- The Basics of Solidworks Simulation
- Structural Analysis
- Thermal Analysis
- Fluid Flow Analysis
- Optimizing Design Performance
- Design Validation
- Parametric Studies
- Enhancing Collaboration and Communication
- Design Review and Feedback
- Collaboration with Manufacturing
- Design Optimization and Iterative Refinement
- Conclusion
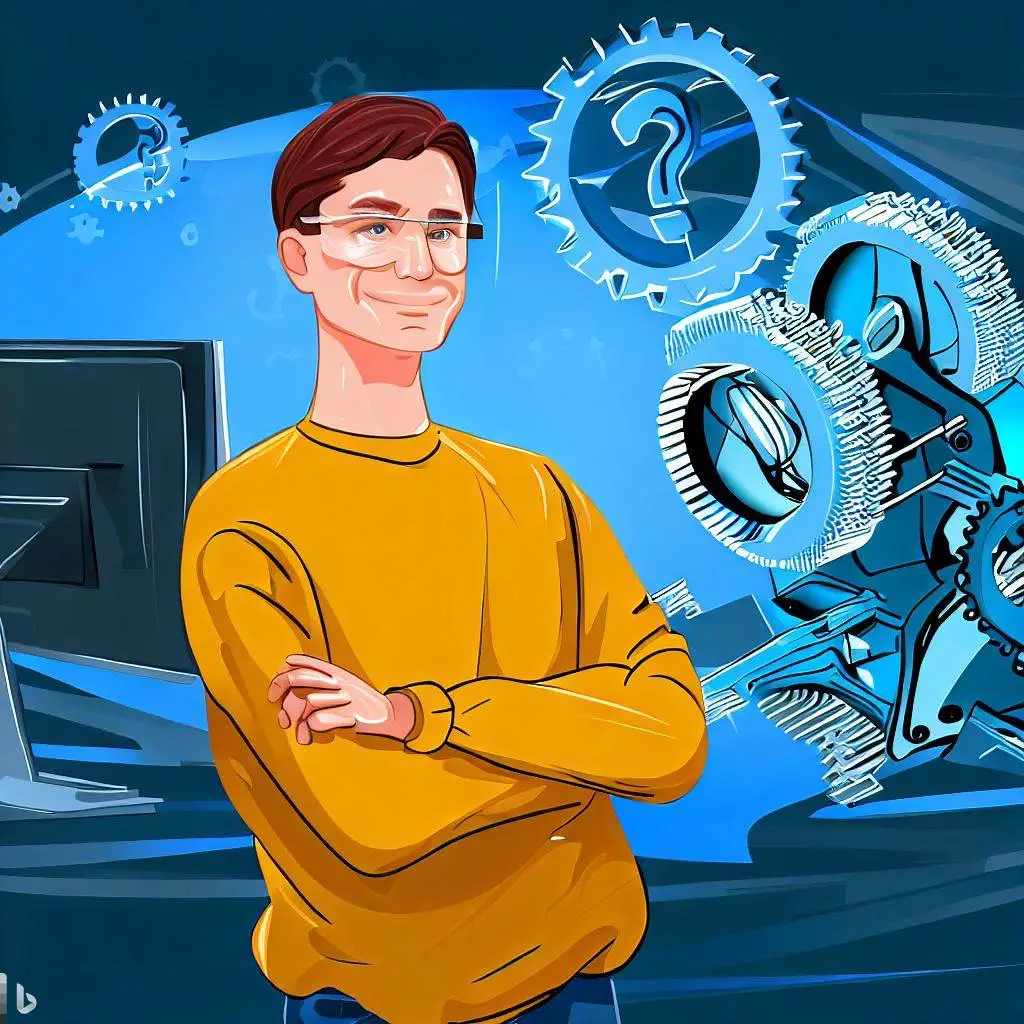
Engineering must include design optimization because it enables the creation of effective and high-performing products. Solidworks Simulation emerges as a potent tool in the field of computer-aided design (CAD) that is essential to achieving goals for design optimization. Solidworks Simulation offers a wide range of simulation assignments and capabilities that enable engineers to evaluate, analyze, and improve designs for optimum performance. In order to shed light on Solidworks Simulation's influence on engineering procedures and the benefits it offers designers and manufacturers, this article will examine the significant role it plays in design optimization assignments. Engineers can evaluate the behavior and characteristics of their designs using the comprehensive suite of simulation tools provided by Solidworks Simulation, allowing for more informed decision-making and performance optimization. We will examine various aspects of Solidworks Simulation's contribution to design optimization throughout this article, highlighting its profound influence on the engineering field and its capacity to provide real advantages to professionals in the sector.
The Basics of Solidworks Simulation
Engineers can simulate and analyze the behavior of their designs in terms of structure, thermal dynamics, and fluid flow using the Solidworks assignment help Simulation module, which is seamlessly integrated into the Solidworks CAD software package. Before investing in the pricey and time-consuming process of physical prototyping, engineers can explore and evaluate various design variations, material options, and operating conditions by utilizing the power of Solidworks Simulation. This capability enables effective design optimization and lowers the possibility of problems developing during the production stage. Engineers can define the necessary parameters for analysis, such as loads, constraints, and material properties, using Solidworks Simulation's user-friendly interface. Following that, the software makes use of cutting-edge numerical techniques, such as finite element analysis (FEA), to precisely simulate and forecast how the design will behave in real-world scenarios. Solidworks Simulation equips engineers to make wise decisions, improve design performance, and ultimately deliver better products to the market by offering this extensive collection of simulation tools. Let's explore the main attributes and capabilities of Solidworks Simulation:
Structural Analysis
Engineers can evaluate the structural performance and integrity of their designs using Solidworks Simulation's structural analysis tools. Engineers can simulate how their designs behave under various real-world scenarios by applying loads, boundary conditions, and material properties. Solidworks Simulation computer stress, displacement, strain, and factor of safety using finite element analysis (FEA) methods. Designers can pinpoint weak spots, maximize material usage, and make wise decisions to improve product performance thanks to this invaluable information. Solidworks Simulation assists in the development of sturdy and dependable designs by accurately assessing structural behavior.
Thermal Analysis
In order to assess heat dissipation and thermal behavior in components and assemblies, thermal analysis is essential. For the purpose of simulating heat transfer, conduction, convection, and radiation within designs, Solidworks Simulation offers a variety of tools. Engineers can optimize designs for effective thermal management by analyzing temperature distributions, gradients, and heat transfer rates. This capability is extremely useful for sectors like electronics, automotive, and aerospace where overheating can result in performance degradation or even failure. Engineers can eliminate thermal problems and guarantee ideal thermal performance with Solidworks Simulation, producing dependable and durable products.
Fluid Flow Analysis
Engineers can examine fluid flow characteristics within their designs thanks to Solidworks Simulation. When it comes to enhancing the performance of systems that use liquids or gases, like pumps, valves, and cooling systems, this capability is invaluable. Engineers can identify inefficient areas by simulating fluid flow patterns, pressure drops, and velocity profiles. They can streamline designs and improve overall performance thanks to this knowledge. Engineers can make the best design choices and achieve the best system performance by visualizing and analyzing fluid flow behavior. Engineers can optimize their designs and guarantee the smooth and effective flow of fluids within their systems with the help of Solidworks Simulation.
Optimizing Design Performance
More than just analysis tools, Solidworks Simulation offers a strong platform for enhancing design performance and successfully achieving design goals. Engineers can investigate various design configurations, materials, and parameters through Solidworks Simulation to improve the effectiveness and efficiency of their designs. Engineers can find areas for improvement and make wise decisions to optimize key components by putting designs through virtual testing and analysis. Engineers can optimize their designs for maximum performance thanks to the software's thorough feedback on stress distribution, heat transfer, fluid flow, and other factors. Furthermore, Solidworks Simulation makes parametric studies possible, enabling designers to systematically research how design variations affect performance. Engineers can speed up the design optimization process and produce products that meet or exceed performance goals while cutting costs and development time by utilizing the capabilities of Solidworks Simulation. Examining Solidworks Simulation's contribution to design optimization will help:
Design Validation
The rigorous testing and analysis that Solidworks Simulation performs on designs help to validate them. Engineers can evaluate how designs perform in various scenarios by simulating real-world conditions. Engineers can optimize designs to guarantee the highest performance and reliability by identifying potential design flaws and areas of concern. Solidworks Simulation's virtual validation process eliminates the need for expensive physical prototyping and testing, saving time and money. Engineers can confidently validate their designs and make wise decisions to produce high-quality products by utilizing the power of simulation.
Parametric Studies
Engineers are able to systematically explore design variations thanks to parametric studies, a crucial component of Solidworks Simulation. Engineers can experiment with design parameters like dimensions, materials, and boundary conditions in Solidworks Simulation to determine how they affect the performance of the design. Engineers can learn a lot about how various combinations of design parameters affect the overall performance of the product by conducting parametric studies. With this iterative method of design optimization, engineers can find the best answers to particular problems and constraints. Engineers can significantly increase the effectiveness of the design optimization process and achieve optimal results that meet or exceed performance objectives by utilizing the parametric study capabilities of Solidworks Simulation.
Enhancing Collaboration and Communication
Collaboration and communication among parties involved in the design optimization process are significantly improved by Solidworks Simulation. Solidworks Simulation enables efficient teamwork and knowledge sharing throughout the design cycle by seamlessly integrating with the Solidworks CAD software package. Engineers can create clear and understandable representations of simulation results, such as stress contours, temperature distributions, and fluid flow patterns, thanks to the software's visualization capabilities. These visual aids make it easier for non-technical stakeholders to understand complex design concepts and the implications of simulation results. Solidworks Simulation encourages collaboration among design teams, manufacturing departments, and other stakeholders by offering a common forum for sharing and discussing simulation results. This, in turn, results in better-informed decision-making and improved design outcomes.
Design Review and Feedback
Design review and feedback procedures greatly benefit from the visual representations of simulation results provided by Solidworks Simulation. For designers and engineers, communicating complex ideas and findings to stakeholders is made simpler by these visualizations. Teams can get useful feedback, deal with issues, and jointly decide on designs by sharing simulation results. Solidworks Simulation's visual nature makes it possible for stakeholders to comprehend how the design behaves and performs, fostering effective communication and enhancing the entire design review process.
Collaboration with Manufacturing
The seamless collaboration between the design and manufacturing teams is made possible by Solidworks Simulation. Engineers can spot potential manufacturing problems early on in the design process by simulating various manufacturing processes, such as sheet metal forming or injection molding. This early detection of manufacturing limitations enables designers to manufacturability-optimize their designs, ensuring that the final product is not only optimized for performance but also feasible to produce efficiently and affordably. Engineers can anticipate and address manufacturing challenges with Solidworks Simulation, enabling more seamless transitions from design to production. Solidworks Simulation accelerates the design optimization process and boosts team collaboration between the design and manufacturing teams, which benefits engineering projects as a whole.
Design Optimization and Iterative Refinement
Engineers have a solid platform for design optimization and iterative improvement with Solidworks Simulation. Engineers can investigate a variety of design iterations and assess their performance by utilizing sophisticated algorithms and analysis tools. Solidworks Simulation enables effective searching for the best design configurations that meet particular performance goals by allowing the definition of objectives, constraints, and variables. Engineers can quickly improve their designs by automating the iteration process and making decisions based on the software's feedback. Engineers can continuously enhance their designs using this iterative refinement process, maximizing their effectiveness, dependability, and functionality. Engineers can simplify their development procedures, cut costs, and ultimately produce high-quality products that meet or exceed customer expectations by using Solidworks Simulation as a tool for design optimization.
Conclusion
In conclusion, Solidworks Simulation provides engineers with a variety of tools to evaluate and enhance their designs, serving as a crucial asset in design optimization assignments. Solidworks Simulation enables engineers to optimize design performance, reduce prototyping costs, and increase product reliability through its capabilities in structural analysis, thermal analysis, and fluid flow analysis. Additionally, the software's ability to promote stakeholder collaboration and communication streamlines the process of design optimization, resulting in improved efficiency and the completion of engineering projects. Designers and manufacturers can create designs that not only meet performance goals but also exceed client expectations by utilizing the strength of Solidworks Simulation. Solidworks Simulation has evolved into a crucial tool in the quest for design innovation and excellence thanks to its extensive feature set and seamless workflow integration.