- Understanding SolidWorks Weldment
- Common Challenges in SolidWorks Weldment Assignments
- 1. Incorrect Sketching Techniques
- Solution: Mastering Sketching Best Practices
- 2. Inaccurate Material Selection
- Solution: Conduct Thorough Material Analysis
- 3. Weldment Profile Customization Problems
- Solution: Mastering Profile Customization
- 4. Assembly and Part Mismatches
- Solution: Consistent Naming and Referencing
- 5. Weldment Cut List Errors
- Solution: Validate and Update Cut List Properties
- Conclusion
Embarking on SolidWorks Weldment assignments can be a gratifying endeavor, but it's not without its hurdles. As design enthusiasts delve into the intricate world of welded structures, they often find themselves grappling with a spectrum of challenges that demand adept troubleshooting. This H1, "Troubleshooting Common Challenges in SolidWorks Weldment Assignments," serves as a beacon for engineers and designers seeking to navigate the complexities of Weldment projects. From sketching intricacies to material selection conundrums, this comprehensive guide addresses the most prevalent issues encountered during the design process, offering insightful solutions to empower users in overcoming obstacles and optimizing their SolidWorks experience. If you need help with your Weldment assignment, consider consulting this guide for valuable assistance in tackling common challenges.
In the realm of SolidWorks Weldment assignments, achieving seamless precision requires a keen understanding of potential stumbling blocks. This H1 title encapsulates the essence of the blog, inviting readers to explore a treasure trove of troubleshooting techniques tailored to the unique demands of Weldment projects. Whether it's ensuring accurate sketching practices, making informed material selections, or mastering profile customization, this guide promises to be an indispensable resource for anyone navigating the challenges inherent in SolidWorks Weldment assignments. Through a lens of practical solutions and strategic insights, the blog aims to equip users with the knowledge needed to not only troubleshoot issues effectively but also elevate the quality and efficiency of their Weldment designs.
Understanding SolidWorks Weldment
SolidWorks Weldment is a robust feature within the SolidWorks suite, designed to empower engineers and designers in the creation of intricate welded structures. This tool is particularly invaluable when working on projects involving frameworks, machinery, or any application requiring welded components. At its core, SolidWorks Weldment simplifies the often complex process of designing these structures by offering a comprehensive set of tools. Users can effortlessly create weldment profiles, customize sections, and simulate weldments to ensure structural integrity. Understanding the nuances of SolidWorks Weldment is crucial for harnessing its full potential and avoiding common pitfalls. From sketching the initial framework to generating accurate cut lists, a profound comprehension of this feature streamlines the design workflow and contributes to the creation of precise and efficient welded structures.
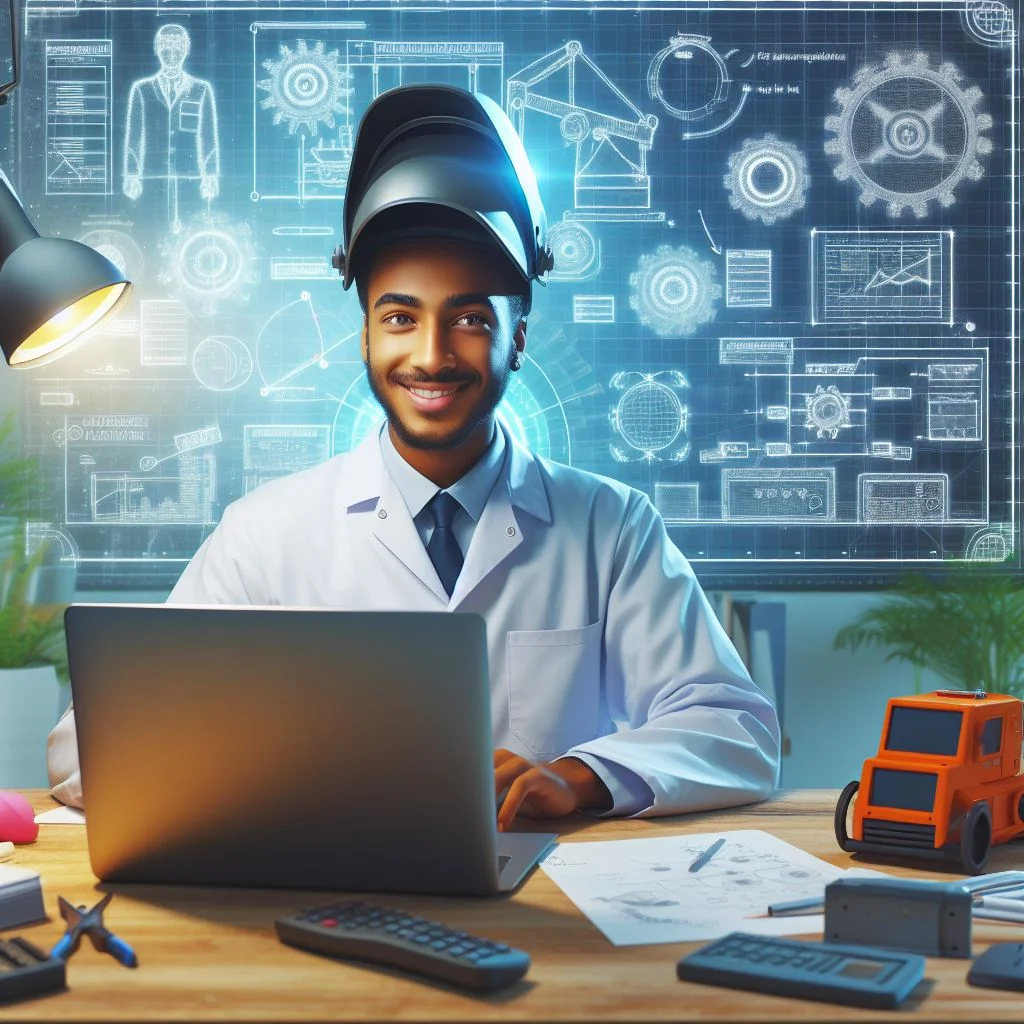
Common Challenges in SolidWorks Weldment Assignments
Embarking on SolidWorks Weldment assignments can be both exhilarating and demanding for engineers and designers. As professionals strive to bring intricate structural designs to life, they inevitably encounter a spectrum of challenges that can impede the seamless progression of their projects. From the nuances of sketching techniques to the complexities of assembly and part matching, the journey through SolidWorks Weldment assignments is dotted with hurdles that demand attention and expertise. This H1 explores these common challenges, unraveling the intricacies and offering insightful solutions to empower users in overcoming obstacles and elevating their proficiency in SolidWorks Weldment design.Now, let's delve into the common challenges users encounter when working on Weldment assignments and how to overcome them.
1. Incorrect Sketching Techniques
When it comes to SolidWorks Weldment assignments, the foundation lies in the precision of sketching techniques. One prevalent challenge that users encounter revolves around the incorrect application of sketching methods. This issue often leads to unanticipated errors throughout the design process. Inadequate sketching can result in undefined shapes, inconsistent dimensions, and difficulties in creating a cohesive structural framework. To address this challenge effectively, it is essential to delve into mastering sketching best practices. By ensuring that sketches are fully defined, employing proper constraints, and utilizing tools like the "Fully Define Sketch" option, users can eliminate ambiguity in their sketches. Additionally, incorporating references and relations to anchor sketches to key points enhances accuracy, setting the stage for a seamless SolidWorks Weldment design.A fundamental step in creating a Weldment structure is sketching the desired shape. However, users often face issues with sketches that lead to errors in the final design. To troubleshoot this:
Solution: Mastering Sketching Best Practices
In tackling the challenge of incorrect sketching techniques within SolidWorks Weldment assignments, mastering sketching best practices is paramount. To overcome this issue, it's essential to ensure that sketches are meticulously defined, leaving no room for ambiguity. Utilize the "Fully Define Sketch" option within SolidWorks to automatically apply necessary constraints, guaranteeing the completeness of your sketches. Furthermore, leverage references and relations to anchor your sketch to critical points, fostering accuracy throughout the entire design process. By adopting these sketching best practices, you not only enhance the precision of your Weldment structures but also create a solid foundation for a seamless and error-free design journey.
2. Inaccurate Material Selection
A critical aspect of any Weldment assignment is the selection of materials, as it profoundly influences the structural integrity and performance of the final design. The challenge often lies in accurately identifying the most suitable materials for the project at hand. Incorrect material selection can lead to a host of issues, including compromised strength, unexpected weight distribution problems, and challenges during the fabrication process. To overcome this hurdle, it's essential to conduct a thorough analysis of the project requirements. Consider factors such as load-bearing capacity, environmental conditions, and the intended application. SolidWorks provides a comprehensive material library, offering a vast array of pre-defined materials with detailed properties, aiding designers in making informed decisions and ensuring the optimal performance of the Weldment structure. By addressing the challenge of inaccurate material selection, designers pave the way for a Weldment design that not only meets but exceeds expectations.
Solution: Conduct Thorough Material Analysis
One of the pivotal challenges in SolidWorks Weldment assignments often lies in the selection of materials. To overcome this hurdle, it is imperative to conduct a comprehensive material analysis before finalizing your design. Begin by understanding the specific requirements of your project, considering factors such as structural strength, weight considerations, and environmental influences. SolidWorks provides a rich material library equipped with detailed properties, allowing users to make informed decisions. By meticulously evaluating and selecting the most suitable material for your Weldment project, you not only ensure the structural integrity of your design but also mitigate potential issues that may arise during assembly or fabrication. Thorough material analysis serves as a cornerstone in the successful resolution of challenges encountered in SolidWorks Weldment assignments, paving the way for a robust and efficient design process.
3. Weldment Profile Customization Problems
Customizing weldment profiles is a crucial aspect of SolidWorks Weldment assignments, yet users often grapple with challenges in this intricate process. Creating profiles tailored to specific project requirements can be demanding, leading to errors and design inconsistencies. Common problems include difficulties in accurately defining dimensions, constraints, and ensuring proper alignment within the weldment structure. Mastering profile customization is essential for achieving precision and avoiding downstream issues in the design. In this section, we'll delve into effective solutions to streamline the profile customization process, empowering users to navigate through these challenges seamlessly.
Solution: Mastering Profile Customization
In addressing the challenges associated with profile customization in SolidWorks Weldment assignments, mastering this aspect of the design process is paramount. Proficient profile customization involves a thorough understanding of the tools and features available within SolidWorks. Users should familiarize themselves with the Profile Library and its extensive range of predefined profiles, while also honing the skill of creating custom profiles tailored to specific project requirements. By paying meticulous attention to dimensions, constraints, and geometric properties, designers can ensure that their custom profiles seamlessly integrate into the Weldment structure. Furthermore, exploring advanced features such as symmetric profiles and mirroring options can enhance efficiency and precision. SolidWorks provides a user-friendly interface that encourages experimentation and iteration, allowing designers to refine their profile customization skills and produce flawless Weldment designs. Through dedication to mastering profile customization, users can elevate the quality of their SolidWorks Weldment assignments and streamline the overall design workflow.
4. Assembly and Part Mismatches
Assembly and part mismatches can disrupt the harmony of your SolidWorks Weldment project, causing confusion and hindering the design process. These discrepancies often emerge when components fail to align correctly, leading to potential errors in the final assembly. To address this challenge, meticulous attention to detail is paramount. Start by adopting consistent naming conventions for both parts and assemblies, ensuring clarity in references. Regularly review and update your assembly to catch and rectify any mismatches early in the design phase. By fostering precision in the relationship between parts and assemblies, you pave the way for a seamless and error-free SolidWorks Weldment experience.
Solution: Consistent Naming and Referencing
Ensuring a smooth SolidWorks Weldment design process involves maintaining a high level of consistency in naming conventions and referencing throughout the assembly. When parts and assemblies are given clear and logical names, it not only enhances the organization of the project but also minimizes the risk of errors. Adopt a standardized naming system for components, making it intuitive and reflective of their function in the overall assembly. Additionally, pay close attention to references between parts, ensuring that each component aligns seamlessly with the design intent. Regularly reviewing and validating the naming and referencing system will help catch discrepancies early in the design stage, contributing to a more efficient and error-free SolidWorks Weldment assignment.
5. Weldment Cut List Errors
Creating an accurate Weldment Cut List is essential for the success of any SolidWorks Weldment assignment, yet users frequently encounter challenges related to cut list errors. These issues may manifest as discrepancies in identifying structural members, inaccuracies in length measurements, or misrepresentation of materials. When faced with Weldment Cut List errors, it's crucial to address them promptly to prevent misunderstandings during the fabrication phase. By meticulously validating and updating cut list properties, users can ensure that each structural element is correctly identified, and essential details such as length, material, and size are accurately reflected. SolidWorks provides convenient tools for this purpose, making it feasible to maintain a precise and error-free Weldment Cut List throughout the design process.
Solution: Validate and Update Cut List Properties
Ensuring accuracy in the Weldment Cut List is paramount for a seamless fabrication process. To tackle this challenge, a systematic approach to validating and updating cut list properties is essential. Begin by meticulously reviewing each structural member's identification, confirming that it aligns with the intended design. Pay close attention to crucial properties such as length, material, and size, rectifying any discrepancies. SolidWorks offers a user-friendly interface to validate and update cut list properties efficiently. By regularly employing this solution, designers can maintain precision in their Weldment assignments, providing clarity and accuracy in the fabrication phase. Consistent validation not only prevents errors but also contributes to a more streamlined and error-free workflow, ensuring that the final product adheres to the specified design parameters.
Conclusion
SolidWorks Weldment is a powerful tool that significantly streamlines the design process for welded structures. However, challenges are inevitable, and the key to a successful Weldment assignment lies in understanding and effectively troubleshooting these issues.
By mastering sketching techniques, conducting thorough material analyses, customizing profiles with precision, maintaining consistency in assembly, and validating cut list properties, users can overcome common challenges in SolidWorks Weldment assignments. Remember, continuous learning and exploration of SolidWorks features will further enhance your proficiency in tackling any hurdles that may arise.
In conclusion, with the right knowledge and troubleshooting strategies, SolidWorks Weldment assignments can be a rewarding and efficient experience for engineers and designers alike.