- Introduction to SolidWorks
- The Evolution of CAD Technology
- SolidWorks Features and Capabilities
- Applications of SolidWorks in Mechanical Engineering
- Case Studies – Real-world Applications
- Integrating SolidWorks with Industry 4.0
- Challenges and Innovations in SolidWorks
- Training and Certification in SolidWorks
- Future Trends and Developments
- Conclusion
SolidWorks stands as a stalwart in the expansive domain of Computer-Aided Design (CAD), leaving an indelible mark on the landscape of mechanical engineering. Its influence extends seamlessly from the initial stages of conceptualization to the intricate nuances of prototyping. What sets SolidWorks apart is its innate ability to not just meet industry standards but to redefine them. As we embark on this exploration, it becomes evident that SolidWorks is not merely a tool; it is a transformative force, guiding the trajectory of mechanical design into uncharted territories. If you need assistance with your 3D Modeling assignment, delving into the capabilities and applications of SolidWorks can provide valuable insights and support to tackle your assignments effectively.
At its core, SolidWorks operates as a dynamic hub where creativity converges with precision. The software provides a virtual canvas where engineers and designers can breathe life into their ideas. The intuitive interface coupled with an extensive array of features empowers users to visualize, simulate, and refine their concepts with unparalleled accuracy. This process, once laborious and time-consuming, is now a fluid and efficient journey thanks to SolidWorks.
The journey of SolidWorks is intertwined with the evolutionary narrative of CAD technology. From its inception, SolidWorks has been at the forefront of embracing technological advancements, constantly adapting to meet the ever-changing demands of the industry. The software's evolution mirrors the rapid progress of computer technology, witnessing leaps from 2D to 3D modeling, and subsequently, embracing the era of smart design and digital collaboration. It is this adaptability that positions SolidWorks as a cornerstone in the history of CAD.
Unpacking the features and capabilities of SolidWorks reveals a toolbox that caters to the diverse needs of mechanical engineering. Whether it's intricate part modeling, assembly design, or simulation analysis, SolidWorks provides a comprehensive suite of tools. The software's parametric modeling capabilities enable the creation of designs that are not just aesthetically pleasing but also inherently functional. The ability to make real-time adjustments and explore "what-if" scenarios empowers designers to fine-tune their creations with precision.
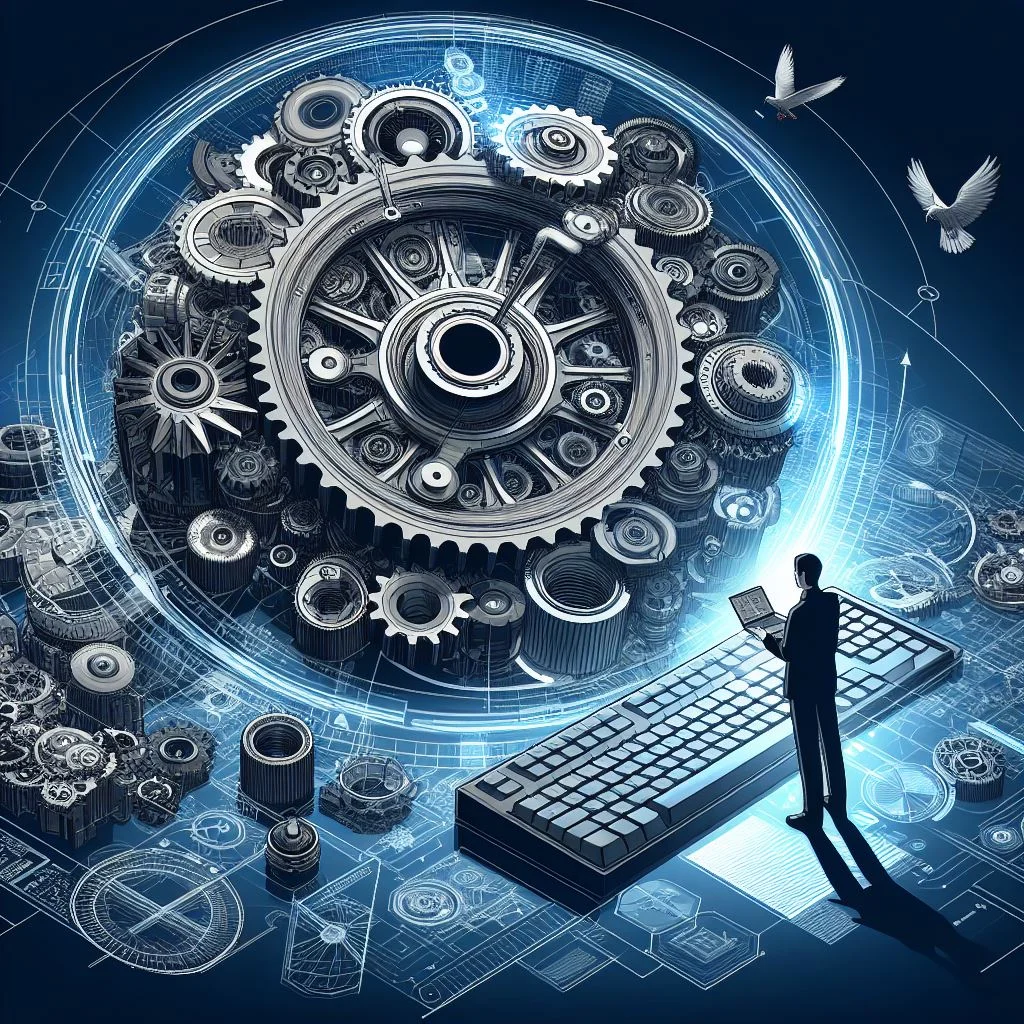
Applications of SolidWorks permeate across a spectrum of industries, making it a versatile and indispensable asset. In the aerospace sector, SolidWorks contributes to the design of cutting-edge aircraft, optimizing aerodynamics and structural integrity. In automotive design, the software facilitates the creation of vehicles that seamlessly blend form and function. The medical field benefits from SolidWorks through the development of innovative medical devices, where precision is paramount.
Real-world case studies illuminate the tangible impact of SolidWorks on mechanical design projects. From reducing time-to-market for consumer products to optimizing manufacturing processes, SolidWorks proves to be a catalyst for efficiency. The software's role in fostering collaboration among cross-functional teams transcends geographical boundaries, ushering in an era where global innovation knows no constraints.
As we navigate the intricate web of challenges and innovations within SolidWorks, it becomes evident that the journey is not without hurdles. The dynamic nature of the engineering landscape brings forth challenges, and SolidWorks continues to evolve in response. Innovations such as cloud-based collaboration, augmented reality integration, and machine learning are positioned as solutions to surmount these challenges, ensuring that SolidWorks remains at the forefront of technological progress.
Training and certification emerge as crucial facets for professionals seeking to master SolidWorks. The complexity and depth of the software necessitate a nuanced understanding, and certified experts stand as the vanguards of efficient and precise design. The educational ecosystem surrounding SolidWorks plays a pivotal role in nurturing a new generation of engineers equipped to harness the full potential of this transformative tool.
As we peer into the future, SolidWorks emerges as a linchpin in the integration of Industry 4.0 principles into mechanical engineering. The synergy between SolidWorks and smart manufacturing processes heralds an era of interconnected, automated, and data-driven design and production. The software's role in shaping tomorrow's designs today extends beyond innovation; it becomes a conduit for sustainable practices, resource optimization, and the creation of products that align with the ethos of the fourth industrial revolution.
Introduction to SolidWorks
SolidWorks, a powerhouse in the realm of Computer-Aided Design (CAD), has emerged as a transformative force in mechanical engineering, revolutionizing the way designers and engineers conceptualize, iterate, and finalize their projects. At its core, SolidWorks is more than just a software application; it's a dynamic ecosystem that has redefined the conventional approach to mechanical design.
The foundations of SolidWorks lie in its commitment to user-friendly interfaces and intuitive functionalities. Born out of a vision to simplify the design process, SolidWorks has democratized access to sophisticated CAD tools, making them accessible to both seasoned professionals and aspiring engineers. Its impact on the field is profound, fostering a culture of innovation where creativity flourishes without the constraints of complex technical intricacies.
SolidWorks acts as a catalyst for collaborative design, breaking down traditional silos that often hinder the creative exchange of ideas. By providing a platform that seamlessly integrates 3D modeling, simulation, and documentation, SolidWorks empowers design teams to work cohesively, resulting in more efficient workflows and accelerated project timelines.
Moreover, the influence of SolidWorks extends beyond individual projects. It has become a cornerstone in the evolution of manufacturing processes, contributing to the efficiency and precision of fabrication. The software's parametric modeling capabilities allow engineers to make quick adjustments and explore various design iterations, ultimately leading to optimized solutions.
The Evolution of CAD Technology
Tracing the evolution of Computer-Aided Design (CAD) reveals a captivating journey marked by technological leaps and industry demands that have constantly propelled SolidWorks to new heights. In its nascent stages, CAD technology sought to digitize and automate manual drafting processes. Early iterations were rudimentary compared to the sophisticated tools we have today. SolidWorks emerged in the 1990s as a pioneer, introducing parametric modeling, a revolutionary feature allowing designers to define relationships between various components in their models.
Over the years, SolidWorks has meticulously adapted to an ever-changing technological landscape. The software's evolution mirrors the relentless pace of advancements in computing power, graphics processing, and software architecture. SolidWorks has seamlessly integrated these innovations, enhancing its performance, speed, and capabilities. The transition from 2D to 3D modeling marked a significant paradigm shift, and SolidWorks not only embraced this change but became a trailblazer in promoting the adoption of three-dimensional design methodologies.
Moreover, SolidWorks has been attentive to industry demands, incorporating features that cater to specific needs across diverse sectors. Whether it's the aerospace industry requiring precise simulations or the automotive sector seeking streamlined prototyping, SolidWorks has evolved as a versatile tool capable of meeting the intricate demands of various engineering disciplines. In doing so, it has cemented its status as a go-to CAD solution, a testament to its agility in navigating the intricate dance between technology and industry requirements. The journey of SolidWorks through the evolution of CAD is a testament to its adaptability and commitment to staying at the forefront of innovation in the dynamic field of mechanical engineering.
SolidWorks Features and Capabilities
A deep dive into the robust features and capabilities of SolidWorks reveals a tool that goes beyond conventional CAD applications. One standout feature is its parametric modeling, allowing designers to create dynamic and easily editable 3D models. This parametric approach enables swift adjustments to design dimensions, fostering a more agile and iterative design process. SolidWorks' intuitive interface empowers both seasoned professionals and newcomers, making the software accessible to a broad spectrum of users.
Moreover, SolidWorks boasts an extensive library of pre-built components and parts, expediting the design process and ensuring accuracy. The software's assembly modeling capabilities enable the creation of intricate assemblies, allowing engineers to visualize and assess the interactions between components seamlessly. SolidWorks simulations further enhance its capabilities, enabling virtual testing and analysis of designs for factors such as stress, strain, and fluid dynamics.
In the realm of sheet metal design, SolidWorks stands out with its dedicated tools for creating complex sheet metal components. This feature facilitates the design of intricate structures with precision and ease. Additionally, the software's electrical design capabilities streamline the integration of electronic components into mechanical designs, fostering a comprehensive approach to product development.
SolidWorks' commitment to interoperability is evident through its compatibility with various file formats, promoting collaboration across diverse design environments. Whether it's importing models from other CAD software or exporting designs for manufacturing, SolidWorks ensures a seamless flow of data throughout the design and production lifecycle.
Applications of SolidWorks in Mechanical Engineering
Applications of SolidWorks in Mechanical Engineering span a vast spectrum, making it an indispensable tool across diverse industries. In the aerospace sector, SolidWorks facilitates the design of intricate components crucial for aircraft and spacecraft. Engineers leverage its parametric modeling capabilities to ensure precision in the aerodynamic profiles of wings, fuselage, and propulsion systems. The software's simulation features aid in testing the structural integrity of components under various conditions, contributing to the creation of safer and more efficient aerospace systems.
Moving into the automotive realm, SolidWorks plays a pivotal role in the design and development of vehicles. From conceptualizing the initial vehicle structure to refining individual components, such as engines and suspension systems, SolidWorks streamlines the entire automotive design process. Its parametric modeling allows for quick adjustments to meet changing specifications, while finite element analysis ensures the durability and safety of vehicle structures. With SolidWorks, automotive engineers can optimize designs for fuel efficiency, aerodynamics, and overall performance, fostering innovation in an industry constantly evolving to meet environmental and technological demands.
Beyond aerospace and automotive, SolidWorks finds applications in industries such as energy, healthcare, and consumer goods, showcasing its versatility in addressing the unique challenges posed by each sector. The software's adaptability makes it a cornerstone in the toolkit of mechanical engineers, empowering them to push the boundaries of design and contribute to the ongoing transformation of mechanical engineering practices across the globe.
Case Studies – Real-world Applications
Delving into real-world applications, SolidWorks shines as a beacon of innovation in mechanical engineering. Case studies illuminate the transformative impact of this CAD powerhouse on diverse projects, showcasing its ability to turn conceptual designs into tangible realities.
In the aerospace sector, SolidWorks has been instrumental in the development of cutting-edge aircraft designs, optimizing aerodynamics, and ensuring structural integrity. These applications have not only enhanced performance but have also contributed to fuel efficiency and environmental sustainability.
Transitioning to the automotive industry, SolidWorks has been a driving force in the creation of next-generation vehicles. From electric cars to autonomous driving systems, the CAD tool facilitates seamless integration of complex components, ensuring safety and efficiency in modern automotive designs.
Moreover, in the field of medical devices, SolidWorks has played a crucial role in the development of life-saving technologies. The precision afforded by the software allows for the meticulous design of surgical instruments, prosthetics, and medical implants, revolutionizing healthcare and improving patient outcomes.
These case studies underscore SolidWorks' adaptability across industries, emphasizing its capacity to address unique challenges and drive innovation. From the conceptualization phase to the final product, SolidWorks continues to be an indispensable tool, propelling mechanical engineering into a future defined by groundbreaking designs and unparalleled efficiency.
Integrating SolidWorks with Industry 4.0
SolidWorks stands at the forefront of the technological wave that is Industry 4.0, seamlessly integrating with the core principles that define this transformative era. As we delve into this integration, it becomes evident that SolidWorks is not merely a CAD tool but a linchpin in the realization of smart manufacturing, automation, and the holistic integration of digital technologies within mechanical engineering processes.
In the context of Industry 4.0, SolidWorks serves as a catalyst for innovation by enabling the creation of intelligent, interconnected design ecosystems. The software facilitates the development of digital twins, virtual replicas of physical objects or systems. This digital twinning capability allows engineers to simulate and analyze the behavior of a product throughout its lifecycle, from conception to decommissioning.
Furthermore, SolidWorks plays a crucial role in the implementation of automation in manufacturing processes. By seamlessly interfacing with robotic systems and other automated machinery, SolidWorks optimizes the design and programming of these systems, enhancing precision, efficiency, and overall productivity.
The integration with Industry 4.0 goes beyond individual processes. SolidWorks provides a collaborative environment where multiple stakeholders can contribute to the design and manufacturing processes in real-time, fostering a culture of teamwork and innovation. This collaborative approach aligns perfectly with the interconnected nature of Industry 4.0, where data-driven decision-making and communication are paramount.
Challenges and Innovations in SolidWorks
Addressing the challenges faced by designers and engineers when using SolidWorks is crucial for optimizing its potential in the field of mechanical engineering. One significant hurdle lies in the learning curve associated with mastering SolidWorks. The complexity of the software can pose challenges for beginners, requiring dedicated training programs to ensure proficiency. Moreover, the software's frequent updates and additions of new features demand continuous learning for seasoned professionals to stay abreast of the latest tools and functionalities.
In addition to the learning curve, interoperability issues can arise when integrating SolidWorks with other software and systems. Designers often encounter compatibility challenges when sharing files with collaborators using different CAD tools. This necessitates a focus on developing standardized file formats and enhanced interoperability protocols, ensuring seamless collaboration across diverse engineering platforms.
To counter these challenges, ongoing innovations in SolidWorks are a beacon of hope. The integration of artificial intelligence (AI) and machine learning (ML) into SolidWorks is revolutionizing the design process. These technologies assist in automating repetitive tasks, predicting design outcomes, and optimizing the overall workflow. Furthermore, the development of intuitive user interfaces and real-time collaboration features is simplifying the user experience, making SolidWorks more accessible to a broader audience.
As SolidWorks continues to evolve, addressing these challenges and embracing innovations will be pivotal in maximizing its potential and ensuring a smoother, more efficient design process for engineers and designers alike.
Training and Certification in SolidWorks
Training and certification in SolidWorks are not merely checkboxes on a professional's to-do list; they are essential steps in unlocking the true potential of this powerful CAD tool. SolidWorks, with its myriad features and intricate functionalities, requires a nuanced understanding to be harnessed effectively. Formal training programs provide individuals with a structured learning environment, imparting not only theoretical knowledge but also hands-on experience with real-world applications.
Professionals who undergo SolidWorks training gain a comprehensive understanding of the software's capabilities, enabling them to navigate its interface seamlessly and leverage its features optimally. These programs often cover a range of topics, from basic sketching and part modeling to advanced assembly design and simulation. Moreover, participants learn best practices for efficient collaboration, data management, and troubleshooting—skills that are invaluable in a professional setting.
Certification, on the other hand, serves as a tangible testament to an individual's proficiency in SolidWorks. Recognized globally, SolidWorks certifications validate one's skills and expertise in using the software proficiently. Employers increasingly value these certifications as indicators of a candidate's commitment to professional development and mastery of the tools crucial to the industry.
In an ever-evolving technological landscape, staying abreast of the latest updates and features in SolidWorks is imperative. Training and certification, therefore, become ongoing processes, allowing professionals to adapt to new functionalities and emerging trends, ensuring they remain at the forefront of their field. As the demand for skilled SolidWorks professionals continues to rise, investing in training and certification becomes a strategic career move, opening doors to exciting opportunities and ensuring sustained success in the dynamic realm of mechanical engineering.
Future Trends and Developments
In anticipation of the future trends and developments in SolidWorks, it becomes evident that the landscape of mechanical engineering is poised for transformative changes. As technology continues to advance at an unprecedented pace, SolidWorks is expected to play a pivotal role in adapting to and shaping these shifts.
One notable trend on the horizon is the integration of Artificial Intelligence (AI) and machine learning algorithms within SolidWorks. This development is set to enhance the software's predictive modeling capabilities, allowing for more intuitive and automated design processes. Engineers can anticipate a more streamlined workflow, with SolidWorks intelligently predicting design iterations based on historical data and user preferences.
Furthermore, the convergence of SolidWorks with Virtual Reality (VR) and Augmented Reality (AR) is set to redefine the way engineers visualize and interact with their designs. Imagine walking through a virtual prototype, examining every detail in a three-dimensional space. SolidWorks is positioned to bring this immersive experience to the forefront, fostering greater collaboration and understanding throughout the design and development stages.
In addition to these technological advancements, the future holds exciting possibilities for SolidWorks in the realm of sustainable design and optimization. As environmental consciousness becomes increasingly integral to engineering practices, SolidWorks is likely to incorporate tools for evaluating and optimizing designs with a focus on efficiency and reduced environmental impact.
Conclusion
In conclusion, SolidWorks stands not merely as a tool within the toolkit of mechanical engineers but as a transformative catalyst, reshaping the very essence of how we conceive and execute designs. It has transcended the boundaries of traditional design processes, propelling the field of mechanical engineering into an era marked by unprecedented innovation and heightened efficiency.
SolidWorks serves as a beacon for designers, providing a dynamic platform that encourages creativity and problem-solving. Its intuitive interface, coupled with powerful features, empowers engineers to think beyond the constraints of conventional design. The software's ability to seamlessly integrate with emerging technologies, such as virtual reality and artificial intelligence, further amplifies its significance in the ever-evolving landscape of mechanical engineering.
One of the remarkable facets of SolidWorks is its role in democratizing design. No longer confined to a select few with specialized training, SolidWorks has made sophisticated design tools accessible to a broader audience. This democratization has led to a democratization of ideas, as individuals from diverse backgrounds contribute to the collective pool of innovative solutions.
Moreover, the collaborative nature of SolidWorks has redefined how teams work together on projects. With real-time collaboration features and cloud-based solutions, engineers scattered across the globe can seamlessly collaborate on intricate designs, fostering a truly global approach to problem-solving. This collaborative environment not only accelerates the design process but also encourages a diversity of thought, resulting in more robust and refined solutions.
Looking ahead, SolidWorks is poised to play a pivotal role in the realization of smart manufacturing and the Internet of Things (IoT). As industries transition towards Industry 4.0, SolidWorks provides a foundation for the integration of digital technologies, enabling a connected and intelligent ecosystem. The software's adaptability to changing technological landscapes ensures that it remains at the forefront of innovation, consistently meeting the demands of an ever-evolving industry.