- Introduction: Unveiling the Essence of FEA in SolidWorks
- Distinguishing Factors: Parameters and Considerations
- Applications of Static Analysis: When Stability is Paramount
- Applications of Dynamic Analysis: Capturing Real-World Dynamics
- Challenges and Limitations: Navigating the Complexities of Analysis
- Choosing the Right Tool for the Job: Practical Considerations
- Case Studies: Real-World Applications and Success Stories
- Conclusion:
In the realm of Finite Element Analysis (FEA) within SolidWorks, the choice between static and dynamic analysis plays a pivotal role in ensuring the accuracy and reliability of simulation results. Each method offers unique insights into the behavior of structures and components under different conditions. In this comprehensive guide, we will delve into the intricacies of static and dynamic analysis, exploring their applications, differences, and the considerations that engineers must take into account. I'm here to provide guidance and support to help you navigate through the complexities of FEA simulation and analysis.
SolidWorks, a widely used computer-aided design (CAD) and computer-aided engineering (CAE) software, has become a cornerstone in the field of product design and simulation. FEA, a numerical method used to analyze the structural and mechanical behavior of complex systems, has further enhanced the capabilities of SolidWorks. It allows engineers to virtually test and validate designs before moving into the physical prototyping phase, saving both time and resources.
Static analysis, the more traditional of the two methods, focuses on studying structures under constant or slowly varying loads. This method assumes that the applied loads and the resulting stresses induce negligible changes in the geometry or material properties over time. It is particularly useful in scenarios where the structure's response can be adequately captured without considering the element of time.
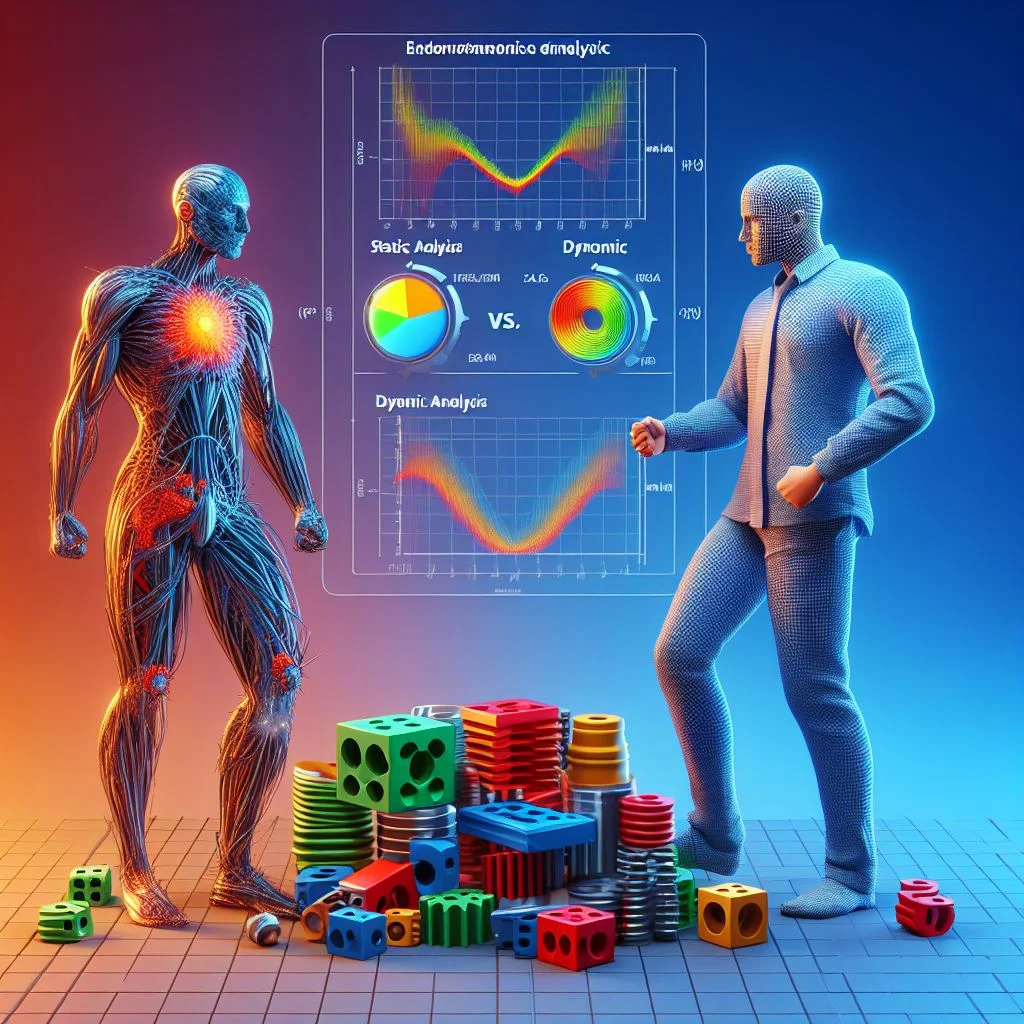
On the other hand, dynamic analysis introduces the time factor into simulations, allowing engineers to study how structures respond to varying loads and dynamic forces over time. This method is essential in scenarios involving moving parts, vibrations, and transient events, where understanding the dynamic behavior is crucial for designing robust and reliable products.
Static and dynamic analyses serve as indispensable tools in the engineer's toolbox, each offering distinct advantages based on the nature of the project. Static analysis provides a quick and computationally efficient way to assess the structural stability of a design, making it suitable for applications where the loads are steady and predictable. On the contrary, dynamic analysis is the go-to choice when dealing with structures subjected to dynamic forces, such as those encountered in machinery, automotive components, and aerospace systems.
Considerations for choosing between static and dynamic analysis extend beyond the nature of the loads. Engineers must also factor in the material properties, boundary conditions, and the overall project goals. For example, if the primary concern is understanding how a structure behaves under a constant load without significant variations, static analysis may suffice. However, in situations where predicting the dynamic response of a system is critical, dynamic analysis becomes imperative.
SolidWorks offers a seamless integration of both static and dynamic analysis capabilities, allowing engineers to transition between these methods seamlessly. This flexibility empowers them to choose the most appropriate analysis type for a given scenario, ensuring that the simulation aligns with the real-world conditions the product will face.
In practical terms, static analysis finds its application in a wide range of scenarios. From assessing the stability of buildings and bridges to evaluating the load-bearing capacity of mechanical components, static analysis provides invaluable insights into the overall structural integrity of a design. Its efficiency lies in its ability to simplify complex problems, making it a preferred choice for preliminary design evaluations.
Dynamic analysis, on the other hand, comes into play when dealing with scenarios where time and motion are critical factors. For instance, in the automotive industry, understanding how a vehicle's suspension system responds to various road conditions requires dynamic analysis. Similarly, in aerospace engineering, simulating the vibrations a spacecraft experiences during launch necessitates the consideration of dynamic forces.
As engineers navigate the complexities of choosing between static and dynamic analysis, they must be mindful of the limitations and challenges associated with each method. Static analysis may oversimplify dynamic scenarios, potentially leading to inaccurate results in situations where time-dependent effects are significant. Conversely, dynamic analysis, while more comprehensive, can be computationally intensive, requiring careful consideration of computational resources and analysis time.
In the upcoming sections of this guide, we will delve deeper into the specifics of static and dynamic analyses, exploring their applications, distinguishing factors, and the considerations that guide engineers in making informed decisions. Whether you're designing a robust machine component or ensuring the structural integrity of a building, understanding the nuances of these analysis methods is essential for achieving reliable and accurate simulation results.
Introduction: Unveiling the Essence of FEA in SolidWorks
Finite Element Analysis (FEA) stands as a cornerstone in the realm of engineering simulations within SolidWorks. Its significance lies in its ability to empower engineers with a predictive lens, allowing them to unravel the intricate behaviors of structures and components subjected to diverse loading conditions. The adoption of FEA in SolidWorks has revolutionized the design and validation process, offering a virtual playground for engineers to test and refine their concepts before they materialize into physical prototypes.
FEA, within the SolidWorks environment, serves as a virtual testing ground where the laws of physics seamlessly merge with cutting-edge computational algorithms. Engineers can subject their designs to a multitude of scenarios, exploring how they respond to various forces, pressures, and environmental conditions. This process not only enhances the efficiency of the design phase but also plays a pivotal role in minimizing the risk of structural failures in real-world applications.
In essence, SolidWorks FEA transforms the design landscape by providing a comprehensive understanding of how structures interact with their surroundings. It's not merely a simulation tool; it's a virtual laboratory where engineers can conduct experiments, iterate on designs, and gain insights that transcend the limitations of traditional trial-and-error methods. As we embark on this exploration of static and dynamic analysis, it's crucial to recognize FEA's pivotal role in shaping the future of engineering, where virtual prototyping paves the way for innovation and reliability.
Distinguishing Factors: Parameters and Considerations
Diving deeper into the realm of Finite Element Analysis (FEA) in SolidWorks, understanding the distinguishing factors between static and dynamic analysis becomes imperative for engineers striving for accurate and meaningful simulation results. One of the pivotal considerations is time – static analysis assumes that the applied loads act slowly or remain constant, while dynamic analysis introduces the time variable, acknowledging the transient nature of forces and the resulting structural response over time. This temporal aspect is particularly crucial when dealing with components subjected to rapid or fluctuating loads, such as machinery in motion or structures exposed to dynamic forces.
Another critical factor is the nature of loading conditions. Static analysis is ideal for scenarios where the applied loads induce slow and gradual changes in the structure's behavior. Conversely, dynamic analysis steps in when the forces are dynamic, varying with time and introducing complex interactions. Engineers must carefully evaluate the loading conditions relevant to their projects to choose the analysis method that aligns with the expected real-world behavior.
Material properties constitute another key consideration in distinguishing between static and dynamic analysis. Different materials respond differently to static and dynamic loads, and understanding these material behaviors is paramount in achieving accurate simulations. Static analysis is well-suited for assessing the structural stability of materials under constant loads, whereas dynamic analysis provides insights into how materials react to time-varying forces, capturing their dynamic responses and potential fatigue effects.
In essence, the choice between static and dynamic analysis in SolidWorks FEA hinges on a nuanced understanding of time, loading conditions, and material properties. Engineers navigating this decision-making process with diligence and expertise ensure that their simulations reflect the intricacies of real-world scenarios, laying the foundation for robust and reliable design outcomes.
Applications of Static Analysis: When Stability is Paramount
Static analysis is an indispensable tool in engineering, offering critical insights in scenarios where stability is of utmost importance. One prominent application lies in the assessment of the structural integrity of buildings. Engineers utilize static analysis to predict the behavior of various structural elements, ensuring that the design can withstand static loads such as gravity, wind, and seismic forces. By accurately simulating these conditions, potential weaknesses or areas of concern can be identified and addressed, ultimately contributing to safer and more robust architectural designs.
In the realm of machine design, static analysis plays a pivotal role in evaluating the strength and stability of components. Whether it's a crucial part of an industrial machine or a component within a consumer product, understanding how these elements respond to static loads is paramount. Engineers leverage static analysis to assess factors like material stress, deformation, and overall structural performance. This meticulous examination aids in optimizing designs, preventing unexpected failures, and ensuring that machines operate within safe operational limits.
Moreover, static analysis finds application in civil engineering projects, such as bridges and infrastructure. By simulating static loads imposed by traffic, equipment, or environmental conditions, engineers can assess the stability of structures over time. This meticulous analysis helps in designing structures that not only meet safety standards but also exhibit longevity and durability in the face of varying static forces.
In summary, static analysis stands as a cornerstone in the engineering toolbox, offering profound insights into stability across diverse applications, from architectural marvels to intricate machinery and critical infrastructure. Its ability to predict slow and predictable structural responses makes it an invaluable asset in ensuring the reliability and safety of designs in various engineering disciplines.
Applications of Dynamic Analysis: Capturing Real-World Dynamics
Dynamic analysis plays a pivotal role in an array of real-world scenarios, providing invaluable insights into the behavior of structures and components subjected to dynamic forces. One significant application lies in the automotive industry, where dynamic analysis helps engineers understand the intricate dynamics of vehicle components under various driving conditions. Whether it's assessing the response of suspension systems to road irregularities or evaluating the impact of sudden accelerations or decelerations, dynamic analysis aids in optimizing the design of automotive structures for enhanced performance, safety, and comfort.
Moving beyond the automotive realm, dynamic analysis finds its place in the evaluation of machinery subjected to impact loads. Industries such as manufacturing and construction often deal with equipment that undergoes sudden and forceful impacts. By employing dynamic analysis, engineers can simulate these impact scenarios, predicting the structural response and ensuring that the machinery can withstand such events without compromising safety or functionality.
In the aerospace sector, dynamic analysis becomes crucial in understanding and mitigating vibrations. Aircraft structures are exposed to a range of dynamic forces during flight, including turbulence, engine vibrations, and control surface movements. Dynamic analysis enables engineers to simulate these vibrations, ensuring that aerospace structures are designed to withstand the harsh and dynamic conditions encountered during their operational life. This meticulous analysis contributes to the overall safety and reliability of aerospace components, emphasizing the importance of dynamic analysis in ensuring the structural integrity of critical systems.
Challenges and Limitations: Navigating the Complexities of Analysis
Navigating the complexities of analysis in SolidWorks FEA involves acknowledging the challenges and limitations inherent in both static and dynamic methods. One of the primary challenges lies in accurately modeling real-world conditions. While FEA provides a powerful platform, achieving a precise representation of complex scenarios, such as material nonlinearity or geometric irregularities, remains a formidable task. Engineers must grapple with the trade-off between simulation accuracy and computational efficiency, as refining models for increased precision often results in longer simulation times.
Another critical limitation revolves around the assumption of linear behavior in static analysis. In reality, many structures exhibit nonlinear characteristics under certain conditions, necessitating more advanced analysis techniques. The intricacies of dynamic analysis introduce challenges related to numerical stability and the need for time-stepping methods. The accurate prediction of dynamic responses relies on finely tuned parameters, making the simulation susceptible to errors if not carefully managed.
Moreover, the validity of simulation results hinges on the quality of input data, such as material properties and boundary conditions. Inaccuracies in these inputs can propagate throughout the analysis, leading to unreliable predictions. Engineers must exercise diligence in obtaining and validating these parameters to enhance the overall reliability of their simulations.
In conclusion, while SolidWorks FEA empowers engineers with a robust simulation environment, an awareness of these challenges is essential. Addressing these limitations requires a nuanced approach, emphasizing a balance between accuracy and computational efficiency, meticulous model refinement, and the conscientious handling of input data. This understanding equips engineers with the knowledge needed to make informed decisions, ensuring the reliability of their simulations and the success of their design endeavors.
Choosing the Right Tool for the Job: Practical Considerations
Guiding engineers through the decision-making process is crucial for ensuring the success of any Finite Element Analysis (FEA) project. When it comes to choosing between static and dynamic analysis in SolidWorks, practical considerations play a pivotal role. Time constraints often dictate the feasibility of conducting elaborate dynamic analyses, especially in scenarios where quick results are imperative. In fast-paced industries, such as manufacturing or automotive design, the need for rapid decision-making may favor the implementation of static analysis due to its quicker computational turnaround.
Furthermore, accuracy needs are paramount in determining the appropriate analysis method. If a project demands a precise understanding of how a structure behaves over time, dynamic analysis becomes indispensable. This is particularly relevant in fields like aerospace engineering, where vibrations and dynamic loads are critical factors in ensuring the safety and performance of components.
Project complexity is another determinant in the analysis method selection process. Simpler structures with predictable loading conditions may lean towards static analysis, while complex systems with varying and unpredictable forces may necessitate the comprehensive insights offered by dynamic analysis.
Ultimately, engineers must strike a balance between time, accuracy, and project complexity to make informed decisions. By carefully evaluating these practical considerations, they can optimize the analysis approach, ensuring the reliability and efficiency of the simulation results. In the ever-evolving landscape of engineering, the ability to choose the right tool for the job is a skill that distinguishes successful projects and engineers alike.
Case Studies: Real-World Applications and Success Stories
Illustrating the concepts discussed with real-world case studies is imperative to grasp the practical applications and success stories of static and dynamic analysis in SolidWorks FEA. In one notable instance, a structural engineering project faced the challenge of ensuring the stability of a complex architectural design. Through rigorous static analysis, engineers identified critical stress points and made targeted design modifications, resulting in a structurally sound and aesthetically pleasing building.
On the dynamic analysis front, an automotive manufacturer leveraged SolidWorks FEA to enhance the performance of a suspension system. By subjecting the components to dynamic simulations simulating various driving conditions, engineers optimized the design to withstand diverse road scenarios. This proactive approach not only prevented potential failures but also significantly improved the overall ride quality and safety of the vehicle.
In the aerospace industry, dynamic analysis played a crucial role in assessing the impact resistance of aircraft components. Simulating scenarios involving bird strikes and turbulent air conditions, engineers utilized SolidWorks FEA to refine the structural design, ensuring the integrity of critical components. These case studies underscore the practical significance of static and dynamic analysis in mitigating risks, optimizing designs, and ultimately elevating the performance of diverse engineering projects.
Conclusion:
In conclusion, the integration of both static and dynamic analysis in SolidWorks FEA is not merely a choice between two methodologies but a strategic approach to achieving comprehensive insights into structural behavior. As we reflect on the various aspects covered in this guide, it becomes evident that each analysis method brings a unique set of advantages to the table. By combining static and dynamic analyses, engineers can harness the synergies between them, resulting in more robust and reliable engineering solutions.
One key takeaway is the intrinsic complementarity of static and dynamic analyses. While static analysis provides crucial information about the equilibrium and stability of structures under constant loads, dynamic analysis introduces the temporal element, allowing engineers to study the response of structures to dynamic forces over time. Together, these analyses create a holistic understanding of how a design will perform in both static and dynamic scenarios, ensuring a comprehensive evaluation of structural integrity.
Moreover, the integration of static and dynamic analysis addresses the limitations inherent in each method when used in isolation. Static analysis may overlook transient phenomena, while dynamic analysis might not fully capture the subtle effects of slow, steady loads. By combining these approaches, engineers can overcome these limitations, gaining a more accurate representation of a structure's behavior under a wide range of conditions.
The importance of this integration becomes even more pronounced in industries where safety and reliability are paramount. Aerospace, automotive, and civil engineering projects often involve intricate structures subjected to diverse and dynamic loading conditions. The combined insights from static and dynamic analyses empower engineers to make informed decisions, mitigating potential risks and ensuring that designs meet stringent safety standards.
Furthermore, the synergy between static and dynamic analyses significantly contributes to the optimization of designs. Engineers can identify critical points of failure under static conditions and refine the design accordingly. Simultaneously, dynamic analysis allows for the exploration of scenarios involving vibrations, impacts, and transient loads, guiding adjustments that enhance the overall performance and longevity of the structure.
The practical implications of integrating static and dynamic analyses extend beyond the realm of simulation. This approach facilitates better communication and collaboration among multidisciplinary teams involved in the design and validation process. Mechanical, structural, and aerospace engineers can collaborate more effectively, leveraging their collective expertise to achieve a more holistic understanding of the system under study.
As technology advances, the integration of static and dynamic analyses is becoming more accessible and efficient. SolidWorks FEA software, with its sophisticated simulation capabilities, empowers engineers to seamlessly transition between these analysis methods, streamlining the overall design process. This not only improves productivity but also encourages a more iterative and collaborative approach to engineering design.
In conclusion, the integration of static and dynamic analysis in SolidWorks FEA is a strategic imperative for modern engineering. It enables engineers to overcome the limitations of individual analyses, provides a more comprehensive understanding of structural behavior, and ultimately leads to the development of more reliable, safe, and optimized designs. As the engineering landscape continues to evolve, the synergy between static and dynamic analyses stands as a testament to the commitment to excellence and innovation within the field.