- The Fundamentals of Finite Element Analysis
- Modeling in SolidWorks for FEA
- Applying Boundary Conditions and Loads
- Meshing the Model
- The Power of SolidWorks in FEA
- Efficient Solver Technology
- Visualization and Result Interpretation
- Benefits of Using SolidWorks for FEA Assignments
- Streamlined Workflow
- User-Friendly Interface
- Extensive Material and Load Libraries
- Conclusion
SolidWorks has become a powerful tool for building virtual prototypes and running simulations in the engineering and design fields. Engineers now approach Finite Element Analysis (FEA) assignments in a completely new way thanks to SolidWorks' powerful capabilities and user-friendly interface. The structural integrity and performance of complex objects under various load conditions are examined using FEA, a numerical method. It gives engineers the ability to assess variables like stress distribution, deformation, and heat transfer, giving them important information for design optimization. By offering a complete set of tools that streamline the entire process, SolidWorks excels in FEA. SolidWorks offers a seamless workflow from modelling and applying boundary conditions to effective solver technology and result interpretation, making it an invaluable tool for engineers working on FEA assignments. Engineers can deliver innovative solutions with greater assurance and efficiency by utilizing the power of SolidWorks to optimize designs, significantly lower prototyping costs, and deliver designs. The various facets of SolidWorks' role in FEA assignments will be covered in this blog, along with its advantages and the potential it offers engineers looking to push the limits of design and analysis.
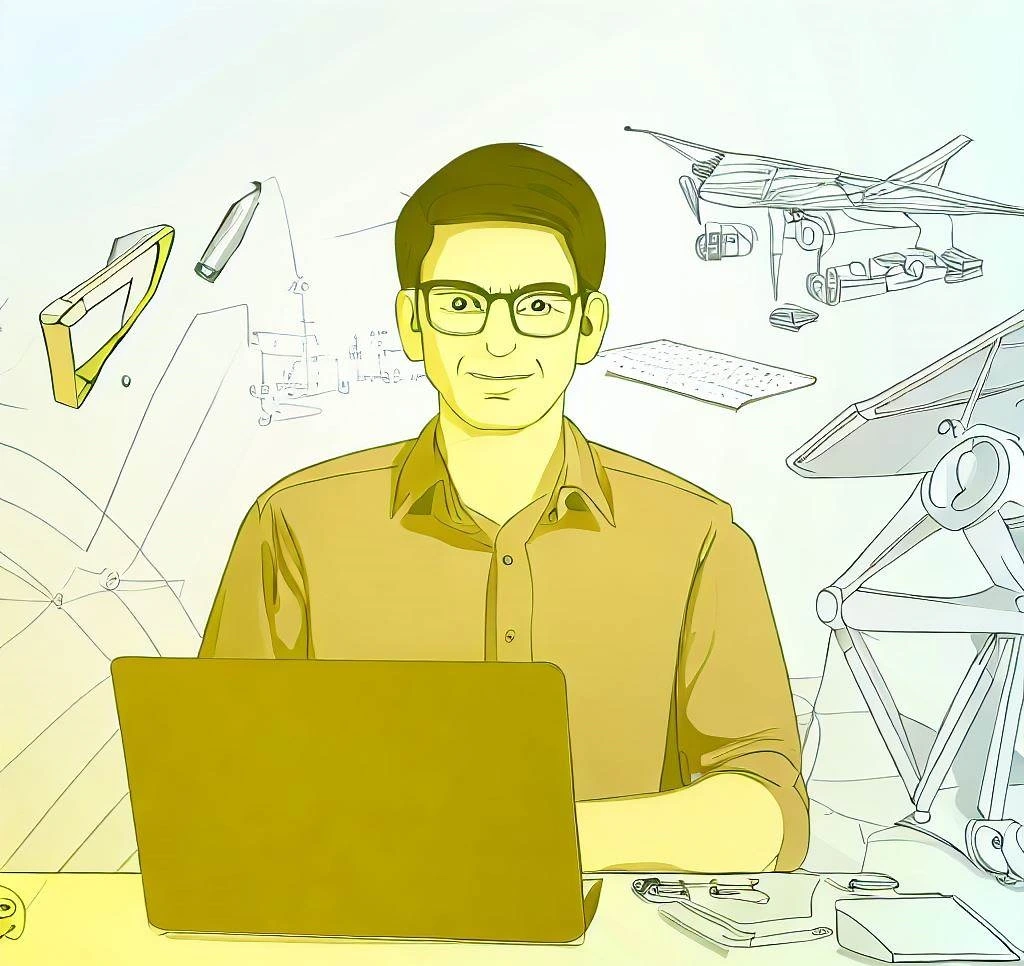
The Fundamentals of Finite Element Analysis
In the fields of engineering and design, Finite Element Analysis (FEA) is a numerical technique that is essential for evaluating the performance and structural integrity of complex objects. A complex object is fundamentally broken down into smaller, connected elements using finite element analysis (FEA), which enables engineers to examine how each of these individual elements behaves under various load scenarios. FEA offers useful insights into the overall performance of the entire structure by analyzing how these elements respond. Engineers can use this analysis technique to examine important elements like stress distribution, deformation, and heat transfer, which are crucial for making wise design decisions. Leading software SolidWorks, which provides a full suite of tools to streamline the analysis process, has emerged as a force to be reckoned with when it comes to carrying out FEA assignments. SolidWorks offers a user-friendly interface and potent features that streamline the FEA workflow, from creating precise 3D models to applying boundary conditions and loads. Engineers can efficiently evaluate and optimize their designs by utilizing the fundamentals of FEA and utilizing the capabilities of SolidWorks, resulting in improved structural integrity, improved performance, and creative engineering solutions.
Modeling in SolidWorks for FEA
A thorough and precise 3D model is necessary before performing a Finite Element Analysis. Engineers can easily create complex geometries thanks to SolidWorks' powerful modelling environment. Users can effectively model the object under consideration by utilizing its user-friendly interface and strong tools, ensuring that all important features and dimensions are accurately represented.
Applying Boundary Conditions and Loads
It is essential to apply the correct boundary conditions and loads to the model in order to get meaningful results. For defining these conditions, SolidWorks provides a complete set of tools. The constraints, forces, pressures, temperatures, and other environmental factors that the structure will experience while in use can be specified by engineers. Engineers can accurately assess the behavior of the design by simulating real-world scenarios with the help of these boundary conditions.
Meshing the Model
The process of meshing involves breaking the model up into smaller finite elements that serve as the foundation for the analysis. Advanced meshing algorithms offered by SolidWorks automatically produce high-quality meshes based on geometry and analysis requirements. Engineers can balance computational resources and mesh density to produce precise results. Tetrahedral, hexahedral, and shell meshing options are just a few of the meshing options that SolidWorks provides, allowing users to select the best mesh type for their particular analysis.
The Power of SolidWorks in FEA
SolidWorks is a powerful tool for Finite Element Analysis (FEA) due to its exceptional capabilities. SolidWorks' effective solver technology, which completes the complex numerical calculations necessary for FEA, is one of its main advantages. Even for large and complex models, the solver uses cutting-edge algorithms to solve complex systems of equations and produces accurate results quickly. This enables engineers to quickly iterate through design variations and effectively optimize their designs. Engineers can interpret the outcomes of their FEA analyses using a variety of visualization tools that SolidWorks offers. Through the use of color-coded contour plots, animations, graphs, and tables, users can quickly view stress distributions, displacements, factors of safety, and other pertinent data. These visual representations make it easier to spot crucial design elements that might need to be changed or improved. Additionally, SolidWorks provides a fully integrated environment for design and analysis, negating the need to import and export models between various software programs. Engineers can move smoothly from the design stage to the analysis phase thanks to this streamlined workflow, which also makes iteration and optimization more effective. SolidWorks empowers engineers to realize optimized designs with greater assurance and efficiency thanks to its user-friendly interface, extensive libraries of materials and loads, and powerful solver technology.
Efficient Solver Technology
The actual numerical calculations necessary for finite element analysis are carried out by SolidWorks' potent solver technology. Its solver makes efficient use of cutting-edge algorithms to solve challenging equation systems. This makes it possible for engineers to get results, even for complex and large models, in a short amount of time. Engineers can quickly iterate through design iterations and efficiently optimize their designs thanks to the solver's accuracy and speed.
Visualization and Result Interpretation
Engineers can interpret the results of their finite element analysis with the help of a variety of visualization tools offered by SolidWorks. Through color-coded contour plots, animations, graphs, and tables, users can view stress distributions, displacements, factors of safety, and other pertinent data. With the help of these visual representations, it is simpler to pinpoint crucial design elements that might need to be changed or improved.
Benefits of Using SolidWorks for FEA Assignments
Engineers and designers can benefit from using SolidWorks for Finite Element Analysis (FEA) assignments in a variety of ways. The streamlined workflow it offers is one of its main benefits. Instead of requiring users to switch between various software programs, SolidWorks provides a fully integrated environment for both design and analysis. Engineers can efficiently move from the design phase to analysis thanks to this seamless integration, which also makes iteration and optimization processes easier. Additionally, SolidWorks has an intuitive user interface that minimizes the learning curve and enables engineers to get started on their FEA assignments right away. The software's robust capabilities are not compromised by the interface's simplicity, making it appropriate for both inexperienced and seasoned users. SolidWorks has an extensive library of materials and loads, which is a very useful feature. There is no longer a need for manual input of material properties because engineers can quickly access and use a variety of material options. This facilitates analysis setup and guarantees accurate FEA representation of real-world behavior. Furthermore, SolidWorks makes use of effective solver technology to carry out the challenging numerical calculations necessary for FEA. Engineers can expedite the analysis process and effectively optimize their designs thanks to the powerful solver's cutting-edge algorithms, which produce accurate results in a short amount of time. Engineers are able to complete FEA assignments with increased efficiency, accuracy, and confidence thanks to SolidWorks' extensive material and load libraries, user-friendly interface, and efficient solver technology.
Streamlined Workflow
A fully integrated environment for design and analysis is provided by SolidWorks. By doing away with the need to import and export models between different software programs, this streamlines the workflow. Engineers can move smoothly from the design stage to the analysis phase, enabling effective iteration and optimization.
User-Friendly Interface
SolidWorks has an intuitive, user-friendly interface that is simple to use. The learning curve for engineers who are new to the software is lowered as a result, allowing them to begin working on their FEA assignments more quickly. The software's robust capabilities are not compromised by the interface's ease of use, making it suitable for both inexperienced and seasoned users.
Extensive Material and Load Libraries
Engineers can use SolidWorks' extensive library of materials and loads for their FEA assignments. This eliminates the need for manual material property input and streamlines the setup process for analyses. A wide variety of material options are available in the library, guaranteeing an accurate representation of the design's behavior in real-world settings.
Conclusion
Finite Element Analysis (FEA) has made SolidWorks an essential tool that has completely changed how engineers approach design and engineering assignments. Engineers can confidently and effectively conduct FEA and optimize their designs with SolidWorks' powerful capabilities, user-friendly interface, and comprehensive set of tools. SolidWorks offers a streamlined workflow that eliminates the need for multiple software packages, enables smooth iteration and optimization processes, and covers everything from modelling and applying boundary conditions to efficient solver technology and result interpretation. SolidWorks' extensive material and load libraries make analysis setup simple and guarantee the accurate representation of real-world behavior. Additionally, the strong solver technology in SolidWorks completes difficult numerical calculations quickly, enabling engineers to get precise results quickly. Engineers can significantly lower prototyping costs, speed up the design process, and deliver cutting-edge solutions that satisfy performance and structural integrity requirements by utilizing the power of SolidWorks. Engineers can make well-informed design decisions, optimize designs, and improve efficiency and confidence in their engineering solutions thanks to SolidWorks, which truly unleashes the potential of FEA. SolidWorks has become a top FEA tool thanks to its extensive capabilities, enabling engineers to push the limits of design and analysis in the name of excellence.