- Understanding Simulation and Design Validation
- The Power of SolidWorks Simulation
- Early Detection of Design Flaws
- Optimizing Design Performance
- Reduced Cost and Time-to-Market
- Enhanced Safety and Reliability
- Iterative Design Improvement
- Complex Behavior Analysis
- Static Analysis
- Dynamic Analysis
- Thermal Analysis
- Fluid Flow Analysis
- Fatigue Analysis
- Model Preparation
- Applying Boundary Conditions and Loads
- Meshing
- Solving the Simulation
- Analysis of Results
- Optimization and Iteration
- Final Design Decision
- Automotive
- Aerospace
- Consumer Electronics
- Medical Devices
- Industrial Equipment
- Accurate Material Properties
- Complex Geometry
- Sensitivity to Input Conditions
- Verification and Validation
- Conclusion
In the world of product design and engineering, ensuring the reliability and performance of a new design is crucial before it goes into production, and it can also be crucial when you need to complete your simulation assignment. The cost of fixing design flaws after production can be astronomical, not to mention the potential damage to a company's reputation. This is where simulation tools like SolidWorks Simulation come into play. SolidWorks Simulation allows engineers and designers to virtually test and analyze their designs, simulating real-world conditions and behaviors to validate and optimize their designs before they are built. In this article, we will explore the significance of SolidWorks Simulation in design validation and understand how it empowers engineers to create better products.
Understanding Simulation and Design Validation
Simulation, in the context of engineering, refers to the process of creating a digital representation of a real-world system or process and using mathematical models to predict its behavior. Design validation involves confirming that a design meets the desired performance and safety criteria. Traditionally, this validation process relied heavily on physical prototypes and testing, which can be time-consuming, expensive, and often limited in the insights they provide. SolidWorks Simulation revolutionizes this process by enabling engineers to simulate various conditions and scenarios digitally.
This allows them to predict how a design will behave under different loads, pressures, temperatures, and other environmental factors. By replicating real-world conditions in a virtual environment, engineers can identify potential issues, optimize designs, and make informed decisions early in the design cycle, reducing the need for costly iterations later on.
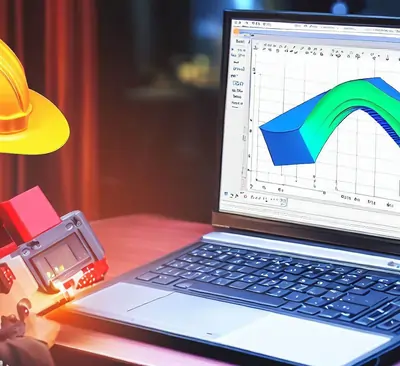
The Power of SolidWorks Simulation
Discover the transformative potential of SolidWorks Simulation. With its advanced capabilities, it empowers you to explore, validate, and optimize your designs with confidence. Let’s explore this deeper:
Early Detection of Design Flaws
One of the most significant advantages of SolidWorks Simulation is its ability to uncover design flaws at an early stage. Engineers can subject their designs to a range of stress, strain, and dynamic simulations, revealing potential weak points, deformation, or failure. This early detection helps prevent expensive design revisions and iterations during the later stages of development.
Optimizing Design Performance
SolidWorks Simulation provides insights into how a design can be optimized for maximum performance. Engineers can experiment with different materials, shapes, and configurations to achieve the desired outcomes. For example, they can determine the optimal thickness of a structure to minimize weight while maintaining structural integrity, or they can refine the shape of a component to improve fluid dynamics.
Reduced Cost and Time-to-Market
By eliminating the need for physical prototypes and extensive testing, SolidWorks Simulation reduces both costs and time-to-market. Companies can allocate resources more efficiently by focusing on designs that have already been validated virtually. This accelerated development cycle can be a game-changer in competitive industries where being first to market can make a significant difference.
Enhanced Safety and Reliability
For products where safety is a critical factor, such as aerospace or medical devices, SolidWorks Simulation provides a comprehensive understanding of how a design will perform under extreme conditions. Engineers can ensure that products will withstand worst-case scenarios and meet industry safety standards, reducing the risk of failures in real-world applications.
Iterative Design Improvement
Simulation isn't a one-time process. It's an iterative journey of refinement. SolidWorks Simulation allows engineers to make small adjustments to their designs and re-run simulations instantly. This iterative approach helps fine-tune designs, progressively eliminating weaknesses and enhancing overall performance.
Complex Behavior Analysis
Real-world systems often exhibit complex behaviors that can't be easily predicted through manual calculations. SolidWorks Simulation excels in handling such complexities, whether it's analyzing nonlinear material behavior, intricate contact interactions, or dynamic responses to varying loads. This depth of analysis provides a more accurate representation of real-world behavior.
Types of Simulations in SolidWorks Simulation
SolidWorks Simulation offers a diverse array of simulation types, each tailored to address specific aspects of design validation. These simulations allow engineers and designers to thoroughly analyze their models, predict behavior, and optimize designs for real-world conditions. Let's delve deeper into each of these simulation types:
Static Analysis
Static analysis involves studying how a design responds to a constant load or set of loads without any changes over time. This type of simulation is ideal for understanding the structural behavior of a design under various static loads. Engineers can determine factors such as stress distribution, deformation, and strain. Static analysis is invaluable for identifying stress concentrations and potential failure points in a design. By subjecting the design to different loading scenarios, engineers can make informed decisions about material selection, geometry modifications, and reinforcement strategies.
Dynamic Analysis
Dynamic analysis, in contrast to static analysis, considers the effects of time-varying loads, impacts, vibrations, and other dynamic forces. This simulation type is essential for assessing how a design responds to real-world scenarios with changing conditions. For example, in the automotive industry, dynamic analysis can help evaluate the response of a vehicle's suspension system to various road conditions. Engineers can predict how components will react to shocks, vibrations, and rapid changes in load. Dynamic analysis aids in optimizing designs for stability, durability, and performance in dynamic environments.
Thermal Analysis
Thermal analysis evaluates how a design reacts to changes in temperature. Engineers can predict temperature distribution, identify hotspots, and ensure that components operate within safe thermal limits. This simulation type is crucial for products that generate or dissipate heat, such as electronic devices, engines, and industrial machinery. Thermal analysis helps prevent overheating, which can lead to premature failures. By understanding how heat is transferred within a design, engineers can make informed decisions about heat sink placement, insulation, and cooling mechanisms.
Fluid Flow Analysis
Fluid flow analysis focuses on simulating the behavior of liquids and gases within a design. This type of simulation is particularly valuable for optimizing fluid dynamics in various applications, such as aerodynamics, HVAC systems, and industrial processes. Engineers can analyze how fluids move, how pressure distributions change, and where flow separation might occur. For instance, in aerospace engineering, fluid flow analysis can aid in designing more efficient and aerodynamic aircraft components. By optimizing fluid flow, engineers can enhance performance, reduce energy consumption, and minimize drag.
Fatigue Analysis
Fatigue analysis is concerned with predicting the lifespan of a design subjected to repetitive loading and unloading cycles. Many products, especially those exposed to ongoing stress, are susceptible to fatigue failure over time. Fatigue analysis helps engineers determine the durability of a design and whether it can withstand prolonged use without failing. This type of simulation is vital for applications where safety is paramount, such as medical implants or critical structural components. By identifying potential fatigue-related issues early on, engineers can design products that maintain their integrity over their expected lifespan.
Steps in a SolidWorks Simulation Process
The utilization of SolidWorks Simulation involves a systematic process to ensure accurate and reliable results. Here are the key steps in this process:
Model Preparation
The process begins with creating a detailed 3D model of the design using SolidWorks CAD software. This model serves as the foundation for simulation and analysis. The accuracy of the model is crucial as simulation results depend on the fidelity of the representation.
Applying Boundary Conditions and Loads
Engineers define the conditions under which the design will operate by applying boundary conditions, loads, pressures, temperatures, and restraints to the model. This step replicates the real-world environment in which the design will function. For example, in a static analysis of a bridge, engineers might simulate the weight of vehicles on the bridge as a load.
Meshing
Meshing is the process of dividing the 3D model into smaller elements or finite elements. These elements are the building blocks for numerical analysis. Proper meshing is essential for accurately solving the mathematical equations that describe the behavior of materials and structures. The mesh density should be balanced to capture both overall trends and local variations.
Solving the Simulation
The simulation software performs complex calculations based on the applied loads, constraints, material properties, and meshing. This step generates a detailed analysis of how the design will respond to the specified conditions. The solver iteratively solves equations to predict deformations, stresses, temperatures, and other relevant parameters.
Analysis of Results
Engineers analyze the simulation results to gain insights into stress distribution, deformation patterns, safety factors, temperature variations, and more. This analysis guides design decisions and improvements. Engineers can pinpoint areas of concern and understand how the design performs under different conditions, allowing them to address potential issues before production.
Optimization and Iteration
Based on the analysis of simulation results, engineers can make design adjustments to enhance performance and address any identified concerns. These changes are followed by re-running simulations to validate the impact of improvements. Iterative optimization ensures that the design meets desired criteria and performs optimally.
Final Design Decision
Once a design iteration meets all performance, safety, and reliability criteria, it can be considered for final production. SolidWorks Simulation provides engineers with the confidence to move forward with manufacturing, knowing that the design has undergone rigorous virtual testing. This step greatly reduces the risk of unexpected failures in the real-world application.
Real-World Applications
SolidWorks Simulation finds applications in a wide range of industries:
Automotive
Automotive engineers use simulation to evaluate the safety of vehicle structures in crashes, optimize suspension systems, and enhance fuel efficiency by analyzing aerodynamics.
Aerospace
In aerospace, simulation ensures the structural integrity of aircraft components, predicts the effects of vibrations during flight, and assesses the impact of extreme conditions.
Consumer Electronics
For consumer electronics, simulation aids in thermal management, predicting how devices will dissipate heat, and ensuring they won't overheat during use.
Medical Devices
Simulation is critical for medical devices, helping design implants that withstand biological forces, modeling fluid flow in medical equipment, and ensuring the safety of diagnostic tools.
Industrial Equipment
Engineers can simulate the performance of industrial machinery under varying loads, ensuring reliability and safety in manufacturing environments.
Overcoming Challenges and Limitations
While SolidWorks Simulation offers numerous benefits, there are certain challenges and limitations to consider:
Accurate Material Properties
Simulation results heavily depend on accurate material properties. Obtaining precise data can be challenging, especially for new or unique materials.
Complex Geometry
Simulation becomes more intricate with complex geometries. Meshing and analyzing such designs might require advanced techniques and increased computational resources.
Sensitivity to Input Conditions
Small variations in input conditions can lead to significant changes in simulation outcomes. Engineers must be cautious when setting up simulations to ensure accurate results.
Verification and Validation
Simulation models need to be verified and validated against physical tests to ensure their accuracy and reliability. This process can be time-consuming and resource-intensive.
The Future of Simulation in Design
As technology continues to advance, the capabilities of simulation software like SolidWorks Simulation are poised to grow even further. Predictive capabilities might become more accurate, real-time simulations could become more feasible, and integration with artificial intelligence could streamline the optimization process.
Conclusion
SolidWorks Simulation has transformed the landscape of product design and engineering by allowing virtual testing of designs under real-world conditions. This simulation-driven approach enhances design validation, reduces costs, accelerates time-to-market, and ultimately leads to the creation of safer and more reliable products. As industries continue to innovate, SolidWorks Simulation will remain a crucial tool for engineers and designers striving to push the boundaries of what's possible while ensuring the highest standards of quality and performance.