- Unveiling the Art of Weldment Modeling
- Organizing Your Workspace for Weldment Success
- Mastering Structural Members: A Deep Dive
- Efficient Sketching Techniques for Weldment Profiles
- Weld Beads and Fillet Welds: Perfecting Connections
- Creating Perfect Connections: The Art of Weld Beads and Fillet Welds
- Utilizing Configurations for Design Variability
- Best Practices for Weldment Cut Lists and Bills of Materials
- Collaborative Design: Tips for Team Projects in SolidWorks
- Conclusion:
SolidWorks, with its intuitive interface and powerful features, has indeed revolutionized the landscape of 3D modeling. When it comes to the intricate realm of weldment designs, a thorough understanding of the tips and tricks embedded in the software can make a substantial difference in enhancing efficiency. In the following paragraphs, we will delve into pivotal strategies aimed at streamlining the weldment modeling process within SolidWorks. These insights range from fundamental principles that lay the groundwork to advanced techniques that can propel your designs to new heights. Whether you're seeking assistance with your weldment assignment or aiming to enhance your proficiency in SolidWorks for weldment modeling, these strategies are tailored to help you optimize your workflow and achieve superior results.
To embark on a successful journey in weldment modeling, it's essential to grasp the foundational principles that underpin the entire process. SolidWorks offers a user-friendly workspace that, when organized effectively, can significantly contribute to a streamlined workflow. Customizing your workspace, strategically placing toolbars, and mastering essential hotkeys are fundamental steps in optimizing your design environment. An efficiently organized workspace not only facilitates quicker access to tools but also minimizes distractions, allowing you to focus on the intricate details of your weldment models.
Moving beyond the workspace, structural members form the backbone of any weldment design. SolidWorks provides a comprehensive structural member tool that not only expedites the modeling process but also ensures accuracy in capturing the essence of real-world structures. Understanding the extensive library of profiles, customizing options, and selecting the right profiles for different applications are crucial aspects of mastering this tool. A deep dive into structural members opens up a world of possibilities for creating diverse and realistic weldment designs.
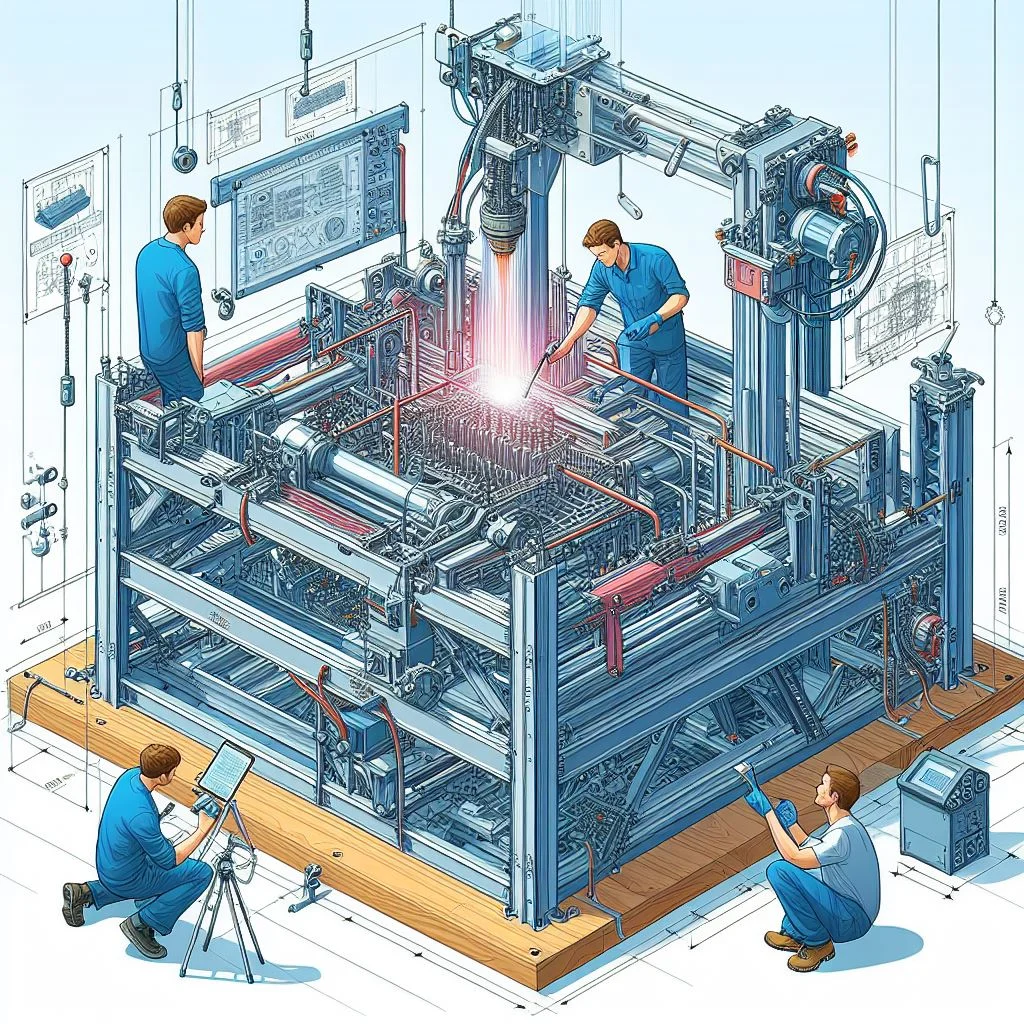
As we progress, sketching emerges as a cornerstone of weldment modeling. The efficiency of your sketches can dictate the overall success of your design. Advanced sketching techniques, such as parametric sketching, allow for greater flexibility and modifiability in your weldment profiles. Learning to harness the full potential of sketching tools empowers you to create designs that not only meet but exceed the requirements of your projects.
Connecting structural elements seamlessly is another critical facet of weldment modeling. SolidWorks offers tools for applying weld beads and fillet welds, simulating real-world welding processes. Mastering these tools not only enhances the visual appeal of your designs but also ensures that they adhere to industry standards. Achieving precision in connections is paramount, and SolidWorks provides the tools to make this process both efficient and accurate.
Configurations play a pivotal role in introducing variability to your designs. Design flexibility is a key advantage in SolidWorks, and configurations enable the creation of variations without starting from scratch each time. Understanding how to leverage configurations effectively ensures that you can adapt your weldment designs to different specifications or project requirements with ease.
Efficient documentation is the final piece of the puzzle. Generating accurate cut lists and bills of materials (BOMs) is essential for the seamless transition of your designs from the digital realm to the fabrication floor. Best practices in organizing and presenting this information ensure that your weldment models are not only visually impressive but also practical and ready for fabrication.
Unveiling the Art of Weldment Modeling
Weldment modeling stands as a cornerstone in the realm of engineering design, playing a pivotal role in industries where the structural integrity of components is paramount. Before we immerse ourselves in the array of tips and tricks to enhance efficiency in SolidWorks weldment modeling, it's crucial to establish a foundational understanding of its significance and broad applications.
Weldments, essentially the joining of structural elements through welding, are prevalent in industries ranging from construction and machinery to automotive and aerospace. The ability to seamlessly integrate diverse components into a unified, robust structure is at the heart of weldment modeling. SolidWorks, as a leading 3D modeling software, provides engineers with a powerful set of tools to create intricate and precise weldment designs.
Understanding the significance of weldment modeling is akin to acknowledging the backbone of many engineering projects. The efficiency and accuracy with which weldments are modeled can directly impact the overall success of a design, influencing factors such as structural stability, fabrication ease, and cost-effectiveness.
In practical terms, weldment modeling in SolidWorks allows engineers to simulate and visualize the assembly of welded structures before they move into the physical realm. This not only saves time and resources but also enables the identification and resolution of potential issues early in the design process. From constructing steel frames to intricate truss systems, SolidWorks weldment modeling empowers engineers to bring their designs to life with precision and reliability.
Organizing Your Workspace for Weldment Success
Efficiency in SolidWorks weldment modeling begins with a well-organized workspace, a foundation that sets the tone for a streamlined design process. To embark on this journey towards optimal organization, start by customizing your SolidWorks workspace. Tailoring the interface to suit your specific needs can significantly enhance your productivity. Arrange toolbars strategically, placing frequently used tools within easy reach. This simple adjustment minimizes the time spent navigating menus and maximizes your focus on the actual design.
Additionally, delve into the world of essential hotkeys. SolidWorks offers a plethora of keyboard shortcuts that can serve as powerful time-saving tools. Mastering these shortcuts not only expedites your modeling process but also cultivates a sense of fluency in your interaction with the software. Whether it's toggling between sketch and feature modes or swiftly switching between views, incorporating hotkeys into your workflow is a game-changer.
Furthermore, consider the spatial arrangement of your workspace. Efficiently managing multiple windows and panels can prevent unnecessary clutter, providing a clean canvas for your weldment modeling endeavors. Explore SolidWorks' customization options for panel visibility, ensuring that only the tools essential to your current task are in view.
Mastering Structural Members: A Deep Dive
Structural members serve as the fundamental building blocks in the realm of weldment design, constituting the very backbone of intricate structures. A deeper understanding of SolidWorks' structural member tool is essential for any designer aiming to harness its full potential. This tool not only simplifies the creation of complex structures but also offers a vast library of predefined profiles, streamlining the design process.
SolidWorks provides an extensive library of structural profiles, ranging from standard shapes to custom profiles, allowing designers to choose components that best suit their specific applications. This library is a treasure trove, offering a diverse array of options that cater to various industries and design requirements. Navigating through this repository efficiently is a skill that can significantly enhance your modeling speed and precision.
Customization is another facet that sets SolidWorks apart in the realm of structural member design. Understanding how to tailor these profiles to fit unique project requirements empowers designers to create weldment structures that align seamlessly with their vision. Whether it's adjusting dimensions, tweaking angles, or creating entirely new profiles, SolidWorks provides the flexibility needed to bring innovative designs to life.
Best practices for selecting the right profiles for different applications form the cornerstone of efficient structural member modeling. Considerations such as load-bearing capacities, material specifications, and manufacturing constraints play a crucial role in making informed decisions during the design phase. By delving into these nuances, designers can ensure that their weldment structures not only meet aesthetic requirements but also adhere to functional and safety standards.
Efficient Sketching Techniques for Weldment Profiles
The foundation of a robust weldment design undeniably lies in the precision and ingenuity of the sketches that define its structural elements. SolidWorks provides a powerful set of tools for sketching, allowing engineers to craft intricate weldment profiles with unparalleled accuracy.
One advanced sketching technique that significantly enhances the versatility of weldment profiles is parametric sketching. Parametric sketching enables the creation of dynamic and adaptable sketches by establishing relationships between different sketch entities. This means that when one aspect of the sketch is modified, such as the length or angle of a line, the entire profile adjusts accordingly. In the context of weldment modeling, this proves invaluable as it allows for swift modifications to the design without the need for extensive rework.
Imagine a scenario where the dimensions of a structural member need adjustment due to changing project requirements. With parametric sketching, a simple alteration of the key dimensions automatically propagates through the entire sketch, ensuring that the weldment profile seamlessly adapts to the new specifications. This not only saves time but also reduces the likelihood of errors associated with manual adjustments.
Furthermore, the use of construction geometry and reference dimensions in sketching adds another layer of precision to weldment profiles. These features enable the creation of relationships between sketch entities and reference geometry, facilitating a more intuitive and controlled sketching process. Engineers can strategically utilize these tools to establish design constraints, ensuring that the weldment profiles adhere to specific standards and criteria.
Weld Beads and Fillet Welds: Perfecting Connections
Connecting structural elements seamlessly is crucial in weldment modeling. Discover the intricacies of applying weld beads and fillet welds in SolidWorks, ensuring that your designs not only look realistic but also adhere to industry standards.
Creating Perfect Connections: The Art of Weld Beads and Fillet Welds
In the realm of weldment modeling, the devil is in the details, and the details often lie in the connections between structural elements. Weld beads and fillet welds play a pivotal role in achieving not just aesthetic appeal but also ensuring the structural integrity of your design.
Understanding the nuances of weld beads is essential. SolidWorks provides a range of tools that allow you to define the size, shape, and positioning of weld beads with precision. Whether it's a straight bead along a joint or a complex pattern, mastering these tools empowers you to create welds that mirror real-world applications.
Fillet welds, known for their rounded profile, are common in weldment designs. SolidWorks enables you to apply fillet welds seamlessly, ensuring that the transitions between connected components are not just visually pleasing but also meet industry standards for strength and durability.
Moreover, exploring the various parameters available for weld customization allows you to tailor your weld beads and fillet welds to specific project requirements. This attention to detail not only enhances the realism of your 3D models but also contributes to the accuracy of simulations and analyses conducted on your weldment designs.
As you delve into perfecting connections through weld beads and fillet welds, keep in mind the importance of adherence to industry standards. SolidWorks provides tools for validating your welds, ensuring that they meet the necessary criteria for structural integrity and performance.
Utilizing Configurations for Design Variability
Design flexibility is a cornerstone of effective 3D modeling, and within SolidWorks, configurations emerge as a powerful tool to harness this advantage. Configurations allow designers to create variations of their weldment designs without the need to initiate projects from scratch each time. This not only saves time but also enhances the overall adaptability of the design.
One of the key benefits of utilizing configurations lies in the ability to manage different design scenarios within a single file. By creating multiple configurations within a project, designers can explore various dimensions, materials, or features without cluttering their workspace with multiple files. This streamlines the design process, making it easier to compare and contrast different iterations of a weldment model.
Moreover, configurations in SolidWorks empower designers to respond efficiently to design changes and client requirements. Whether it's adjusting the size of structural members, modifying weld details, or experimenting with different assembly arrangements, configurations enable a dynamic and iterative approach to design.
To leverage configurations effectively, it's essential to master the art of setting up and managing configurations within the SolidWorks environment. This includes understanding how to create, switch between, and suppress configurations based on specific design needs. Additionally, learning to utilize global variables and design tables enhances the efficiency of managing configurations, providing a structured approach to design variability.
Best Practices for Weldment Cut Lists and Bills of Materials
Efficient documentation is essential for any engineering project. When it comes to weldment modeling, this rings especially true. Accurate cut lists and bills of materials (BOMs) are the linchpin between a meticulously designed digital model and a tangible, fabricated structure.
One fundamental best practice is to start by meticulously labeling and categorizing each component in your weldment model. Consistent and clear naming conventions not only make your model more manageable within SolidWorks but also lay the groundwork for a smooth transition to cut lists and BOMs. By adopting a systematic approach, you ensure that each part is correctly identified, reducing the likelihood of errors during the fabrication process.
Next, delve into the specifics of cut list properties. SolidWorks provides powerful tools to customize and optimize cut lists, enabling you to display essential information such as part quantities, lengths, and even custom properties. Take advantage of these features to tailor your cut list to the unique requirements of your project, providing fabricators with the precise information they need.
When it comes to bills of materials, clarity is key. Structure your BOM in a logical order, mirroring the assembly sequence or grouping similar components together. This not only enhances readability but also streamlines the procurement process, making it easier for those responsible for ordering materials.
Collaboration is another aspect to consider. Ensure that your cut lists and BOMs are easily shareable and accessible to relevant team members. Whether it's the fabrication team on the shop floor or the procurement department, providing a clear and concise documentation package fosters effective communication and minimizes the risk of misunderstandings.
Collaborative Design: Tips for Team Projects in SolidWorks
Collaborative design environments require a delicate balance of individual creativity and seamless communication. In SolidWorks, where teamwork plays a crucial role, effective collaboration is paramount for project success. To enhance collaborative design experiences, it's essential to delve deeper into practical tips for managing team projects.
When engaged in team projects within SolidWorks, implementing robust version control mechanisms is a game-changer. Version control ensures that team members are working on the most recent iteration of the design, preventing confusion and potential errors. By adopting a systematic approach to versioning, such as using revision numbers or date stamps, teams can maintain clarity throughout the design process.
Collaborative editing tools in SolidWorks further facilitate real-time contributions from team members. Explore features that enable simultaneous editing, allowing multiple team members to work on different aspects of the project concurrently. This not only accelerates the design process but also promotes a dynamic exchange of ideas.
In the collaborative design landscape, conflicts are inevitable. SolidWorks offers strategies for resolving design conflicts efficiently. Understanding how to navigate and merge conflicting changes ensures that the final design reflects the collective input of the team. Additionally, fostering open communication channels among team members is crucial to preemptively address potential conflicts and maintain a harmonious workflow.
Conclusion:
As we draw the curtains on our exploration of weldment modeling in SolidWorks, it's abundantly clear that the mastery of these tips and tricks can serve as a transformative catalyst for your design efficiency and overall quality. Implementing these strategies into your everyday workflow can yield remarkable results, turning your weldment models into paragons of precision and innovation.
The significance of efficiency in weldment modeling cannot be overstated. By incorporating the insights shared in this blog, you are not merely adopting a set of guidelines; you are embracing a paradigm shift in your approach to design. Your workflow will evolve from mere functionality to a seamless integration of precision, creativity, and practicality.
One of the prime takeaways from our journey through SolidWorks weldment modeling is the newfound capability to navigate the intricacies of structural design with finesse. The streamlined workspace organization, adept sketching techniques, and judicious use of configurations all contribute to a design process that is not just efficient but also intellectually satisfying.
Furthermore, the integration of collaborative design strategies showcased in this blog opens up new vistas for teamwork. As you apply these principles in a collaborative setting, you'll find that the exchange of ideas becomes more fluid, conflicts are resolved with agility, and the overall project dynamics gain a remarkable coherence.
What sets apart a proficient weldment designer is not just the ability to create functional structures but the knack for elevating them to a level where they stand as testimonies to ingenuity. Your weldment models, when sculpted with the precision and care outlined in these tips, become more than just designs—they become artifacts that narrate a story of thoughtful engineering and design excellence.
As you embark on the journey of implementing these strategies, remember that the key lies not just in the execution but in the continuous refinement of your process. Regularly revisit and reassess your workflow, incorporating new insights and innovations that resonate with the ever-evolving landscape of 3D modeling.