- Building Multiple Configurations of Parts
- Steps to Create Configurations:
- Updating Models Automatically
- Key Techniques for Automatic Updates:
- Importing and Exporting Files
- Importing Files:
- Exporting Files:
- Performing Stress Analysis
- Steps to Perform Stress Analysis:
- Customizing SOLIDWORKS
- Customization Tips:
- Sharing Models
- Best Practices for Sharing Models:
- Creating Photo-Realistic Images of Models
- Steps to Create Photo-Realistic Images:
- Animating Assemblies
- How to Animate Assemblies:
- Managing SOLIDWORKS Files
- File Management Tips:
- Accessing a Library of Standard Parts
- How to Use Standard Parts:
- Examining and Editing Model Geometry
- Key Tools for Examining and Editing Geometry:
- Conclusion
When working on intricate assignments in SolidWorks, understanding and mastering a variety of tools and features is critical. This blog explores key techniques to optimize your workflow, manage complex projects, and create robust, accurate models. Whether you're building multiple configurations of parts, performing stress analysis, or creating photo-realistic images, these strategies will enhance your proficiency and ensure the success of your assignments.
In the realm of SolidWorks assignments, it’s not just about knowing the software; it’s about leveraging its full potential to solve complex design challenges efficiently. By mastering these advanced techniques, you'll be better equipped to handle projects that require precise geometry, thorough analysis, and the ability to collaborate effectively with team members. For instance, incorporating stress analysis early in your design process can prevent costly mistakes down the line. Furthermore, these skills will prove invaluable in solving your design assignments, where the accuracy of your models is paramount. Whether you’re working on a simple part or a complex assembly, these strategies will empower you to produce high-quality results that meet both your academic and professional goals.
Building Multiple Configurations of Parts
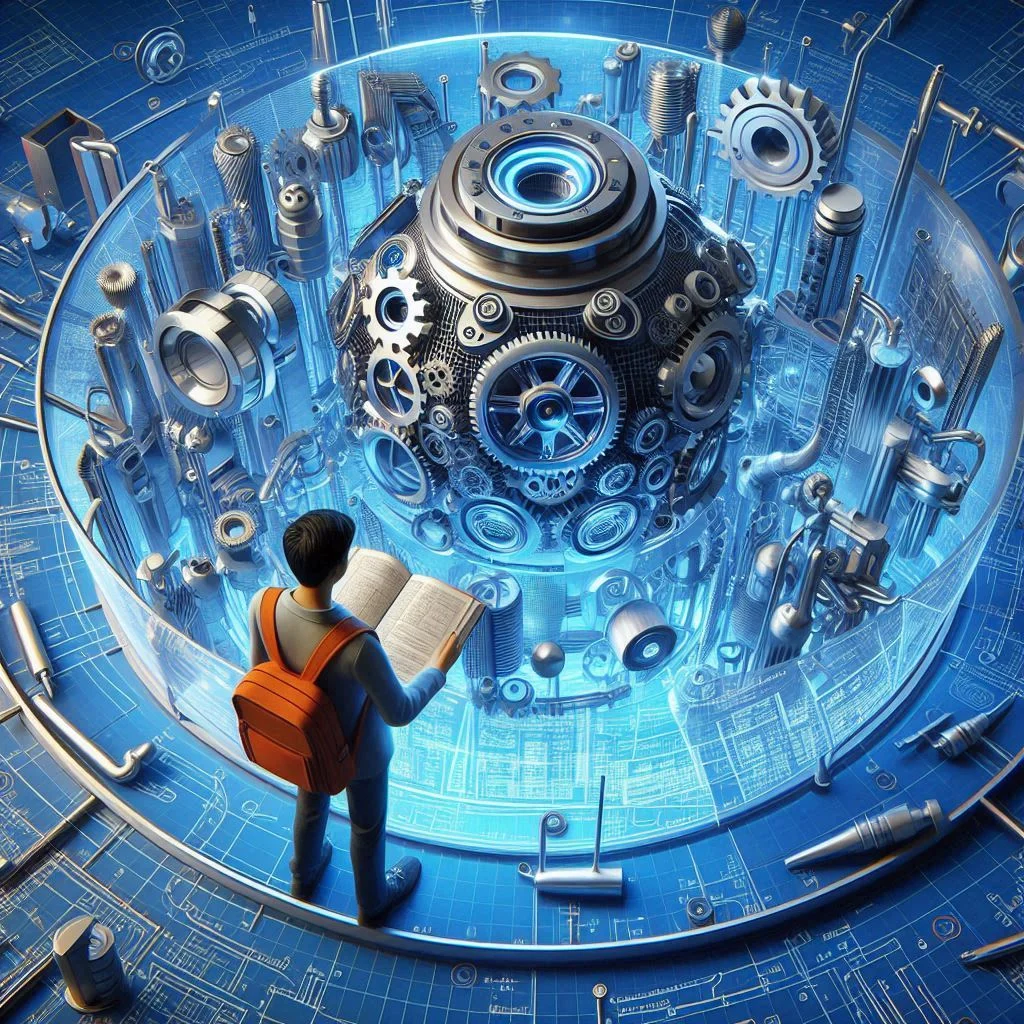
Creating multiple configurations of parts is one of the most powerful features in SolidWorks, allowing you to manage different versions of a part within a single file. This capability is especially useful in design projects that require variations in dimensions, materials, or features, such as producing parts with different lengths, thicknesses, or material grades.
Steps to Create Configurations:
- Open the Configurations Manager: Navigate to the Configurations tab in the FeatureManager design tree.
- Add New Configuration: Right-click on the part name and select "Add Configuration." Here, you can name your configuration and adjust parameters such as dimensions, suppression states of features, and materials.
- Edit Dimensions for Each Configuration: Double-click on a dimension in the model, then adjust the value for the selected configuration.
- Suppress or Unsuppress Features: Right-click on features and select "Suppress" or "Unsuppress" for the specific configuration.
- Switch Between Configurations: Simply click on the configuration in the Configurations Manager to view and work on different versions of your part.
Practical Application: Suppose you're designing a series of brackets that need to fit different frame sizes. By creating multiple configurations, you can design all the variants within one part file, reducing the need for multiple files and simplifying the management of your design data.
Updating Models Automatically
Automating updates in SolidWorks is a crucial feature for maintaining consistency and accuracy across complex models, especially in assemblies where a change in one part can affect others.
Key Techniques for Automatic Updates:
- Equations: Use equations to define relationships between dimensions. For example, if one dimension should always be twice another, you can set this up with an equation, ensuring that changing one dimension automatically updates the related ones.
- Design Tables: Design tables in Excel allow you to control multiple dimensions and configurations from one place. This is particularly useful when dealing with parts or assemblies that require frequent adjustments.
- Global Variables: Define global variables that can be used across different features and parts. When you update a global variable, all linked dimensions update automatically.
- External References: Parts within assemblies can reference the geometry of other parts. These external references ensure that changes in one part reflect in the others.
Practical Application: In an assembly where multiple parts share a common feature (e.g., a bolt pattern that must align perfectly), using equations or external references ensures that any changes to the bolt pattern in one part are automatically reflected in all related parts, maintaining alignment and reducing errors.
Importing and Exporting Files
SolidWorks provides robust capabilities for importing and exporting files, which is essential for collaboration, manufacturing, and integrating with other CAD systems.
Importing Files:
- Supported Formats: SolidWorks supports a wide range of file formats, including IGES, STEP, DXF/DWG, Parasolid, and more. This allows you to bring in models from other CAD systems for further development or analysis.
- Feature Recognition: When importing files, SolidWorks can attempt to recognize features, allowing you to edit imported models as if they were created natively in SolidWorks.
- Handling Imported Geometry: For complex models, you may need to use tools like "Check" and "Repair Sketch" to ensure the geometry is error-free and suitable for further design work.
Exporting Files:
- Saving for Collaboration: Exporting files in formats like STEP or IGES allows you to share models with collaborators using different CAD systems. eDrawings is another powerful tool for sharing lightweight, annotated models that can be viewed without a full CAD system.
- Preparing for Manufacturing: Exporting to DXF or DWG is common when creating flat patterns for sheet metal, or when sharing detailed drawings with manufacturers.
Practical Application: If you receive a 3D model in STEP format from a client, you can import it into SolidWorks, use feature recognition to add editable features, and then proceed with modifications. Conversely, when sending a model to a manufacturer, exporting as a STEP file ensures compatibility with their CAM software.
Performing Stress Analysis
Incorporating stress analysis into your design process is critical for ensuring that your parts and assemblies can withstand operational loads without failure. SolidWorks Simulation provides a comprehensive set of tools for performing stress analysis, thermal analysis, and more.
Steps to Perform Stress Analysis:
- Apply Material Properties: Assign the appropriate material to your part, ensuring that the analysis considers the correct physical properties.
- Define Fixtures and Loads: Specify where your part is fixed (e.g., bolted or welded) and where loads are applied. These could be forces, pressures, or even thermal loads.
- Mesh the Model: SolidWorks will divide your model into small elements (mesh) for analysis. The quality of the mesh can greatly affect the accuracy of the results.
- Run the Analysis: Once set up, run the simulation to calculate stress, strain, and displacement.
- Interpret Results: Analyze the results to identify high-stress areas that may need design modifications. The software provides color-coded stress plots that make it easy to spot potential problem areas.
Practical Application: Imagine designing a bracket that supports a significant load. By performing a stress analysis, you can identify whether the material is adequate, if there are stress concentrations that could lead to failure, and if any design changes are needed to improve the bracket's strength.
Customizing SOLIDWORKS
Customizing SolidWorks to fit your specific workflow can greatly enhance your efficiency, allowing you to focus on design rather than navigating menus and options.
Customization Tips:
- Custom Toolbars and Shortcuts: Create custom toolbars with your most frequently used commands. Assign keyboard shortcuts to commonly used tools to speed up your workflow.
- Macros: Automate repetitive tasks by creating macros. For example, if you frequently create the same set of features or need to export files in a specific format, a macro can perform these tasks with a single click.
- Custom Templates: Set up custom part, assembly, and drawing templates that include your preferred units, title blocks, and other settings. This ensures consistency across your projects.
- User Interface Layout: Adjust the layout of your SolidWorks interface to suit your workflow. Dock and pin toolbars, customize the command manager, and use the S-key shortcut for a quick-access menu.
Practical Application: If you often work with a specific set of features or tools, such as sheet metal design, creating a custom toolbar with all the relevant commands and assigning keyboard shortcuts can drastically reduce the time spent on these tasks, allowing you to focus more on the creative aspects of your design.
Sharing Models
Collaboration is a key part of any design project, and SolidWorks offers several tools to facilitate model sharing and review.
Best Practices for Sharing Models:
- eDrawings: Use eDrawings to share models with team members or clients who do not have access to SolidWorks. eDrawings allow for easy viewing, measurement, and annotation of models, making it ideal for review and feedback.
- Pack and Go: When sharing a complete project, use "Pack and Go" to package all associated files, including parts, assemblies, drawings, and references, into a single zip file. This ensures that the recipient has everything needed to open and work on the project.
- Collaborative Design: SolidWorks 3DEXPERIENCE provides cloud-based collaboration tools that allow multiple users to work on the same model simultaneously, share updates in real-time, and manage project data efficiently.
Practical Application: If you need to send a model to a client for approval, using eDrawings allows them to view the model, make annotations, and provide feedback without needing SolidWorks. For larger projects, "Pack and Go" ensures that all necessary files are included, preventing issues with missing references.
Creating Photo-Realistic Images of Models
Photo-realistic images can greatly enhance the presentation of your designs, whether for client approval, marketing, or documentation. SolidWorks Visualize is a powerful tool for creating these images.
Steps to Create Photo-Realistic Images:
- Apply Materials: Use the SolidWorks material library or import custom materials to give your model realistic textures.
- Set Up Lighting: Adjust the lighting environment to simulate natural or studio lighting. This includes setting up lights such as spotlights, directional lights, and HDR environments.
- Camera Setup: Position the camera to get the best angle of your model. You can also adjust the field of view, depth of field, and perspective to enhance the realism of the image.
- Render the Image: Choose the rendering quality and output format. For high-quality images, SolidWorks Visualize allows you to render with detailed settings, including reflections, refractions, and shadows.
Practical Application: If you need to present a new product design to a client, using SolidWorks Visualize to create photo-realistic images can help convey the design intent more effectively than standard CAD renderings, leading to better client understanding and quicker approvals.
Animating Assemblies
Animating assemblies in SolidWorks provides a dynamic way to showcase how your designs work. This is particularly useful for demonstrating mechanisms, assembly sequences, or product functionality.
How to Animate Assemblies:
- Create Motion Studies: Open the Motion Study tab and add components, motors, forces, and gravity to simulate real-world interactions.
- Timeline Setup: Use the timeline to control the timing of movements and interactions between parts. You can adjust keyframes to create smooth transitions.
- Exploded View Animations: Use exploded view animations to show how an assembly is put together or taken apart. This is particularly useful for assembly instructions or maintenance guides.
- Export Animations: Once your animation is complete, you can export it as a video file, which can be shared with clients, manufacturers, or team members.
Practical Application: If you're designing a complex mechanism, animating the assembly can help you and your clients understand how the parts interact, identify potential issues, and communicate the design intent clearly before moving to prototyping.
Managing SOLIDWORKS Files
Effective file management is crucial in SolidWorks, especially when working on large projects with multiple parts, assemblies, and drawings. Proper file management ensures that your projects remain organized, accessible, and free of errors.
File Management Tips:
- SolidWorks PDM: Use SolidWorks PDM (Product Data Management) to manage file versions, control access, and maintain a clear design history. PDM helps you avoid issues such as overwriting files or losing track of changes.
- Organize Folders: Set up a clear folder structure for your projects. Group related files (parts, assemblies, drawings) together and use descriptive names to make files easy to find.
- Backup Regularly: Regularly back up your files to prevent data loss. SolidWorks PDM can automate backups, but you should also consider using external storage or cloud services for added security.
- Revision Control: Implement a revision control system to track changes to your designs. This is especially important in collaborative environments where multiple people may be working on the same project.
Practical Application: In a large assembly project, using SolidWorks PDM allows you to manage all parts and sub-assemblies efficiently, ensure that everyone on the team is working with the correct versions, and keep a detailed record of all changes made throughout the design process.
Accessing a Library of Standard Parts
Using standard parts from SolidWorks' extensive library can save time and ensure that your designs meet industry standards. The library includes fasteners, bearings, gears, and other common components that are ready to be inserted into your assemblies.
How to Use Standard Parts:
- Access the Toolbox: The SolidWorks Toolbox is where you’ll find a wide range of standard parts. You can access it from the Design Library tab.
- Insert Parts into Assemblies: Drag and drop parts from the Toolbox into your assembly. SolidWorks will automatically size the parts based on the geometry they’re being attached to.
- Customize Parts: While the standard parts are designed to meet industry standards, you can customize them to meet specific project requirements, such as changing the length of a bolt or the number of teeth on a gear.
- Create Custom Libraries: If your projects frequently use specific non-standard parts, you can create custom libraries within the Toolbox for quick access.
Practical Application: When designing a machine assembly, using the Toolbox to insert standard bolts, nuts, and washers not only saves time but also ensures that the components are readily available and meet industry specifications. This reduces the need for custom parts and simplifies the manufacturing process.
Examining and Editing Model Geometry
Accurate geometry is the foundation of any successful design. SolidWorks offers a range of tools to examine and edit model geometry, ensuring that your designs are precise and error-free.
Key Tools for Examining and Editing Geometry:
- FeatureManager: Use the FeatureManager to navigate through your model’s features. You can easily edit, suppress, or reorder features to make adjustments.
- Check Geometry Tool: The Check Geometry tool helps you identify issues such as overlapping surfaces, gaps, and invalid features. This tool is essential for ensuring that your model is ready for manufacturing or analysis.
- Sketch Tools: Sketch tools like “Check Sketch for Feature” and “Repair Sketch” help you identify and correct issues in your sketches before they are used to create features.
- Interference Detection: In assemblies, use the Interference Detection tool to identify overlapping parts or components that may cause issues during assembly or operation.
Practical Application: Before sending a model for manufacturing, use the Check Geometry tool to ensure that all features are valid and there are no issues that could cause problems during CNC machining. In an assembly, use Interference Detection to ensure that parts fit together correctly without overlaps.
Conclusion
Mastering these advanced SolidWorks techniques will not only help you complete your assignments more efficiently but will also enhance the quality and accuracy of your designs. Whether you're working on complex assemblies, performing detailed analysis, or presenting your designs to clients, these tools and strategies will empower you to tackle any challenge with confidence.
By integrating these practices into your workflow, you'll be better equipped to handle the demands of advanced design projects, ensuring successful outcomes and the ability to deliver high-quality work in any SolidWorks assignment.