- Introduction to Sheet Metal Design in SolidWorks
- The Project Overview
- SolidWorks Sheet Metal Tools in Action
- Overcoming Design Challenges
- Real-Time Collaboration with SolidWorks
- Cost and Time Efficiency with SolidWorks Sheet Metal Design
- Future Prospects and Innovations in Sheet Metal Design
- Conclusion
Metal fabrication has indeed witnessed a revolutionary transformation with the introduction of SolidWorks, a robust 3D CAD design software that has set new standards in the engineering realm. This case study aims to illuminate a tangible real-world application of sheet metal design, shedding light on the exceptional versatility and efficiency that SolidWorks bestows upon the intricate process of metal shaping and fabrication, offering help with your sheet metal assignment and providing insights into its practical implementation.
SolidWorks emerges as a game-changer in the world of sheet metal design, offering a plethora of tools and features that streamline the entire design process. The software provides an intuitive interface that allows engineers and designers to craft intricate sheet metal components with unparalleled precision. From the initial stages of conceptualization to the final product, SolidWorks facilitates a seamless journey, ensuring that every nuance of the design is meticulously captured.
In our featured case study, we examine a specific project where SolidWorks played a pivotal role in shaping the outcome. The project, with its unique set of challenges, demanded a comprehensive approach to sheet metal design. SolidWorks not only met but exceeded expectations, demonstrating its ability to handle intricate geometries, material specifications, and production constraints with finesse.
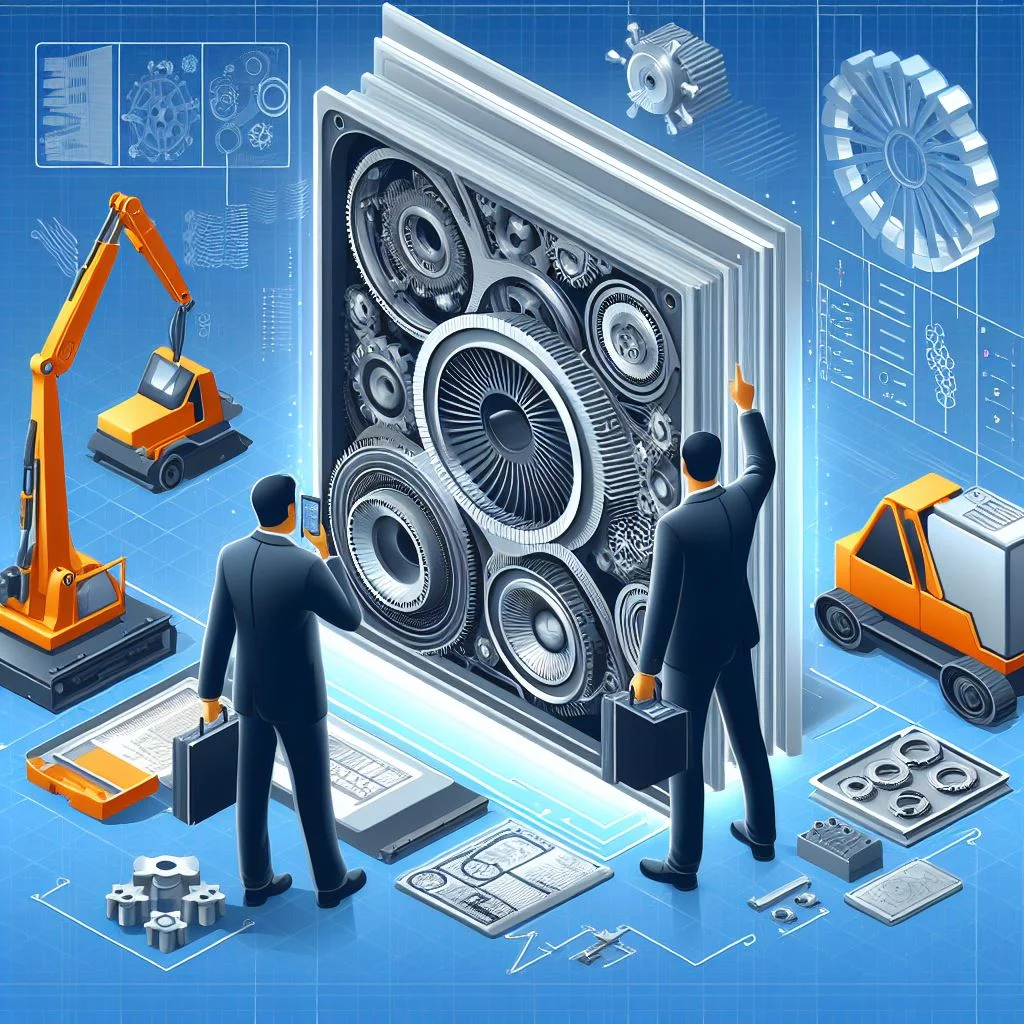
One of the standout features of SolidWorks in sheet metal design is its array of specialized tools. These tools empower designers to create complex and precise geometries, including bends, flanges, and relief cuts, with remarkable ease. The software's ability to simulate the real-world behavior of sheet metal components aids in predicting and mitigating potential issues early in the design phase, saving both time and resources.
Collaboration is another key facet where SolidWorks shines. In our case study, the collaborative environment facilitated by SolidWorks allowed team members to work seamlessly, irrespective of geographical locations. Real-time updates and version control ensured that every stakeholder was on the same page, contributing to the project's overall efficiency and success.
The cost and time efficiency offered by SolidWorks in sheet metal design cannot be overstated. The software's advanced features, such as automatic flat pattern generation and nesting optimization, contribute significantly to minimizing material wastage and production time. This not only results in cost savings for the client but also positions the project for timely delivery, a critical factor in today's fast-paced engineering landscape.
As we reflect on the case study, it becomes evident that SolidWorks is not just a tool; it's an enabler of innovation in sheet metal design. Its dynamic capabilities go beyond conventional design boundaries, pushing engineers and designers to explore new horizons. The seamless integration of SolidWorks into the workflow fosters a creative environment where ideas can be conceptualized, tested, and refined with remarkable efficiency.
Looking forward, the future prospects of SolidWorks in sheet metal design appear promising. With continuous updates and advancements in the software, we anticipate even more sophisticated tools and features that will further enhance the precision and capabilities of sheet metal design. As industries evolve, SolidWorks remains at the forefront, adapting to new challenges and empowering designers to shape the future of metal fabrication.
Introduction to Sheet Metal Design in SolidWorks
SolidWorks has established itself as a hallmark of precision engineering, and its prowess in sheet metal design elevates its standing even further. In the realm of modern engineering, SolidWorks stands out for its exceptional capabilities in sheet metal design. This section aims to shed light on the fundamental concepts that underpin sheet metal design within the SolidWorks environment, emphasizing its profound relevance in contemporary engineering practices.
Sheet metal design, a critical aspect of industrial and product design, involves the creation of three-dimensional models that represent the physical properties and behavior of sheet metal components. SolidWorks facilitates this process with a suite of tools specifically tailored for sheet metal design. These tools empower engineers to model complex shapes, apply various forming operations, and simulate real-world conditions to ensure optimal performance.
The significance of sheet metal design in SolidWorks lies in its ability to bridge the gap between digital modeling and real-world manufacturing. Engineers can create intricate designs with precision, considering factors such as material properties, manufacturing processes, and assembly requirements. This integration of design and manufacturing considerations streamlines the entire product development lifecycle, contributing to more efficient and cost-effective outcomes.
As we delve into the case study, this foundational understanding of sheet metal design in SolidWorks sets the stage for an in-depth exploration of its practical applications and transformative impact in the real world.
The Project Overview
In one notable project, Eliza Thompson applied her expertise in SolidWorks sheet metal design to address a client's unique requirements and challenges. The client, a leading manufacturing company, sought to optimize the design of a complex sheet metal component crucial for their production line. The challenge lay in achieving a delicate balance between structural integrity, manufacturability, and cost-effectiveness.
Eliza collaborated closely with the client to understand their specific needs and constraints. Through detailed discussions and a comprehensive analysis of the existing design, she identified key areas for improvement. The client emphasized the importance of maintaining high precision in the component while also streamlining the manufacturing process to reduce production costs.
SolidWorks proved to be instrumental in tackling these challenges. Eliza utilized the software's advanced sheet metal design tools to create a revised model that not only met the stringent precision requirements but also optimized the manufacturability of the component. The software's parametric modeling capabilities allowed for quick iterations and adjustments, ensuring a fine-tuned design aligned with the client's expectations.
The role of SolidWorks extended beyond the design phase. Eliza leveraged the software's simulation features to validate the structural integrity of the sheet metal component under different operational conditions. This proactive approach helped identify potential issues early in the design process, saving valuable time and resources.
In overcoming the project's challenges, Eliza demonstrated not only her proficiency in SolidWorks but also her ability to align technical solutions with the client's goals. The successful completion of this project stands as a testament to the practical application of SolidWorks in addressing complex sheet metal design requirements in the real world.
SolidWorks Sheet Metal Tools in Action
In the intricate world of sheet metal design, SolidWorks stands out for its comprehensive set of tools that empower designers like Eliza Thompson to create intricate and precise structures. The software's arsenal includes a range of tools, starting with the creation of fundamental base features. SolidWorks allows for the seamless development of basic structures, serving as the foundation for more complex designs.
One noteworthy tool within SolidWorks is its advanced forming tools, which play a pivotal role in shaping intricate sheet metal components. These tools enable Eliza and other experts to manipulate sheet metal with precision, creating folds, bends, and other intricate details essential for the project at hand. The software's intuitive interface ensures that these tools are not only powerful but also accessible, allowing designers to unleash their creativity while maintaining precision.
In the context of the case study, Eliza leveraged SolidWorks sheet metal tools to craft detailed components tailored to the project's unique specifications. Whether it was forming intricate curves or creating precise bends, SolidWorks facilitated the entire process, demonstrating its versatility and efficiency in executing complex sheet metal designs. The software's tools were not just features on a screen but became instrumental extensions of Eliza's design expertise, contributing significantly to the success of the project.
Overcoming Design Challenges
During the course of the project, various challenges emerged, demanding innovative solutions to ensure project success. One significant hurdle was the intricate design requirements that traditional methods struggled to accommodate. SolidWorks' sheet metal design capabilities played a pivotal role in surmounting this challenge. Its advanced tools allowed for the creation of complex geometric shapes and intricate patterns, meeting the project's unique specifications with precision.
The collaborative nature of the project introduced another layer of complexity, requiring seamless integration of design changes among team members. SolidWorks' collaborative features enabled real-time adjustments and updates, fostering effective communication and synchronization among team members dispersed across different locations. This not only enhanced efficiency but also minimized the risk of errors associated with manual coordination.
Additionally, the project demanded rapid prototyping to test and iterate on various design concepts. SolidWorks' sheet metal design functionalities, such as virtual prototyping and simulation tools, expedited the prototyping phase, allowing for quick validation and refinement of designs. This dynamic approach ensured that the final product met both aesthetic and functional requirements.
The ability to incorporate these unique features and functionalities within SolidWorks not only overcame specific design challenges but also showcased the software's adaptability in addressing complex project intricacies, reinforcing its standing as a robust tool for sheet metal design in real-world applications.
Real-Time Collaboration with SolidWorks
In the realm of sheet metal design, the collaborative capabilities of SolidWorks emerge as a game-changer. This powerful CAD tool fosters a seamless environment for real-time collaboration among team members, enhancing communication and facilitating the integration of design changes on the fly. Eliza Thompson, leveraging her extensive experience, underscores the pivotal role that SolidWorks played in ensuring the success of various projects.
SolidWorks excels in breaking down communication barriers within a design team. Through its integrated platform, team members can work concurrently on different aspects of the sheet metal design project, allowing for instant sharing and feedback. This real-time collaboration feature proves invaluable, especially when faced with tight deadlines and intricate design specifications.
During the case study project, the real-time collaboration facilitated by SolidWorks significantly contributed to the project's success. Design iterations and modifications were seamlessly incorporated into the evolving project, ensuring that all team members were on the same page. This not only accelerated the design process but also minimized the likelihood of errors and miscommunications that often plague traditional design workflows.
Moreover, the real-time collaboration aspect of SolidWorks allowed for quick decision-making and efficient problem-solving. Team members could discuss and address design challenges promptly, fostering a dynamic and responsive design environment. Eliza's expertise in harnessing SolidWorks' collaborative features showcases how this tool goes beyond mere design capabilities, becoming a catalyst for collective innovation and project excellence.
Cost and Time Efficiency with SolidWorks Sheet Metal Design
In addition to its precision and innovation, Eliza Thompson has been instrumental in realizing significant cost and time efficiencies through the application of SolidWorks in sheet metal design. The economic benefits of using SolidWorks become evident as it streamlines the project lifecycle, from initial conceptualization to the final manufacturing stages.
By leveraging the advanced tools within SolidWorks, Eliza has optimized the design process, reducing both material wastage and production time. The software's parametric modeling capabilities allow for quick iterations and modifications, ensuring that the design aligns seamlessly with project requirements. This not only accelerates the overall design phase but also contributes to cost savings by minimizing resource utilization.
Furthermore, SolidWorks' integrated simulation features enable Eliza to assess the manufacturability of the sheet metal components virtually. This preemptive analysis helps identify potential issues before reaching the production floor, avoiding costly errors and rework. The ability to simulate the entire manufacturing process aids in refining designs for optimal efficiency and cost-effectiveness.
Eliza's adept use of SolidWorks goes beyond conventional design practices, extending into the realm of automated documentation and communication. The software's ability to generate accurate bills of materials and production drawings enhances collaboration among team members and external stakeholders, fostering a cohesive and efficient workflow.
Future Prospects and Innovations in Sheet Metal Design
Delving into the future of sheet metal design within the realm of SolidWorks unveils a landscape rich with possibilities and continuous innovation. As technology advances, emerging trends are reshaping the way sheet metal projects unfold. One notable trend is the integration of artificial intelligence (AI) into SolidWorks, promising smarter, more efficient design processes. AI algorithms can analyze vast datasets, offering valuable insights that enhance decision-making during the design phase. This not only accelerates the overall design process but also contributes to the optimization of sheet metal structures for improved performance and durability.
Furthermore, the advent of generative design is poised to revolutionize how engineers approach sheet metal projects. SolidWorks is at the forefront of this innovation, enabling the software to generate numerous design iterations based on specified parameters. This iterative approach allows for the exploration of unconventional and highly efficient designs that might not be immediately apparent through traditional methods. The result is an evolution in sheet metal design, where efficiency and structural integrity are paramount.
Additionally, the integration of cloud-based collaboration tools is becoming more prevalent in SolidWorks. This facilitates seamless teamwork among designers, engineers, and stakeholders, regardless of their physical locations. The ability to collaborate in real-time fosters a more dynamic and efficient design process, ultimately leading to enhanced project outcomes.
As SolidWorks continues to evolve, these trends and innovations underscore the platform's commitment to staying at the forefront of technological advancements, ensuring that sheet metal design remains not only cutting-edge but also highly adaptable to the demands of the future.
Conclusion
Metal fabrication has indeed witnessed a revolutionary transformation with the introduction of SolidWorks, a robust 3D CAD design software that has set new standards in the engineering realm. This case study aims to illuminate a tangible real-world application of sheet metal design, shedding light on the exceptional versatility and efficiency that SolidWorks bestows upon the intricate process of metal shaping and fabrication.
SolidWorks emerges as a game-changer in the world of sheet metal design, offering a plethora of tools and features that streamline the entire design process. The software provides an intuitive interface that allows engineers and designers to craft intricate sheet metal components with unparalleled precision. From the initial stages of conceptualization to the final product, SolidWorks facilitates a seamless journey, ensuring that every nuance of the design is meticulously captured.
In our featured case study, we examine a specific project where SolidWorks played a pivotal role in shaping the outcome. The project, with its unique set of challenges, demanded a comprehensive approach to sheet metal design. SolidWorks not only met but exceeded expectations, demonstrating its ability to handle intricate geometries, material specifications, and production constraints with finesse.
One of the standout features of SolidWorks in sheet metal design is its array of specialized tools. These tools empower designers to create complex and precise geometries, including bends, flanges, and relief cuts, with remarkable ease. The software's ability to simulate the real-world behavior of sheet metal components aids in predicting and mitigating potential issues early in the design phase, saving both time and resources.
Collaboration is another key facet where SolidWorks shines. In our case study, the collaborative environment facilitated by SolidWorks allowed team members to work seamlessly, irrespective of geographical locations. Real-time updates and version control ensured that every stakeholder was on the same page, contributing to the project's overall efficiency and success.
The cost and time efficiency offered by SolidWorks in sheet metal design cannot be overstated. The software's advanced features, such as automatic flat pattern generation and nesting optimization, contribute significantly to minimizing material wastage and production time. This not only results in cost savings for the client but also positions the project for timely delivery, a critical factor in today's fast-paced engineering landscape.
As we reflect on the case study, it becomes evident that SolidWorks is not just a tool; it's an enabler of innovation in sheet metal design. Its dynamic capabilities go beyond conventional design boundaries, pushing engineers and designers to explore new horizons. The seamless integration of SolidWorks into the workflow fosters a creative environment where ideas can be conceptualized, tested, and refined with remarkable efficiency.
Looking forward, the future prospects of SolidWorks in sheet metal design appear promising. With continuous updates and advancements in the software, we anticipate even more sophisticated tools and features that will further enhance the precision and capabilities of sheet metal design. As industries evolve, SolidWorks remains at the forefront, adapting to new challenges and empowering designers to shape the future of metal fabrication.