- Introduction to SolidWorks Simulation Study Cases
- Case 1: Virtual Wall
- Steps to Approach:
- Insights and Applications:
- Case 2: Bonded
- Steps to Approach:
- Insights and Applications:
- Case 3: Pin Connect
- Steps to Approach:
- Insights and Applications:
- Recommendations for Practical Application
- Future Work and Advanced Considerations
- Conclusion
SolidWorks Simulation stands out as a robust tool empowering engineers and designers to foresee how their designs will perform across diverse conditions even before physical manufacturing commences. Competence in navigating SolidWorks Simulation study cases is pivotal for ensuring precision in analysis and achieving superior design outcomes. Throughout this guide, we delve into three fundamental study cases—Virtual Wall, Bonded, and Pin Connect—offering detailed instructions on configuring simulations, deciphering outcomes, and guiding informed design choices.
Each study case illuminates distinct constraints and their implications on structural behavior. For instance, the Virtual Wall scenario exemplifies rigid constraints that prohibit translational and rotational movement, thereby spotlighting stress concentration points and minimal deformation characteristics. In contrast, the Bonded case introduces rotational freedom while preventing separation, illustrating how such flexibility can affect stress distribution and deformation patterns. Meanwhile, the Pin Connect case allows translational movement while constraining rotation, providing insights into stress distribution akin to the Virtual Wall scenario but with varied deformation profiles.
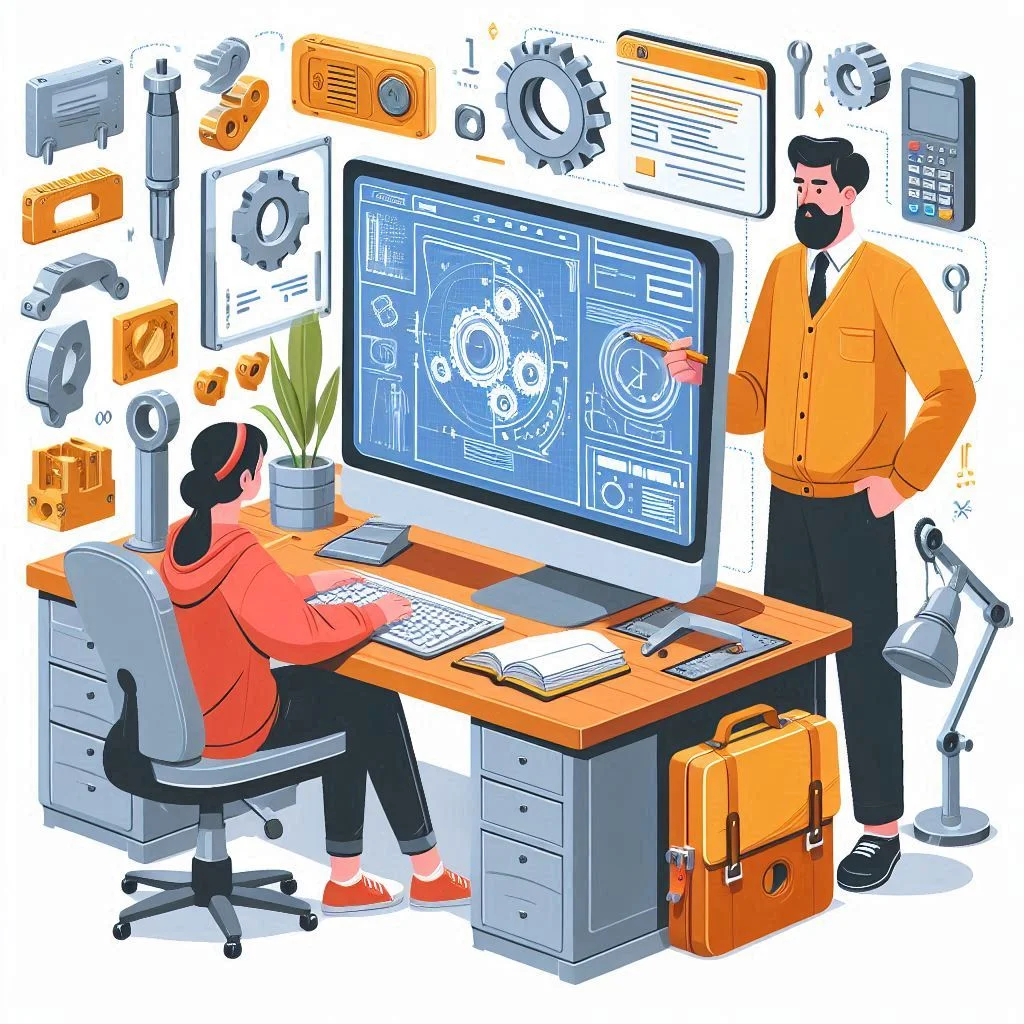
By comprehensively exploring these scenarios, engineers gain proficiency in leveraging SolidWorks Simulation to optimize designs early in the development phase. This approach not only minimizes the need for costly physical prototypes but also accelerates the iterative design process. Simulation Assignment Help is crucial as SolidWorks Simulation's ability to simulate real-world conditions accurately empowers designers to anticipate challenges and refine solutions preemptively, ensuring robust and efficient designs.
SolidWorks Simulation is not merely a software tool but a strategic asset in the arsenal of modern engineering and design. Mastery of its study cases equips professionals to tackle complex challenges with confidence, fostering innovation and efficiency in product development. As you integrate these principles into your practice, embrace the iterative nature of simulation-driven design, continuously refining and enhancing your understanding through practical application and exploration of advanced features.
Introduction to SolidWorks Simulation Study Cases
SolidWorks Simulation offers several study cases that simulate different types of constraints and connections between components. These simulations are essential for engineers to predict critical factors such as stress distribution, deformation, and overall structural integrity before physical prototypes are made. By virtually testing designs under various conditions, SolidWorks Simulation enables engineers to make informed decisions early in the design process, reducing costs and time associated with iterative testing and modifications.
In this guide, we will explore three fundamental study cases commonly used in SolidWorks Simulation: Virtual Wall, Bonded, and Pin Connect. These cases serve as foundational tools for understanding how different contact types affect the behavior of mechanical systems. By mastering these simulations, engineers gain insights into how designs respond to external forces and constraints, empowering them to optimize performance and reliability. Through practical examples and step-by-step instructions, we aim to equip you with the skills needed to apply SolidWorks Simulation effectively in your engineering projects.
Case 1: Virtual Wall
Description: In this scenario, the object (let's say a table) is constrained by a virtual wall on one side. The virtual wall acts as a rigid barrier that prevents the table from penetrating through it.
Objective: Understand how the virtual wall constraint affects stress distribution and deformation in the table.
Steps to Approach:
1. Setting Up the Study:
- Geometry and Materials: Begin by creating the 3D model of the table in SolidWorks. Assign appropriate material properties to the table and other components involved.
- Load and Constraints: Apply a load to the table, such as a downward force of 1000 N. Define the virtual wall constraint to restrict movement in the specified direction (e.g., in the x-direction).
- Meshing: Generate a mesh that discretizes the geometry for accurate simulation results.
2. Running the Simulation:
- Execute the simulation within SolidWorks Simulation module.
- Monitor the progress and ensure convergence of the solution.
- Review the stress and deformation results post-simulation.
3. Interpreting Results:
- Analyze the stress distribution across the table surface. Note areas of high stress concentrations.
- Evaluate the maximum deformation experienced by the table under the applied load.
- Discuss how the virtual wall constraint influences stress levels and deformation patterns.
Insights and Applications:
- Virtual wall constraints are ideal for scenarios where components must remain fixed in position without any movement.
- Stress tends to concentrate around areas where the virtual wall constraint is applied, leading to potentially high stress levels.
- Deformation is typically minimized due to the rigid nature of the virtual wall constraint.
Case 2: Bonded
Description: Here, the table is bonded to the ground surface. Bonded contact allows the table to rotate but prevents any separation between the table and the ground.
Objective: Evaluate how bonded contact affects stress distribution and deformation compared to the virtual wall scenario.
Steps to Approach:
1. Setting Up the Study:
- Use the same table model and material properties as in Case 1.
- Apply the same load and ensure consistent boundary conditions except for changing the contact type to bonded.
- Define bonded contact between the table and the ground to allow rotational freedom but prevent separation.
2. Running the Simulation:
- Execute the simulation and monitor for convergence.
- Check stress and deformation results post-simulation.
3. Interpreting Results:
- Compare stress distribution and deformation patterns with those from the virtual wall case.
- Discuss how rotational freedom affects stress levels and deformation characteristics.
- Highlight differences in stress concentrations and deformation profiles between bonded and virtual wall constraints.
Insights and Applications:
- Bonded contact is suitable when rotational freedom is necessary but separation is to be prevented.
- Stress distribution may vary compared to the virtual wall case due to rotational degrees of freedom.
- Deformation levels might be higher under bonded contact conditions compared to virtual wall constraints.
Case 3: Pin Connect
Description: In this case, the table is pin-connected to the ground. This allows the table to translate in certain directions but restricts rotational movement.
Objective: Analyze stress and deformation patterns under pin-connected constraints and compare them with previous cases.
Steps to Approach:
1. Setting Up the Study:
- Maintain consistency in model geometry and material properties.
- Apply the same load as in previous cases.
- Define pin connections to allow translation in specified directions while restricting rotation.
2. Running the Simulation:
- Execute the simulation process and ensure accurate meshing.
- Monitor solution convergence and runtime performance.
3. Interpreting Results:
- Evaluate stress distribution and deformation patterns under pin connection constraints.
- Compare results with virtual wall and bonded cases to identify similarities and differences.
- Discuss how translation-only constraints influence stress levels and deformation characteristics.
Insights and Applications:
- Pin connections are beneficial when limited translation is required without rotational movement.
- Stress distribution may resemble the virtual wall case due to restricted degrees of freedom.
- Deformation patterns can vary based on the specific directions allowed for translation.
Recommendations for Practical Application
Based on the findings from these study cases, here are practical recommendations for applying SolidWorks Simulation in engineering projects:
- Choosing the Right Contact Type: Select the appropriate contact type based on design requirements. Use virtual wall for fixed components, bonded for rotational flexibility, and pin connect for restricted translation.
- Understanding Stress and Deformation: Interpret stress and deformation results critically. High stress areas may indicate potential failure points, while deformation insights help refine designs for better performance.
- Iterative Design Improvement: Use simulation results iteratively to refine designs. Adjust geometry, material properties, or contact conditions based on simulation outcomes to optimize performance.
- Documentation and Reporting: Maintain detailed documentation of simulation setups, results, and conclusions. Clear reporting ensures effective communication and decision-making within design teams.
Future Work and Advanced Considerations
To further enhance your understanding and application of SolidWorks Simulation, consider exploring the following areas for future study and advanced applications:
- Detailed Stress Analysis: Conduct more detailed studies on stress distribution within components. Explore methods to mitigate stress concentrations and optimize designs accordingly.
- Parameter Sensitivity Analysis: Investigate the effects of varying parameters such as material properties, loading conditions, or contact coefficients on stress and deformation outcomes.
- Dynamic Analysis: Extend your simulations to dynamic scenarios where time-varying loads or vibrations affect structural behavior. SolidWorks Simulation offers capabilities for dynamic analysis that can simulate real-world operational conditions.
- Thermal Analysis: Incorporate thermal effects into your simulations to understand how temperature variations impact structural integrity and material performance.
Conclusion
SolidWorks Simulation study cases—virtual wall, bonded, and pin connect—are fundamental tools that empower engineers and designers to accurately predict and optimize mechanical designs. Mastery of these study cases enables professionals to create designs that are not only robust and efficient but also cost-effective and faster to market.
Practical application of SolidWorks Simulation involves more than just theoretical knowledge; it requires hands-on experience and a willingness to experiment with different scenarios. By analyzing simulation results critically, engineers can uncover potential design flaws early in the development process, leading to iterative improvements that enhance product performance and reliability.
Continuous improvement in simulation techniques is essential for staying competitive in the field of engineering. Engineers who excel in SolidWorks Simulation can confidently tackle complex challenges, innovate new solutions, and contribute significantly to the advancement of their respective industries.
This guide aims to provide valuable insights and practical guidance on leveraging SolidWorks Simulation study cases effectively. For further skill development, consider exploring additional resources, participating in training programs, and engaging in community forums to exchange knowledge and best practices in simulation-driven design.