- Assembly Modeling in SolidWorks
- Approaches to Assembly Modeling
- 1. Top-Down Approach:
- 2. Bottom-Up Approach:
- Choosing the Right Approach
- Hybrid Approach:
- A Case Study: Using Both Approaches
- Top-Down Approach:
- Bottom-Up Approach:
- Conclusion
SolidWorks is a powerful and widely used computer-aided design (CAD) software that is essential for engineers, designers, and students in various fields. One of the key features of SolidWorks is assembly modeling, which allows users to create complex assemblies of parts and components, facilitating the design of intricate machinery, products, and systems. In this blog post, we will delve into the world of assembly modeling in SolidWorks, focusing on two primary approaches: top-down and bottom-up. If you need assistance to complete your SolidWorks assembly assignment, don't hesitate to reach out for help.
Assembly Modeling in SolidWorks
Before we dive into the specifics of top-down and bottom-up approaches, it's essential to understand what assembly modeling is and why it's crucial. Assembly modeling is the process of creating a virtual representation of a product or system by combining individual parts and components into a single, interconnected model. This representation enables designers and engineers to evaluate how the parts fit together, check for interferences, and assess the overall functionality of the assembly.
In SolidWorks, assembly modeling provides a structured environment for designing and visualizing complex products. The software allows users to create, modify, and analyze assemblies with ease. This is particularly beneficial for students who are learning how to design and assemble various mechanical systems as part of their coursework.
Approaches to Assembly Modeling
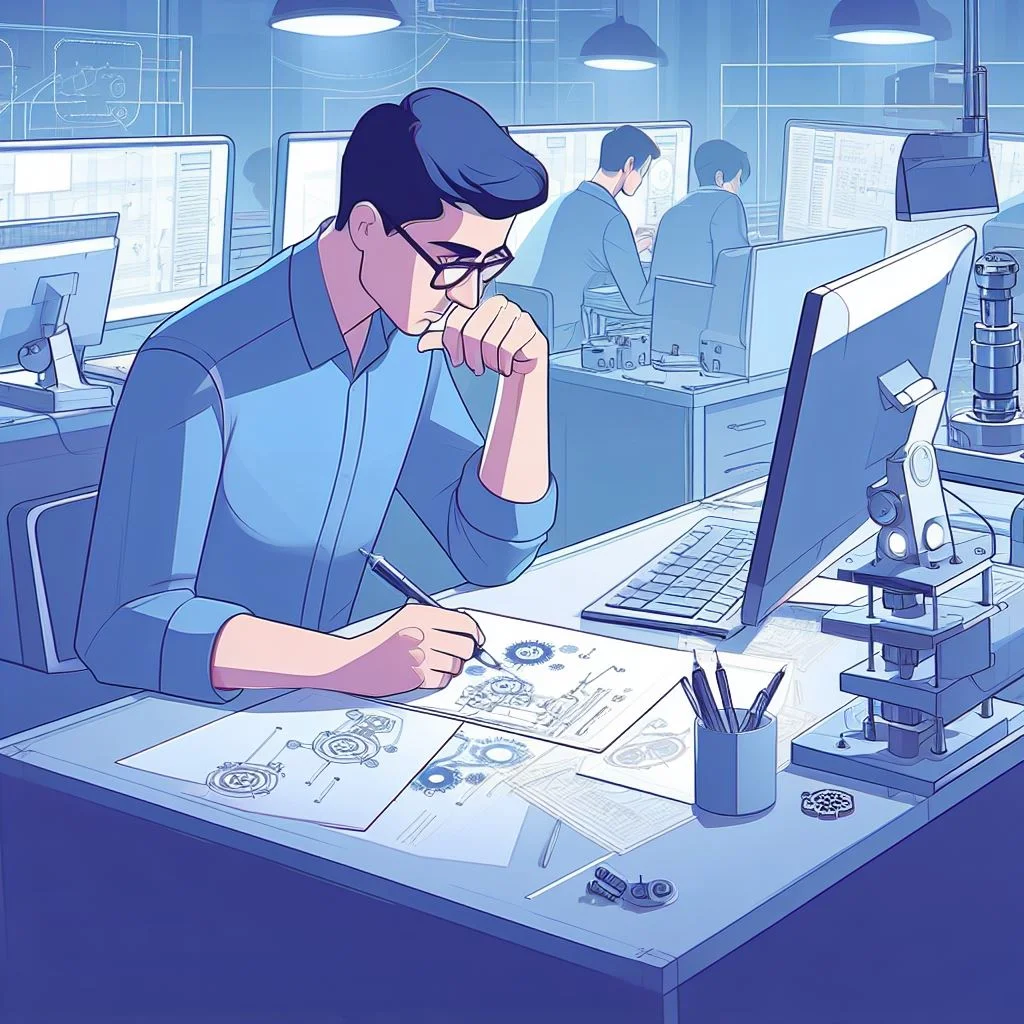
When it comes to assembly modeling in SolidWorks, there are two primary approaches: the top-down approach and the bottom-up approach. Each approach has its advantages and disadvantages, and the choice between them depends on the specific project, design goals, and personal preferences.
1. Top-Down Approach:
The top-down approach, also known as the "design from the top" approach, is a methodology in which you start by creating the main assembly or higher-level components and then work your way down to create the individual parts and sub-assemblies. This approach is often used when you have a well-defined concept of the final product or when the design process is driven by certain requirements, such as functional relationships, kinematics, or specific interfaces.
Advantages of the Top-Down Approach:
- Design Control:With the top-down approach, you have full control over the entire assembly from the beginning. This control is beneficial when you need to ensure that the design adheres to specific constraints or requirements.
- Global Changes:Modifying the top-level assembly can easily propagate changes throughout the entire model. This means that you can make global changes to the design without having to update individual parts or sub-assemblies manually.
- Improved Collaboration:The top-down approach is conducive to team collaboration because team members can work on different aspects of the assembly simultaneously, knowing that the design is evolving in a coordinated manner.
- Complex Systems:It is well-suited for complex systems with intricate relationships and interdependencies. For example, designing a robotic arm with multiple degrees of freedom is best approached from the top-down.
Disadvantages of the Top-Down Approach:
- Initial Complexity:Starting with the top-level assembly can be complex, especially for beginners. You need a clear understanding of the entire design before diving into the details.
- Time-Consuming:Creating the top-level assembly and defining relationships can take time, potentially slowing down the design process.
- Revisions: Frequent design changes can lead to a complex web of relationships, making it challenging to manage revisions effectively.
2. Bottom-Up Approach:
The bottom-up approach, also known as the "design from the bottom" approach, involves creating individual parts and sub-assemblies first and then combining them to form the final assembly. This approach is more intuitive for many users, as it allows you to focus on individual components and their design without the constraints imposed by the top-level assembly.
Advantages of the Bottom-Up Approach:
- Modularity:The bottom-up approach promotes modularity, making it easy to reuse existing parts and sub-assemblies in multiple designs.
- Flexibility: It offers a high degree of flexibility, as you can create and modify components without being constrained by the top-level assembly.
- Rapid Prototyping: Bottom-up design is often quicker for simple assemblies or when you're iterating on a design. You can quickly prototype and test individual components.
- Ease of Learning:This approach is often more accessible for beginners, as it allows them to focus on one component at a time without overwhelming complexities.
Disadvantages of the Bottom-Up Approach:
- Interference Issues: You may encounter interference problems when combining components, as the software doesn't inherently enforce constraints between parts. It's up to you to ensure that parts fit together correctly.
- Global Changes:Making changes to the entire assembly can be more time-consuming, as you'll need to update each part individually.
- Lack of Design Control:With the bottom-up approach, you may find it challenging to maintain control over the design's global aspects, such as kinematics or functional relationships.
- Limited Collaboration: Collaboration can be more challenging with the bottom-up approach because changes made by one team member may affect other parts or sub-assemblies without their knowledge.
Choosing the Right Approach
The decision to use either the top-down or bottom-up approach depends on various factors, including the project's complexity, your familiarity with the software, and your design goals. In practice, many designers and engineers use a combination of both approaches, often referred to as a "hybrid approach." This allows for greater flexibility and control, leveraging the strengths of each method as needed.
Hybrid Approach:
In the hybrid approach, you start with a top-level concept or key components and then use a bottom-up methodology to design the individual parts. This approach strikes a balance between design control and flexibility, making it a popular choice for many projects.
Here are some tips to help you choose the right approach for your SolidWorks assembly modeling tasks:
- Project Complexity:For relatively simple assemblies, a bottom-up approach can be more efficient. For complex systems with intricate relationships, a top-down approach may be more suitable.
- Design Control:If you require strict control over the design, particularly for functional or kinematic requirements, the top-down approach is preferable.
- Time and Experience:Consider your familiarity with SolidWorks and the time available for the project. Beginners may find it easier to start with a bottom-up approach, while experienced users can harness the power of the top-down approach more effectively.
- Collaboration:Assess the level of collaboration required for your project. If you're working in a team, the top-down approach can facilitate concurrent work on different aspects of the assembly.
- Reuse and Standardization:If you anticipate reusing components or standardizing parts across multiple projects, a bottom-up approach can make component management more efficient.
A Case Study: Using Both Approaches
Let's consider a case study of designing a bicycle assembly in SolidWorks to illustrate the use of both top-down and bottom-up approaches.
Top-Down Approach:
Begin by creating the top-level assembly, which includes the frame, wheels, handlebars, and pedals. Establish key relationships, such as the distance between the wheels and the alignment of the handlebars with the frame.
Once the top-level assembly is defined, you can create sub-assemblies for each major component (e.g., wheel assemblies, pedal assemblies) and specify their interfaces and kinematics within the context of the top-level assembly.
Bottom-Up Approach:
Design individual components, such as the wheel spokes, pedal gears, and handlebar grips, in separate part files. Optimize each component's design for its specific function and appearance.
After you've designed the individual components, assemble them together in the context of the top-level assembly. Ensure that all components fit together properly and make any necessary adjustments.
By combining both approaches, you can benefit from the design control and global changes enabled by the top-down approach while enjoying the flexibility and modularity offered by the bottom-up approach. This hybrid approach is particularly useful for complex assemblies like the bicycle, where different components have unique design requirements and interfaces.
Best Practices for Assembly Modeling in SolidWorks
Regardless of the approach you choose, there are several best practices to follow when working on assembly modeling projects in SolidWorks:
File Management: Effective file management is essential for maintaining a structured and organized assembly modeling workflow in SolidWorks. Here are some key considerations:
- Well-Organized File Structure:Create a clear and logical folder structure for your projects. Divide your work into folders for parts, assemblies, and drawings. This structure makes it easier to locate and manage your files.
- Descriptive File Names: Use descriptive file names for your parts, assemblies, and drawings. A meaningful name should reflect the part's function or its role in the assembly. Avoid generic names or default file names like "Part1" or "Assembly2."
- Version Control: Implement a version control system to track changes and revisions. Tools like SolidWorks PDM or third-party solutions can help manage different iterations of your design.
- Backup and Recovery:Regularly back up your files to prevent data loss. Consider utilizing cloud storage or external drives to safeguard your work. SolidWorks also has an autosave feature that can be configured to create periodic backups.
Component Reuse:Reusing components is a smart way to save time, maintain design consistency, and streamline your assembly modeling process:
- Library of Standard Components:Create a library of standard components that you frequently use, such as nuts, bolts, washers, and other fasteners. These components can be quickly inserted into your assemblies, reducing the time spent modeling them from scratch.
- Parametric Models: When creating components, make them parametric by using custom properties and configuration options. This allows you to adapt them for different projects by simply changing parameters rather than creating entirely new parts.
- Catalogs and Design Tables:Utilize catalogs and design tables to organize and manage standard parts and components. This ensures easy access and consistent use of these elements in various assemblies.
Standardize Fasteners:Standardizing fasteners is crucial for ensuring design consistency and efficiency:
- Fastener Library: Maintain a comprehensive library of standardized fasteners, including screws, nuts, bolts, washers, and other common hardware. These components should adhere to industry standards, such as ISO or ANSI.
- Custom Fasteners: For specialized or unique fasteners, create custom parts with configurable features that allow you to adapt their sizes and dimensions as needed for different projects.
- Mate References: Define mate references for your standard fasteners to make their insertion and positioning in assemblies more convenient. This minimizes manual alignment and simplifies the mating process.
Design Intent:Clearly defining your design intent is crucial for effective assembly modeling:
- Functional Specifications: Document the intended function of the assembly and any critical performance requirements. This ensures that the design aligns with the project's goals and objectives.
- Constraints and Relationships: Identify and establish constraints and relationships between components. For example, specify that certain parts should be concentric, coincident, or flush with each other. These constraints maintain design integrity and functionality.
- Master Sketches:Use master sketches to outline key design features and dimensions that govern the overall shape and behavior of the assembly. Master sketches act as a roadmap for your design and help maintain consistency.
Mate References:SolidWorks provides mate references that can greatly streamline the assembly process:
- Part Design:When creating individual parts, establish mate references within the part files. This allows for automatic alignment when assembling parts, simplifying the mate selection process.
- Smart Mates: Utilize Smart Mates to easily align and connect components. SolidWorks offers intelligent mate suggestions based on the geometry of the parts, making it quicker to mate components accurately.
- Group Mates: When dealing with multiple components, use the group mates feature to apply the same set of mates to various instances of a component. This speeds up the assembly process and ensures consistency.
Interference Detection:Interference detection is a critical step in the assembly modeling process, helping you identify and address problems early:
- Regular Checks: Use SolidWorks' interference detection tool to periodically check for interferences or collisions between components. This proactive approach allows you to rectify issues before they become more challenging to resolve.
- Assembly Analysis:Conduct assembly analysis to evaluate the performance and behavior of your design. This includes checking for overconstraints, underconstraints, and other issues that could affect functionality.
- Clearance Verification: Ensure that all moving parts have the necessary clearances to avoid collisions and interference during operation.
Collaboration:Collaboration is crucial for successful assembly modeling, especially in team environments:
- Communication: Maintain open and effective communication with team members and stakeholders. Regularly discuss design changes, updates, and project goals to ensure everyone is on the same page.
- Collaboration Tools:Utilize collaboration tools such as eDrawings to share and review designs with team members or clients. These tools simplify the process of gathering feedback and making necessary adjustments.
- Documentation:Document design decisions, change requests, and meeting minutes to maintain a record of project progress and communication.
Version Control: Implementing version control is essential for tracking changes, managing revisions, and preserving the history of your assembly:
- Version Control Systems: Use version control systems to keep track of different iterations of your assembly. These systems maintain a history of changes and allow you to roll back to previous versions if needed.
- Change Logs:Maintain detailed change logs that document modifications, who made them, and why. This information is invaluable for understanding the evolution of the design.
- Backups:Regularly back up your entire assembly, including related files such as drawings and parts. This safeguards your work against data loss and provides a fallback option in case of unforeseen issues.
Incorporating these best practices into your assembly modeling workflow will not only improve efficiency but also lead to more robust and organized designs in SolidWorks. These principles are essential for both individual designers and teams working on complex projects, ensuring that your assembly models are well-structured, easy to manage, and aligned with your design intent.
Conclusion
SolidWorks assembly modeling is a fundamental skill for students, engineers, and designers involved in product development. Whether you choose a top-down, bottom-up, or hybrid approach, understanding the strengths and weaknesses of each method is crucial for successful assembly modeling.
By selecting the right approach for your specific project, following best practices, and leveraging SolidWorks' powerful assembly modeling tools, you can efficiently create and manage complex assemblies while maintaining design intent and control.
As you continue your journey into the world of SolidWorks, remember that practice and experience are your best allies. Experiment with both approaches, learn from your successes and challenges, and you'll become a proficient assembly modeler in no time. SolidWorks offers a vast array of resources, tutorials, and communities to support your learning and help you master the art of assembly modeling.