- Understanding Topology Optimization
- Benefits of Topology Optimization:
- Setting Up Your Project
- Contrasting with Parametric Optimization
- Parametric Optimization Considerations:
- Comparison Insights:
- Analyzing and Interpreting Results
- Tips for Success
- Conclusion
SolidWorks assignments often present challenges that demand proficiency in advanced features like topology optimization. This methodological approach is pivotal for enhancing the structural efficiency of designs by strategically redistributing material within defined spatial constraints. By focusing on achieving optimal performance metrics such as stiffness, strength, and weight reduction, topology optimization ensures that engineering designs meet rigorous performance standards set by industry requirements. If you need assistance with your Simulation assignment, understanding these advanced features will be crucial for successfully tackling complex design problems.
In this comprehensive guide, we delve into the essentials of employing topology optimization through SolidWorks Simulation. Our focus centers on a practical scenario involving a cantilevered bracket, a common structural component in engineering applications. By examining this specific case, students gain practical insights into how to apply topology optimization techniques effectively in their own projects.
Understanding topology optimization starts with a clear definition of project objectives and constraints. These parameters not only guide the optimization process but also ensure that the resulting design meets functional requirements.
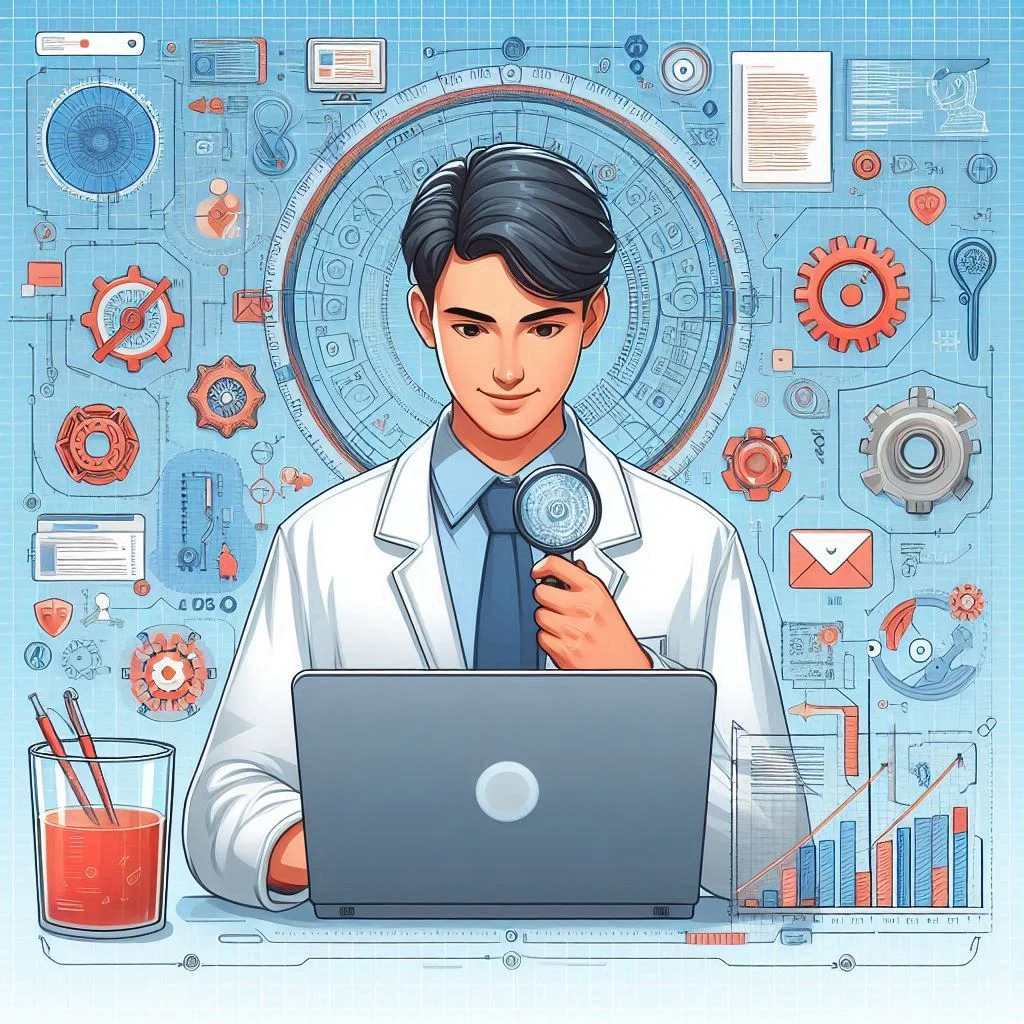
For instance, specifying load conditions, such as forces and pressures, alongside constraints like maximum stress limits and displacement thresholds, provides the necessary framework for SolidWorks Simulation to compute an optimized material layout.
Topology optimization differs significantly from traditional parametric optimization methods. While parametric optimization adjusts geometric parameters iteratively to achieve desired outcomes, topology optimization focuses on reconfiguring material distribution within a design space to maximize structural performance. This distinction is critical in industries where achieving lightweight yet robust designs is paramount, such as aerospace and automotive sectors.
Upon setting up the topology optimization simulation in SolidWorks, students embark on evaluating and interpreting simulation results. This phase involves scrutinizing key performance indicators such as stress distribution patterns, displacement characteristics, and material utilization efficiency. Through systematic analysis, students can identify areas for potential design refinement or optimization fine-tuning, ensuring that the final design meets or exceeds predefined engineering criteria.
Success in mastering SolidWorks assignments, especially those involving advanced features like topology optimization, hinges on practical experience and continuous learning. Familiarizing oneself with SolidWorks Simulation tools through hands-on exercises, tutorials, and real-world applications is crucial for building proficiency. Each assignment serves as an opportunity for students to deepen their understanding of engineering principles and hone their skills in optimizing mechanical designs effectively.
Understanding Topology Optimization
Topology optimization is a sophisticated computational technique aimed at enhancing the performance of mechanical designs by strategically redistributing material within a predefined design volume. Unlike traditional optimization methods that focus on iterative adjustments to geometric parameters like thicknesses or dimensions, topology optimization takes a fundamentally different approach. It seeks to achieve optimal structural performance while simultaneously minimizing the overall weight of the component or assembly.
This method is highly prized in industries where achieving a balance between weight reduction and maintaining structural integrity is paramount. For instance, in aerospace applications, reducing weight without sacrificing strength can lead to significant improvements in fuel efficiency and overall performance. Similarly, in automotive engineering, lighter vehicle components can contribute to better handling and lower fuel consumption. Even in consumer goods sectors, such as sports equipment or electronics, where lightweight yet durable products are in demand, topology optimization offers a powerful tool to meet these requirements effectively.
By leveraging advanced computational algorithms, topology optimization identifies the most efficient distribution of material based on specified performance criteria and constraints. This process often results in designs that are not only lighter but also structurally robust, capable of withstanding the intended operational loads and conditions. This innovative approach encourages engineers and designers to explore unconventional shapes and configurations that may not be immediately intuitive but prove superior in terms of performance and efficiency.
Benefits of Topology Optimization:
Topology optimization offers several key benefits that contribute to enhanced design efficiency and innovation:
- Improved Structural Performance: By redistributing material to areas experiencing higher stress concentrations, topology optimization optimizes designs for superior stiffness, strength, and fatigue resistance. This results in components that can withstand operational loads more effectively while potentially extending their operational lifespan.
- Material Efficiency: Reducing unnecessary material usage through topology optimization not only lowers manufacturing costs but also promotes sustainable practices in engineering. This efficiency in material usage contributes to lighter designs without compromising structural integrity, which is crucial for industries where weight reduction directly impacts performance and operational efficiency.
- Facilitates Innovative Designs: Topology optimization challenges traditional design paradigms by enabling engineers to explore unconventional shapes and structures. By focusing on functional requirements rather than preconceived notions of form, engineers can discover new design solutions that are both efficient and innovative, pushing the boundaries of what's possible in product development and engineering.
These benefits underscore the transformative impact of topology optimization in modern engineering practices, making it an indispensable tool for optimizing designs across various industries.
Setting Up Your Project
To effectively apply topology optimization in SolidWorks, follow these fundamental steps:
- Define Objectives and Constraints: Begin by clearly defining the design objectives and constraints. Objectives may include minimizing weight while ensuring structural integrity, optimizing stiffness under specified loads, or achieving a certain level of stress distribution. Constraints typically involve factors like maximum allowable stress, displacement limits, and loading conditions.
- Model Preparation: Create a detailed SolidWorks model of the component or assembly you intend to optimize. Ensure accuracy in geometry representation, material properties assignment, and boundary conditions definition.
- Topology Optimization Setup:
- Apply Loads and Constraints: Define the loading conditions (forces, pressures, thermal loads) and constraints (fixed supports, movement constraints) that simulate real-world operating conditions.
- Select Optimization Type: Within SolidWorks Simulation, choose the topology optimization feature. Specify parameters such as minimum member size, maximum displacement, and factor of safety to guide the optimization process.
- Run the Simulation: Initiate the simulation process to allow SolidWorks to compute the optimal material distribution based on the defined objectives and constraints.
Contrasting with Parametric Optimization
While topology optimization focuses on redistributing material within a given space, parametric optimization adjusts geometric parameters iteratively to achieve desired performance outcomes. Understanding the differences between these approaches is crucial for effectively selecting the right method for a given design challenge.
Parametric Optimization Considerations:
- Flexibility in Design Exploration: Allows for exploration of various geometric configurations.
- Simplicity in Implementation: Often easier to implement and understand for straightforward design modifications.
- Application in Early Design Stages: Useful for initial concept development before committing to detailed analysis and optimization.
Comparison Insights:
- Topology Optimization: Emphasizes material efficiency and structural performance through redistribution, suitable for designs where weight reduction and strength optimization are critical.
- Parametric Optimization: Focuses on geometric adjustments, beneficial for exploring design variations and refining concepts iteratively.
Analyzing and Interpreting Results
Upon completion of the topology optimization simulation, proceed with a thorough analysis and interpretation of the results to derive meaningful insights and potential improvements:
- Review Simulation Outputs: Begin by evaluating the comprehensive performance metrics derived from the topology-optimized design. Focus on critical aspects such as:
- Stress Distribution: Examine how stress is distributed across the structure. Identify areas of high stress concentration and ensure they meet safety margins defined by constraints.
- Displacement Characteristics: Assess the displacement patterns to verify structural integrity under operational loads. Ensure displacements are within permissible limits to avoid functional impairments.
- Material Utilization Efficiency: Analyze the material usage efficiency achieved through topology optimization. Compare the optimized design’s mass distribution with initial assumptions and benchmarks to gauge effectiveness.
- Iterative Refinement: Based on the simulation outcomes and analysis, consider iterative refinements to further enhance design performance:
- Adjust Constraints: Fine-tune constraints such as load magnitudes, boundary conditions, or safety factors to optimize specific performance metrics like stress levels or displacement.
- Revisit Initial Assumptions: Review initial design assumptions regarding material properties, manufacturing processes, or operational conditions. Adjust parameters based on simulation insights to align with real-world requirements.
- Explore Alternative Material Selections: Investigate the potential benefits of using different materials or composites. Conduct comparative analyses to determine if alternative materials offer superior performance characteristics or cost-efficiency.
Tips for Success
Mastering SolidWorks assignments, especially those involving advanced features like topology optimization, requires a structured approach and continuous practice. Consider the following tips to enhance your proficiency:
- Understand Design Requirements: Clearly defining project objectives and constraints is essential for guiding your design optimization efforts effectively. This clarity ensures that your solutions align closely with the desired outcomes, whether it's maximizing stiffness, minimizing weight, or optimizing performance under specific conditions.
- Familiarize Yourself with SolidWorks Tools: Invest dedicated time in mastering SolidWorks Simulation tools, particularly the topology optimization features. Engage in tutorials, hands-on practice exercises, and real-world applications to deepen your understanding and proficiency. Familiarity with the software’s capabilities empowers you to leverage its full potential for complex design challenges.
- Iterate and Learn: Approach each assignment as an opportunity for growth. Experiment with different design scenarios, analyze simulation outcomes critically, and incorporate feedback from instructors or peers to refine your skills continuously. Iterative learning not only strengthens your technical abilities but also enhances your problem-solving acumen in engineering design.
- Seek Additional Resources: Utilize resources beyond classroom assignments, such as online forums, webinars, and advanced SolidWorks training courses. These resources provide valuable insights, tips, and best practices shared by experienced professionals and peers, further enriching your learning journey.
Conclusion
Topology optimization in SolidWorks Simulation empowers engineers and students alike to optimize mechanical designs efficiently. By leveraging computational methods to redistribute material and optimize structural performance, designers can achieve significant advancements in design efficiency and effectiveness. This approach not only reduces the weight of components but also enhances their strength and functionality, making it ideal for industries where lightweight yet robust structures are essential, such as aerospace and automotive engineering.
In conclusion, mastering SolidWorks assignments involving topology optimization demands a blend of technical proficiency, creative problem-solving skills, and a deep understanding of engineering principles. Each assignment serves as a valuable learning opportunity to refine skills and prepare for real-world challenges in mechanical design. Embracing tools like SolidWorks Simulation fosters innovation and ensures graduates are well-prepared to tackle complex engineering problems in their careers.
For further guidance on SolidWorks assignments and to explore more about topology optimization, interested individuals can visit solidworksassignmenthelp.com or consult with professionals experienced in SolidWorks tools, such as those at GoEngineer. Their expertise and insights can provide invaluable support in navigating the intricacies of SolidWorks applications and optimization techniques.