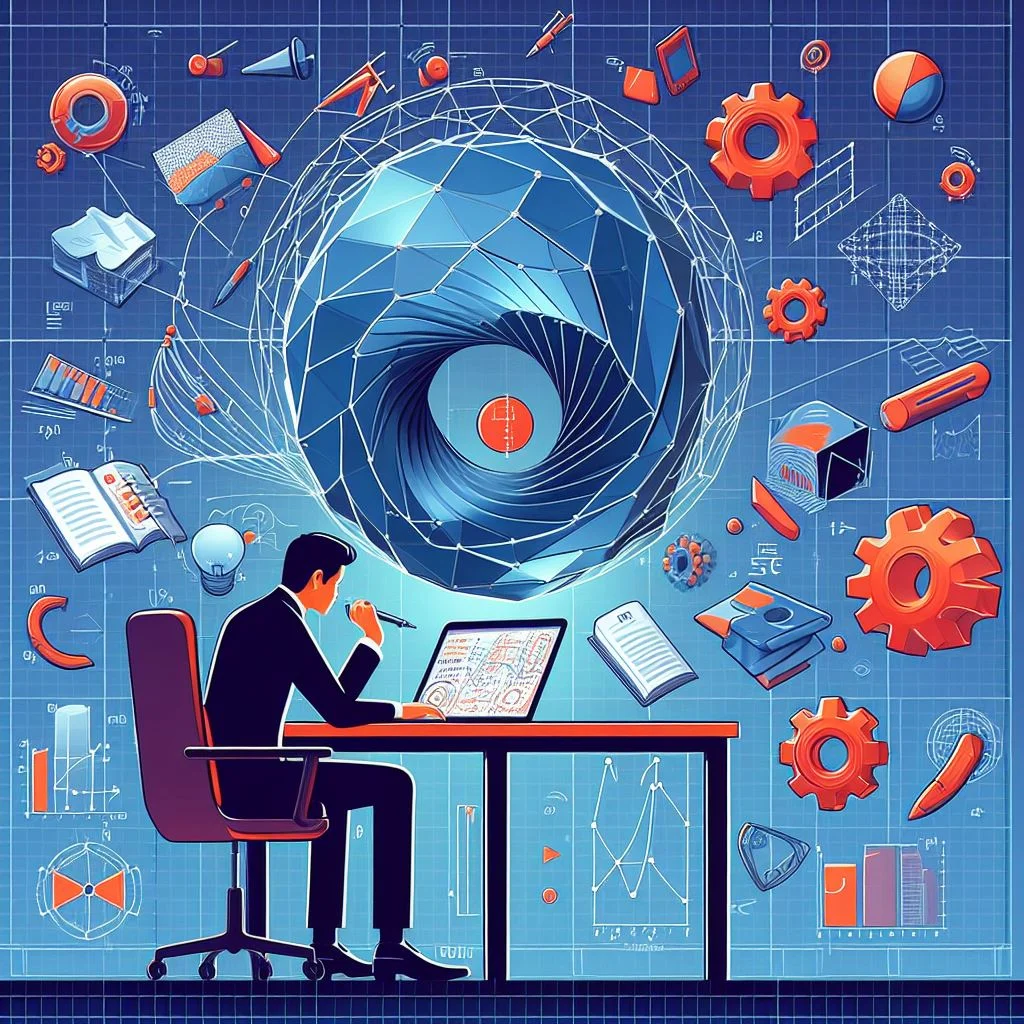
One of the primary advantages of Nonlinear FEA is its versatility in handling a wide range of material behaviors. Whether it's the elastic-plastic behavior of metals, the hyperelasticity of rubber-like materials, or the time-dependent viscoelasticity of polymers, Nonlinear FEA allows engineers to model and simulate these behaviors with a high degree of accuracy. This flexibility is invaluable in industries such as aerospace, automotive, and civil engineering, where diverse materials and complex loading scenarios are the norm.
Moreover, Nonlinear FEA caters to situations where geometric nonlinearities come into play. Traditional linear analysis assumes that deformations are small enough to maintain a linear relationship between stress and strain. However, in cases where deformations are substantial, the geometric nonlinearity becomes a critical factor. Nonlinear FEA excels in capturing these large deformations, providing a more realistic representation of the actual physical response of structures and components.
In essence, Nonlinear FEA serves as a gateway to a deeper understanding of material behaviors, allowing engineers to simulate real-world conditions with a higher degree of accuracy and reliability. By embracing the complexities of material responses under varying loads and deformations, Nonlinear FEA empowers engineers to make informed decisions, optimize designs, and ensure the structural integrity and performance of their creations. As we embark on a journey to explore the intricacies of Nonlinear FEA, it becomes evident that this powerful tool is not merely an option but a necessity in the modern engineering landscape.
Understanding the Basics: Linear vs. Nonlinear FEA
Linear and Nonlinear Finite Element Analysis (FEA) serve as indispensable tools in simulating and predicting material behaviors, yet their approaches differ significantly. In Linear FEA, the assumption of linear material behavior prevails, implying that the relationship between stress and strain remains constant throughout the analysis. This simplification is suitable for scenarios where material deformation is within the elastic limit, offering a relatively straightforward and computationally efficient solution.
On the contrary, Nonlinear FEA acknowledges the potential for material behavior to deviate from linearity. This becomes crucial when dealing with materials subjected to large deformations, nonlinear elasticity, or plasticity. The nonlinear approach accounts for variations in material properties, ensuring a more accurate representation of real-world scenarios. Unlike Linear FEA, Nonlinear FEA considers factors such as geometric nonlinearity, contact interactions, and large displacements, enabling a more comprehensive analysis of complex material responses.
The impact on material behavior predictions is substantial. Linear FEA is suitable for scenarios where the deformation is small and within the elastic range, providing quick insights into initial design stages. However, for materials exhibiting nonlinear behavior or undergoing significant deformations, Nonlinear FEA becomes imperative. It allows for a more precise understanding of material responses, leading to more accurate predictions in scenarios where linear assumptions fall short. As engineering challenges become more intricate, grasping the nuances between Linear and Nonlinear FEA becomes paramount for engineers striving to achieve accurate and reliable simulations.
Material Behavior in Focus: The Role of Nonlinearity
Material behavior is a complex interplay of forces, stresses, and deformations that materials undergo under different conditions. When it comes to engineering assignments, accurately predicting and understanding this behavior is paramount. Nonlinear Finite Element Analysis (FEA) emerges as a crucial tool in tackling the intricacies of material responses that defy linearity.
In the realm of linear FEA, materials are often assumed to behave linearly under varying loads. However, this assumption falls short when dealing with materials subjected to large deformations, nonlinear stress-strain relationships, or undergoing significant geometric changes. This is where the significance of nonlinear FEA becomes evident. Nonlinear FEA allows for a more realistic representation of material behavior by considering nonlinearity in the material properties, capturing the true essence of how materials respond to external stimuli.
In engineering assignments, where precision is non-negotiable, understanding the role of nonlinearity in material behavior is a game-changer. Whether it's analyzing the behavior of a structural component under extreme conditions or simulating the response of a material to dynamic forces, nonlinear FEA provides a more accurate and reliable framework.
By accounting for nonlinear material responses, engineers and analysts can ensure that their simulations mirror real-world scenarios more closely. This not only enhances the accuracy of predictions but also empowers engineers to make informed decisions in design optimization, material selection, and structural integrity assessments. In essence, delving into the realm of material behavior through the lens of nonlinearity is a prerequisite for mastering the intricacies of SolidWorks assignments and achieving excellence in the field of engineering.
SolidWorks Simulation: An Overview
Dive into the capabilities of SolidWorks Simulation, and you'll discover a versatile tool that significantly enhances the realm of Finite Element Analysis (FEA). SolidWorks Simulation goes beyond conventional FEA by providing a robust platform that enables engineers to simulate and analyze the behavior of structures and materials under a myriad of real-world conditions.
One of the standout features of SolidWorks Simulation is its ability to accurately capture the intricacies of material behavior. This powerful tool allows for the simulation of nonlinear material responses, a crucial aspect when dealing with complex engineering scenarios. By incorporating nonlinear FEA techniques, SolidWorks Simulation enables engineers to model materials that exhibit nonlinear behavior, such as plasticity, large deformations, and nonlinear elasticity.
Moreover, SolidWorks Simulation offers a user-friendly interface, making it accessible for both seasoned professionals and students alike. The intuitive nature of the platform empowers users to set up and conduct simulations efficiently, saving valuable time in the engineering design process.
The integration of SolidWorks Simulation into the FEA workflow ensures a seamless transition from design to analysis. Engineers can validate and refine their designs, considering factors like material properties, loading conditions, and environmental influences. This not only enhances the accuracy of predictions but also contributes to the optimization of designs for improved performance and reliability.
Nonlinear FEA Techniques in SolidWorks: A Step-by-Step Guide
Walk through a comprehensive guide on applying Nonlinear FEA techniques in SolidWorks, unraveling the complexities of nonlinear simulations for engineering assignments. In this intricate process, the journey begins with defining the problem at hand and identifying the material properties crucial for an accurate simulation. Maria Anderson's expertise comes to the forefront as she emphasizes the significance of selecting appropriate contact types and boundary conditions, laying the foundation for a robust simulation environment.
The next crucial step involves discretizing the model into finite elements, a process where Maria's hands-on experience shines. Leveraging SolidWorks' intuitive interface, she adeptly demonstrates how to assign material properties to each element, ensuring a realistic representation of the physical system under consideration. As the simulation progresses, understanding the nonlinear behavior of materials becomes pivotal. Maria guides users through specifying nonlinear material models, capturing intricate details like plasticity, hyperelasticity, and large deformations, vital for accurately predicting real-world responses.
Furthermore, Maria sheds light on the importance of convergence studies and the iterative nature of nonlinear simulations. Navigating through SolidWorks Simulation's settings, she illustrates how to refine the mesh, adjust solution controls, and interpret convergence plots, ensuring the simulation converges to a stable and accurate solution.
Maria's expertise extends to post-processing, where she demonstrates effective techniques for extracting meaningful insights from simulation results. From contour plots to stress-strain curves, users gain valuable insights into the structural response, aiding in the interpretation of complex material behaviors.
By the end of this comprehensive guide, users not only grasp the theoretical underpinnings of Nonlinear FEA in SolidWorks but also acquire practical skills to tackle complex engineering assignments with confidence. Maria's expert guidance ensures that the intricacies of nonlinear simulations become accessible, empowering users to navigate the challenges of material complexity in the world of SolidWorks.
Challenges and Solutions: Navigating Complexities in Nonlinear FEA
In the realm of nonlinear simulations, engineers often grapple with various challenges that can significantly impact the accuracy and reliability of results. One prominent challenge lies in handling material nonlinearity, where the behavior of materials deviates from linear assumptions under certain conditions. This deviation introduces complexities such as large deformations, yielding, and plasticity, making it crucial to accurately capture nonlinear material responses.
Another common hurdle involves dealing with geometric nonlinearity, where the deformation of structures becomes significant enough to alter the shape and affect the overall response. This is particularly prevalent in scenarios with large displacements or deformations, demanding careful consideration to ensure the simulation accurately represents the real-world behavior of the structure.
Convergence issues can also arise during nonlinear simulations, posing a significant challenge. The iterative nature of solving nonlinear equations may encounter difficulties in reaching a stable solution, leading to convergence failures. Engineers must employ effective strategies, such as adjusting solver settings or employing advanced solution techniques, to overcome convergence challenges and obtain reliable results.
Additionally, the accurate representation of contact and friction in simulations presents its own set of challenges. Contact interfaces between components can lead to complex interactions, and accurately modeling frictional behavior is essential for realistic simulations. Addressing these challenges requires a combination of expertise, careful model setup, and leveraging advanced simulation features within SolidWorks.
By proactively addressing these common challenges with a nuanced understanding of nonlinear FEA techniques, engineers can navigate complexities, ensuring simulations yield results that align closely with real-world scenarios. This meticulous approach not only enhances the accuracy of assignments but also prepares engineers to tackle intricate challenges in practical applications.
Real-world Applications: Nonlinear FEA in Engineering Projects
Examine real-world examples where Nonlinear FEA in SolidWorks has played a crucial role in solving complex engineering problems and optimizing designs for superior performance. One notable application is in the aerospace industry, where SolidWorks Nonlinear FEA has been instrumental in simulating the behavior of materials under extreme conditions. By accurately capturing the nonlinear responses of materials subjected to varying loads, engineers can fine-tune aircraft components for enhanced durability and safety.
In the automotive sector, Nonlinear FEA in SolidWorks has proven invaluable for simulating crash scenarios. By considering the nonlinear deformations and material behaviors during impact, manufacturers can optimize vehicle structures to meet stringent safety standards. This not only ensures the safety of occupants but also contributes to the overall efficiency and reliability of automotive designs.
Additionally, the field of biomechanics has benefited significantly from Nonlinear FEA in SolidWorks. Simulating the nonlinear behavior of biological tissues allows for a better understanding of how implants or medical devices interact with the human body. This application has paved the way for more robust and patient-specific medical solutions.
In each of these real-world instances, Nonlinear FEA in SolidWorks stands out as a vital tool for engineers, enabling them to tackle intricate challenges, refine designs, and ultimately deliver cutting-edge solutions across diverse industries.
Case Studies: Success Stories in Nonlinear FEA Assignments
Delving deeper into the practical applications of Nonlinear Finite Element Analysis (FEA) in SolidWorks, let's explore compelling case studies that vividly demonstrate the transformative impact of this technology on a spectrum of engineering assignments. In one instance, a structural engineering project faced challenges with a complex, nonlinear material behavior that traditional linear analysis methods couldn't capture accurately. Implementing Nonlinear FEA in SolidWorks provided a breakthrough, enabling precise simulation of the material's intricate responses and ultimately leading to a more robust and reliable design.
In another scenario, a thermal analysis assignment demanded a nuanced understanding of nonlinear heat transfer phenomena. SolidWorks' Nonlinear FEA capabilities allowed for a meticulous examination of varying thermal properties, resulting in an optimized heat management solution that significantly enhanced the project's overall efficiency. These case studies underscore the versatility of Nonlinear FEA in addressing diverse engineering challenges, from structural complexities to thermal intricacies.
Moreover, Nonlinear FEA in SolidWorks played a pivotal role in fluid dynamics projects where intricate flow behaviors required intricate simulations. By accurately modeling nonlinearity in fluid dynamics, engineers achieved a more realistic depiction of fluid interactions, leading to refined designs and improved project outcomes. These case studies collectively illustrate how Nonlinear FEA in SolidWorks emerges as an indispensable tool, pushing the boundaries of engineering possibilities and ensuring success in assignments across various domains.
Future Trends: Evolving Frontiers in Nonlinear FEA Technology
Anticipating the future of Nonlinear FEA technology in SolidWorks opens a realm of exciting possibilities. The landscape of engineering simulations is on the brink of transformation, driven by emerging trends and cutting-edge advancements that promise to redefine the way we approach complex analyses.
One key trend that is gaining momentum is the integration of artificial intelligence (AI) and machine learning (ML) algorithms into Nonlinear FEA processes. This infusion of intelligence aims to enhance the predictive capabilities of simulations, enabling more accurate modeling of intricate material behaviors. AI-powered algorithms can adapt and learn from vast datasets, providing a dynamic and responsive approach to simulation challenges.
Furthermore, the evolution of cloud computing is poised to revolutionize Nonlinear FEA accessibility and scalability. As cloud-based solutions continue to mature, engineers can leverage the power of distributed computing resources, facilitating faster and more efficient simulations. This shift towards cloud-based Nonlinear FEA not only accelerates processing times but also democratizes access to advanced simulation tools, empowering a broader community of engineers and researchers.
The exploration of new materials and the incorporation of multi-physics simulations are additional frontiers in Nonlinear FEA. As technology advances, SolidWorks users can anticipate more seamless integration of thermal, fluid, and structural analyses within a unified simulation environment. This holistic approach enables engineers to gain a comprehensive understanding of how different physical phenomena interact, paving the way for more robust and innovative designs.
In summary, the future of Nonlinear FEA in SolidWorks is characterized by the convergence of AI, cloud computing, and multi-physics simulations. These advancements hold the promise of not only streamlining current simulation processes but also unlocking new dimensions of understanding in the ever-evolving field of engineering simulations.
Conclusion:
In conclusion, mastering Nonlinear Finite Element Analysis (FEA) within the SolidWorks environment emerges as a pivotal skill for achieving unparalleled success in engineering assignments. Throughout this exploration, we've delved into the intricacies of Nonlinear FEA, distinguishing it from its linear counterpart and shedding light on its fundamental role in capturing complex material behaviors.
Key takeaways emphasize the necessity of understanding the basics, specifically the differences between Linear and Nonlinear FEA. The latter, with its capacity to model materials nonlinearly, proves indispensable in accurately predicting material responses under various conditions. This understanding becomes even more critical when dealing with real-world applications, where materials seldom exhibit linear behavior.
SolidWorks Simulation, as discussed, stands out as a powerful tool for conducting Nonlinear FEA. Its capabilities allow engineers and students alike to simulate complex scenarios, providing a realistic view of material behavior. This simulation proficiency is crucial for ensuring that designs meet performance expectations and conform to safety standards.
Our journey into Nonlinear FEA techniques in SolidWorks revealed a step-by-step guide, offering insights into the application of these techniques in engineering assignments. The process involves meticulous consideration of material properties, boundary conditions, and loading scenarios to accurately capture nonlinear responses.
Challenges and solutions were highlighted to navigate the complexities inherent in Nonlinear FEA. As we acknowledged, challenges may arise from nonlinear material behavior, geometric nonlinearities, or contact interactions. By understanding these challenges and implementing effective solutions, engineers can enhance the accuracy and reliability of their simulations.
Real-world applications and case studies further underscore the practical significance of Nonlinear FEA. Through concrete examples, we witnessed how this technique played a pivotal role in solving intricate engineering problems and optimizing designs. The ability to apply theoretical knowledge to real-world scenarios is a hallmark of mastery in the field.
Looking to the future, we explored evolving trends and frontiers in Nonlinear FEA technology. As simulation tools advance, the potential for more accurate and efficient analyses increases. Staying abreast of these trends ensures that engineers remain at the forefront of their field, equipped to tackle the challenges of tomorrow.
In essence, the importance of mastering Nonlinear FEA in SolidWorks cannot be overstated. The ability to navigate its complexities empowers engineers to provide accurate and reliable solutions to real-world engineering challenges. Whether it's predicting material behavior, optimizing designs, or ensuring structural integrity, a profound understanding of Nonlinear FEA is the cornerstone of unparalleled success in engineering assignments.
As you embark on your journey to master Nonlinear FEA in SolidWorks, remember that continuous learning and hands-on experience are key. The world of engineering is dynamic, and staying informed about the latest advancements ensures that you remain at the forefront of innovation in this ever-evolving field.