- Key Features of SolidWorks Sheet Metal Design
- Step-by-Step Guide to Creating a Sheet Metal Part in SolidWorks
- Step 1: Create a New Part Document
- Step 2: Sketch the Base Profile
- Step 3: Apply Sheet Metal Features
- Step 4: Add Bend Relief and Corner Relief
- Step 5: Create Cuts and Bends
- Step 6: Generate the Flat Pattern
- Step 7: Add Additional Features
- Step 8: Create Drawings
- Step 9: Collaboration and Review
- Step 10: Finalize Design
- Best Practices for SolidWorks Sheet Metal Design
- Conclusion
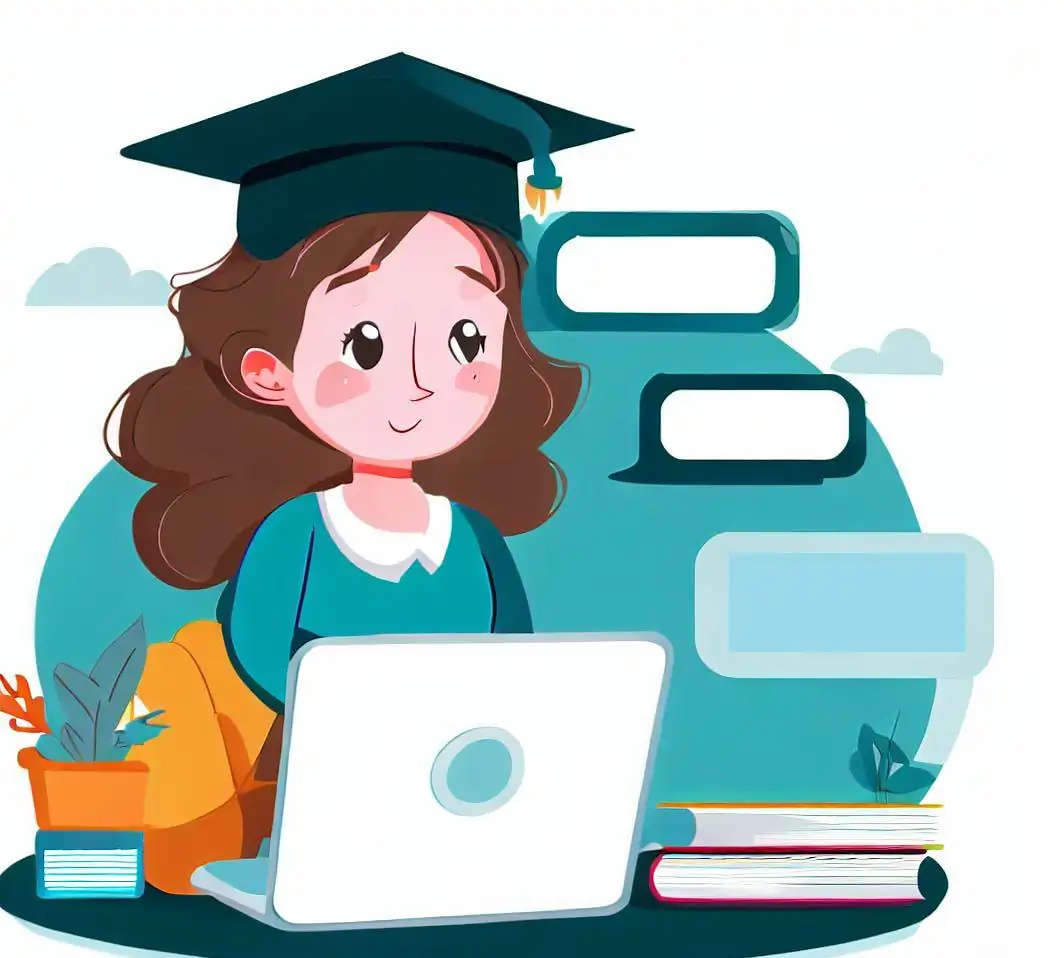
Sheet metal design is a crucial aspect of modern engineering and manufacturing. It involves the creation of complex, functional, and efficient designs using thin sheets of metal. SolidWorks, a leading 3D computer-aided design (CAD) software, offers powerful tools and features specifically tailored for sheet metal design. In this comprehensive guide, we will explore the fundamentals of SolidWorks sheet metal design, its benefits, and key features, and provide step-by-step insights into creating sheet metal parts and assemblies to help you complete your sheet metal Assignment.
SolidWorks, renowned for its versatile capabilities in 3D computer-aided design (CAD), extends its prowess to sheet metal design with a range of exceptional benefits that empower designers and engineers to create efficient and precise sheet metal components. Here's a closer look at the advantages SolidWorks brings to the realm of sheet metal design:
SolidWorks stands out in its ability to provide accurate and automatic unfolding of sheet metal parts. This feature allows designers to transition seamlessly from the 3D model to the 2D flat pattern representation. By visualizing the unfolded view before fabrication, designers can identify potential issues, such as material distortions or misalignments, and rectify them before they impact the manufacturing process. The result is minimized errors and a higher degree of precision in the final product.
- Parametric Design:
- Integrated Workflow:
- Material Library:
- Bend Deduction Calculations:
- Collaboration:
Sheet metal design often entails iterative modifications to meet specific manufacturing constraints or design changes. SolidWorks' parametric design capabilities shine in this context. Designers can create a sheet metal model with flexibility in mind, allowing them to adjust dimensions, angles, and other parameters effortlessly. As changes are made, the model updates dynamically, maintaining the integrity of the design throughout the iterative process.
SolidWorks streamlines the sheet metal design process by offering an integrated workflow that spans from initial concept to final fabrication. Designers can seamlessly transition from creating sheet metal parts to generating their flat patterns and producing detailed manufacturing drawings—all within a unified software environment. This integration reduces the need to switch between different software tools, saving time and ensuring consistency across the design process.
A robust material library is at the heart of SolidWorks' sheet metal design capabilities. The software provides a comprehensive collection of sheet metal materials, each with its specific properties and thicknesses. This feature allows designers to simulate real-world conditions accurately. By selecting the appropriate material, designers can assess factors like weight, strength, and cost, contributing to well-informed design decisions.
SolidWorks takes the complexity out of bend allowances and deductions. Through its automated calculations, the software determines the necessary material deformation allowances for various bends based on factors such as material type, thickness, and bend angles. This automated accuracy ensures that sheet metal forming processes yield results that align with expectations and design specifications.
Collaboration lies at the heart of successful engineering and manufacturing projects. SolidWorks excels in facilitating collaboration between designers, engineers, and manufacturers. Its built-in tools enable seamless sharing of designs, real-time model reviews, and collaborative feedback incorporation. This capability promotes efficient communication among team members and stakeholders, ensuring that design decisions are well-informed and that the final product aligns with collective goals.
In essence, SolidWorks transforms the sheet metal design process by offering a suite of benefits that enhance accuracy, efficiency, and collaboration. From accurate flat pattern generation to flexible parametric modeling, SolidWorks empowers designers to tackle the challenges of sheet metal design with confidence and creativity, resulting in products that are not only functional but also optimized for manufacturing success.
Key Features of SolidWorks Sheet Metal Design
SolidWorks, a powerful 3D CAD software, includes a comprehensive suite of features specifically designed to address the unique challenges and intricacies of sheet metal design. These features provide engineers and designers with the tools needed to create accurate, manufacturable, and efficient sheet metal parts. Let's explore these key features in greater detail:
- Sheet Metal Features:
SolidWorks offers a range of specialized sheet metal features that simplify the creation of sheet metal parts. These features include:
- Base Flange: This feature allows you to create the initial extruded geometry of the sheet metal part. It's especially useful for creating the main body of the part.
- Edge Flange: Edge flanges are used to create bends along the edges of the sheet metal part. You can specify the length, angle, and other parameters for precise bending.
- Miter Flange: Miter flanges are handy for creating angular bends, such as when you need to join two sheet metal components at an angle.
- Hem: The hem feature is used to create folded-over edges, providing a smoother and safer edge for the sheet metal part.
- Swept Flange: Swept flanges enable the creation of complex bends that follow a specified path.
- Flat Pattern:
The Flat Pattern feature in SolidWorks automatically generates the unfolded representation of a sheet metal part. This is a critical aspect of sheet metal design because it provides the essential information needed for cutting and bending operations during manufacturing. Designers can review the flat pattern to ensure that it accurately reflects the intended geometry of the final part.
- Bend Allowances and Deductions:
SolidWorks excels in calculating bend allowances and bend deductions. It takes into account various factors, such as material properties, sheet thickness, and bend angles, to accurately determine the amount of material required for bending. This feature is crucial for achieving precise sheet metal bending and ensuring that the final part conforms to design specifications.
- Corner Relief:
Corner relief features in SolidWorks are essential for ensuring that the material can bend without distortion or tearing, especially at sharp corners. SolidWorks provides options for different types of corner reliefs, including square, circular, and tear-drop shapes. This flexibility allows designers to choose the most suitable relief type for each corner of the sheet metal part.
- Sheet Metal Gussets:
Sheet metal gussets are often used to enhance the structural integrity of sheet metal assemblies. SolidWorks simplifies the creation and modification of gussets, making it easier to strengthen sheet metal parts as needed. This feature is particularly valuable in applications where rigidity and load-bearing capacity are critical.
- Jog and Notch Features:
Jog and notch features are essential for creating tabs, slots, and other intricate shapes within sheet metal parts. SolidWorks provides dedicated tools for creating these features accurately, allowing designers to customize sheet metal components to meet specific design requirements. This versatility is especially useful when designing sheet metal parts with complex geometries.
These sheet metal-specific features ensure that the design process is tailored to the unique requirements of sheet metal manufacturing, including the accurate representation of bend allowances and relief cuts.
Step-by-Step Guide to Creating a Sheet Metal Part in SolidWorks
Creating a sheet metal part in SolidWorks involves a series of well-defined steps that guide you through the process, from initial sketching to finalizing the design for manufacturing. Let's delve deeper into each step:
Step 1: Create a New Part Document
- Open SolidWorks: Launch the SolidWorks software on your computer.
- New Part Document: Choose to create a new part document. You'll be presented with various templates; select the one that's specific to sheet metal design.
The sheet metal template provides the necessary environment and tools tailored for sheet metal modeling.
Step 2: Sketch the Base Profile
- Use Sketch Tools: Activate the sketching environment and utilize tools like lines, arcs, circles, rectangles, and more to create the outline of your sheet metal part's base profile.
- Apply Dimensions and Constraints: Apply dimensions to define the sizes and positions of the sketch elements. Constraints ensure the sketch maintains its intended shape while being adjustable.
- Add Cutouts, Holes, or Features: Within the sketch, you can add cutouts, holes, fillets, or other features that are integral to the design of your sheet metal part.
Step 3: Apply Sheet Metal Features
- Base Flange Feature: Access the Sheet Metal toolbar and select the "Base Flange" feature. This is where you'll begin transforming your 2D sketch into a 3D sheet metal part.
- Select Sketch Profile: Choose the sketch you created in the previous step as the contour for the base flange. This profile will form the basis for your sheet metal part's shape.
- Define Parameters: Specify parameters for the base flange, including the material type, thickness, and bend radius. These parameters are crucial for accurate representation and manufacturing simulation.
Step 4: Add Bend Relief and Corner Relief
- Bend Relief: For areas of the sheet metal part that will undergo bending, apply bend reliefs. These relief cuts help prevent material distortion or tearing during the bending process.
- Corner Relief: Choose the appropriate corner relief type for each corner of the part. SolidWorks offers options for square, circular, and tear-drop corner reliefs.
Step 5: Create Cuts and Bends
- Cut-Extrude: Utilize the "Cut-Extrude" feature to create holes, cutouts, or openings in the sheet metal part. Specify the dimensions and positions of these features as needed.
- Edge Flange: Apply the "Edge Flange" feature to create bends along the edges of the sheet metal part. This step transforms the flat part into its bent form.
Step 6: Generate the Flat Pattern
- Flat Pattern Feature: Activate the "Flat Pattern" feature. This feature calculates and generates the flat, unfolded representation of your sheet metal part. It's the critical information needed for manufacturing.
- Review Accuracy: Thoroughly review the generated flat pattern. Ensure that all bends, cuts, and reliefs are accurately represented and that the dimensions match your design intentions.
Step 7: Add Additional Features
- Additional Features: If your sheet metal design requires additional features like gussets, tabs, or notches, apply these features at this stage.
Step 8: Create Drawings
- Generate Manufacturing Drawings: Create manufacturing drawings that include details about the flat pattern, bend lines, hole locations, and dimensions. This drawing provides the information manufacturers need to fabricate your part accurately.
- Annotations and Notes: Add annotations, dimensions, and notes to the drawing to communicate specific instructions to the manufacturer. These details ensure that your design is properly understood and produced.
Step 9: Collaboration and Review
- Share Designs: Share your SolidWorks file or the generated manufacturing drawings with colleagues, collaborators, or manufacturers for review and feedback.
- Incorporate Feedback: Review the feedback received and make any necessary design adjustments based on the input from stakeholders. Addressing issues at this stage prevents costly changes during manufacturing.
Step 10: Finalize Design
- Final Adjustments: Make any final tweaks or adjustments to the design based on feedback and reviews. Ensure that the design is accurate and meets all functional and aesthetic requirements.
- Manufacturability Check: Verify that the design is manufacturable without any issues. Check for interference, manufacturability constraints, and feasibility.
Once you've completed these steps, you'll have successfully created a sheet metal part using SolidWorks. The result is a well-designed, accurately represented part ready for fabrication. SolidWorks' dedicated sheet metal tools and features streamline the process and ensure that your designs translate smoothly from the virtual environment to the physical world.
Best Practices for SolidWorks Sheet Metal Design
To create effective and efficient sheet metal designs in SolidWorks, consider the following best practices:
- Understand Manufacturing Processes: Familiarize yourself with sheet metal manufacturing processes, such as bending, forming, and cutting. Design parts that can be fabricated using available equipment and techniques.
- Material Selection: Choose appropriate sheet metal materials based on factors like strength, corrosion resistance, and cost. SolidWorks provides a material library to assist in accurate simulations.
- Minimize Welding: Minimize the need for welding by designing parts that can be formed from a single sheet with minimal joining. This reduces fabrication complexity and costs.
- Use Standard Components: Incorporate standard hardware and fasteners whenever possible to simplify assembly and reduce manufacturing lead times.
- Consider Tolerances: Account for manufacturing tolerances in your design to ensure the proper fit and functionality of assembled parts.
- Validate Design: Use SolidWorks simulation tools to perform virtual testing and validation of your sheet metal designs under different loading conditions.
- Organize Feature Tree: Keep your feature tree organized and well-structured for easy editing and modifications as the design evolves.
- Collaborate Effectively: Leverage SolidWorks' collaboration tools to share designs, review models, and make changes based on feedback from team members and stakeholders.
Conclusion
SolidWorks sheet metal design empowers engineers and designers to create intricate and functional sheet metal parts with ease. With its specialized features, accurate flat pattern generation, and parametric capabilities, SolidWorks streamlines the sheet metal design process from concept to fabrication. By following best practices and mastering key features, designers can create innovative and manufacturable sheet metal designs that meet the demands of modern manufacturing industries. Whether you're designing simple brackets or complex enclosures, SolidWorks is an indispensable tool for achieving success in sheet metal design.