- Understanding Assemblies in SolidWorks
- Assembly Design Methods
- Bottom-up Design
- Steps for Bottom-up Design:
- Example: Designing a Vanity Cabinet
- Advantages of Bottom-up Design:
- Top-down Design
- Steps for Top-down Design:
- Advantages of Top-down Design:
- Preparing for Assembly
- Practical Example: Vanity Cabinet Assembly
- Faucet and Faucet Handles Subassembly
- Bottom-up Design Highlights:
- Door and Moldings Subassembly
- Bottom-up Design Highlights:
- Door Subassembly, Cabinet, and Hinge
- Top-down Design Highlights:
- Final Tips for Efficient Assembly Design
- Conclusion
Assemblies in SolidWorks are a critical component of any complex design, allowing for the integration of multiple parts into a cohesive whole. They can range from a couple of components to over a thousand, including both parts and subassemblies. Understanding how to create and manage these assemblies is essential for efficient and effective design. This comprehensive guide will delve into the intricacies of SolidWorks assemblies, covering the basic methods of assembly design, preparation steps, and practical examples. When working on an assembly assignment, it's crucial to grasp the fundamental concepts and best practices to ensure that all components fit together seamlessly and function as intended. Whether you're dealing with simple assemblies or intricate designs involving numerous parts and subassemblies, having a solid understanding of the processes involved can significantly enhance your productivity and accuracy. For those who might find themselves struggling with their projects, seeking assistance from SolidWorks assignment help can provide the expertise needed to overcome challenges and achieve success. By leveraging professional support, you can gain insights and solutions tailored to your specific needs, ensuring that your assembly projects are completed efficiently and to a high standard.
Understanding Assemblies in SolidWorks
SolidWorks assemblies enable designers to visualize and simulate the interaction between different components within their degrees of freedom. This interaction is defined through assembly mates, which establish relationships between parts. The primary types of mates used in assemblies are:
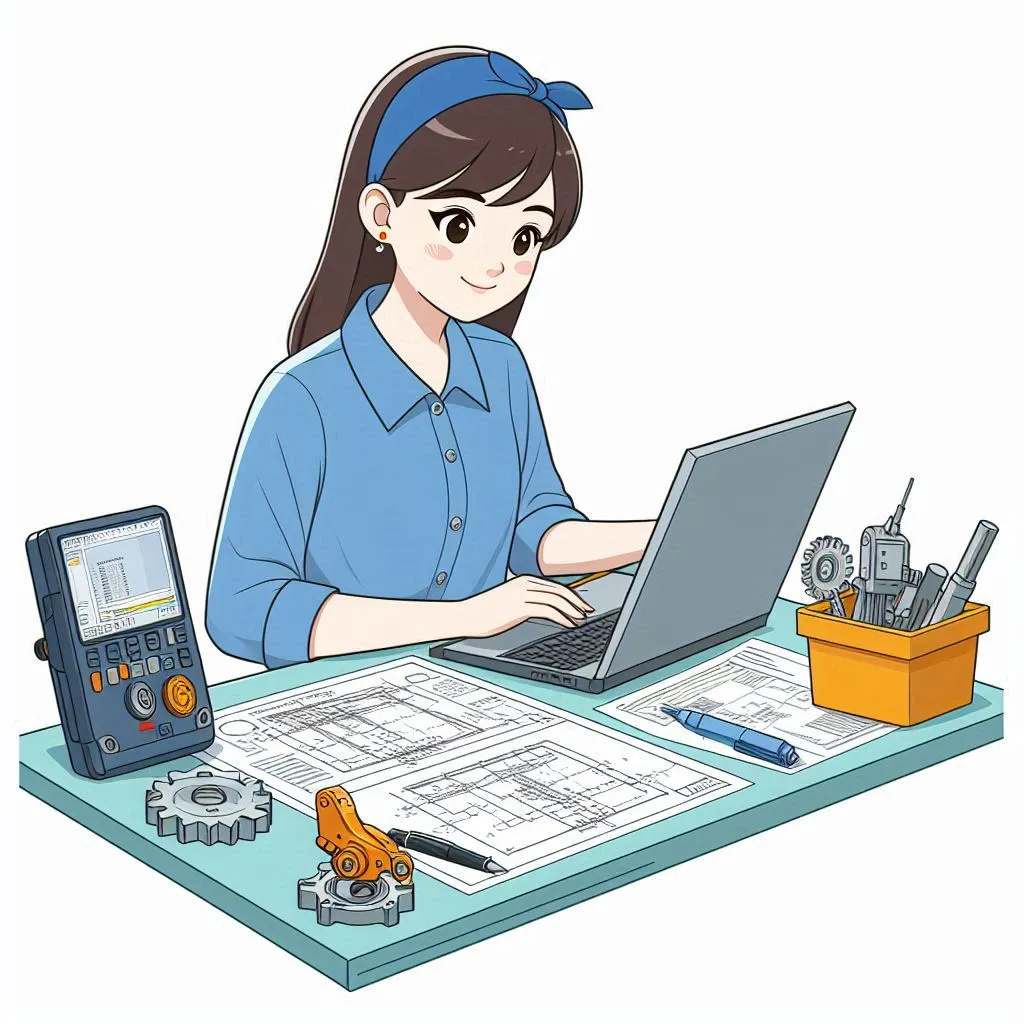
- Coincident Mates: Align two faces, edges, or points to be collinear.
- Concentric Mates: Align the centers of circular edges or cylindrical faces.
- Distance Mates: Maintain a specified distance between two components.
For example, in a vanity cabinet assembly, the faucet handle components are mated to the faucet base component using concentric and coincident mates. These mated components form a subassembly, which can then be integrated into the main assembly, such as the vanity cabinet.
Assembly Design Methods
There are two primary methods for creating assemblies in SolidWorks: bottom-up design and top-down design. Each method has its advantages and is suitable for different scenarios. Designers can also use a combination of both methods to optimize their workflow.
Bottom-up Design
Bottom-up design involves creating individual parts independently, inserting them into an assembly, and mating them as required. This method is ideal for designs using pre-existing parts or off-the-shelf components. The key advantage of bottom-up design is the simplicity of relationships and regeneration behavior, as components are designed independently.
Steps for Bottom-up Design:
- Create Individual Parts: Design each part separately in its own part window.
- Insert Parts into Assembly: Open a new assembly document and insert the individual parts.
- Mate Components: Use assembly mates to define the relationships between the parts, ensuring they interact as intended.
Example: Designing a Vanity Cabinet
For a vanity cabinet, you might create components like the sink and spigot separately. Then, in an assembly document, you insert these parts and use various mates to position them correctly. This method allows you to focus on the details of each part before integrating them into the larger assembly.
Advantages of Bottom-up Design:
- Simplifies part creation by focusing on individual components.
- Ideal for using pre-existing parts.
- Ensures clear and straightforward relationships between components.
Top-down Design
Top-down design starts with the assembly and uses its geometry to define parts, create features affecting multiple parts, or add machined features post-assembly. This method is also known as in-context design, as it allows parts to be created with direct references to other parts in the assembly. This approach is beneficial when parts need to be interdependent or when changes in one part must update related parts automatically.
Steps for Top-down Design:
- Start in Assembly: Begin by defining the overall assembly structure.
- Define Part Geometry in Context: Create parts with references to the assembly geometry, ensuring interdependencies.
- Update Parts Automatically: Changes in one part will propagate to all related parts due to geometric relationships.
Example:Designing a Fixture Based on a Part
In a top-down design approach, you might insert a part into an assembly and then build a fixture around it. By creating the fixture in context, you can reference the original part's geometry, ensuring that any changes to the part will automatically update the fixture. This method is particularly useful for designs where the size and shape of parts are tightly interdependent.
Advantages of Top-down Design:
- Facilitates interdependent part creation.
- Allows for dynamic updates across related parts.
- Ideal for complex assemblies requiring integrated designs.
Preparing for Assembly
Before diving into building an assembly, proper preparation of components is essential. This preparation ensures that the assembly process is smooth and efficient. Here are the key steps to prepare for assembly:
- Load and Anchor the First Component: Anchor the initial component to the assembly origin to serve as the reference point for other components.
- Load Additional Components: Insert other components into the assembly.
- Move and Position Components: Use mates to position the components accurately.
Practical Example: Vanity Cabinet Assembly
Let's explore a detailed example of creating a vanity cabinet assembly, which includes several subassemblies like the faucet and faucet handles, door and moldings, and door subassembly, cabinet, and hinge. This example will illustrate both bottom-up and top-down design methods.
Faucet and Faucet Handles Subassembly
Step-by-Step Guide:
1. Create Individual Parts: Design the faucet base and handle components separately. Use features like extrude, revolve, and fillet to achieve the desired shapes.
2. Assemble Parts:
- Open a new assembly document.
- Insert the faucet base as the first component and anchor it to the assembly origin.
- Insert the handle components.
3. Mate Components:
- Use concentric mates to align the handle components with the faucet base.
- Use coincident mates to position the handles correctly in relation to the base.
Bottom-up Design Highlights:
- Independent design of faucet base and handles ensures simplicity.
- Easy integration of parts into the assembly with straightforward mates.
Door and Moldings Subassembly
Step-by-Step Guide:
1. Create Door Components: Design the door and molding parts separately. Use features like extrude and chamfer for the door and extrude and cut-extrude for the moldings.
2. Insert into Assembly:
- Open a new assembly document.
- Insert the door as the first component and anchor it to the assembly origin.
- Insert the molding components.
3. Mate Components:
- Use appropriate mates to position the moldings around the door edges.
Bottom-up Design Highlights:
- Independent design of door and moldings allows for detailed work on each part.
- Simple mating process to integrate parts into the assembly.
Door Subassembly, Cabinet, and Hinge
Step-by-Step Guide:
1. Create Cabinet and Hinge Parts: Design the cabinet and hinge parts separately. Use features like extrude, cut-extrude, and fillet for detailed design.
2. Assemble Door Subassembly:
- Open a new assembly document.
- Insert the door, moldings, and hinge components.
3. Mate Components:
- Anchor the door subassembly to the cabinet.
- Use mates to position the hinges accurately.
Top-down Design Highlights:
- Integrated design allows for creating parts with direct references to the assembly geometry.
- Dynamic updates ensure that changes to one part affect related parts automatically.
Final Tips for Efficient Assembly Design
Creating efficient and effective assemblies in SolidWorks requires attention to detail and a thorough understanding of both bottom-up and top-down design methods. Here are some final tips to help you excel in your assembly projects:
- Use Mates Wisely: Choose mates that reflect real-world relationships and movements. Ensure that mates do not over-constrain the assembly, allowing for natural movement within the degrees of freedom.
- Check Degrees of Freedom: Regularly check that components move as expected within their degrees of freedom. This ensures that the assembly will function correctly in real-world scenarios.
- Test Assemblies: Simulate the assembly movement and check for interferences. Use SolidWorks' interference detection tools to identify and resolve any conflicts between components.
- Optimize Performance: Large assemblies can slow down performance. Use lightweight components, simplify parts, and leverage configurations to optimize the assembly's performance.
- Document Your Work: Keep detailed documentation of the assembly process, including sketches, references, and mates used. This documentation will be invaluable for future modifications and troubleshooting.
Conclusion
Mastering SolidWorks assemblies is a crucial skill for any designer working on complex projects. By understanding and effectively applying both bottom-up and top-down design methods, you can create assemblies that are not only accurate and functional but also easy to manage and update. Whether you're working on a vanity cabinet or any other intricate design, the principles outlined in this guide will help you achieve your goals efficiently.
Embrace the challenge of assembly design in SolidWorks, and let your creativity and technical skills shine through every project you undertake.