- The Basics of Heat Transfer
- SolidWorks FEA Overview
- Setting Up a Heat Transfer Analysis in SolidWorks
- Conducting Conduction Simulations
- Convection Simulations with SolidWorks FEA
- Radiative Heat Transfer Analysis
- Common Challenges and Troubleshooting
- Case Studies: Real-world Applications
- Conclusion:
Understanding the fundamentals of heat transfer is a cornerstone in the realm of engineering, influencing a myriad of applications. Whether it's optimizing the thermal performance of electronic devices, designing efficient HVAC systems, or ensuring the structural integrity of industrial machinery, a profound comprehension of heat transfer is indispensable. In this context, SolidWorks Finite Element Analysis stands out as a formidable ally, wielding its capabilities to address the intricate and multifaceted challenges posed by heat transfer phenomena. Leveraging SolidWorks FEA can provide invaluable insights and solutions to complex heat transfer problems, enhancing your ability to tackle real-world engineering challenges effectively.
In engineering, the dynamics of heat transfer play a pivotal role in shaping the performance and reliability of diverse systems. Heat transfer can manifest in three primary modes: conduction, convection, and radiation. Conduction involves the transfer of heat through a material without any apparent movement of the material itself. On the other hand, convection deals with the transfer of heat through the motion of fluids, such as liquids or gases. Finally, radiation involves the emission of electromagnetic waves, facilitating heat transfer across space. Each of these modes contributes uniquely to the overall thermal behavior of a system, and an adept understanding of their interplay is essential for engineers seeking to optimize designs and troubleshoot thermal issues.
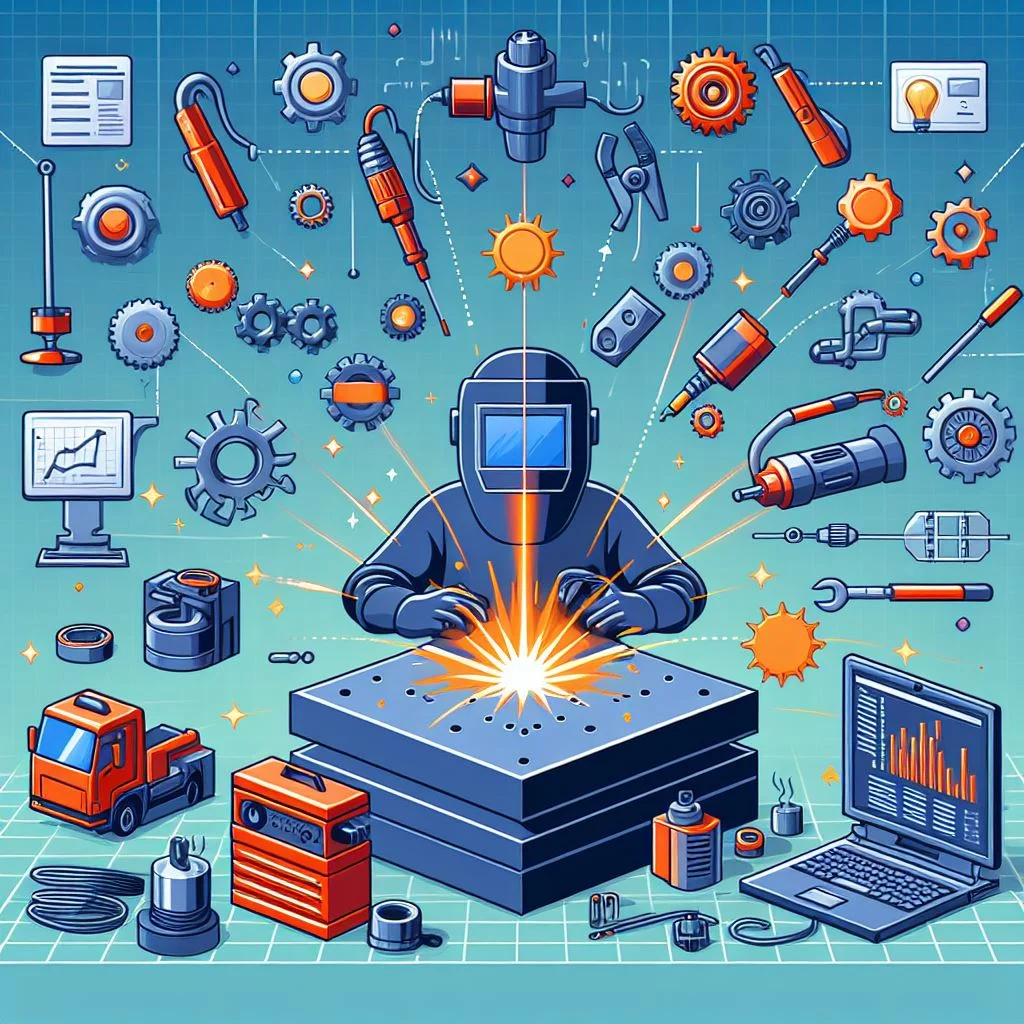
SolidWorks FEA, with its sophisticated simulation capabilities, becomes a linchpin in unraveling the complexities embedded in heat transfer problems. The tool empowers engineers to create accurate virtual prototypes of their designs, enabling them to explore and analyze the thermal behavior of systems under varying conditions. This capability is particularly invaluable in scenarios where real-world testing may be impractical or cost-prohibitive.
One of the key advantages of SolidWorks FEA is its ability to provide a comprehensive overview of thermal performance, allowing engineers to identify potential hotspots, assess temperature distributions, and optimize designs for enhanced efficiency. The accuracy of SolidWorks FEA simulations ensures that the results closely mirror the real-world behavior of the systems under consideration, instilling confidence in the decision-making process.
As engineering projects become increasingly complex and multifaceted, the demand for reliable simulation tools like SolidWorks FEA continues to rise. The tool's prowess extends beyond basic heat transfer simulations, encompassing a spectrum of analyses such as structural, fluid, and electromagnetic simulations. This integration of capabilities makes SolidWorks FEA a versatile and comprehensive solution for engineers facing intricate challenges across various domains.
In the intricate dance of thermal dynamics, SolidWorks FEA emerges as the choreographer, guiding engineers through the complexities of heat transfer with precision and efficacy. The tool's user-friendly interface, coupled with its robust computational algorithms, ensures that even novice users can harness its power to gain insights into thermal behavior and make informed design decisions.
SolidWorks FEA is not merely a software solution; it's a transformative tool that reshapes the landscape of engineering design and analysis. Its impact extends beyond the digital realm, influencing the physical manifestation of innovations that propel industries forward. As we navigate the intricate pathways of heat transfer in the world of engineering, SolidWorks FEA stands as a beacon, illuminating the way towards optimized designs, enhanced performance, and innovative solutions.
In conclusion, the intricate tapestry of heat transfer in engineering finds its unraveling through the powerful capabilities of SolidWorks FEA. This tool, with its ability to simulate and analyze heat transfer scenarios accurately, becomes an indispensable asset for engineers navigating the complexities of thermal dynamics. From the foundational understanding of heat transfer modes to the practical application of SolidWorks FEA in diverse engineering scenarios, the journey is one of continuous learning and innovation, ultimately shaping a future where efficiency and precision go hand in hand.
The Basics of Heat Transfer
Heat transfer, the cornerstone of thermal analysis, is a fascinating interplay that governs the movement of heat energy within and between systems. In the realm of engineering, understanding the intricacies of heat transfer is paramount for designing efficient and reliable systems. There are three primary modes through which heat is transferred – conduction, convection, and radiation.
Conduction is the mode where heat travels through a solid material, primarily driven by molecular vibrations. The efficiency of conduction depends on the material's thermal conductivity, providing a foundational understanding for engineers to optimize material choices.
Convection, on the other hand, involves the transfer of heat through fluids (liquids or gases) and is influenced by fluid properties and flow conditions. The dynamics of convection play a crucial role in various applications, from cooling systems in electronics to industrial heat exchangers.
Radiation, the third mode, introduces electromagnetic waves as carriers of heat energy. Unlike conduction and convection, radiation does not require a material medium, making it applicable in scenarios where direct contact is impractical.
Understanding the distinct contributions of conduction, convection, and radiation to the overall thermal behavior of a system is fundamental. Engineers must navigate the delicate balance between these modes to achieve optimal thermal performance in diverse engineering applications. Whether designing electronic components, optimizing HVAC systems, or developing cutting-edge industrial processes, a profound grasp of heat transfer fundamentals lays the groundwork for successful thermal analysis and system design.
SolidWorks FEA Overview
SolidWorks Finite Element Analysis (FEA) stands as a pinnacle in the realm of engineering simulation, empowering professionals to navigate the intricate landscapes of heat transfer scenarios with unparalleled precision. The versatility of SolidWorks FEA extends beyond mere simulations; it serves as a virtual testing ground where engineers can meticulously analyze the thermal behavior of their designs before bringing them into the physical realm.
With SolidWorks FEA, engineers can delve into the core of heat transfer complexities, gaining insights into temperature distributions, thermal gradients, and material responses under varying conditions. This comprehensive overview allows for the identification of potential issues, ensuring a robust design that meets performance criteria and regulatory standards.
The real power of SolidWorks FEA lies in its ability to accurately model and predict how heat is transferred within a system, whether through conduction, convection, or radiation. Engineers can simulate a myriad of scenarios, from intricate electronic components to large-scale industrial machinery, replicating the dynamic nature of heat exchange in diverse environments. This capability not only enhances the design process but also minimizes the need for costly physical prototypes, ultimately saving time and resources.
SolidWorks FEA stands as a reliable ally for engineers seeking to optimize thermal performance, offering a sophisticated platform that transforms complex heat transfer problems into manageable, insightful simulations. Through this comprehensive overview, engineers can harness the full potential of SolidWorks FEA, propelling their designs towards success in the ever-evolving landscape of engineering challenges.
Setting Up a Heat Transfer Analysis in SolidWorks
Setting up a heat transfer analysis in SolidWorks involves a meticulous process that sets the stage for accurate simulations. The initial step is defining the material properties, a critical factor influencing heat transfer behavior. SolidWorks FEA allows users to select materials from an extensive database or define custom properties, ensuring a precise representation of real-world scenarios. This step is pivotal in capturing the thermal conductivity, specific heat, and density of the materials involved.
Once materials are established, the focus shifts to defining boundary conditions. This step involves specifying the external constraints and thermal interactions that the system experiences. Engineers must identify and apply heat sources, environmental conditions, and any other factors influencing the thermal behavior of the model. SolidWorks FEA simplifies this process with intuitive interfaces, allowing users to set up and modify boundary conditions seamlessly.
Mesh generation follows material and boundary definition, where the geometry is discretized into finite elements. Mesh quality significantly impacts the accuracy of simulations; therefore, engineers must strike a balance between computational efficiency and result precision. SolidWorks provides robust meshing tools, automating the process and offering options for refinement based on user-defined criteria.
Post-meshing, engineers proceed to solver setup, configuring the analysis settings and solver parameters. SolidWorks FEA offers a range of solver options, allowing users to tailor settings to the specific requirements of the heat transfer analysis. Convergence criteria, time steps, and solution controls are adjusted to ensure reliable and efficient simulations.
The final step involves result interpretation and visualization. SolidWorks FEA provides comprehensive post-processing tools, enabling engineers to analyze temperature distributions, heat fluxes, and other critical parameters. Visualization aids in identifying hotspots, understanding thermal gradients, and validating the effectiveness of the heat transfer analysis.
Mastering the essentials of setting up a heat transfer analysis in SolidWorks is foundational for obtaining reliable and insightful simulation results. Engineers equipped with this proficiency can confidently address diverse heat transfer challenges in their designs, ensuring optimal performance and efficiency.
Conducting Conduction Simulations
In the realm of heat conduction simulations with SolidWorks, engineers delve into a world where thermal intricacies are meticulously unraveled. The process involves a comprehensive understanding of how to model and analyze heat flow through solids, a critical facet in diverse engineering applications.
SolidWorks facilitates a seamless experience in creating intricate 3D models that encapsulate the geometry of the solids under consideration. As these models evolve, SolidWorks FEA steps in to simulate the transfer of heat within the structures. Engineers gain insights into temperature distributions, a key parameter influencing the overall thermal behavior of the system.
Crucial to this simulation is the exploration of thermal conductivity, a material property dictating how efficiently heat transfers through a given substance. SolidWorks FEA allows for the incorporation of real-world material properties, ensuring the accuracy and reliability of the simulations. Engineers can assess how different materials influence heat conduction, enabling them to make informed decisions in material selection for optimal thermal performance.
The simulations extend beyond mere analysis, providing a dynamic platform to visualize temperature gradients, identify potential hotspots, and refine designs for enhanced heat dissipation. SolidWorks FEA, with its intuitive interface and robust capabilities, empowers engineers to navigate the intricacies of heat conduction, ensuring that their designs stand up to the rigorous demands of real-world thermal scenarios.
Convection Simulations with SolidWorks FEA
Convection simulations with SolidWorks FEA open a gateway to understanding the dynamic interplay between heat transfer and fluid flow. Engineers can meticulously model and analyze the complexities inherent in systems where heat is exchanged through fluid mediums. SolidWorks FEA empowers users to explore the intricate details of convection, allowing for a comprehensive grasp of how different flow conditions influence thermal behavior.
One notable feature of SolidWorks FEA in convection simulations is its ability to simulate natural and forced convection scenarios. Engineers can simulate heat transfer in scenarios ranging from the natural cooling of a heated surface to the forced circulation of fluid through a system. This versatility is invaluable in designing and optimizing systems where fluid flow plays a crucial role in managing temperature.
Moreover, SolidWorks FEA provides insights into the impact of fluid properties on convection heat transfer. Engineers can analyze the influence of viscosity, density, and thermal conductivity of fluids on the overall thermal performance of a system. This level of detail allows for precise adjustments in designs to enhance efficiency and mitigate potential issues related to convection.
Additionally, SolidWorks FEA facilitates the exploration of turbulence effects in convection. Understanding the behavior of turbulent flows is essential in scenarios where heat transfer rates are significantly affected by fluid dynamics. Engineers can simulate and analyze turbulence, optimizing designs to ensure stability and reliability in real-world applications.
In summary, SolidWorks FEA not only enables engineers to simulate convection but also empowers them to delve deep into the nuanced aspects of fluid dynamics. This capability is indispensable in designing systems where efficient heat transfer through fluid mediums is paramount for optimal performance and reliability.
Radiative Heat Transfer Analysis
Radiative heat transfer, a fundamental aspect of thermal analysis, encompasses the transfer of heat through electromagnetic waves. SolidWorks FEA empowers engineers to delve into the intricate world of radiative heat transfer, allowing for a comprehensive simulation of electromagnetic radiation within complex engineering systems.
In the context of thermal analysis, understanding the nuances of thermal radiation is paramount. SolidWorks FEA provides a sophisticated platform for engineers to explore how electromagnetic waves transport thermal energy, contributing significantly to the overall heat transfer dynamics in various applications.
One crucial aspect of radiative heat transfer is the consideration of emissivity, absorptivity, and reflectivity of materials. SolidWorks FEA facilitates the incorporation of these material properties into simulations, enabling a realistic representation of how different surfaces interact with and influence thermal radiation.
Moreover, engineers can utilize SolidWorks FEA to study the impact of surface orientations, shape factors, and environmental conditions on radiative heat transfer. The software's capabilities extend to analyzing complex geometries and intricate structures, allowing for a detailed examination of radiation patterns and heat distribution in scenarios ranging from electronic devices to industrial settings.
By leveraging SolidWorks FEA for radiative heat transfer analysis, engineers gain insights into optimizing designs for enhanced thermal performance, ensuring the efficiency and reliability of diverse engineering systems. The ability to simulate electromagnetic radiation within SolidWorks FEA enhances its utility as a comprehensive tool for tackling the multifaceted challenges associated with heat transfer in the modern engineering landscape.
Common Challenges and Troubleshooting
In the realm of heat transfer simulations, engineers often confront a myriad of challenges that can impede the accuracy of results. One common stumbling block is the intricacies of mesh refinement. Achieving an optimal mesh is crucial for capturing the nuances of temperature distribution accurately. Inadequate mesh refinement may lead to inaccurate predictions and compromise the reliability of the entire simulation. SolidWorks FEA offers advanced meshing tools, allowing engineers to strike a delicate balance between computational efficiency and result accuracy.
Another hurdle engineers may encounter is the challenge of achieving convergence. Convergence ensures that the simulation reaches a stable solution, but it can be elusive in complex heat transfer scenarios. SolidWorks FEA provides robust convergence diagnostics, enabling engineers to identify and rectify issues promptly. Adjusting solver settings, refining mesh elements, or revisiting boundary conditions are common strategies employed to enhance convergence.
Additionally, the proper consideration of material properties poses a potential challenge. Inaccurate or incomplete material data can significantly impact simulation outcomes. SolidWorks FEA facilitates the incorporation of detailed material properties, aiding engineers in achieving simulations that closely mirror real-world conditions.
Furthermore, boundary conditions play a pivotal role in the accuracy of heat transfer simulations. Incorrectly specified boundary conditions can lead to unrealistic results, making it essential for engineers to meticulously define and validate these parameters. SolidWorks FEA streamlines this process, offering intuitive tools for precise boundary condition setup.
In overcoming these challenges, engineers armed with SolidWorks FEA can navigate the complexities of heat transfer simulations with confidence. By leveraging the platform's sophisticated features and troubleshooting strategies, they can ensure the reliability and accuracy of their thermal analyses, ultimately contributing to the success of their engineering endeavors.
Case Studies: Real-world Applications
Delve into a myriad of real-world scenarios where SolidWorks FEA has played a pivotal role in overcoming heat transfer challenges. In the realm of electronic devices, engineers grapple with the delicate balance between optimal performance and temperature management. SolidWorks FEA has proven instrumental in designing efficient heat dissipation systems for electronic components, ensuring reliability and longevity.
Moving into the domain of industrial machinery, the need for robust thermal analysis becomes even more critical. Large-scale systems, such as power plants or manufacturing equipment, require meticulous attention to heat transfer dynamics. SolidWorks FEA enables engineers to model and simulate heat distribution within these colossal structures, identifying potential hotspots and optimizing cooling mechanisms.
In the automotive sector, where efficiency and safety are paramount, SolidWorks FEA has been employed to enhance the thermal performance of engines and braking systems. Accurate simulations enable engineers to fine-tune designs, mitigating overheating risks and ensuring optimal functionality under varying conditions.
The impact of SolidWorks FEA extends beyond traditional engineering sectors. In the design of energy-efficient buildings, architects leverage thermal simulations to optimize insulation and HVAC systems, reducing energy consumption and creating environmentally sustainable structures.
These case studies underscore the versatility of SolidWorks FEA in addressing heat transfer challenges across diverse industries, reaffirming its position as a cornerstone tool for engineers navigating the complexities of thermal analysis in real-world applications.
Conclusion:
In conclusion, SolidWorks FEA stands as a formidable ally for engineers grappling with the complexities of heat transfer. Through our exploration of the various facets of this powerful tool, it is evident that SolidWorks FEA not only provides accurate simulations but also empowers engineers to efficiently address heat transfer problems.
One of the key takeaways is the versatility offered by SolidWorks FEA in modeling different modes of heat transfer. Whether it's conduction through solids, convection in fluids, or radiative heat transfer, the software accommodates diverse scenarios, allowing engineers to gain a comprehensive understanding of thermal behavior. This versatility is crucial for industries where a variety of materials and operating conditions are encountered.
Furthermore, the ability to set up a heat transfer analysis with SolidWorks FEA is a straightforward process. Engineers can define materials, apply boundary conditions, and fine-tune parameters, enabling them to tailor simulations to specific real-world conditions accurately. This ease of use contributes to a more efficient workflow, allowing engineers to focus on interpreting results rather than wrestling with the complexities of the simulation setup.
SolidWorks FEA not only excels in individual simulations but also shines in its capability to troubleshoot common challenges. The software provides tools for mesh refinement, convergence diagnostics, and other features that enable engineers to identify and address issues swiftly. This ensures that simulations are not only accurate but also reliable, instilling confidence in the results obtained.
Perhaps one of the most significant advantages of SolidWorks FEA lies in its practical application to real-world problems. Through case studies presented in Section 8, we witnessed the software's impact on optimizing designs in various industries, from electronic devices to industrial machinery. Engineers can leverage SolidWorks FEA to fine-tune their designs, improving efficiency, and ensuring that the final product meets performance expectations.
The importance of simulation in the design process cannot be overstated, and SolidWorks FEA plays a pivotal role in this regard. By allowing engineers to virtually test and analyze heat transfer scenarios, the software contributes to the reduction of time-to-market. Iterative physical prototyping can be time-consuming and expensive, but with SolidWorks FEA, engineers can iterate more rapidly in the virtual space, accelerating the overall product development timeline.
In essence, SolidWorks FEA is not just a tool; it's a catalyst for innovation and efficiency in the realm of heat transfer analysis. As we navigate the ever-evolving landscape of engineering challenges, having a reliable and robust simulation tool like SolidWorks FEA is paramount. It empowers engineers to push the boundaries of what's possible, enabling them to design and optimize systems with a level of precision that was once unimaginable.
In a world where technology is advancing at an unprecedented pace, SolidWorks FEA stands as a beacon for engineers seeking to navigate the intricate domain of heat transfer. Its impact extends beyond the virtual realm, influencing the physical manifestation of designs that shape our technological landscape. As we continue to push the boundaries of what can be achieved in engineering, SolidWorks FEA remains an indispensable tool, a companion for those who strive for excellence in every thermal analysis.