- Understanding Weldments in SolidWorks:
- Case Study 1: Optimizing Welding Processes for Structural Integrity:
- Case Study 2: Designing Efficient Welded Joints for Industrial Machinery:
- Case Study 3: Overcoming Weld Distortions with SolidWorks Simulation:
- Advanced Techniques in Weldment Simulation:
- Best Practices for Weldment Design in SolidWorks:
- Conclusion:
SolidWorks stands as a cornerstone in the realm of engineering, reshaping the traditional approach to tackling welding challenges encountered in real-world scenarios. It serves as an indispensable tool that empowers engineers to navigate through intricate weldment issues with finesse and precision. In this blog, we embark on a journey through practical case studies, offering a firsthand look at how SolidWorks seamlessly addresses the multifaceted challenges posed by complex weldment problems. If you need assistance with your weldment assignment, delving into SolidWorks' capabilities can provide valuable insights and strategies to overcome these challenges effectively.
The significance of SolidWorks in the field of engineering cannot be overstated. Its robust features and user-friendly interface make it an ideal companion for professionals seeking innovative solutions to intricate problems associated with weldments. The ability to visualize, design, and simulate welding processes in a virtual environment has redefined the paradigm of weldment design and analysis.
As we venture into the realm of case studies, it becomes evident that SolidWorks is not merely a software tool but a catalyst for innovation in the welding industry. The first case study unfolds a scenario where SolidWorks played a pivotal role in optimizing welding processes to enhance structural integrity. Through accurate simulations, potential failures were identified and rectified, ensuring a robust and reliable end product. This exemplifies how SolidWorks empowers engineers to foresee challenges before they manifest in the physical realm.
Moving forward, the second case study delves into the intricacies of designing efficient welded joints for industrial machinery. Welded joints in such applications are subjected to rigorous stress and operational demands. SolidWorks provides a comprehensive platform to meticulously design joints, ensuring they meet the highest standards of performance and durability. The step-by-step guide presented in this case study serves as a valuable resource for engineers grappling with the complexities of industrial machinery design.
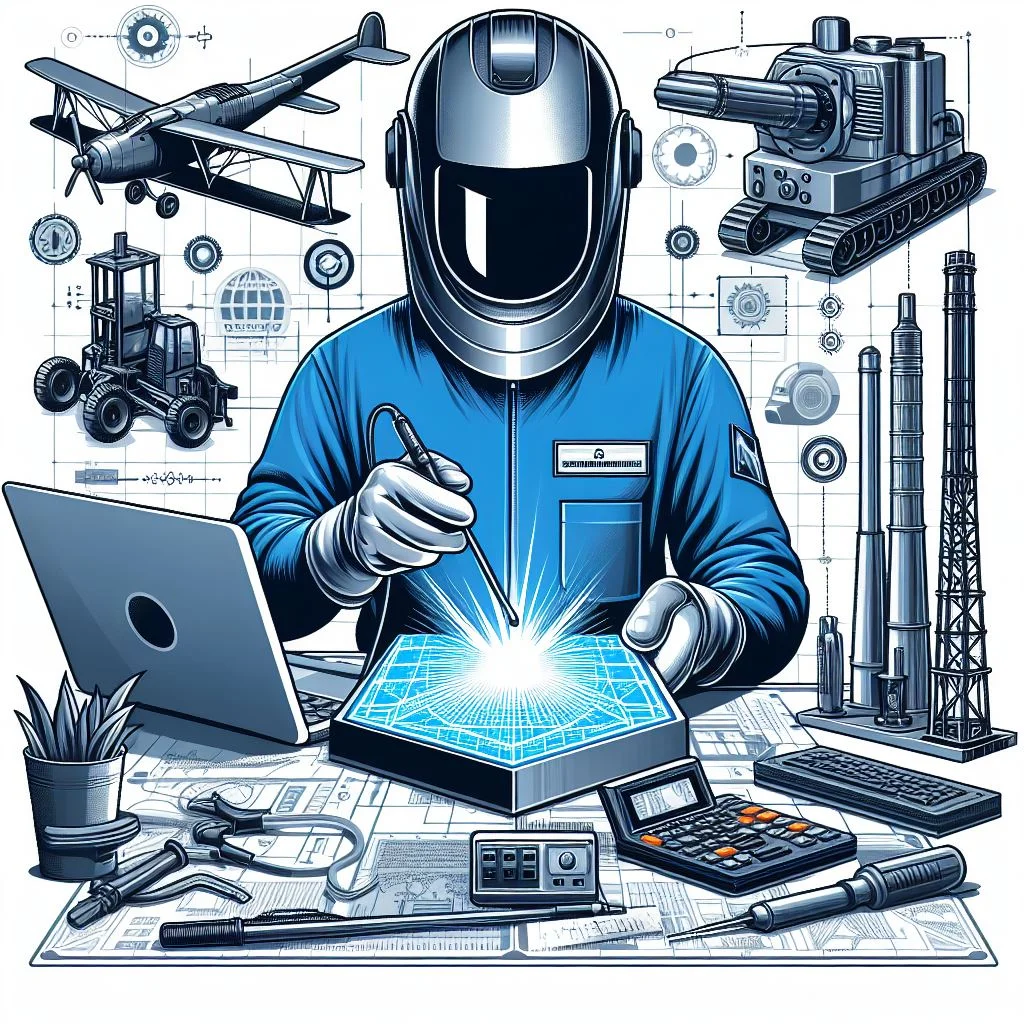
One of the persistent challenges in welding is the occurrence of distortions during the fabrication process. The third case study sheds light on how SolidWorks Simulation emerges as a savior in overcoming weld distortions. By accurately predicting and mitigating distortions, engineers can save valuable time and resources while ensuring the final product meets the desired specifications. This case study unravels the depth of SolidWorks capabilities in addressing not just design challenges but also inherent manufacturing complexities.
As we navigate through these practical case studies, it becomes apparent that SolidWorks is not confined to basic simulations. It goes beyond, offering advanced techniques in weldment simulation. Thermal analysis, fatigue simulation, and non-linear studies are among the sophisticated tools that SolidWorks puts at the disposal of engineers. These advanced techniques elevate the precision of simulations, allowing engineers to simulate real-world conditions with unparalleled accuracy.
Understanding Weldments in SolidWorks:
Understanding Weldments in SolidWorks is foundational to unlocking the software's potential for solving real-world welding challenges. SolidWorks offers a comprehensive suite of tools and features specifically tailored for designing and simulating welded structures.
At its core, a weldment in SolidWorks is a multi-body part composed of structural members such as beams, tubes, and plates. This functionality is particularly advantageous for projects involving frameworks, support structures, or any application where welded components play a vital role. SolidWorks simplifies the creation of weldments by providing an extensive library of standard structural profiles that users can easily customize and incorporate into their designs.
The software's intuitive interface allows engineers to sketch the desired framework, add structural members, and instantly create a 3D representation of the weldment. This streamlined process accelerates the design phase, providing engineers with a visual prototype that aids in refining the structure before moving to the simulation stage.
SolidWorks excels in simulation, enabling users to assess the weldment's performance under various conditions. The software incorporates finite element analysis (FEA) tools to evaluate factors such as stress, strain, and deformation. Engineers can simulate real-world scenarios, ensuring that the weldment meets safety and performance standards. This pre-simulation phase is instrumental in identifying potential issues early in the design process, minimizing the need for costly revisions during fabrication.
Moreover, SolidWorks offers parametric design capabilities, allowing for quick adjustments to the weldment's dimensions and configurations. This parametric flexibility proves invaluable when responding to design changes or optimizing the structure for enhanced performance.
Case Study 1: Optimizing Welding Processes for Structural Integrity:
In a recent real-life scenario, SolidWorks emerged as a game-changer by playing a pivotal role in optimizing welding processes to enhance structural integrity. The challenge at hand involved the fabrication of a complex steel structure for a high-rise building. The traditional approach to welding processes was proving time-consuming and posed a significant risk to the structural integrity of the building.
SolidWorks came to the rescue with its powerful simulation capabilities. Engineers used the software to create a virtual model of the entire structure, allowing them to simulate various welding scenarios. The software's accurate simulations provided valuable insights into potential weak points and stress concentrations in the welds, enabling engineers to make informed decisions in the design phase.
One critical aspect addressed was the choice of welding techniques. SolidWorks allowed engineers to compare the effects of different welding methods, such as MIG and TIG welding, on the overall structural integrity. By running simulations for each technique, they were able to identify the optimal welding process that not only met the project's timeline but also ensured the longevity and safety of the structure.
Furthermore, SolidWorks simulation capabilities went beyond the basic structural analysis. It allowed engineers to consider external factors such as environmental conditions and load variations, providing a comprehensive understanding of how the building would perform under different circumstances. This holistic approach proved invaluable in preventing potential failures that might have been overlooked using conventional methods.
In the end, SolidWorks not only optimized the welding processes for efficiency but also significantly contributed to the structural integrity of the building. The accurate simulations provided by the software ensured that the final design not only met industry standards but exceeded them, setting a new benchmark for excellence in weldment processes. This case study exemplifies how SolidWorks can be a transformative tool in addressing real-life welding challenges, ensuring the success of complex projects.
Case Study 2: Designing Efficient Welded Joints for Industrial Machinery:
In the realm of industrial machinery, the design of welded joints holds paramount importance. Engineers often grapple with challenges ranging from structural stability to material compatibility when tasked with creating welded joints for heavy-duty machinery. In this case study, we will explore the intricacies of designing welded joints for industrial machinery and unveil a step-by-step guide on how SolidWorks can be leveraged to craft robust joints that ensure both longevity and optimal performance.
One of the primary challenges faced in designing welded joints for industrial machinery is the need for a delicate balance between strength and flexibility. Machinery operates in dynamic environments, subjecting welded joints to various stresses and forces. Engineers must navigate through complex considerations, such as the choice of welding technique, material selection, and joint geometry, to ensure that the final design can withstand the demanding conditions encountered in industrial settings.
SolidWorks proves to be an invaluable tool in addressing these challenges. The software's intuitive interface and powerful features enable engineers to create detailed 3D models of welded joints, allowing for a comprehensive analysis of the joint's behavior under different conditions. Through SolidWorks Simulation, engineers can virtually test the joints for structural integrity, identifying potential weak points and optimizing the design before any physical prototypes are produced.
The step-by-step guide involves defining the joint specifications within SolidWorks, including weld type, dimensions, and material properties. SolidWorks then facilitates the creation of an accurate 3D model, considering factors like fillet size, groove design, and weld preparation. Through simulation, engineers can assess the joint's performance, making necessary adjustments to enhance its strength and durability.
By seamlessly integrating design and simulation capabilities, SolidWorks empowers engineers to iterate rapidly, refining welded joint designs until they meet the stringent requirements of industrial machinery. This holistic approach not only accelerates the design process but also ensures that the final product excels in terms of both reliability and performance in real-world applications.
Case Study 3: Overcoming Weld Distortions with SolidWorks Simulation:
Weld distortions can pose significant challenges during the fabrication process, impacting the overall quality and precision of the final product. In a real-life scenario, a manufacturing company faced intricate distortions in their welded components, leading to increased production time and material wastage. SolidWorks Simulation emerged as the beacon of solution, offering a sophisticated platform to predict and mitigate these distortions effectively.
The initial phase involved importing the 3D model of the welded structure into SolidWorks Simulation. The software's intuitive interface allowed for the application of realistic loads, material properties, and welding sequences, creating a virtual environment that closely mirrored the actual fabrication process. The simulation accurately predicted the areas prone to distortion, providing invaluable insights for preemptive measures.
SolidWorks Simulation's thermal analysis capabilities played a crucial role in understanding the heat distribution during the welding process. By simulating the welding sequences and analyzing the temperature gradients, engineers gained a comprehensive understanding of how thermal expansion contributed to distortions. This insight enabled the team to fine-tune the welding parameters, adjusting heat input and sequencing to minimize distortions while maintaining structural integrity.
As the simulation progressed, real-time visualizations showcased the evolving deformations in the virtual model. This dynamic representation allowed engineers to make on-the-fly adjustments, optimizing the welding process for reduced distortions. The iterative nature of SolidWorks Simulation ensured a refined approach, saving both time and resources that would have otherwise been spent on trial-and-error methods in the physical realm.
The successful implementation of SolidWorks Simulation not only alleviated the distortions in the welded components but also contributed to a streamlined fabrication workflow. The case study exemplifies how leveraging advanced simulation tools can significantly enhance the efficiency of weldment processes, underlining SolidWorks' prowess in tackling real-world challenges in fabrication.
Advanced Techniques in Weldment Simulation:
Delving deeper into the capabilities of SolidWorks, we uncover advanced simulation techniques that prove instrumental in addressing intricate weldment challenges. One such technique involves thermal analysis, which allows engineers to assess the impact of heat on welded structures. By simulating the thermal effects during welding processes, designers gain valuable insights into potential distortions and weaknesses in the welds, enabling preemptive adjustments for enhanced structural integrity.
Fatigue simulation is another critical aspect of advanced weldment analysis in SolidWorks. Engineers can predict how repeated loading and unloading cycles may affect the welds over time. This proactive approach aids in designing weldments that withstand prolonged usage without succumbing to fatigue-induced failures. The ability to simulate and analyze fatigue is invaluable, especially in industries where equipment is subjected to continuous and rigorous operational conditions.
Non-linear studies further expand SolidWorks' capabilities in weldment simulation. Real-world scenarios often involve complex behaviors that traditional linear analyses may not capture accurately. Non-linear studies enable engineers to simulate material yielding, large deformations, and contact interactions, providing a more realistic representation of how weldments behave under various conditions. This sophisticated analysis allows for a comprehensive understanding of potential failure points, guiding designers in refining their weldment designs.
Incorporating these advanced simulation techniques into the weldment design process not only ensures the structural soundness of the final product but also contributes to significant time and cost savings. By identifying and rectifying potential issues during the virtual design phase, engineers can mitigate the risks associated with physical prototyping and testing, streamlining the overall product development cycle.
Best Practices for Weldment Design in SolidWorks:
In the realm of weldment design using SolidWorks, adhering to best practices is paramount to ensure the creation of robust and efficient structures. One crucial aspect is material selection. SolidWorks provides a comprehensive database of materials, enabling designers to choose the most suitable ones for specific applications. From metals with high tensile strength to alloys tailored for specific environments, the software's material selection tools empower engineers to make informed decisions that directly impact the performance and longevity of welded structures.
Equally significant is the joint design, where SolidWorks excels in offering versatile options. Engineers can experiment with various joint configurations, such as fillet welds, groove welds, and corner welds, to achieve optimal strength and stability. The software's intuitive interface allows for seamless exploration and modification of joint designs, facilitating the creation of weldments tailored to specific project requirements.
Efficient use of features is another cornerstone of best practices in SolidWorks weldment design. The software offers an array of features dedicated to weldments, such as structural members, weld beads, and end caps. Understanding how to leverage these features effectively can significantly enhance manufacturability. SolidWorks' parametric design capabilities enable engineers to make quick and precise adjustments, ensuring that the final weldment meets both design specifications and manufacturing constraints.
Moreover, the software's assembly features enable the simulation of the entire welding process, allowing designers to visualize and analyze how individual components come together. This holistic approach aids in identifying potential clashes, interferences, or stress concentrations, contributing to a more accurate and reliable weldment design.
In essence, mastering the best practices in SolidWorks weldment design involves a nuanced understanding of material properties, judicious joint design, and skillful utilization of the software's features. By integrating these practices into the design workflow, engineers can elevate the quality and efficiency of their weldment projects, ultimately delivering solutions that stand the test of real-world applications.
Conclusion:
In conclusion, the case studies presented here highlight the profound impact of SolidWorks in addressing real-life weldment challenges. Through these practical applications, several key takeaways emerge, underscoring the software's significance in the field of welding and structural design.
Firstly, SolidWorks has proven instrumental in optimizing welding processes for enhanced structural integrity. The ability to simulate and analyze various welding techniques ensures that engineers can identify the most efficient methods, reducing the risk of structural failures and improving the overall reliability of welded structures.
Secondly, the case studies illustrate how SolidWorks aids in designing efficient welded joints, particularly in the context of industrial machinery. The step-by-step guide provided demonstrates how the software facilitates the creation of robust joints, contributing to the longevity and optimal performance of machinery. This aspect is crucial in industries where machinery is subjected to rigorous operational demands.
Moreover, SolidWorks demonstrates its utility in overcoming weld distortions, a common challenge in the fabrication process. The software's simulation capabilities allow engineers to predict and address distortions before the actual fabrication process begins. This not only saves valuable time but also ensures cost-effectiveness by minimizing material wastage due to rework.
The exploration of advanced simulation techniques in weldment design using SolidWorks further reinforces its role as an indispensable tool. Thermal analysis, fatigue simulation, and non-linear studies empower engineers to delve into intricate aspects of weldment design, enabling a more comprehensive understanding of how structures will behave under different conditions.
As we reflect on these case studies collectively, the importance of SolidWorks in the realm of weldment design becomes evident. The software is not merely a drafting tool but a comprehensive solution that integrates simulation, analysis, and optimization into the design process. This integration streamlines workflows, enhances accuracy, and ultimately contributes to the delivery of robust and reliable welded structures.
In practice, the best practices outlined for weldment design in SolidWorks serve as a guide for engineers seeking to leverage the software's full potential. Material selection, joint design considerations, and the efficient use of features are pivotal aspects that, when implemented judiciously, result in designs that are not only structurally sound but also conducive to efficient and cost-effective manufacturing.
In essence, SolidWorks emerges as a cornerstone in the toolkit of professionals dealing with weldment challenges. Its versatility, coupled with advanced simulation capabilities, empowers engineers to tackle complex issues with confidence and precision. The software's user-friendly interface and powerful features make it accessible to both seasoned professionals and those new to the field, democratizing the process of efficient weldment design.
In a landscape where structural integrity, efficiency, and cost-effectiveness are paramount, SolidWorks stands as a reliable ally for engineers grappling with real-life weldment problems. As technology continues to advance, SolidWorks is poised to evolve and meet the ever-changing demands of the industry, solidifying its position as a go-to solution for tackling the challenges of weldment design in the modern era.