- Importance of Simulation in Sheet Metal Design
- Ensuring Structural Integrity
- Evaluating Performance and Functionality
- Minimizing Cost and Time
- Types of Simulation in Solidworks for Sheet Metal Assignments
- Structural Simulation
- Motion Simulation
- Thermal Simulation
- Benefits of Simulation in Solidworks Sheet Metal Assignments
- Improved Design Efficiency
- Enhanced Design Optimization
- Cost and Time Savings
- Conclusion
With its extensive set of tools and features, Solidworks, a popular computer-aided design (CAD) programmed in the engineering and manufacturing sectors, empowers designers and makes it simple to create complex sheet metal designs. In order to ensure compliance with the desired functionality and performance requirements, accurate and efficient sheet metal designs require more than just the ability to draw shapes and dimensions. This is the precise situation where simulation becomes essential. We will explore the significant role of simulation in sheet metal assignments in this blog post, highlighting its essential role in the testing and validation process. Designers can virtually analyze and assess the behavior of sheet metal components under various conditions and loads by using simulation techniques. They can use this to locate areas of high stress, potential weaknesses, and deformation susceptibility. Furthermore, simulation enables the optimization of variables like material selection and thickness, improving structural integrity and achieving the best design performance. Solidworks users can reduce the likelihood of failure, cut down on expensive iterations, and speed up the design iteration process, all of which will lead to more effective and reliable sheet metal designs in the end.
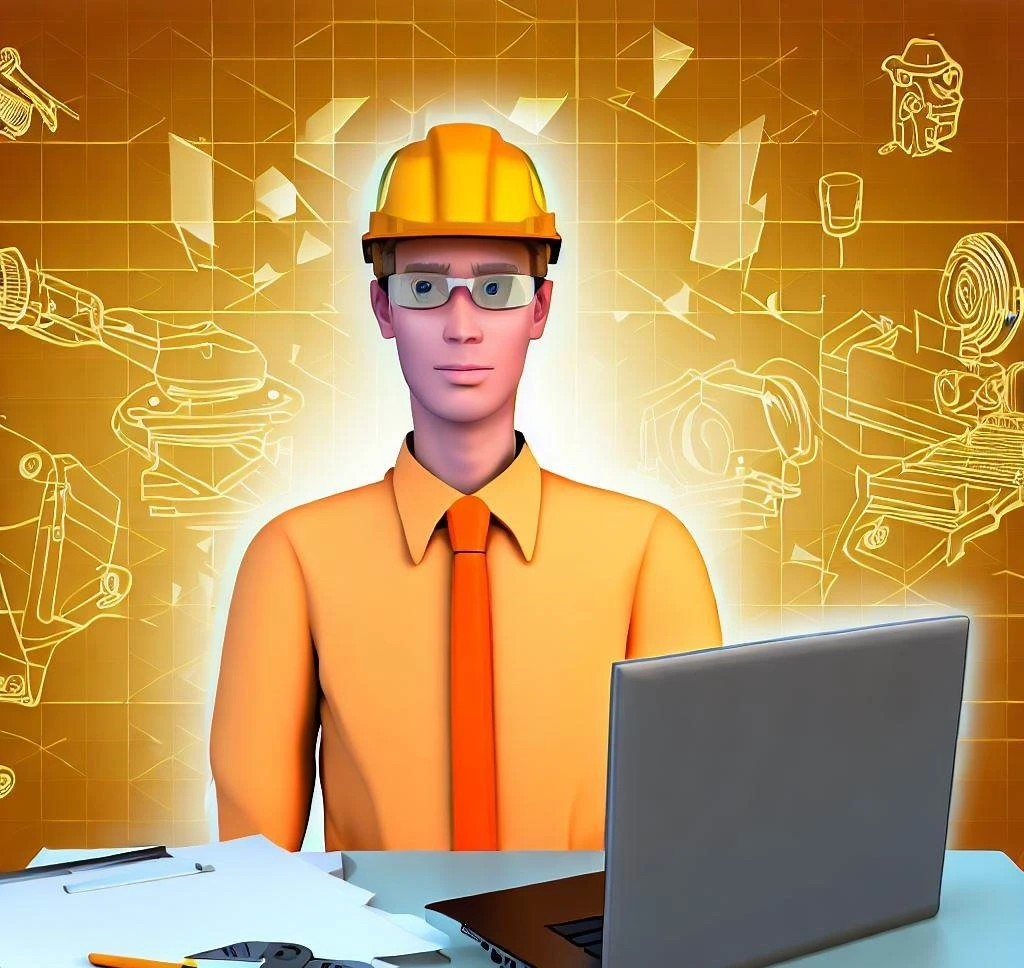
Importance of Simulation in Sheet Metal Design
Understanding the need for simulation in the first place is crucial before delving into the specifics of simulation in sheet metal assignments. Throughout their operational life, sheet metal designs frequently have to withstand a variety of loads, including bending, stretching, and twisting. Without adequate testing and validation, the finished product might not hold up to these loads, resulting in expensive repairs, delays in production, and decreased safety. Engineers and designers can make educated decisions to enhance the design and performance of sheet metal components by simulating the behavior of those components under various conditions. Simulated testing of the designs enables the detection of potential weak points, areas of high stress, and deformation susceptibility. It aids in the optimisation of variables like material choice, thickness, and reinforcements by offering insightful information about how the design will respond to actual environmental conditions. Engineers can ensure the structural soundness and performance of sheet metal designs through simulation, resulting in dependable and effective products.
Ensuring Structural Integrity
Structural integrity is one of the main goals of simulation in sheet metal design. Engineers can locate potential weak points, areas of high stress, and regions susceptible to deformation by subjecting the design to virtual testing. Designers can choose the right material, thickness, and other elements that contribute to structural strength by accurately simulating the loads and constraints that the sheet metal component will encounter in actual situations. By optimizing the structural integrity, sheet metal components can be manufactured with confidence, knowing they will meet the necessary strength and durability requirements, and it also leads to optimized designs that use the least amount of material necessary.
Evaluating Performance and Functionality
In order to assess the performance and functionality of sheet metal designs, simulation is essential. Sheet metal components must satisfy specific requirements, such as aerodynamic effectiveness or crashworthiness, in sectors like automotive and aerospace. Engineers can evaluate the design's performance in relation to these criteria by simulating how it will behave under different operating conditions. Before production, they can alter the design to enhance the performance and functionality of the sheet metal component, such as by optimising the shape or adding reinforcements. Additionally, simulation enables the exploration of potential trade-offs and the testing of various design iterations to achieve the desired performance characteristics. Engineers can improve the design using this iterative process, which also helps to guarantee that the final product will perform as expected or better.
Minimizing Cost and Time
Simulation reduces the time and costs involved in the design process. Engineers can avoid expensive rework and iterations by finding design flaws and performance problems early in the design process rather than finding them during physical prototyping or after the product is in production. Virtual testing and validation made possible by simulation speed up the design iteration process by obviating the need for costly physical prototypes. For manufacturers, this means a shorter time to market and lower costs. Additionally, simulation helps in waste reduction, cost reduction, and material use optimisation. Engineers can find the most effective design that satisfies the necessary performance criteria while using the least amount of material by simulating various material thicknesses and configurations. Promoting sustainable design principles, not only lowers material costs but also has a beneficial effect on the environment.
Types of Simulation in Solidworks for Sheet Metal Assignments
Numerous simulation tools designed specifically for sheet metal projects are available through Solidworks. With the aid of these tools, engineers can precisely simulate the behaviour of sheet metal components and adjust their designs as necessary. Engineers can make sure that their sheet metal designs have the desired performance, structural integrity, and manufacturability by using simulation. Structural simulation, one of the notable simulation features in Solidworks, enables engineers to examine the structural behaviour of sheet metal designs under various loads and boundary conditions. Engineers can evaluate crucial elements like stress distribution, deformation, and safety considerations by virtually applying forces and constraints to the model. This information helps in locating weak spots, improving the design, and guaranteeing the sheet metal component's overall robustness. Engineers can confidently optimise their sheet metal designs for performance and functionality using Solidworks' simulation tools. Let's look at some of the most important Solidworks sheet metal simulation features.
Structural Simulation
Designers can examine the structural behavior of sheet metal designs under various loads and boundary conditions thanks to Solidworks' structural simulation capabilities. It aids in assessing elements like safety factors, deformation, and stress distribution. Engineers can examine how the design will respond to real-world conditions by applying fictitious forces and constraints to the model. They are able to spot potential weak spots, high-stress zones, and areas that require reinforcement. The design can be improved for performance and structural integrity using this information. In order to create lightweight and effective sheet metal designs, structural simulation also helps in identifying areas where material can be strategically removed to reduce weight while maintaining sufficient strength.
Motion Simulation
Engineers can examine the motion and interaction of sheet metal components within an assembly using motion simulation in Solidworks. It assists with assessing elements like interference, clearance, and range of motion. Engineers can locate potential collision points, interferences, and immobilized regions by simulating the motion of the design. To ensure proper sheet metal component fit, functionality, and assembly, this information is essential. Engineers can optimize designs for smooth operation and prevent potential problems during assembly and use by using motion simulation to confirm that sheet metal parts can move as intended without interference.
Thermal Simulation
Solidworks's thermal simulation tools let engineers examine the heat transfer and thermal behavior of sheet metal designs. This is crucial for parts that operate in high-temperature conditions or go through thermal cycling. Engineers can locate potential hotspots and vulnerable regions by simulating the heat flow and temperature distribution. They can also optimize the design for thermal performance. Thermal simulation ensures the durability of sheet metal components by assisting in the prevention of thermal failures like overheating or thermal deformation. It enables designers to incorporate suitable heat dissipation components, like cooling channels or heat sinks, to maintain ideal operating temperatures and raise the overall performance and dependability of the sheet metal design.
Benefits of Simulation in Solidworks Sheet Metal Assignments
When it comes to sheet metal assignments in Solidworks, simulation offers a number of advantages. Engineering professionals can improve the overall effectiveness and quality of their sheet metal designs by incorporating simulation into the design process. Improved design efficiency is one of the simulation's main benefits. Engineers can quickly and accurately iterate designs by using virtual testing and validation to detect performance problems and design flaws early on. This shortens the development time by streamlining the design process. Additionally, simulation allows for improved design optimisation. Engineers can pinpoint problem areas and optimise elements like material choice, thickness, and structural reinforcements by precisely simulating the behaviour of sheet metal components. As a result, sheet metal designs become more reliable and economical. By obviating the need for pricey physical prototypes and lowering the likelihood of expensive design iterations, simulation also helps to save money and time. In general, simulation is essential to Solidworks sheet metal projects because it helps engineers produce high-quality designs that satisfy performance specifications while reducing costs and time-to-market. Let's look at a few of the most important benefits of using simulation in the design process.
Improved Design Efficiency
Simulation makes it possible to test and validate sheet metal designs virtually, doing away with the need for pricey physical prototypes. Engineers can make wise design decisions and iterate quickly by spotting design flaws and performance issues early in the design stage. This results in faster development times and more effective design processes. With the aid of simulation, designers can quickly test various design iterations and assess their effects on performance, ensuring that the final design satisfies the required criteria.
Enhanced Design Optimization
Engineers can improve the structural integrity, performance, and functionality of their designs by accurately simulating the behavior of sheet metal components. Simulated results can be used to pinpoint potential areas for improvement, such as maximizing material thickness, strengthening vulnerable areas, or removing pointless weight. Engineers can achieve the desired design objectives by making educated decisions by understanding how various design decisions affect the performance of the sheet metal component. These design improvements lead to efficient and affordable sheet metal components that meet or surpass the necessary performance requirements.
Cost and Time Savings
The design process is significantly less expensive and time-consuming with simulation. Manufacturers can release their products to the market more quickly and for less money by doing away with the need for physical prototypes and cutting down on iterations. Engineers can identify and fix design problems early on with simulation, preventing expensive failures, rework, and production delays. Manufacturers can minimise material waste, cut down on manufacturing errors, and improve the production process by optimising the design in the virtual environment. As a result, manufacturers gain a competitive edge in the market and experience significant cost savings over the course of the product's lifecycle.
Conclusion
In Solidworks sheet metal projects, simulation is essential because it enables engineers to test and validate designs before they are manufactured. Engineers can guarantee structural integrity, assess performance and functionality, and reduce the cost and time involved in the design process by using the various simulation tools offered by Solidworks. Simulated testing and validation enable the reduction of design iterations and the need for expensive physical prototypes. This shortens the development cycle and increases design efficiency. Additionally, simulation aids in improving design optimisation by highlighting potential areas for improvement and enhancing the performance, strength, and weight of the sheet metal components. Engineers can produce strong, effective, and dependable sheet metal designs that satisfy the required performance standards by utilising the power of simulation. A simulation is a crucial tool for sheet metal design in Solidworks because of its advantages, including increased design efficiency, improved design optimisation, and cost and time savings. It enables engineers to make knowledgeable design choices and bring high-quality products to market more quickly and affordably.