- Understanding SolidWorks Weldment
- Pros of SolidWorks Weldment:
- Cons of SolidWorks Weldment:
- Traditional Welding: The Conventional Approach
- Pros of Traditional Welding:
- Cons of Traditional Welding:
- Making the Choice: SolidWorks Weldment or Traditional Welding?
- Conclusion:
SolidWorks, renowned for its capabilities in 3D computer-aided design (CAD), has significantly transformed the landscape of welding through its advanced Weldment feature. This particular tool stands as a testament to the software's commitment to providing efficient solutions for engineers and designers engaged in the creation of intricate welded structures. Exploring SolidWorks' Weldment feature can provide valuable insights and assistance in mastering the intricacies of welded structure design.
The Solidworks Weldment feature emerges as a game-changer, facilitating the streamlined design of welded structures with a level of efficiency that sets it apart. Engineers and designers utilizing SolidWorks find themselves equipped with a tool that not only simplifies the process but also enhances precision in the creation of complex structures. The advanced features within the Weldment module allow for the seamless integration of various structural elements, providing a comprehensive solution for those dealing with welding projects of diverse complexities.
One of the standout advantages of SolidWorks Weldment is its user-friendly interface, which empowers users to navigate through the design process with ease. The intuitive nature of the software ensures that even those less experienced in 3D CAD can quickly adapt and harness the full potential of the Weldment feature. This ease of use becomes particularly advantageous when compared to the learning curve associated with traditional welding methods.
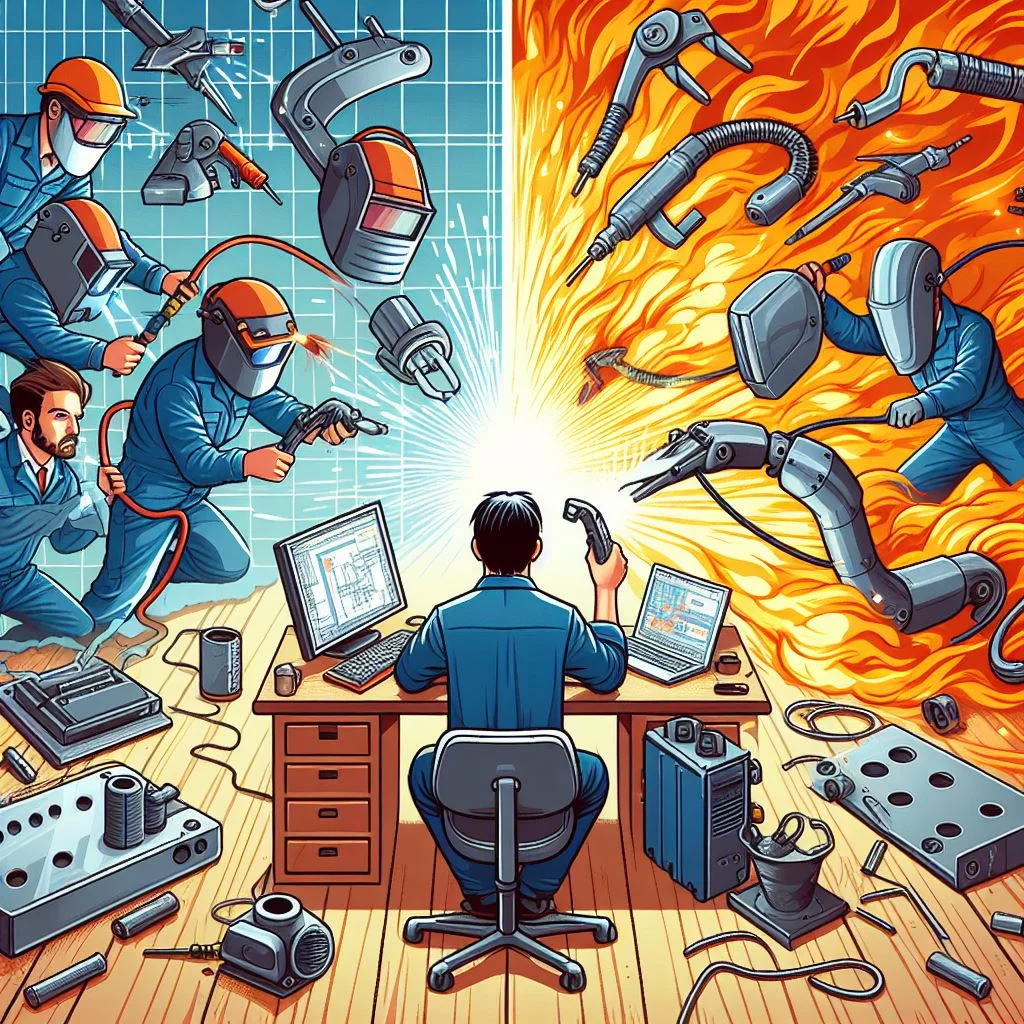
The inclusion of a standardized library within SolidWorks Weldment further elevates its utility. The library contains a plethora of standard structural profiles that users can readily access and incorporate into their designs. This not only expedites the design phase but also contributes to maintaining consistency and adherence to industry standards. Designers can efficiently select and implement common structural elements, saving valuable time in the process.
Parametric modeling stands out as another notable feature of SolidWorks Weldment. This functionality allows for easy incorporation of design changes, ensuring that the model remains adaptable throughout the various stages of the project. This flexibility is a significant advantage in dynamic engineering environments where alterations to the original design are commonplace.
Additionally, the automated Bill of Materials (BOM) generation feature within SolidWorks Weldment simplifies the documentation process. By automatically compiling a detailed list of materials used in the design, the software reduces the likelihood of errors in material selection and provides an invaluable resource for project management. This automated approach not only saves time but also enhances the accuracy of the documentation, a critical aspect in any welding project.
However, as with any technology, SolidWorks Weldment comes with its set of challenges. For newcomers to 3D CAD software, there exists a learning curve that requires an investment of time and effort to master. While the intuitive interface eases the transition, users need to dedicate resources to become proficient in leveraging the full potential of SolidWorks Weldment.
Another consideration is the cost associated with acquiring SolidWorks licenses. The software operates on a commercial basis, and the initial investment in licenses can be a significant factor for smaller businesses or individual users. Additionally, running SolidWorks Weldment efficiently demands a computer system with substantial processing power and memory, adding to the overall cost of implementation.
In conclusion, SolidWorks Weldment emerges as a powerful tool that significantly enhances the efficiency and precision of welding projects. Its user-friendly interface, standardized libraries, parametric modeling, and automated BOM generation contribute to a seamless design process. However, the learning curve and associated costs must be weighed against the benefits, especially for smaller-scale projects or those with budget constraints. As technology continues to advance, SolidWorks Weldment stands at the forefront of innovation, offering a glimpse into the future of welding design and fabrication.
Understanding SolidWorks Weldment
SolidWorks Weldment, a dedicated tool within the software, is ingeniously crafted to address the specific needs of welding applications. Its purpose is to simplify and enhance the process of creating welded structures, offering a suite of features meticulously designed for the unique requirements of welding projects.
The heart of SolidWorks Weldment lies in its ability to expedite the design process while maintaining precision. Users can leverage an intuitive interface that seamlessly integrates with a variety of structural profiles. This integration significantly reduces the time and effort required to create complex welded structures, making it an invaluable asset for engineers and designers.
One notable feature is the inclusion of standardized libraries containing a wide array of structural profiles. These libraries empower users with the flexibility to choose from pre-defined elements, ensuring consistency and conformity to industry standards. The utilization of parametric modeling further amplifies efficiency, allowing for swift adjustments to the design as needed.
Additionally, SolidWorks Weldment goes beyond mere design capabilities by automating the generation of Bills of Materials (BOM). This automation not only expedites the documentation process but also minimizes the likelihood of errors in material lists, contributing to the overall accuracy of the welding project.
In essence, SolidWorks Weldment is a sophisticated tool that brings together efficiency, flexibility, and precision, making it an indispensable asset for those engaged in the intricate world of welding design.
Pros of SolidWorks Weldment:
SolidWorks Weldment stands out for its multitude of advantages that cater specifically to welding applications. Let's delve deeper into the notable benefits:
- Efficiency in Design: SolidWorks Weldment's efficiency in design extends beyond just speed. The software's intuitive interface empowers designers to swiftly conceptualize and refine intricate welded structures. This not only accelerates the design phase but also enhances the overall productivity of the project, making it an ideal choice for time-sensitive endeavors.
- Standardized Libraries: The inclusion of standardized libraries within SolidWorks Weldment is a game-changer for designers and engineers. With a diverse array of pre-defined structural profiles at their disposal, users can effortlessly select and incorporate common elements into their welding projects. This not only streamlines the design process but also contributes to the consistency and standardization of structural components.
- Parametric Modeling: Parametric modeling is a cornerstone of SolidWorks Weldment's flexibility. This feature allows for seamless adaptation to evolving project requirements. Design changes can be effortlessly integrated, ensuring that the model remains dynamic and responsive to adjustments. This level of flexibility is particularly valuable in projects where design iterations are common, providing a robust foundation for creative exploration and problem-solving.
- Automated Bill of Materials (BOM): SolidWorks Weldment goes beyond design by automating the creation of a Bill of Materials (BOM). This feature is a time-saving boon, as it instantly compiles an accurate list of materials required for the welding project. The automated BOM not only expedites the documentation process but also minimizes the risk of manual errors, ensuring that the project progresses smoothly with the correct materials in place.
- Interference Detection: Ensuring the structural integrity of a welded assembly is paramount, and SolidWorks Weldment addresses this concern through its interference detection capabilities. The software adeptly identifies potential interferences within the design, allowing designers to rectify issues before they manifest in the physical construction. This proactive approach enhances the reliability of the final product, instilling confidence in the structural soundness of the welded assembly.
Cons of SolidWorks Weldment:
- Learning Curve: Mastery of SolidWorks Weldment requires time and effort, especially for users new to 3D CAD software. The software's extensive capabilities may overwhelm beginners, necessitating comprehensive training to unlock its full potential. This initial learning curve can lead to delays in project timelines as users familiarize themselves with the intricacies of the tool.
- Software Cost: SolidWorks is a commercial software, and obtaining licenses can be costly for smaller businesses or individual users. While the investment can be justified for larger enterprises with frequent welding projects, smaller entities may find the upfront expense prohibitive. Exploring alternative licensing options or considering the long-term benefits is crucial when assessing the financial impact.
- System Requirements: Running SolidWorks Weldment efficiently demands a computer system with substantial processing power and memory. This requirement can pose challenges for users with outdated hardware, as upgrading may incur additional costs. Ensuring compatibility with the software's system requirements is essential to avoid performance issues and maintain a smooth workflow. Regular updates and advancements in SolidWorks may necessitate periodic hardware upgrades to keep pace with evolving technology.
Traditional Welding: The Conventional Approach
Traditional welding methods have indeed stood as the backbone of structural fabrication for decades, forming the very essence of metalworking and construction. The reliance on skilled welders and manual processes is deeply rooted in the craftsmanship and expertise these artisans bring to their work. A seasoned welder not only welds joints but also infuses an element of artistry into their creations, creating welds that not only serve a structural purpose but also possess an aesthetic appeal.
One of the distinctive aspects of traditional welding lies in its adaptability to various settings and materials. From the construction of towering skyscrapers to the meticulous assembly of delicate metal artworks, traditional welding methods have proven their versatility. The hands-on nature of traditional welding allows for a level of adaptability that can be challenging to replicate with automated processes. This adaptability has made traditional welding a preferred choice for unique or custom projects where a personal touch and craftsmanship are paramount.
While traditional welding may be labor-intensive, with skilled personnel dedicating time and effort to manual welding tasks, the results often reflect the dedication and expertise of the welder. The limitations of traditional welding, such as longer production times and potential inconsistencies, are balanced by the human touch and the ability to achieve welds that go beyond mere structural requirements. As industries evolve, striking a balance between the traditional artistry of welding and the efficiency of modern technologies becomes key to meeting the diverse demands of structural fabrication.
Pros of Traditional Welding:
- Welding Artistry: Skilled welders can bring a level of artistry to their work, creating visually appealing welds that may be challenging to achieve with automated processes. The intricate and personalized touch in traditional welding allows for creative expression, making it suitable for projects where aesthetics play a significant role. This artistic flair can result in unique designs that stand out, showcasing the welder's craftsmanship and attention to detail.
- Adaptability: Traditional welding methods can be employed in diverse settings and for various materials, offering flexibility in application. From working on construction sites to fabricating custom pieces in a workshop, traditional welding adapts seamlessly to different environments. Moreover, it accommodates a wide range of materials, making it a versatile choice for projects involving various metals and alloys. The adaptability of traditional welding contributes to its enduring popularity across different industries.
- Cost-Effective for Small Projects: For small-scale projects, traditional welding setups might be more cost-effective than investing in CAD software licenses. In situations where the complexity of a project doesn't justify the expense of implementing CAD software, traditional welding remains a viable and budget-friendly option. The initial investment in welding equipment and skilled labor may be more economical for projects with limited scope, ensuring a practical approach to cost-effectiveness without compromising on quality.
Cons of Traditional Welding:
- Labor-Intensive: Traditional welding can be labor-intensive, requiring skilled personnel to manually perform welding tasks. The intricacies of handcrafted welds demand a keen eye and steady hand, contributing to prolonged work hours. Skilled welders invest substantial time in creating precise welds, making traditional welding suitable for projects where craftsmanship is paramount. However, this labor-intensive nature can lead to increased project durations, potentially affecting overall project timelines and costs.
- Limited Automation: The lack of automation in traditional welding processes may result in longer production times and potential inconsistencies. Unlike SolidWorks Weldment's automated precision, traditional welding relies on the expertise of welders to control every aspect of the process manually. This manual intervention can introduce variations in weld quality, impacting the overall structural integrity of the final product. Additionally, the absence of automated workflows may hinder the ability to meet tight production schedules, particularly in projects with high volume or strict timelines.
- Quality Control Challenges: Ensuring consistent quality across welds can be challenging, as it heavily relies on the skill level of the welder. Traditional welding places a significant burden on quality control measures, as variations in technique and skill among welders may result in inconsistencies in weld appearance and structural soundness. Implementing stringent quality control processes becomes crucial to address these challenges. Inspection and supervision are essential to detect and rectify any deviations from the desired standards, adding an extra layer of complexity to the overall welding process.
Making the Choice: SolidWorks Weldment or Traditional Welding?
The decision-making process between SolidWorks Weldment and traditional welding methods is multifaceted, involving careful consideration of project scale, budget constraints, and the desired level of precision.
Project Scale: For extensive projects characterized by intricate designs, SolidWorks Weldment's efficiency and automation present a clear advantage. The software's capability to reduce errors and expedite the design-to-fabrication process makes it an ideal choice for large-scale endeavors. The intricate nature of such projects often demands precision and consistency, areas where SolidWorks Weldment excels.
Conversely, traditional welding may find its niche in smaller projects where the potential cost of CAD software licenses outweighs the benefits of automation. While large-scale projects benefit from the streamlined processes of SolidWorks Weldment, smaller projects may find the manual approach of traditional welding more practical and cost-effective.
Budget Considerations: SolidWorks Weldment necessitates an upfront investment in software licenses and training. Despite this initial cost, companies engaged in numerous welding projects can realize long-term efficiency gains and a reduction in manual errors, justifying the initial financial outlay.
On the other hand, traditional welding setups offer a more budget-friendly alternative, particularly for one-off projects or smaller businesses operating with limited capital. The absence of substantial upfront software costs can make traditional welding an economically viable choice for those with constrained budgets.
Precision and Consistency: SolidWorks Weldment's strength lies in its ability to deliver precision and consistency. The software's parametric modeling and automated features contribute to the uniformity of design and execution, ensuring the production of high-quality welds across projects.
In contrast, traditional welding, while allowing for artistic expression, may encounter challenges in achieving the same level of precision consistently. The outcome often heavily relies on the skillset of individual welders, introducing variability that may be mitigated by the automated processes of SolidWorks Weldment.
Conclusion:
In the ever-evolving landscape of welding technologies, the debate between SolidWorks Weldment and traditional welding methods underscores the need for a nuanced approach. There is no universal solution that fits all scenarios; rather, the choice hinges on the distinct requirements of each project and the available resources.
SolidWorks Weldment, embedded within the powerful framework of 3D CAD software, introduces a paradigm shift in the realm of welding design. Its streamlined and automated features pave the way for efficient project execution, minimizing errors and accelerating the design-to-fabrication timeline. This is particularly advantageous for large-scale projects where precision and consistency are paramount. The software's parametric modeling and standardized libraries not only enhance accuracy but also contribute to the creation of intricate structures with ease.
On the flip side, traditional welding methods, steeped in a rich history of craftsmanship, bring a unique set of qualities to the table. The artistry and adaptability inherent in the hands-on approach of skilled welders allow for a level of customization and finesse that may be challenging to replicate with automated processes. Small-scale projects, where the cost of CAD software licenses might outweigh the benefits, can benefit from the cost-effectiveness and flexibility of traditional welding setups.
As technology continues its rapid evolution, the pursuit of finding the right balance between automation and traditional techniques becomes increasingly crucial. The advent of new tools and technologies, along with advancements in artificial intelligence and robotics, adds further complexity to this decision-making process.
Efforts to strike this delicate balance center on optimizing efficiency without compromising on the quality of welding projects. SolidWorks Weldment's ability to offer a standardized and automated approach aligns with the demand for precision and consistency in today's competitive landscape. However, it's essential to recognize that the human touch, the skilled hand of a welder, contributes a unique value that goes beyond the realm of automation.
The future of welding may witness a harmonious integration of these two approaches, where CAD software complements the expertise of welders rather than replacing it. Collaborative workflows that leverage the strengths of both SolidWorks Weldment and traditional welding methods could emerge as a winning strategy. For instance, the initial design and planning phases could leverage the efficiency of SolidWorks Weldment, while skilled welders take the reins during the actual fabrication, infusing their expertise into the process.
In conclusion, the SolidWorks Weldment vs. traditional welding debate signifies not a binary choice, but an ongoing evolution in the field of welding. The synergy between automated design processes and skilled craftsmanship holds the key to unlocking new possibilities and pushing the boundaries of what can be achieved in welding projects. As industries adapt to these changing dynamics, the quest for the right balance will continue to shape the future of welding, ensuring that each project receives the attention and methodology it truly deserves.