- Understanding Thermal Analysis in Mechanical Engineering
- Applications of Thermal Analysis in Mechanical Systems
- Introduction to SolidWorks for Thermal Analysis
- Conducting Thermal Analysis with SolidWorks: A Step-by-Step Guide
- Advanced Techniques for Thermal Analysis in SolidWorks
- Challenges and Solutions in Thermal Analysis with SolidWorks
- Future Trends: Thermal Analysis and SolidWorks
- Conclusion
In the realm of mechanical engineering, a comprehensive grasp of thermal effects is indispensable for the creation of robust and efficient systems. SolidWorks, a premier computer-aided design (CAD) software, stands out by providing potent tools specifically designed for conducting thermal analysis. This blog aims to deepen our understanding of the critical importance of thermal analysis in the field of mechanical engineering and shed light on how SolidWorks plays a pivotal role in empowering engineers to craft designs grounded in well-informed decisions. Whether you require help with your 3D Modeling assignment or are exploring the intricacies of thermal analysis in mechanical engineering, SolidWorks offers a powerful platform for integrating thermal considerations into the design process and optimizing system performance.
In the intricate world of mechanical systems, the impact of temperature on materials and structures cannot be overstated. Thermal analysis serves as the linchpin in ensuring that components can not only withstand diverse thermal loads but also function optimally under an array of conditions. It acts as a proactive measure, allowing engineers to preemptively identify potential challenges related to temperature distribution and heat transfer, thus fortifying the design process.
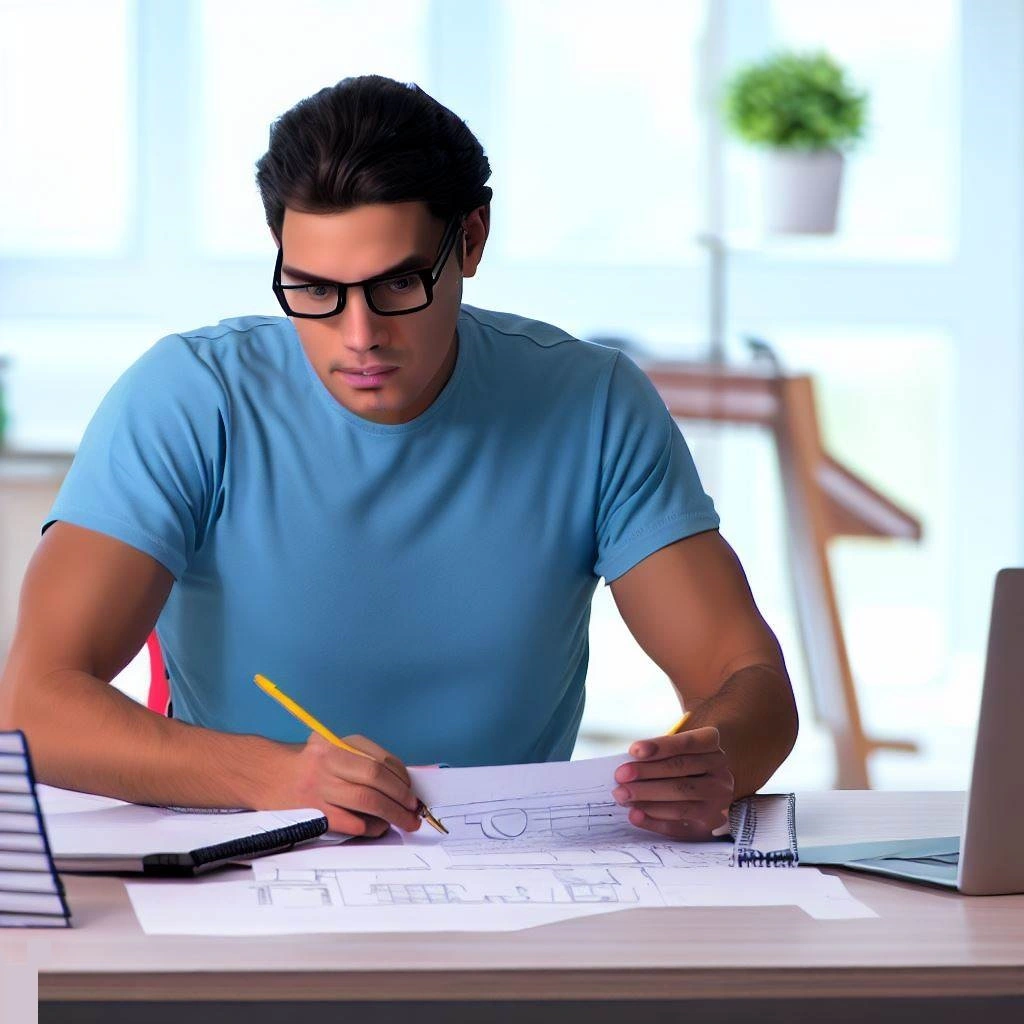
SolidWorks, renowned for its prowess in CAD, extends its capabilities seamlessly into the domain of thermal analysis through its simulation module. This integration is a game-changer, providing engineers with a comprehensive toolkit to simulate and analyze heat transfer, conduction, and convection within their designs.
SolidWorks, renowned for its prowess in CAD, extends its capabilities seamlessly into the domain of thermal analysis through its simulation module. This integration is a game-changer, providing engineers with a comprehensive toolkit to simulate and analyze heat transfer, conduction, and convection within their designs.The software's versatility allows for a meticulous examination of how different materials respond to varying thermal conditions, facilitating the development of designs that are not only structurally sound but also resilient to temperature fluctuations.
Setting up thermal studies in SolidWorks is a methodical process, requiring engineers to define materials, establish boundary conditions, and incorporate heat sources accurately. This meticulous approach ensures that the simulation mirrors real-world scenarios, offering insights into how the designed systems will behave under different thermal circumstances. By accurately representing the thermal environment, SolidWorks empowers engineers to refine and optimize their designs for maximum efficiency.
Interpreting the results of thermal analysis is a crucial aspect of the design process. SolidWorks provides engineers with intuitive tools and visualizations to make sense of complex thermal data. By understanding how heat is distributed within a system, engineers can pinpoint areas of concern, assess the effectiveness of cooling mechanisms, and iteratively refine their designs. This level of insight is invaluable in the pursuit of creating not just functional but highly efficient mechanical systems.
The applications of thermal analysis in mechanical engineering are diverse and impactful. In the realm of electronics, SolidWorks aids in the design of effective cooling solutions, preventing electronic components from succumbing to the detrimental effects of overheating. The automotive industry leverages thermal analysis to optimize engine cooling, exhaust systems, and overall thermal efficiency, contributing to the development of more reliable and high-performance vehicles.
Real-world case studies further illuminate the practical implications of thermal analysis conducted through SolidWorks. From resolving heat dissipation issues in electronic devices to enhancing the thermal efficiency of industrial machinery, these case studies underscore the tangible benefits of incorporating thermal analysis into the design workflow.
Understanding Thermal Analysis in Mechanical Engineering
Understanding Thermal Analysis in Mechanical Engineering is an essential facet that permeates the core of designing resilient mechanical systems. It is not merely an analytical tool but a crucial methodology that scrutinizes the intricate dance of temperature across diverse components. This process is integral, ensuring that mechanical systems not only perform optimally but also exhibit prolonged longevity in the face of varying thermal conditions.
At its core, thermal analysis in mechanical engineering seeks to unravel the impact of temperature fluctuations on different elements within a system. Engineers embark on a meticulous journey, examining the behavior of materials when subjected to heat, identifying potential weak points, and strategizing solutions for improved performance. This investigation extends beyond conventional temperature considerations; it encompasses the thermal dynamics of complex structures, electronic components, and moving parts.
As mechanical systems become increasingly sophisticated, the need for robust thermal analysis grows exponentially. Understanding the intricate interplay between temperature and material properties is imperative for designing components that withstand the rigors of real-world applications. Thermal analysis acts as a sentinel, guarding against unforeseen challenges and offering insights into how materials behave under diverse thermal stressors.
In essence, thermal analysis is the cornerstone of mechanical engineering precision. It transforms the design process from a mere conceptualization into a scientific endeavor, where each element's response to temperature is scrutinized for optimal functionality and longevity. The importance of this analytical approach cannot be overstated; it is the compass guiding engineers through the complex landscape of thermal intricacies, ensuring that the systems they design are not only efficient but also resilient in the face of dynamic thermal environments.
Applications of Thermal Analysis in Mechanical Systems
Thermal analysis stands as a linchpin in the world of mechanical engineering, weaving its influence across a myriad of applications. One of the primary arenas where thermal analysis shines is in the realm of electronic devices. As our gadgets become increasingly compact and powerful, managing heat dissipation becomes a critical consideration. Thermal analysis allows engineers to predict and optimize the thermal performance of electronic components, ensuring they function within safe temperature limits.
Moreover, in the automotive industry, thermal analysis becomes a driving force behind design decisions. Modern vehicles house complex systems where engines, exhaust systems, and electronic components must coexist harmoniously. Through thermal analysis, engineers can assess how heat generated during operation impacts various components, influencing the choice of materials and the overall design. This ensures not only optimal performance but also contributes to the longevity and reliability of automotive systems.
In manufacturing processes, where precision is paramount, thermal analysis plays a key role. Understanding how temperature variations affect materials during production enables engineers to refine manufacturing parameters, leading to higher quality and consistency in the end product. From electronics to automobiles and manufacturing, the real-world impact of thermal analysis is profound, shaping the landscape of mechanical systems design in diverse and transformative ways.
Introduction to SolidWorks for Thermal Analysis
SolidWorks, a prominent player in the realm of computer-aided design (CAD), stands as a transformative force in the field of thermal analysis. This software has redefined the way engineers approach the complexities of thermal studies, offering a robust set of features and tools tailored for precision and accuracy.
One of the standout features of SolidWorks lies in its user-friendly interface, making thermal analysis accessible to engineers with varying levels of expertise. The intuitive design streamlines the process of setting up simulations, allowing users to define parameters, materials, and environmental conditions seamlessly. This ease of use extends to the extensive library of pre-defined materials and thermal properties within SolidWorks, simplifying the assignment of accurate data crucial for realistic simulations.
Furthermore, SolidWorks boasts an array of powerful simulation tools that cater specifically to thermal analysis. Engineers can employ Finite Element Analysis (FEA) techniques to model and evaluate heat transfer, ensuring a comprehensive understanding of how temperature variations impact the structural integrity and performance of mechanical components. The software's ability to simulate conduction, convection, and radiation provides engineers with a holistic view of thermal behavior, enabling them to make informed design decisions.
Conducting Thermal Analysis with SolidWorks: A Step-by-Step Guide
In the realm of mechanical engineering, conducting thermal analysis with SolidWorks is a nuanced process that requires careful consideration of various factors. Let's delve deeper into a comprehensive step-by-step guide, providing invaluable insights into the intricate world of thermal analysis.
The first crucial step in conducting thermal analysis with SolidWorks involves the simulation setup. Engineers need to define the boundary conditions, input the thermal loads, and establish the geometry of the system under scrutiny. SolidWorks offers an intuitive interface that simplifies this process, allowing for the creation of a realistic virtual model that mirrors the physical system.
Once the simulation setup is complete, attention turns to specifying material properties. SolidWorks provides an extensive material library, enabling engineers to choose from a wide array of materials with accurate thermal properties. This step is pivotal in ensuring the fidelity of the analysis, as material characteristics play a significant role in determining how heat is transferred within the system.
With the simulation parameters and material properties defined, the SolidWorks software performs the analysis, generating a wealth of data and results. Interpretation of these results is a critical aspect of the process. Engineers must scrutinize temperature distributions, heat flux, and thermal gradients to gain insights into how the system responds to varying thermal conditions.
Advanced Techniques for Thermal Analysis in SolidWorks
Explore advanced techniques and functionalities within SolidWorks that empower engineers to tackle complex thermal scenarios with efficiency and accuracy.
Conducting thermal analysis with SolidWorks, though powerful, comes with its set of challenges. One common challenge engineers face is accurately defining material properties for complex structures. The variation in material behavior under different temperatures can lead to discrepancies in simulation results. To tackle this, thorough research on material characteristics and leveraging SolidWorks' extensive material database becomes imperative. Engineers should also ensure that the material properties are inputted correctly, considering factors such as thermal conductivity, specific heat, and coefficient of thermal expansion.
Another hurdle lies in simulating transient thermal scenarios with precision. Transient analyses involve understanding how temperatures change over time, adding a layer of complexity. SolidWorks provides dynamic simulation capabilities, but users must carefully set up time-dependent boundary conditions and accurately define the transient behavior of materials to obtain realistic results.
Furthermore, dealing with geometric complexities poses a challenge in thermal analysis. Intricate designs, intricate geometries, and intricate meshing can lead to prolonged simulation times and potential errors. SolidWorks offers mesh refinement and adaptive meshing options to address this challenge, enabling engineers to strike a balance between accuracy and computational efficiency.
Challenges and Solutions in Thermal Analysis with SolidWorks
Conducting thermal analysis with SolidWorks, though powerful, comes with its set of challenges. One common challenge engineers face is accurately defining material properties for complex structures. The variation in material behavior under different temperatures can lead to discrepancies in simulation results. To tackle this, thorough research on material characteristics and leveraging SolidWorks' extensive material database becomes imperative. Engineers should also ensure that the material properties are inputted correctly, considering factors such as thermal conductivity, specific heat, and coefficient of thermal expansion.
Another hurdle lies in simulating transient thermal scenarios with precision. Transient analyses involve understanding how temperatures change over time, adding a layer of complexity. SolidWorks provides dynamic simulation capabilities, but users must carefully set up time-dependent boundary conditions and accurately define the transient behavior of materials to obtain realistic results.
Furthermore, dealing with geometric complexities poses a challenge in thermal analysis. Intricate designs, intricate geometries, and intricate meshing can lead to prolonged simulation times and potential errors. SolidWorks offers mesh refinement and adaptive meshing options to address this challenge, enabling engineers to strike a balance between accuracy and computational efficiency.
Future Trends: Thermal Analysis and SolidWorks
As we peer into the future of thermal analysis within the realm of mechanical engineering, it becomes evident that SolidWorks is at the forefront of innovation, adapting to the ever-changing landscape of cutting-edge technologies. The rapid advancements in computational power, artificial intelligence, and the internet of things (IoT) are reshaping the way engineers approach thermal analysis, and SolidWorks is not lagging behind.
In the coming years, we anticipate a seamless integration of SolidWorks with emerging technologies, enabling engineers to conduct even more intricate and sophisticated thermal studies. The synergy between SolidWorks and AI algorithms is expected to streamline the simulation process, reducing the time required for complex analyses while enhancing accuracy.
Moreover, as the demand for sustainable engineering practices rises, SolidWorks is likely to incorporate features focused on eco-friendly designs. Engineers can anticipate tools that aid in optimizing thermal performance with a minimal environmental footprint, aligning with the global push towards greener technologies.
Additionally, the future may witness SolidWorks expanding its capabilities to address challenges in thermal analysis related to new materials and manufacturing processes. The software is poised to provide enhanced compatibility with evolving industry standards, ensuring engineers have the tools they need to navigate the dynamic landscape of mechanical engineering with confidence.
Conclusion
In conclusion, the exploration of thermal analysis in mechanical engineering, particularly when implemented through SolidWorks, underscores its indispensable role in elevating the efficiency and reliability of mechanical systems. Throughout this blog, we have navigated the fundamentals of thermal analysis, uncovering its broad applications across various industries. By delving into the intricacies of SolidWorks, we have highlighted how this powerful CAD software serves as a catalyst in achieving precise thermal studies.
The applications of thermal analysis in diverse sectors, ranging from electronic devices to automotive engines, have been elucidated. Understanding how temperature influences different components is paramount in ensuring optimal performance and durability. As we've seen, thermal analysis plays a pivotal role in making informed design decisions, mitigating risks associated with overheating, and ultimately enhancing the overall functionality of mechanical systems.
SolidWorks emerges as a game-changer in this scenario, offering a robust platform for conducting thermal analysis with unparalleled precision. The detailed step-by-step guide provided in this blog illuminates the seamless integration of SolidWorks into the thermal analysis process. Engineers can harness the software's features to simulate complex thermal scenarios, ensuring a comprehensive understanding of temperature distributions and their effects on mechanical components.
Moving beyond the basics, advanced techniques and functionalities within SolidWorks have been explored. This includes a discussion on how engineers can leverage the software's capabilities to tackle intricate thermal challenges efficiently. Real-world case studies further exemplify the practical applications of SolidWorks in diverse industries, showcasing its effectiveness in optimizing thermal performance and driving successful design outcomes.
Despite the myriad advantages, challenges in thermal analysis persist, as discussed in this blog. However, SolidWorks provides effective solutions to these challenges, ensuring that engineers can obtain accurate and reliable results. The continual evolution of SolidWorks to meet the demands of emerging technologies and its commitment to addressing industry challenges position it as a forward-looking tool for thermal analysis in mechanical engineering.
Looking to the future, the blog touched upon upcoming trends in thermal analysis and SolidWorks, providing insights into how these technologies are set to evolve. As the field of mechanical engineering continues to push boundaries, SolidWorks remains at the forefront, adapting to new requirements and enabling engineers to stay ahead of the curve.
In essence, the key takeaways emphasize that thermal analysis, especially when facilitated by SolidWorks, is not merely a technical exercise but a strategic imperative. It is an integral part of the design process that ensures the reliability, efficiency, and longevity of mechanical systems. SolidWorks stands as a cornerstone in this pursuit, offering a comprehensive suite of tools that empowers engineers to navigate the complexities of thermal analysis with confidence and precision. As we advance into the future of mechanical engineering, the synergy between thermal analysis and SolidWorks will undoubtedly play a pivotal role in shaping innovative and resilient designs.