- Understanding Software Limitations
- Meshing Complex Geometries
- Interpreting Results Accurately
- Optimizing Computational Resources
- Collaborating and Communicating Results Effectively
- Conclusion
SolidWorks Simulation is indeed a powerful ally for engineers and designers, offering them the ability to scrutinize and refine their designs in a virtual environment, thereby saving time and resources that would otherwise be spent on physical prototyping. However, despite its robust capabilities, users frequently find themselves grappling with a myriad of challenges when engaging with SolidWorks Simulation assignment. These challenges can range from technical intricacies to practical constraints, often demanding innovative solutions and strategic approaches to overcome them effectively. Leveraging expert insights and strategic methodologies can significantly enhance your ability to tackle these challenges successfully.
One of the foremost hurdles users encounter is understanding the limitations inherent in the software itself. While SolidWorks Simulation is equipped with an array of analysis tools, it's imperative for users to grasp the boundaries within which these tools operate. This necessitates a thorough perusal of the software documentation, participation in training sessions, and seeking guidance from seasoned practitioners. Moreover, acknowledging when supplementary tools or software integrations might be necessary to bolster SolidWorks Simulation's capabilities for specialized analyses is crucial for navigating this challenge successfully.
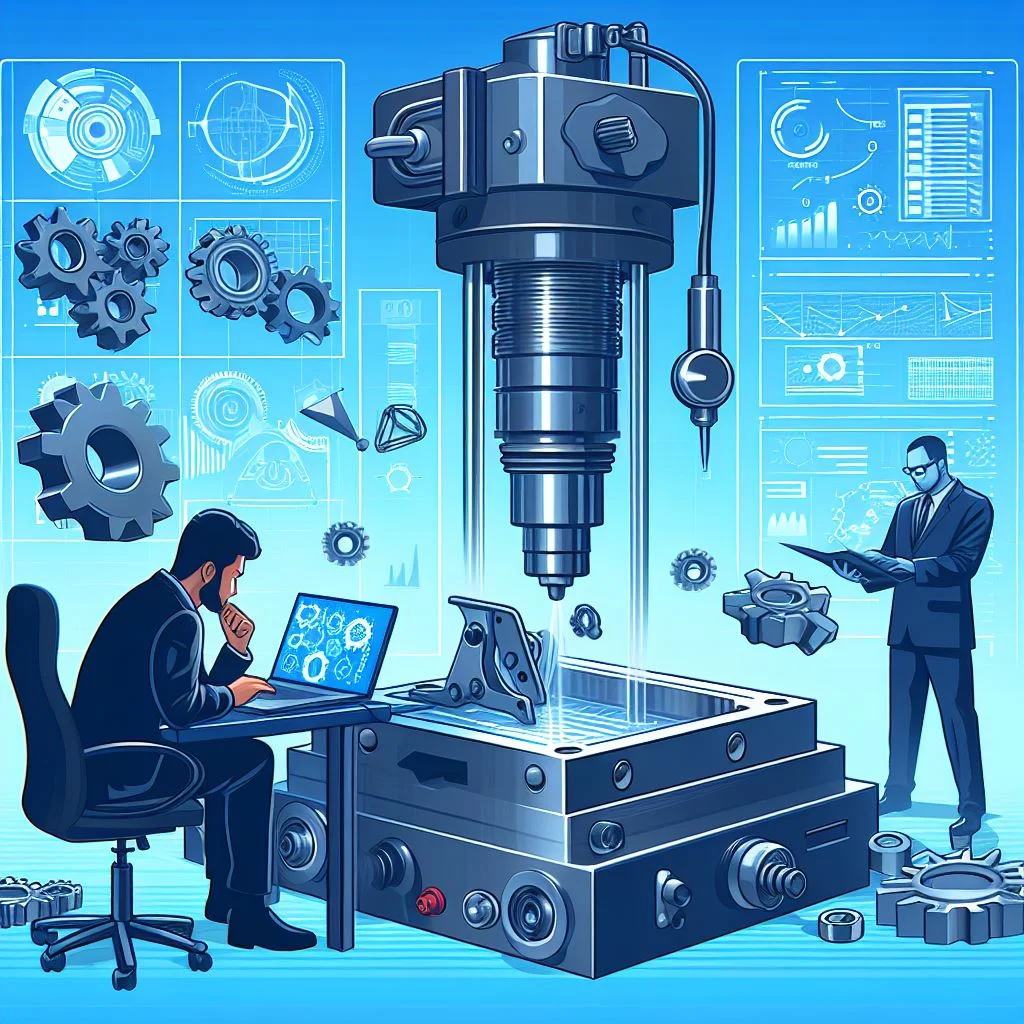
Another common stumbling block lies in the realm of meshing complex geometries. Meshing, the process of dividing a complex geometry into smaller, manageable elements for analysis, is a critical step in any finite element analysis (FEA) workflow. However, achieving an accurate mesh for intricate or irregular shapes can prove to be a daunting task. In such scenarios, users must acquaint themselves with a spectrum of meshing techniques available within SolidWorks Simulation. While automatic meshing algorithms offer convenience for simpler geometries, manual meshing affords greater control and refinement, particularly in complex scenarios. By honing their meshing skills and optimizing mesh settings in alignment with the analysis requirements, users can surmount this challenge and pave the way for more accurate simulation results.
Interpreting simulation results accurately presents yet another hurdle for SolidWorks Simulation users. Despite the wealth of output data furnished by the software, distilling meaningful insights from the results can be a formidable endeavor, particularly in analyses involving multiple parameters and variables. To navigate this challenge adeptly, users must cultivate a deep understanding of the underlying physics governing the simulated behavior and the interplay of various parameters. Visualization tools, such as animations, graphs, and plots, serve as invaluable aids in elucidating complex phenomena and facilitating informed decision-making. Additionally, conducting sensitivity analyses and validation studies bolsters confidence in the simulation results, thereby enhancing their utility for design optimization and decision support.
Optimizing computational resources emerges as a significant challenge, particularly in the context of large-scale or computationally intensive simulations. Limited hardware resources or inefficient simulation setups can lead to prolonged computation times, impeding project timelines and escalating costs. To address this challenge effectively, users must adopt a holistic approach to simulation optimization. This entails refining mesh densities, leveraging symmetry and simplification techniques, and harnessing parallel processing capabilities to expedite computations. Moreover, exploring alternative solutions, such as high-performance computing (HPC) resources or cloud-based simulation platforms, can offer scalability and agility in managing computational demands, thereby enhancing overall productivity and efficiency.
Collaboration and effective communication represent pivotal aspects of the SolidWorks Simulation workflow, yet they often pose significant challenges for users. Bridging the gap between technical intricacies and layman comprehension, and fostering seamless collaboration among multidisciplinary teams, requires a concerted effort. Leveraging collaborative tools and platforms, such as SolidWorks PDM or cloud-based project management solutions, can streamline communication channels and facilitate knowledge sharing. Moreover, transparent documentation of simulation methodologies, assumptions, and limitations cultivates trust and credibility among stakeholders, thereby fostering a conducive environment for collaboration and decision-making.
In essence, while SolidWorks Simulation empowers users with unparalleled capabilities for engineering analysis and design validation, navigating the challenges inherent in its utilization demands ingenuity, perseverance, and strategic acumen. By equipping themselves with a comprehensive understanding of the software's limitations, mastering meshing techniques, interpreting results judiciously, optimizing computational resources, and fostering effective communication and collaboration, users can surmount these challenges and harness the full potential of SolidWorks Simulation in their endeavors.
Understanding Software Limitations
One of the primary challenges in SolidWorks Simulation assignments is understanding the limitations of the software. While SolidWorks Simulation offers a wide range of analysis capabilities, it's essential to recognize its boundaries. For instance, complex nonlinear analyses may require advanced expertise and computational resources beyond what the software can provide efficiently.
To overcome this challenge, users should invest time in understanding the software's documentation, attending training sessions, and seeking guidance from experienced users or mentors. Additionally, leveraging supplementary tools or software integrations can extend SolidWorks Simulation's capabilities for specialized analyses.
It's crucial for users to grasp the specific scenarios where SolidWorks Simulation may not yield optimal results. For example, while the software excels in linear static analyses, it may struggle with highly nonlinear material behavior or intricate contact interactions. Recognizing these limitations early in the simulation process enables users to explore alternative approaches or seek assistance from domain experts when necessary.
Moreover, staying updated with the latest software developments and advancements is essential for overcoming limitations effectively. SolidWorks regularly releases updates and patches to address bugs, enhance performance, and introduce new features. By keeping abreast of these updates and actively participating in user communities and forums, users can leverage best practices and insights from the broader SolidWorks community to overcome software limitations more effectively.
Furthermore, users can explore interoperability options with other simulation software packages or CAD platforms to complement SolidWorks Simulation's capabilities. Integrating specialized tools for specific analysis types, such as computational fluid dynamics (CFD) or finite element analysis (FEA) plugins, can broaden the scope of simulations that can be performed within the SolidWorks environment.
In essence, understanding SolidWorks Simulation's limitations is a fundamental step in mastering the software and achieving reliable and accurate simulation results. By investing in continuous learning, leveraging supplementary tools and resources, and staying informed about software updates and advancements, users can effectively navigate and overcome the challenges posed by SolidWorks Simulation in their engineering projects.
Meshing Complex Geometries
Meshing complex geometries accurately is essential for obtaining reliable results in SolidWorks Simulation. When dealing with intricate or irregular shapes, inadequate meshing can lead to inaccuracies and computational inefficiencies. To tackle this challenge effectively, users should explore various meshing techniques and tools available in SolidWorks Simulation.
Automatic meshing algorithms are beneficial for simpler geometries, as they can streamline the meshing process and save time. However, for complex scenarios, manual meshing offers greater control and refinement. By manually adjusting mesh parameters, such as element size and distribution, users can ensure that the mesh accurately captures the geometric details and features of the model.
Furthermore, optimizing mesh settings based on the specific analysis requirements is crucial for improving accuracy and computational efficiency. This involves balancing the trade-off between mesh refinement and computational cost. A finer mesh may provide more accurate results but can increase computational time and resource requirements. Conversely, a coarser mesh may reduce computational overhead but may sacrifice accuracy.
Experimenting with different mesh configurations and conducting sensitivity analyses can help users determine the optimal mesh density for their simulations. Additionally, leveraging meshing best practices and guidelines provided by SolidWorks Simulation documentation and training materials can enhance proficiency in meshing complex geometries.
By mastering meshing techniques and diligently optimizing mesh settings, users can overcome the challenges associated with meshing complex geometries in SolidWorks Simulation and ensure the accuracy and reliability of their simulation results.
Interpreting Results Accurately
Interpreting simulation results accurately is another common challenge faced by SolidWorks users. While the software provides comprehensive output data, understanding and extracting meaningful insights from the results can be daunting, especially for complex analyses involving multiple parameters and variables. To overcome this challenge, users should develop a thorough understanding of the physics underlying the simulated behavior and how different parameters influence the results. Visualizing results through animations, graphs, and plots can aid in comprehension and facilitate decision-making. Additionally, conducting sensitivity analyses and validation studies can enhance confidence in the simulation results and their implications for design optimization.
Moreover, it's crucial to consider the context and objectives of the simulation when interpreting results. Users should align their interpretations with the specific goals of the analysis, whether it's assessing structural integrity, thermal performance, or fluid flow characteristics. This requires a holistic approach that integrates technical expertise with domain knowledge and engineering intuition.
Furthermore, users should critically evaluate the assumptions and simplifications made during the simulation process. Sensitivity analyses help identify the sensitivity of results to variations in input parameters, highlighting areas of uncertainty or potential error. Validation studies involve comparing simulation results with experimental data or theoretical predictions to assess the accuracy and reliability of the simulation model.
In essence, interpreting simulation results accurately requires a combination of technical proficiency, critical thinking, and domain expertise. By leveraging visualization tools, conducting thorough analyses, and validating results rigorously, users can extract actionable insights from SolidWorks Simulation and make informed decisions to optimize design performance and efficiency.
Optimizing Computational Resources
To mitigate the challenge of demanding computational resources in SolidWorks Simulation, users should optimize their simulation setups and workflows. This optimization involves several key strategies aimed at maximizing computational efficiency. Firstly, users can refine mesh densities to strike a balance between accuracy and computational cost. By adjusting mesh parameters based on the complexity of the geometry and the resolution required for accurate results, users can minimize unnecessary computational overhead.
Furthermore, leveraging symmetry and simplification techniques can significantly reduce the computational burden associated with complex analyses. Identifying symmetrical features or redundant components within the model and exploiting them to reduce the size and complexity of the simulation can lead to substantial gains in computational efficiency without sacrificing accuracy.
Additionally, taking advantage of parallel processing capabilities can dramatically accelerate simulation times for large-scale analyses. By distributing computational tasks across multiple processing cores or utilizing GPU acceleration, users can harness the power of parallel computing to expedite simulations and improve overall productivity.
Moreover, investing in high-performance computing (HPC) resources or cloud-based simulation platforms can provide users with access to scalable computational resources on-demand. These platforms offer the flexibility to scale computing resources according to the specific requirements of the simulation, allowing users to tackle complex analyses efficiently without being constrained by limited hardware resources.
By implementing these optimization strategies, users can effectively mitigate the challenges posed by demanding computational requirements in SolidWorks Simulation, ensuring faster computation times, smoother workflows, and ultimately, more cost-effective project outcomes.
Collaborating and Communicating Results Effectively
Collaborating with team members and stakeholders and effectively communicating simulation results are crucial components of successful project outcomes. In many cases, this task presents a significant challenge, particularly when bridging the gap between technical intricacies and the comprehension levels of non-technical audiences or interdisciplinary teams.
To navigate this challenge, it's imperative for users to employ various communication strategies that enhance clarity and understanding. Visual aids, such as charts, graphs, and simulations, can simplify complex concepts and facilitate comprehension across diverse audiences. Additionally, employing simplified explanations and real-world analogies can help contextualize technical information and make it more accessible to individuals with varying levels of expertise.
Incorporating collaborative tools and platforms into the workflow can also streamline communication and foster teamwork. Solutions like SolidWorks PDM (Product Data Management) or cloud-based project management platforms enable seamless sharing of information, feedback, and updates among team members, regardless of their geographical locations. These tools promote transparency and accountability, ensuring that everyone involved in the project remains informed and aligned throughout the process.
Furthermore, transparent documentation of simulation methodologies, assumptions, and limitations is essential for maintaining credibility and building trust among stakeholders. By clearly articulating the rationale behind simulation decisions and the constraints of the analysis, users can mitigate misunderstandings and instill confidence in the validity of the results.
Overall, effective collaboration and communication are essential pillars of successful SolidWorks Simulation projects. By leveraging a combination of communication strategies, collaborative tools, and transparent documentation practices, users can overcome the challenges associated with conveying technical information and achieve optimal project outcomes.
Conclusion
In conclusion, it is evident that SolidWorks Simulation is a valuable tool for engineers and designers, providing robust capabilities for conducting engineering analysis and validating design concepts. However, navigating through the complexities of simulation assignments can be daunting, with users often facing a multitude of challenges. Nonetheless, with the right approach and strategies, these hurdles can be effectively overcome, allowing users to harness the full potential of SolidWorks Simulation in their projects.
Understanding the limitations of the software is crucial in ensuring realistic expectations and optimal use of resources. By acknowledging the boundaries of SolidWorks Simulation and seeking guidance when needed, users can avoid pitfalls and make informed decisions throughout the simulation process. Moreover, mastering meshing techniques is essential for achieving accurate and reliable results. Whether employing automated meshing algorithms or fine-tuning mesh settings manually, investing time in refining the mesh ensures the fidelity of the simulation model and enhances the validity of the analysis outcomes.
Interpreting simulation results accurately is paramount for deriving meaningful insights and making informed design decisions. Users must not only possess a deep understanding of the underlying physics but also be adept at extracting relevant information from the plethora of output data generated by SolidWorks Simulation. Visualization tools and sensitivity analyses play a vital role in facilitating result interpretation, enabling users to identify critical trends and correlations effectively.
Optimizing computational resources is essential for maximizing efficiency and productivity in simulation workflows. By leveraging parallel processing capabilities, utilizing cloud-based simulation platforms, or investing in high-performance computing resources, users can significantly reduce computation times and expedite the simulation process. Furthermore, streamlining communication and collaboration among team members and stakeholders is essential for project success. Clear and concise documentation, coupled with effective communication strategies, fosters transparency and ensures alignment of goals and expectations throughout the project lifecycle.
In essence, overcoming the challenges associated with SolidWorks Simulation assignments requires a combination of technical expertise, strategic planning, and effective communication. By continuously refining their skills, staying abreast of software advancements, and fostering a collaborative work environment, users can navigate through complex simulation tasks with confidence and unlock the full potential of SolidWorks Simulation in driving innovation and optimizing design solutions. SolidWorks Simulation not only empowers users to validate their designs virtually but also serves as a catalyst for continuous improvement and innovation in the field of engineering and design.