- Introduction to SolidWorks:
- Conceptual Design:
- Detailed Design and Validation:
- Collaboration and Communication:
- Design for Manufacturing (DFM):
- Prototyping and Testing:
- Data Management and Documentation:
- CAM Integration:
- Quality Control and Inspection:
- Creation of Inspection Documentation:
- Quality Inspection Plans:
- Enhancing Product Reliability:
- Reducing Rework and Costs:
- Lifecycle Management:
- Tracking Changes and Revisions:
- Efficient Updates and Enhancements:
- Compliance with Regulations:
- Sustainability and Environmental Impact:
- Enhancing Performance and Reliability:
- Collaboration and Cross-Functional Communication:
- Conclusion:
In today's fast-paced world, where innovation and efficiency are paramount, the role of computer-aided design (CAD) software in product development and manufacturing cannot be overstated, and it can also be essential when you need to complete your SolidWorks assignment. Among the various CAD tools available, SolidWorks stands out as a powerful and versatile solution that has revolutionized the way products are designed, developed, and manufactured. In this blog post, we will explore the significant role that SolidWorks plays in the entire product development and manufacturing lifecycle.
Introduction to SolidWorks:
SolidWorks, developed by Dassault Systèmes, is a leading 3D CAD software that provides a comprehensive suite of tools for designing, simulating, visualizing, and managing product development processes. It was first introduced in 1995 and has since gained widespread popularity due to its user-friendly interface, robust features, and extensive capabilities.
Conceptual Design:
The initial phase of product development involves conceptualizing ideas and transforming them into tangible designs. SolidWorks plays a pivotal role by offering a suite of tools that empowers engineers and designers to give shape to their creative visions. With its powerful sketching and modeling capabilities, SolidWorks enables users to convert abstract concepts into 3D models. This step is critical as it sets the foundation for the entire product development journey.
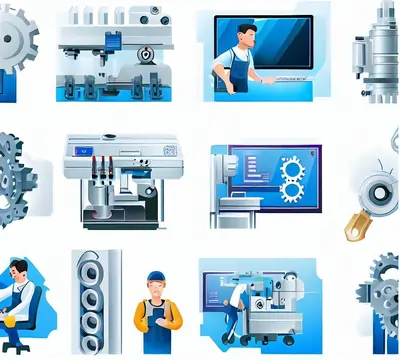
One of the standout features of SolidWorks is its parametric modeling approach. Parametric modeling allows designers to define parameters such as dimensions, constraints, and relationships that govern the geometry of the model. This parametric nature means that modifications to these parameters automatically update the entire design. This flexibility is invaluable for exploring various design iterations without the need to recreate the entire model from scratch.
By facilitating efficient exploration of design possibilities, SolidWorks encourages innovation. Designers can experiment with different shapes, sizes, and configurations, refining their concepts before proceeding to the next stages. This iterative process is essential for refining the design and arriving at an optimal solution that aligns with both functional requirements and aesthetic preferences.
Detailed Design and Validation:
Once the conceptual design is established, the focus shifts to detailed design. SolidWorks streamlines this phase by offering an extensive library of pre-built features, components, and assemblies. Designers can leverage these resources to accelerate the design process, avoiding redundant work and maximizing efficiency. This library not only saves time but also promotes consistency and standardization across designs.
Additionally, SolidWorks' simulation capabilities play a vital role in detailed design and validation. Engineers can subject the digital model to virtual tests and analyses, simulating real-world conditions and scenarios. This allows for the assessment of factors like structural integrity, thermal performance, and fluid dynamics. By identifying potential issues and challenges early in the design process, SolidWorks helps prevent costly design flaws that might only become apparent during manufacturing or testing.
Collaboration and Communication:
In today's interconnected world, collaboration is essential for successful product development. SolidWorks understands this need and offers cloud-based solutions that enable teams to collaborate in real-time, irrespective of geographical barriers. Team members can work on the same design simultaneously, ensuring that everyone remains on the same page and avoiding version control issues.
This collaborative environment fosters efficient communication and the seamless sharing of design data. Designers, engineers, and other stakeholders can provide input, share feedback, and make necessary adjustments in real-time. Moreover, SolidWorks' visualization tools enable the creation of realistic renderings and animations that simplify the communication of complex design concepts to non-technical stakeholders. This is particularly beneficial when presenting ideas to clients, investors, or marketing teams.
Design for Manufacturing (DFM):
A well-designed product is one that can be manufactured without excessive complexity or cost. SolidWorks recognizes this and integrates Design for Manufacturing (DFM) tools into its platform. These tools assess the design for potential manufacturing challenges, such as intricate geometries that might be difficult to machine or expensive to produce. By identifying these issues during the design phase, SolidWorks empowers designers to optimize their designs for manufacturability.
Optimizing for manufacturability leads to reduced production costs and shorter lead times. This integration between design and manufacturing considerations contributes to a smoother transition from design to the manufacturing phase.
Prototyping and Testing:
Prototyping is a pivotal step in product development, enabling designers and engineers to physically validate the design's functionality and performance. SolidWorks aids in this process by generating detailed engineering drawings that serve as blueprints for creating physical prototypes. Whether it's a 3D-printed model or a functional prototype, SolidWorks ensures that the physical prototype closely aligns with the digital design, minimizing discrepancies and the need for iterative adjustments.
This alignment between the digital and physical realms accelerates the prototyping process and reduces the likelihood of unexpected design flaws cropping up during manufacturing or testing.
Data Management and Documentation:
Effective data management is crucial to maintaining order and clarity throughout the product development process. SolidWorks provides robust data management solutions that assist in organizing design files, tracking changes, and promoting collaboration among team members. These solutions help prevent version control issues and ensure that the correct design revisions are used during manufacturing.
Furthermore, SolidWorks enables the creation of comprehensive documentation that is essential for manufacturing and quality control. Assembly instructions, bills of materials (BOMs), technical specifications, and other documentation can be generated directly from the 3D model. This not only saves time but also reduces the chances of errors or discrepancies in the manufacturing process.
CAM Integration:
The seamless transition from design to manufacturing is made possible by SolidWorks' integration of Computer-Aided Manufacturing (CAM) tools. CAM software takes the 3D CAD model and generates precise toolpaths for CNC machines and other manufacturing equipment. This integration eliminates the need to manually recreate manufacturing instructions, reducing the potential for errors and streamlining the production workflow.
By ensuring accurate communication between design and manufacturing, SolidWorks contributes to the production of high-quality parts and components.
Quality Control and Inspection:
In the competitive landscape of modern manufacturing, the quality of products is non-negotiable. Adhering to stringent quality standards is not only essential for customer satisfaction but also for regulatory compliance and maintaining a strong reputation. SolidWorks recognizes the critical role that quality control and inspection play in the manufacturing process and provides comprehensive tools to ensure that the final product meets the highest standards.
Creation of Inspection Documentation:
SolidWorks empowers manufacturers to create thorough and precise inspection documentation directly from the 3D model. This integration of design and quality control streamlines the process and eliminates potential discrepancies that may arise when translating design specifications into inspection documents manually. By generating inspection documentation directly from the 3D model, SolidWorks ensures that the information is accurate and up-to-date.
These inspection documents outline the specifications that the final product must adhere to. They detail dimensions, tolerances, and other critical parameters that define the product's quality. This approach eliminates the ambiguity that can arise when using traditional 2D drawings for inspections, reducing the chances of errors and misinterpretations.
Quality Inspection Plans:
SolidWorks enables the creation of comprehensive quality inspection plans that guide inspectors through the process of evaluating the product's conformity to design specifications. These plans lay out the sequence of inspections, measurements, and tests that need to be performed at various stages of the manufacturing process. By providing a clear roadmap for quality control, SolidWorks ensures consistency in inspections across different batches and manufacturing runs.
The integration of design data and inspection plans minimizes the risk of overlooking critical dimensions or features during the inspection process. This attention to detail enhances the overall quality of the product and reduces the likelihood of defects reaching customers.
Enhancing Product Reliability:
Ensuring that manufactured parts align precisely with the design specifications is paramount for product reliability. A minor deviation in dimensions or tolerances can have a significant impact on the performance and durability of the final product. By leveraging SolidWorks for quality control and inspection, manufacturers can catch and rectify these deviations before they result in costly defects or recalls.
By eliminating variations and discrepancies between design and production, SolidWorks contributes to the creation of products that consistently meet customer expectations. This not only enhances customer satisfaction but also establishes a reputation for producing reliable and high-quality products.
Reducing Rework and Costs:
Defects discovered during or after manufacturing can lead to substantial costs in terms of rework, scrap, and potential recalls. SolidWorks' quality control features significantly reduce the likelihood of such scenarios. By providing accurate inspection documentation and clear quality inspection plans, the software helps manufacturers catch issues early in the process, when corrective actions are less resource-intensive and costly.
By minimizing rework and ensuring that products meet specifications the first time around, SolidWorks contributes to cost savings, more efficient production, and shorter time-to-market.
Lifecycle Management:
The journey of a product doesn't end once it's been designed and manufactured; rather, it continues throughout its lifecycle with maintenance, updates, and improvements. SolidWorks recognizes the significance of this phase and offers robust Product Data Management (PDM) solutions that empower organizations to manage the entire lifecycle of their products efficiently. This lifecycle management is a critical component of sustaining a product's performance, ensuring compliance with evolving regulations, and facilitating ongoing enhancements.
Tracking Changes and Revisions:
In a dynamic manufacturing environment, changes to product designs are inevitable. Whether driven by performance optimizations, component upgrades, or regulatory adjustments, maintaining accurate records of these changes is paramount. SolidWorks' PDM solutions enable organizations to meticulously track changes and maintain a history of design revisions. This meticulous record-keeping aids in accountability, transparency, and the ability to retrace the evolution of the product's design.
Efficient Updates and Enhancements:
As technology evolves and customer needs change, products often require updates and enhancements to remain competitive and relevant. SolidWorks' lifecycle management capabilities provide a streamlined process for implementing updates. With comprehensive records of past designs and changes, engineers and designers can more easily identify the areas that need modification or improvement. This efficiency translates to shorter development cycles for updates, enabling organizations to respond swiftly to market demands.
Compliance with Regulations:
In today's highly regulated industries, products must adhere to an ever-changing landscape of safety, environmental, and quality standards. Failing to comply with these regulations can result in legal repercussions and reputational damage. SolidWorks' lifecycle management features help organizations maintain compliance by ensuring that design changes are properly documented and evaluated for regulatory impact. This proactive approach minimizes the risk of non-compliance and costly recalls.
Sustainability and Environmental Impact:
As sustainability becomes a focal point for businesses and consumers alike, product lifecycle management gains even greater significance. Organizations are increasingly tasked with reducing their environmental footprint and ensuring the responsible disposal or recycling of products at the end of their lifecycle. SolidWorks' lifecycle management solutions provide tools to assess the environmental impact of design changes, helping companies make informed decisions that align with their sustainability goals.
Enhancing Performance and Reliability:
Products that undergo regular updates and improvements tend to exhibit better performance and reliability over their lifecycle. SolidWorks aids in this endeavor by providing a platform for iterative design improvements based on real-world feedback and data. By integrating customer feedback, performance analytics, and simulation results, organizations can refine their products to deliver enhanced functionality, durability, and user experiences.
Collaboration and Cross-Functional Communication:
SolidWorks' lifecycle management features encourage cross-functional collaboration by providing a centralized platform where teams from different departments can access and contribute to the product's lifecycle data. This ensures that design decisions are made with input from various perspectives, resulting in more comprehensive and well-informed enhancements.
Conclusion:
In conclusion, SolidWorks plays a pivotal role in every stage of the product development and manufacturing process. From conceptualization and detailed design to collaboration, simulation, manufacturing, and beyond, SolidWorks empowers engineers and designers to bring their ideas to life efficiently and effectively. Its comprehensive suite of tools, user-friendly interface, and integration with various manufacturing processes make it an indispensable asset in today's competitive market. As technology continues to advance, SolidWorks is poised to remain at the forefront of innovation, shaping the future of product development and manufacturing.